Upgrading bio-oils with petroleum feedstocks at existing refineries—known as “co-processing”—could offer a fast pathway for lowering the carbon footprint of today’s transportation fuels.
April 21, 2022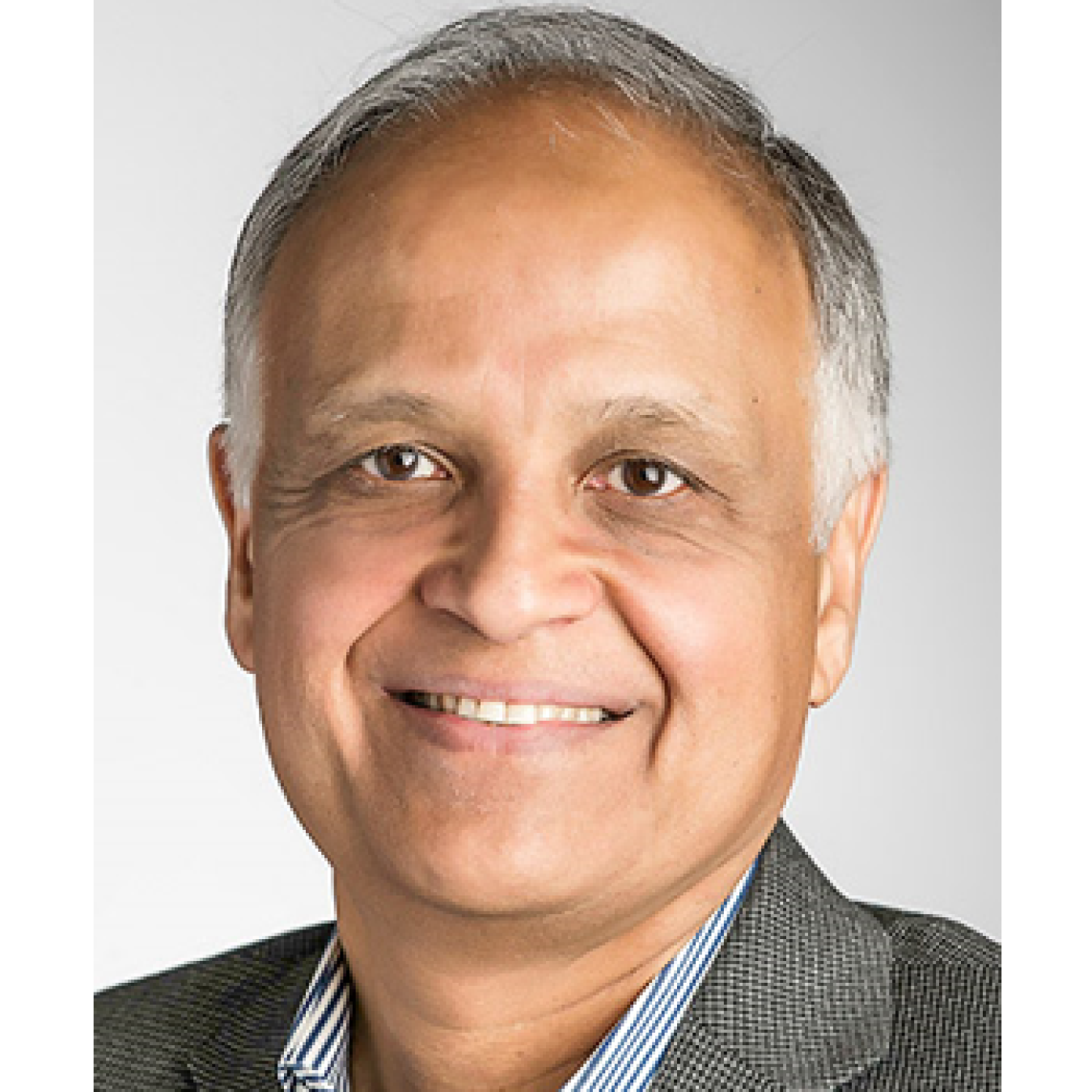
Author: Zia Abdullah, Laboratory Program Manager, National Renewable Energy Laboratory
Read Zia's bio ►
Meet the other bloggers ►
Return to Bioprose blog ►
Upgrading bio-oils with petroleum feedstocks at existing refineries—known as “co-processing”—could offer a fast pathway for lowering the carbon footprint of today’s transportation fuels. With equipment and infrastructure already in place, more than 100 refineries across the country are equipped to integrate bio-oil into their processes. But just where might companies insert renewable bio-oils into existing refinery systems like fluid catalytic crackers and hydrotreaters? If successful, just how much of that renewable or “green” carbon makes it into final fuel products?
