EM crews at the Savannah River Site’s (SRS) 70-year-old H Canyon Chemical Separations Facility safely replaced a motor on a crane for the first time recently, ensuring its viability in this one-of-a-kind facility for years to come.
Office of Environmental Management
May 2, 2023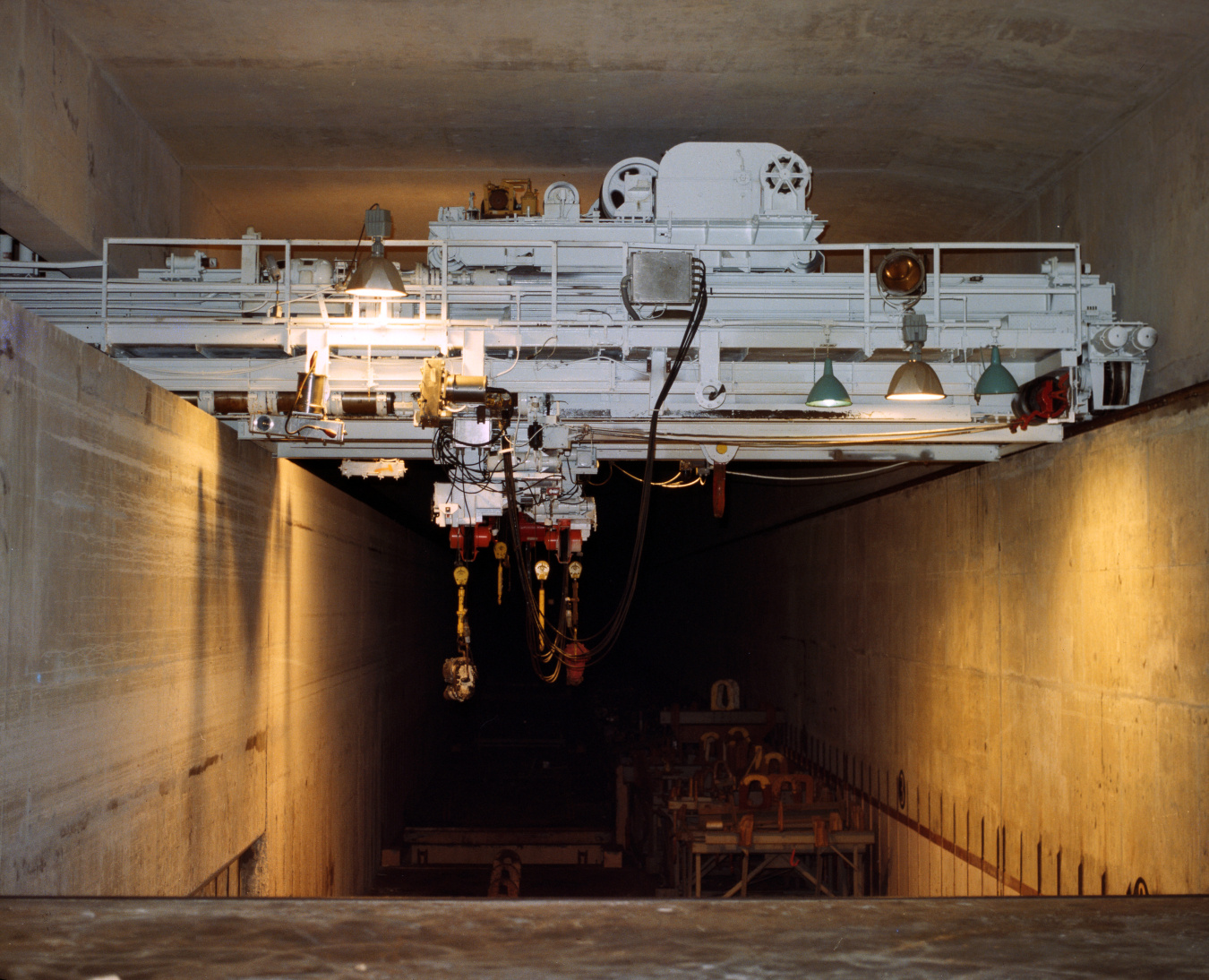
AIKEN, S.C. – EM crews at the Savannah River Site’s (SRS) 70-year-old H Canyon Chemical Separations Facility safely replaced a motor on a crane for the first time recently, ensuring its viability in this one-of-a-kind facility for years to come.
Cranes are essential to H Canyon operations. They are controlled remotely for use in the facility’s radioactive areas to perform work where personnel cannot go. Because of the importance of the cranes, they regularly go through preventive maintenance; however, this is the first time a part replacement of this magnitude has been performed on the crane used for the most radioactive operations.
“This work was more involved than a lot of maintenance work we do because mechanics had to deal with lifts, asbestos, tight spaces and numerous other hazards, all while being performed in Hot Crane Maintenance Area,” said Jeff Bickley, H Canyon Maintenance manager for Savannah River Nuclear Solutions, the SRS managing and operating contractor.
H Canyon is divided into three sections: the hot side, where there are higher levels of radiation; the warm side, with lower levels of radiation; and the middle section, where there is no radiation. Both the hot and warm sides are where operations are performed using cranes. No personnel have entered the hot or warm canyon since material was first introduced to the facility in the 1950s.
Mechanics working on the crane motor replacement project wore fall protection due to the crane’s height, in addition to two pairs of coveralls under breathing air suits to protect them from contamination.
“We worked very deliberately and carefully to make sure no one tripped over any of the hoses and that everyone was safe during all aspects of the job,” Bickley said.
Replacing the approximately 850-pound motor took weeks of planning and preparation, as well as integration between many different departments at SRS including rigging, radiation protection and operations.
“We found old videos of the original motor assembly from the manufacturer and watched them as a group to aid in the planning of the work,” said Bickley. “Because of the planning and communication between departments, the job went off flawlessly.”
To receive the latest news and updates about the Office of Environmental Management, submit your e-mail address.