EM’s use of replica components of a liquid waste treatment facility at the Idaho National Laboratory (INL) Site has proven effective.
Office of Environmental Management
February 23, 2021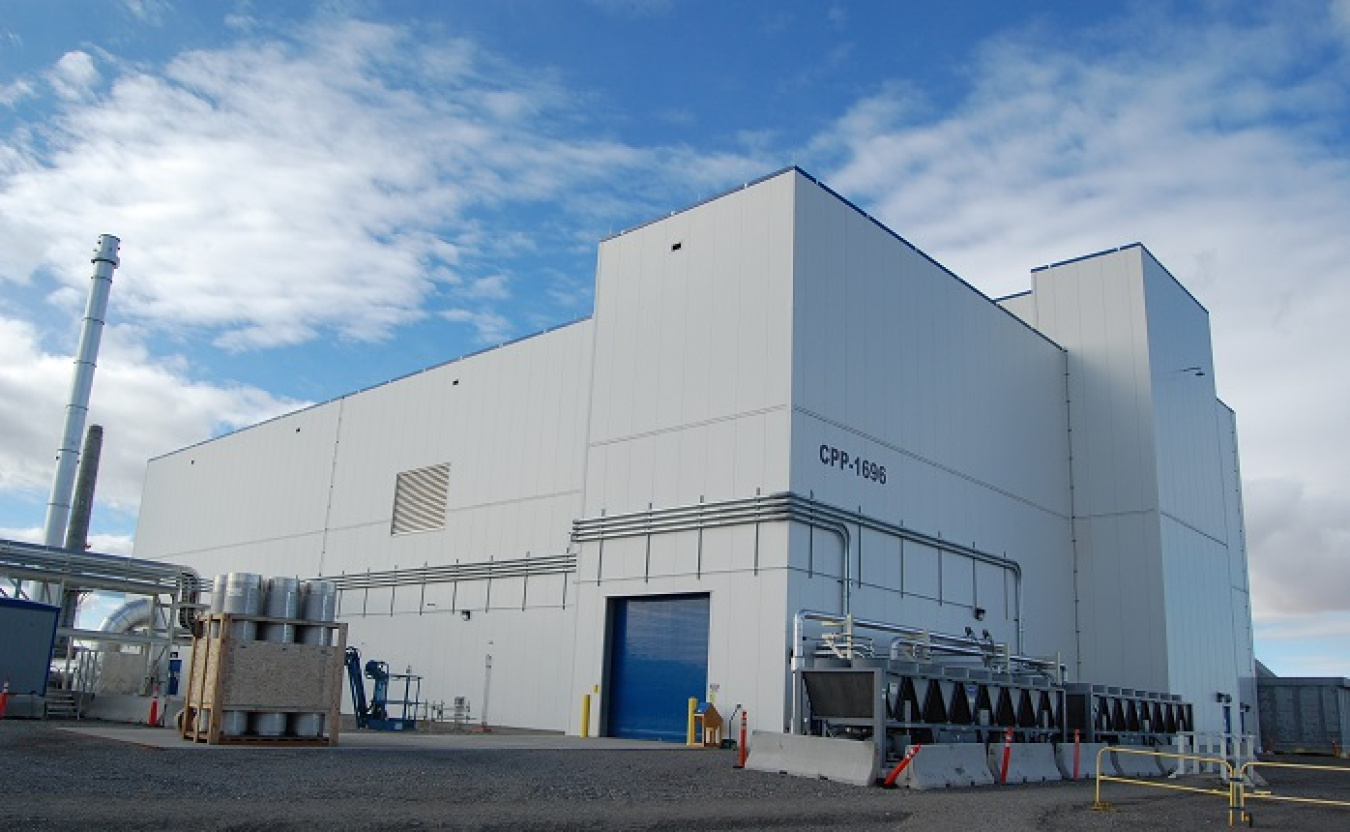
IDAHO FALLS, Idaho – EM’s use of replica components of a liquid waste treatment facility at the Idaho National Laboratory (INL) Site has proven effective in preparing for the facility’s active operations.
Diversified Metals, an Idaho Falls-based metal fabrication shop, erected a mock-up to prepare radiation protection technicians and operators with Fluor Idaho, EM’s INL Site cleanup contractor, for radiological work once the Integrated Waste Treatment Unit (IWTU) is operating.
“Using this mock-up not only allows our teams to develop and perfect the procedures they’ll use once the facility is processing actual waste, it also helps the teams develop safety measures and build in radiological controls,” Fluor Idaho IWTU Project Safety Manager Allen Nellesen said.
The IWTU was constructed to treat the remaining approximately 900,000 gallons of liquid waste from a nearby tank farm at the INL Site that accepted rinse water and other effluents from historic spent nuclear fuel reprocessing runs at the Idaho Nuclear Technology and Engineering Center. So far, the facility has treated more than 225,000 gallons of a simulant of the liquid waste in six demonstration runs.