In this three-part blog series, the National Renewable Energy Laboratory (NREL), Pacific Northwest National Laboratory (PNNL), and Los Alamos National Laboratory (LANL) offer insights into these pressing co-processing questions—and others—amid the push to dramatically expand the production of climate-friendly fuels. Read part 2 and part 3.
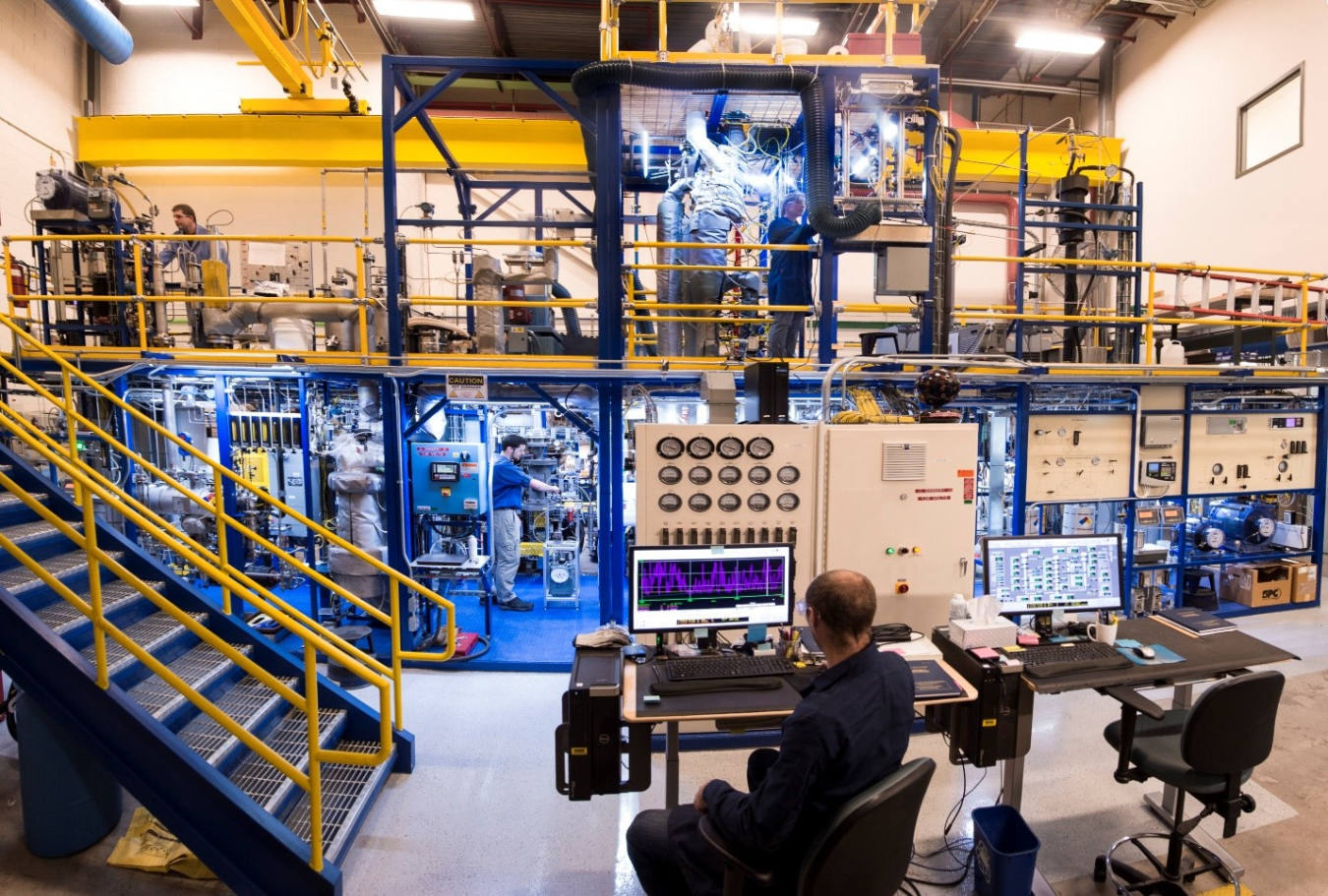
A Lab to Reflect the Real World—NREL’s customizable Davison Circulating Riser enables real-time analysis of the dynamics of co-processing in fluid catalytic crackers—common units at many U.S. refineries. Photo courtesy of Dennis Schroeder, NREL
With carbon footprints far smaller than petroleum-based fuels, bio-oils made from biomass or waste resources can be upgraded into net-zero-emission fuels to lower emissions in the aviation and marine sectors. Injecting more of these renewable biofuels into the market requires robust production infrastructure to support growing demand for climate-friendly fuels.
Co-processing bio-oils with petroleum at existing refineries is a promising way of bringing more of these fuels to market in as few as five years. But it has been difficult to predict how co-processing might work with existing fuel production