EM Richland Operations Office (RL) contractor Central Plateau Cleanup Company is testing a new mobile ventilation system that will protect workers.
Office of Environmental Management
March 2, 2021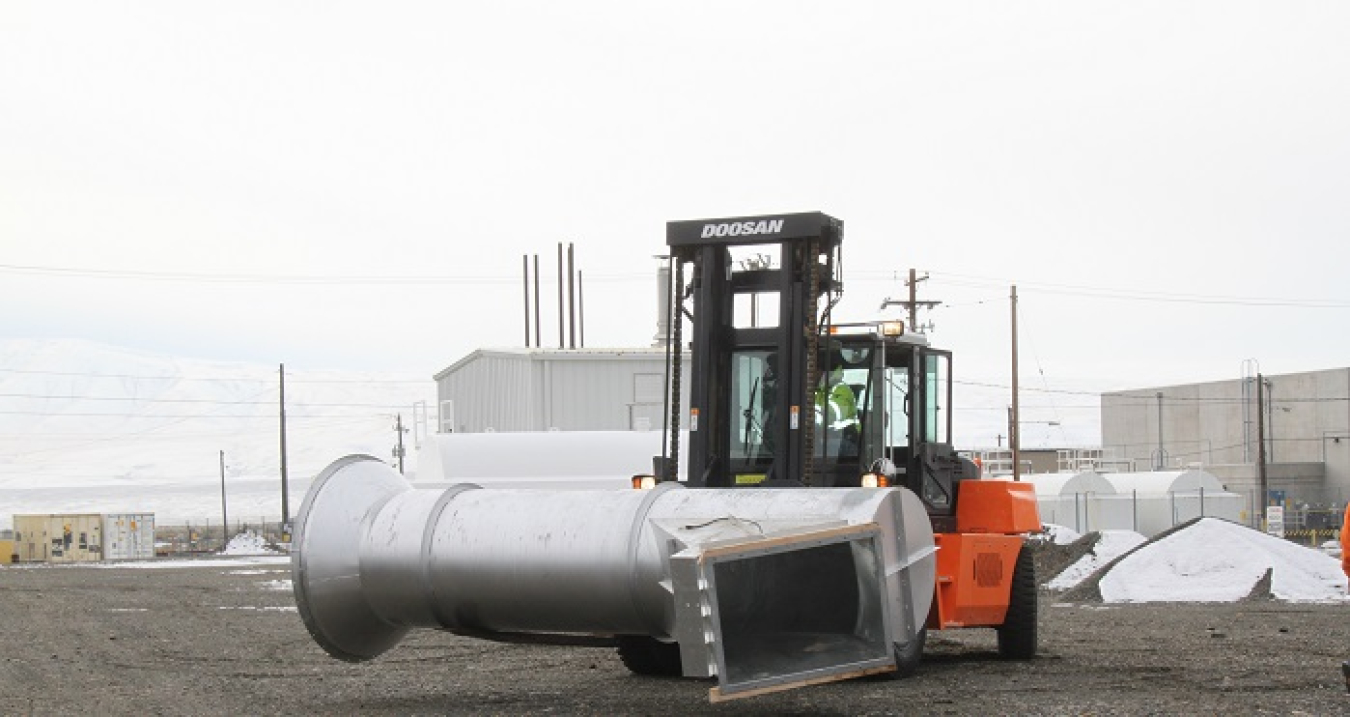
RICHLAND, Wash. – EM Richland Operations Office (RL) contractor Central Plateau Cleanup Company (CPCCo) is testing a new mobile ventilation system that will protect workers while they decontaminate former plutonium processing facilities on the Hanford Site’s Central Plateau.
As workers move from facility to facility to prepare them for demolition, they will be able to use the same mobile ventilation system, rather than build temporary systems for each facility, saving time and money on the projects.
The new system would also allow workers to remove tons of contaminated material from old ventilation systems and shut them down. Those systems supported some of the largest and most contaminated facilities, which together produced nearly two-thirds of the plutonium for U.S. nuclear weapons.
From 1952 to 1967, the massive Reduction-Oxidation (REDOX) Plant processed approximately 24,000 tons of uranium fuel rods to recover plutonium. The plant is 470 feet long, 160 feet high, and up to 160 feet wide and was designed to minimize worker exposure to radiation and contamination.
The plant’s interior is made up of several floors and areas called galleries. Sample galleries were used to collect radioactive samples from remotely operated processing equipment. Pipe galleries supplied chemicals, water, air, and gases for processing and sampling. Workers in operating galleries controlled plant systems.
