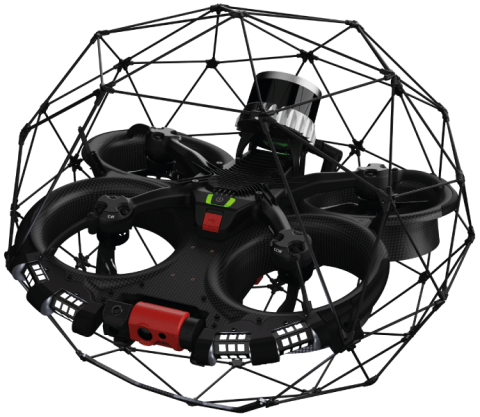
The U.S. Department of Energy Office of Environmental Management is deploying drones for the first time to perform internal inspections of radioactive liquid waste tanks at the Savannah River Site.
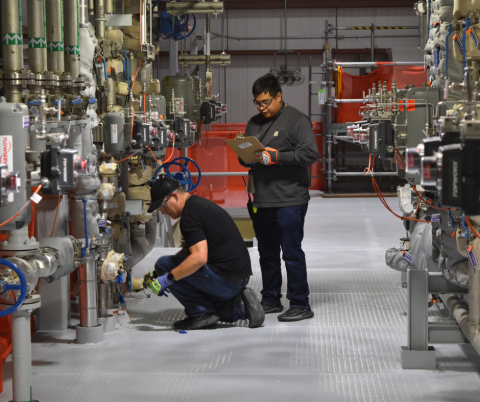
Contractor teams recently collaborated to transfer 4,000 gallons of wastewater between two Hanford Site facilities.
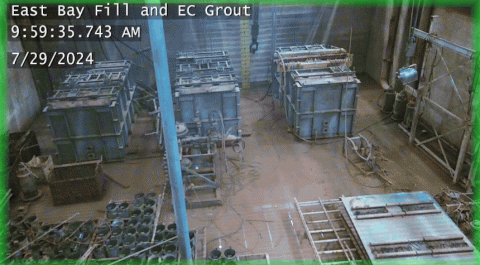
Workers at the Hanford Site recently finished filling the last large concrete basin at the K Reactor Area with cement-like grout. The basin stored reactor fuel rods from the plutonium production mission.

A One Hanford contractor partnership has developed a new process to ensure radioactive and chemical tank waste is ready for pretreatment quickly and efficiently at the Hanford Site.
A student who worked on a capstone project for the U.S. Department of Energy Office of Environmental Management’s liquid waste contractor at the Savannah River Site (SRS) heard a calling to join the nuclear industry.
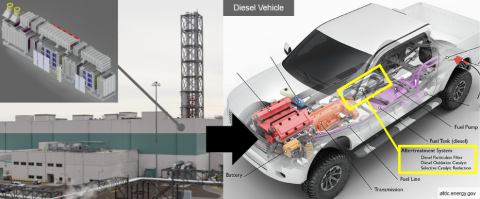
Crews at the Hanford Site’s Waste Treatment and Immobilization Plant are maintaining a large-scale thermal catalytic oxidizer to prepare for operations.
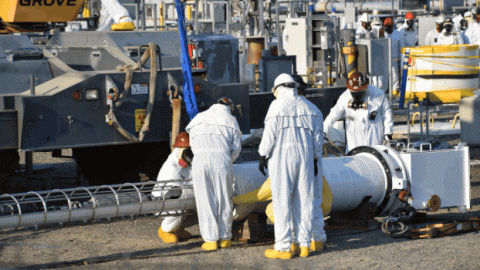
Hanford Site workers are installing equipment to demonstrate how an alternative treatment technology could safely accelerate cleanup of radioactive tank waste.
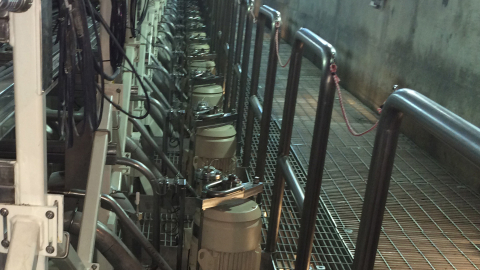
The U.S. Department of Energy (DOE) Office of Environmental Management (EM) has received a shipment of replacement centrifugal contactors for the Salt Waste Processing Facility (SWPF) at Savannah River Site (SRS), which should increase production at the facility by reducing the amount of downtime for maintenance.

U.S. Department of Energy Office of Environmental Management team members at the Savannah River Site (SRS) recently replaced equipment essential to operations in the H Canyon chemical separations facility following more than six months of research, troubleshooting and coordination.
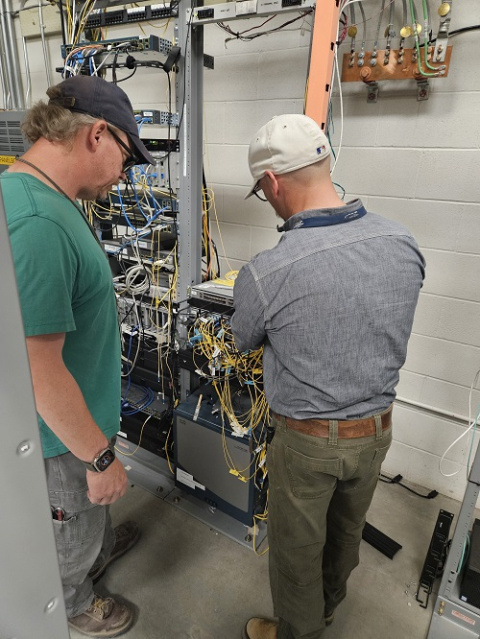
Workers are upgrading and strengthening the framework of the Hanford Site’s local area network to continue supporting the cleanup mission for years to come.