equipment. Refinery engineers need to know how bio-oil interacts with refinery feedstocks, catalysts, components, and reactors. They must also understand just what chemical compounds bio-oils yield.
Fortunately, refineries don’t have to predict anymore. New data and insights from NREL’s laboratories confirm that co-processing is already possible using fluid catalytic crackers present at numerous refineries across the country.
NREL’s Pilot Plant Designs Co-Processing Roadmap for Refineries
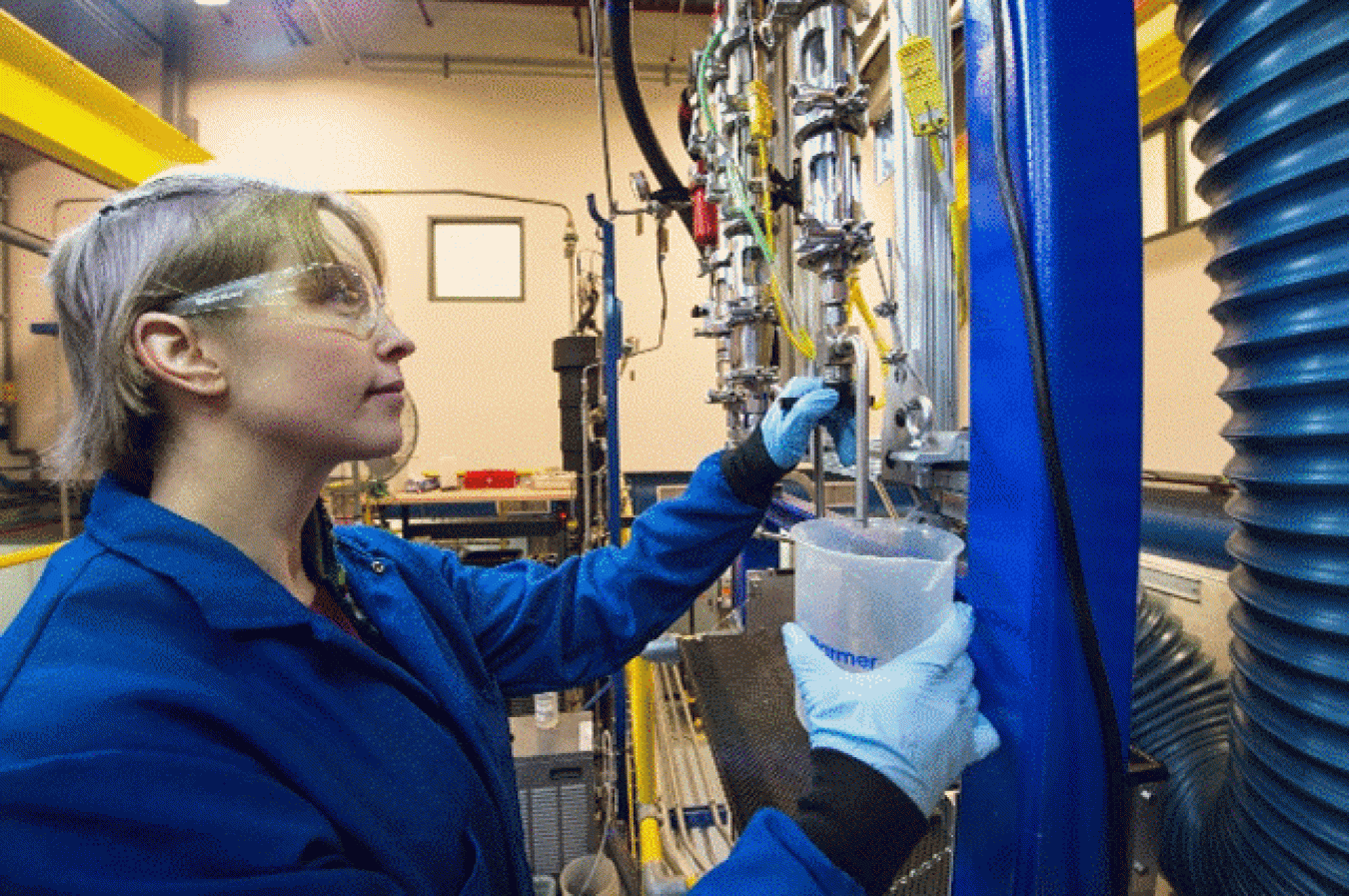
An NREL researcher takes a fuel sample from the Davison Circulating Riser. Photo courtesy of Dennis Schroeder, NREL
In partnership with the refinery catalyst company Johnson Matthey, NREL scientists Kim Magrini and Calvin Mukarakate have shown that refinery-compatible catalysts and processes transform bio-oil into many of the same compounds found in today’s petroleum-based fuels.
The private-public partnership achieved this by co-processing oak bio-oil and petroleum using the fluidized catalytic cracker in NREL’s Davison Circulating Riser, which duplicates process conditions at large U.S. refineries. By amending the bio-oil with carbon-13, an isotope that leaves a traceable chemical mark, the team could follow its metamorphosis for easy comparison to petroleum-derived fuel.
The fluidized catalytic cracker broke the hydrocarbon molecules in the petroleum and bio-oil into simpler components. This standard refinery process takes places in a tall reactor called a riser, which fractured the hydrocarbons into a spectrum of hot vapors using high heat and a moving bed of reactive catalyst.
A stripping column then separated the vapors from the catalyst, sending them to a condenser where they were cooled and liquified. The result was a dark liquid full of useful compounds:
- Strong, double-bonded alkenes such as ethylene, a ubiquitous industrial commodity for making plastics (polyethylene and styrene) and for ripening fruit;
- Alkanes saturated with hydrogen, which is often used to make jet fuel;
- Cyclic aromatics like benzene, which are intermediates for jet fuel and commodity chemicals for manufacturing rubbers, plastics, lubricants, and other products.
The carbon in the co-processed liquid had come from different feedstocks—petroleum and net-zero-carbon bio-oil—but the resulting compounds were strikingly similar to energy-dense hydrocarbons used in gasoline, diesel, and sustainable aviation fuels.