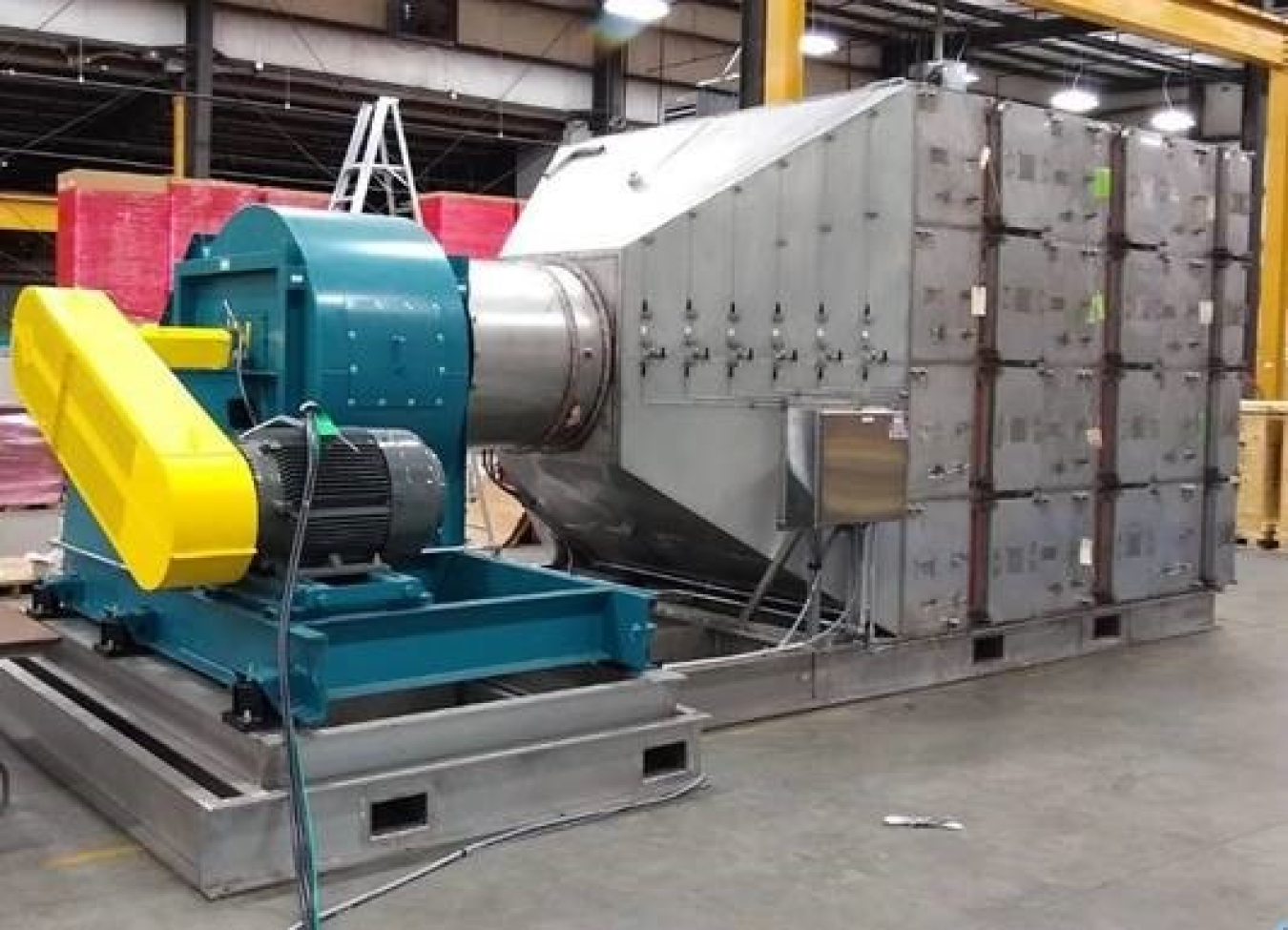
Perhaps the plant’s most impressive area is the canyon, a large, open area that is hundreds of feet long and stretches to the ceiling. Called a canyon because of its resemblance to a box canyon, which is narrow with a flat bottom and vertical walls, the area is open to allow a crane to lift thick covers off of cells, which are structures that contain highly radioactive and contaminated processing equipment.
In addition to the shielding the cell covers provided, thick concrete and metal walls throughout the plant also shielded workers from radiation during operations. The plant’s enormous ventilation system minimized the spread of contamination, and filtration systems prevented airborne contamination in processing cells and sample galleries from reaching REDOX Plant operators and site personnel outside the plant.
“Since processing at the REDOX Plant ended in the late 1960s, the plant has been in a surveillance and maintenance mode,” said Mark French, RL federal project director for the Central Plateau. “Updating the ventilation system is critical to protecting workers in the plant and site personnel while we clean up the building and prepare it for demolition.”
The new ventilation system is currently undergoing testing. When installed, the system’s exhauster units will be capable of moving up to 100,000 cubic feet of air per minute while filtering out contaminants, including naturally occurring radon. Workers will also replace the plant’s old sand filtration system, which was the last one to operate at Hanford, with high-efficiency particulate air (HEPA) filters that will use the facility’s existing ventilation stack.
“One of our main objectives was to replace the old sand filter technology with state-of-the-art HEPA filter technology,” said Bob Nichols, CPCCo inner area end states director. “An added benefit is that the new system was also designed for mobility and flexibility, so the exhauster units can be deployed to other buildings in the future, which will also cut costs. It’s a great example of the ingenuity of our team.”