EM’s Depleted Uranium Hexafluoride Conversion Project completed several plant modifications at its Portsmouth, Ohio and Paducah, Kentucky facilities.
Office of Environmental Management
February 23, 2021LEXINGTON, Ky. – EM’s Depleted Uranium Hexafluoride (DUF6) Conversion Project completed several plant modifications at its Portsmouth, Ohio and Paducah, Kentucky facilities to improve their safety and reliability.
“These plant upgrades will increase worker safety while improving productivity at our conversion plants,” said Robert Edwards, manager of EM’s Portsmouth/Paducah Project Office (PPPO). “It represents time and effort well spent in preparation for the safe and deliberate restart of facilities.”
The DUF6 Project addresses the nation’s legacy of six decades of uranium enrichment operations at DOE gaseous diffusion plants at Portsmouth, Paducah, and Oak Ridge, Tennessee. The project converts the DUF6 byproduct, currently stored in cylinders at Portsmouth and Paducah, to a more stable oxide form for reuse or disposal.
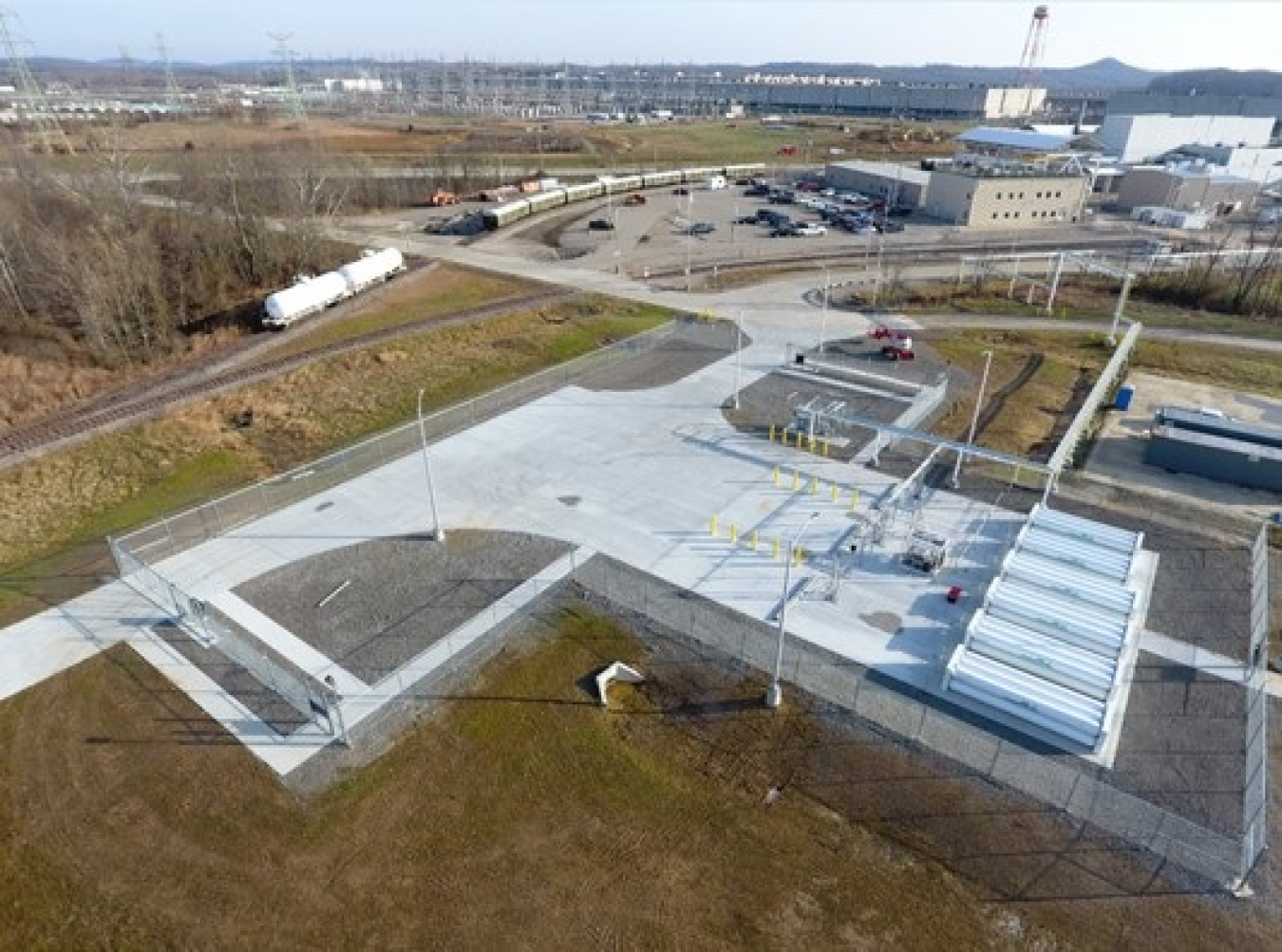
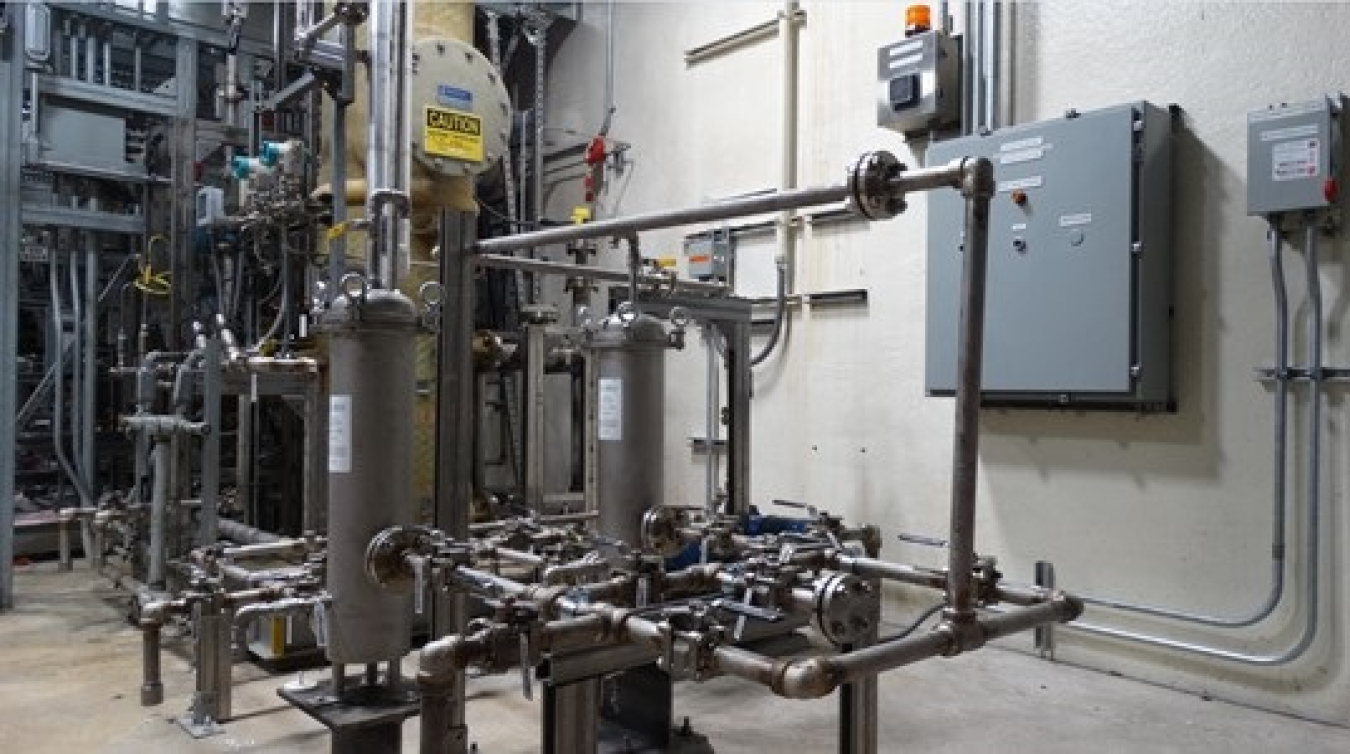
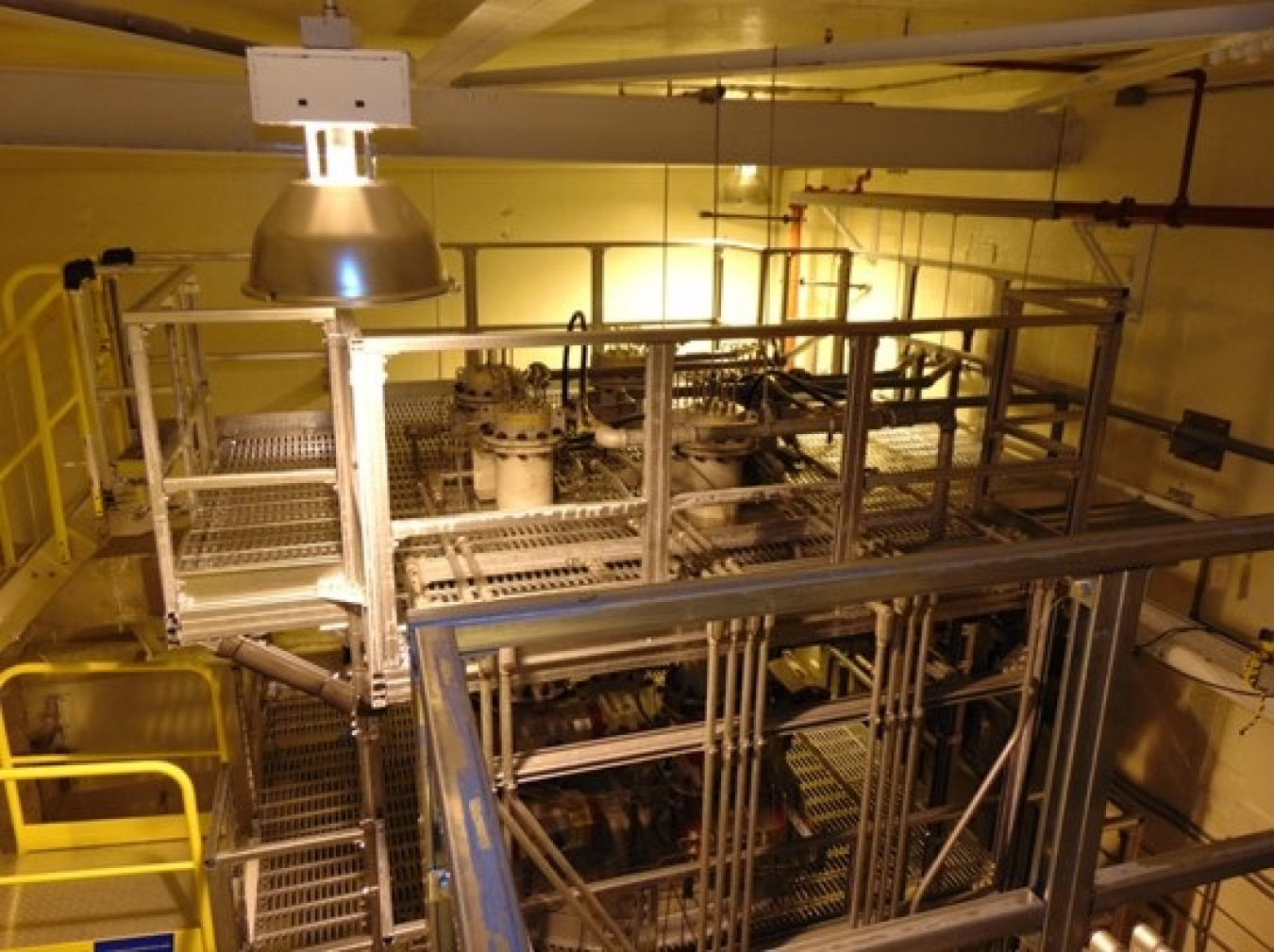
Among the improvements at both sites are new backup systems and improved piping to reduce the possibility of worker injury, plant outages, or chemical leaks.
The backup system is for producing hydrogen when the primary system is offline. Hydrogen is a necessary component of the conversion process. The new stainless steel piping reduces the possibility of potassium hydroxide leaks.
Other improvements intended to further improve worker safety include permanent maintenance access platforms to replace scaffolding in the Oxide Powder Handling Hopper Rooms, and new maintenance isolation valves in the hydrogen fluoride storage system.
Zack Smith, president and project manager for PPPO operations and maintenance contractor Mid-America Conversion Services, said United Steel Workers (USW) input was essential to the projects’ successful completion.
“USW worker feedback was fundamental in targeting areas for improvement that provided the greatest return on employee safety,” Smith said. “We recognize that the workforce is our most valuable asset and will continue to put safety first."
DUF6 Project safety accomplishments in the last year include shipping 2.3 million gallons of hydrogen fluoride for commercial reuse, completing 24,000 required storage-cylinder inspections, and processing 69 non-standard DUF6 cylinders.