But just where had the carbon from bio-oil ended up? What did the carbon-13 reveal?
Vivid Isotopic Highlights Reveal the Metamorphosis of Bio-Oil
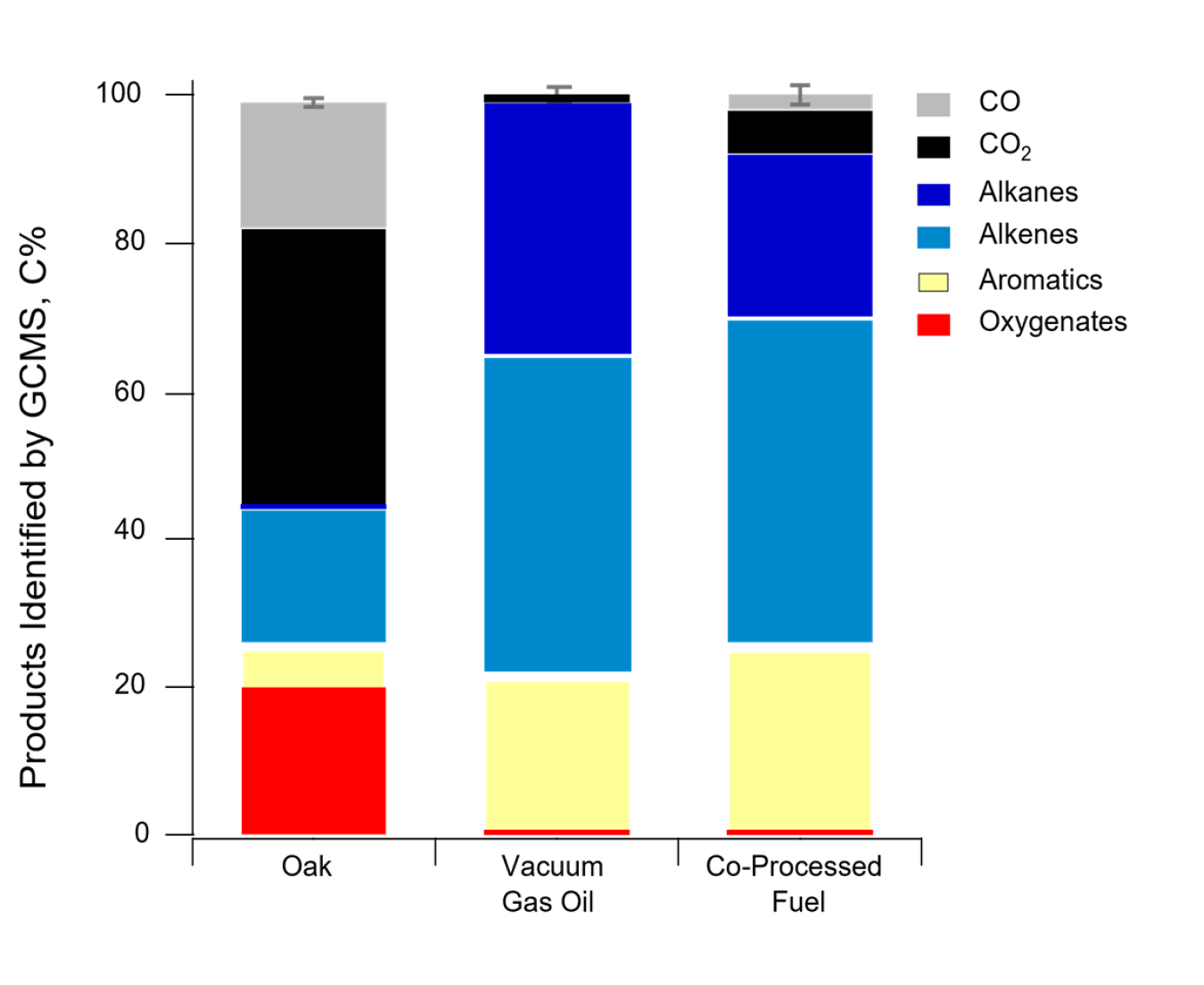
What The Highlights Revealed: The NREL co-processed mixture contained enhanced aromatics and alkenes from the oak feedstock. Image courtesy of Kim Magrini, NREL
Using a specialized chemical measuring tool called a mass spectrometer, the scientists searched for the isotopic markers left in the co-processed liquid from petroleum and oak bio-oil.
Because carbon-13 is heavier than the carbon found in petroleum—and contains an extra neutron—the tool made it easy to distinguish products made from bio-oil from those made from petroleum.
Where the petroleum was transformed into alkanes, alkenes, and aromatics, the team found that the bio-oil was primarily remade into additional aromatics, alkenes, and cycloalkanes.
In other words, the process had yielded the right ingredients for making fuel from renewable feedstocks such as oak.
Collaborative Research Drives Co-processing Potential
Along with researchers from Los Alamos National Laboratory, Pacific Northwest National Laboratory, and other organizations, NREL continues researching and developing the potential of co-processing. Tweaking feedstocks and catalysts, for example, could enable companies to “tune” the composition and properties of bio-oil.
Additional studies are already underway to answer lingering questions on about co-processing mechanics:
- Can refinery catalysts be improved for co-processing? Catalysts amended with metals like lanthanum could yield more bio-oil aromatics, which are key precursors for jet fuel.
- How do bio-oils made from varied feedstocks affect co-processing? The composition of bio-oil can change depending on the biomass used in its creation, whether hardwood, softwood, grasses, or even used paper and cardboard. NREL is studying how varying amounts of lignin, cellulose, and hemicellulose in these feedstocks could impact how a refinery co-processes bio-oil.
- How much green carbon makes it into the co-processed fuel? LANL researchers are developing economical and reliable tools to measure green carbon in co-processed fuels and are using NREL- and PNNL-produced fuels to benchmark green carbon incorporation.
Reducing the Risks of Co-processing Amid Push for Climate Solutions
NREL’s research underscores a simple truth: it is possible for refineries to start co-processing bio-oil with petroleum to lower net greenhouse gas emissions.
By showing the chemical outputs of co-processing at a pilot scale, NREL and Johnson Matthey have lowered the risk for petroleum refineries across the country to begin implementing co-processing. With fluid catalytic crackers already in place, more than 100 U.S. refiners are set to begin lowering the carbon footprints of their fuels within the next five years. Chevron and Parkland refineries are already exploring co-processing waste oils (i.e., fats, oils, and greases) into sustainable aviation fuels using existing equipment and reactors.
That progress is welcome news as the need for climate solutions continues to accelerate. Co-processing is a promising solution for rapidly expanding supplies of alternative fuels at airports and seaports across the country, making it a key part of U.S. strategies to slash greenhouse gas emissions in half by 2030.
Dr. Zia Abdullah
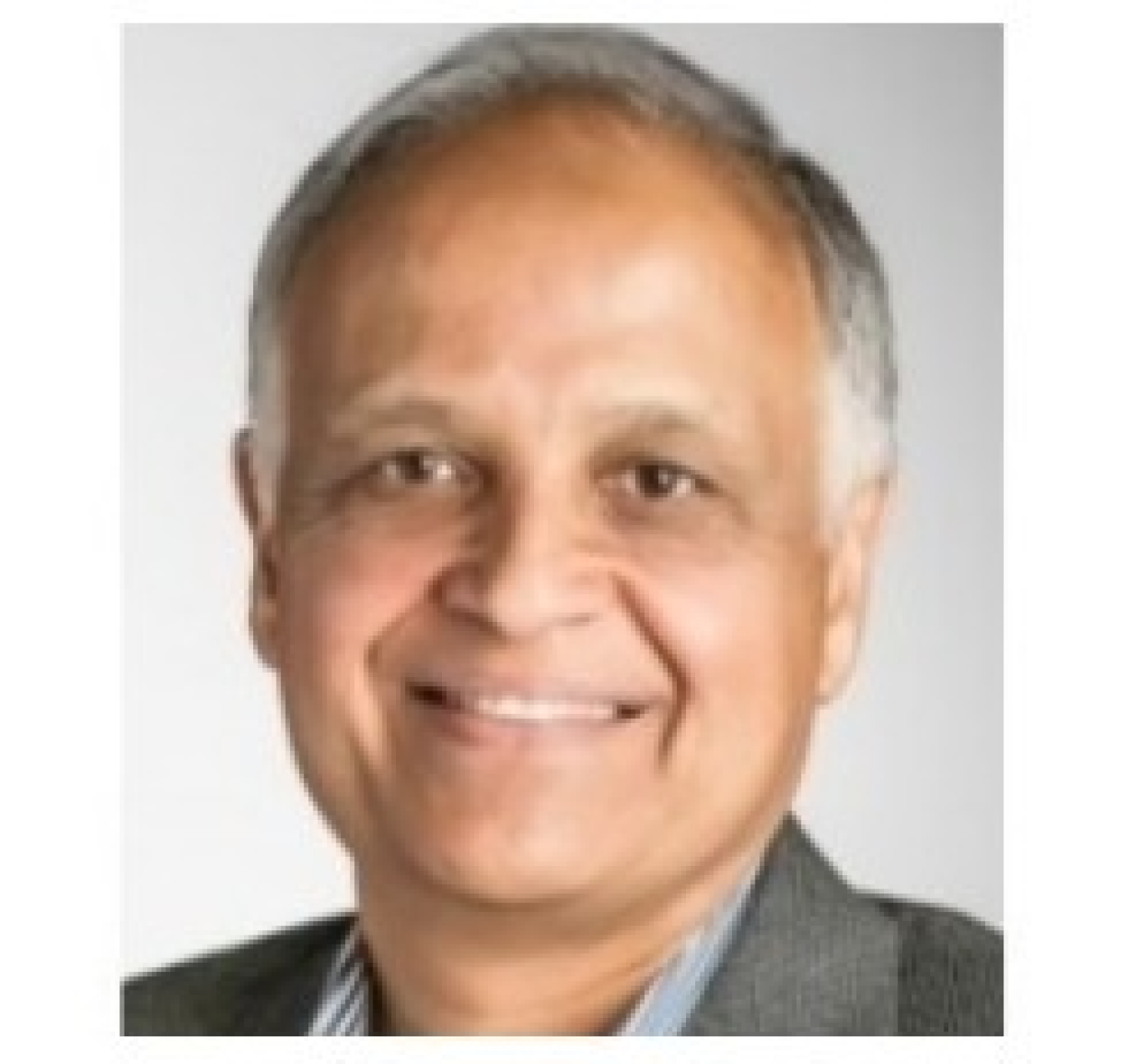
Dr. Zia Abdullah is laboratory program manager for the National Renewable Energy Laboratory’s (NREL’s) Bioenergy Technologies Office program.
Zia has extensive experience and accomplishments in thermochemically and biochemically converting biomass to fuels and chemicals. His experience includes more than 25 years of industrial research and development in biomass conversion, as well as problem solving, new product development, business development, and project management.
Prior to joining NREL, Zia was chief technology officer at Versa Renewables LLC, where he developed and commercialized biomass pyrolysis and biopolyol technologies. Before Versa, Zia served as one of the Battelle Memorial Institute’s 11 fellows, leading the development of technology and commercial application for fuels, chemicals, and materials from the thermochemical and biochemical conversion of biomass. Prior to working at Battelle, Zia was a research advisor (fellow) at Weyerhaeuser Company, where he worked on challenges related to manufacturing and biomass valorization.
Meet our other bloggers ►
Return to Bioprose blog ►