Diversified Metals also built a mock-up to test flow control valves necessary for transferring liquid waste during operations. Engineers created a liquid slurry containing water and sand particles to simulate the liquid sodium-bearing waste that the IWTU was constructed to convert to a granular solid. The slurry was pumped through the valves to ensure they wouldn’t plug. Both the particle size and flowrate were modified during testing.
Nellesen said the tests using a mock-up were a success.
“We were able to determine that the valves will perform as designed and no flow restrictors would be needed,” he said.
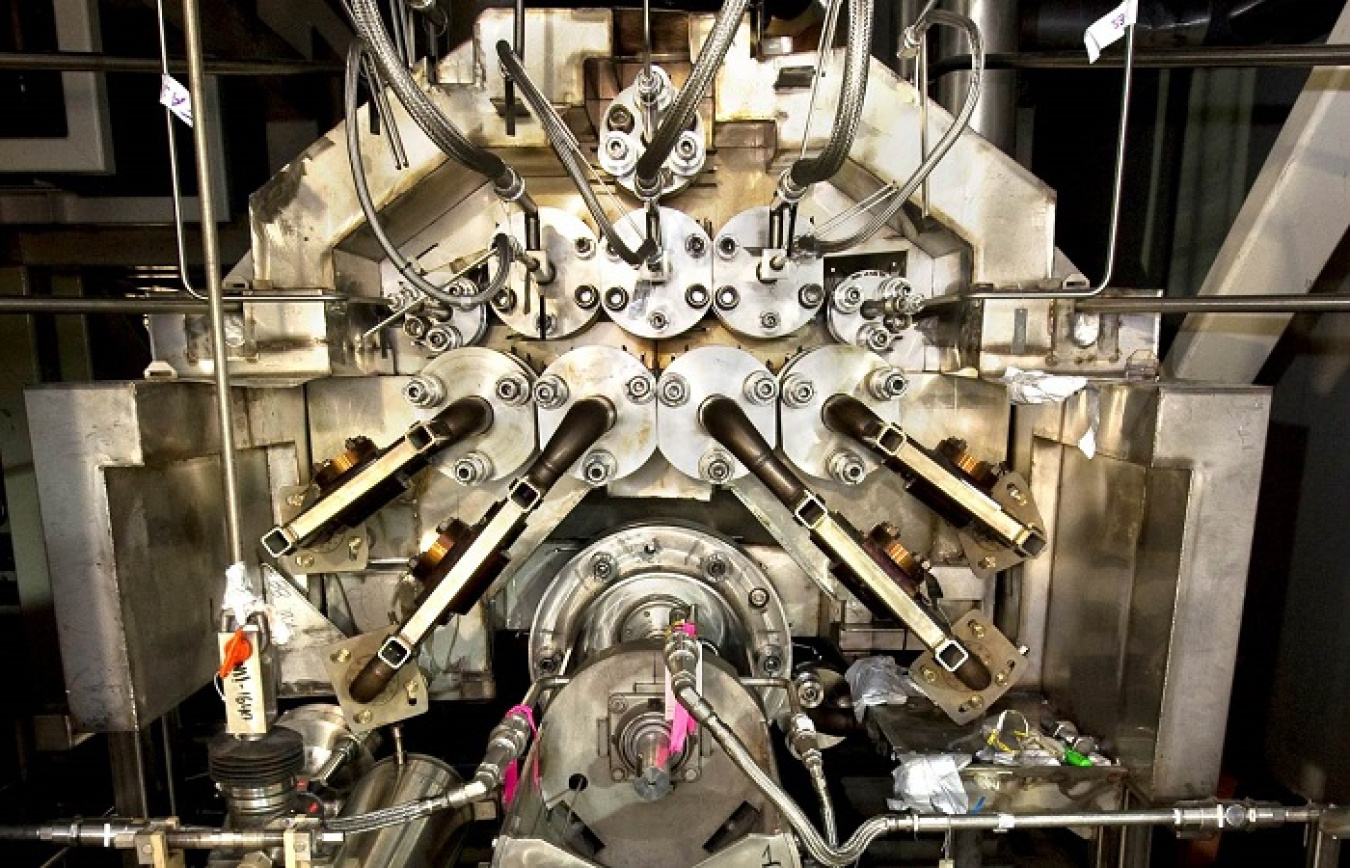
Diversified Metals also conducted mock-up testing on a decontamination system for dissolving dried waste in the Denitration Mineralization Reformer (DMR) — IWTU’s primary reaction vessel — and transferring the material to a holding tank.
The resulting slurry from that system would then be mixed in the tank to reduce its particle size to less than 800 microns — about twice the size of large coffee grounds — and eventually reinjected into the DMR.
Previously, the IWTU team used a mock-up of the DMR to test the facility’s auger-grinder, which pulverizes chunks of treated material and transfers the particles to other processes.
“We were able to test a more robust design for the auger-grinder using the mock-up and we knew in advance of installing it in the IWTU that it would be much more effective than previous designs,” Nellesen said. “Three demonstrations runs at the IWTU proved what we had learned in testing using the mock-up. We now have an auger-grinder that operates as designed.”
Following several modifications, the facility is scheduled to begin a 50-day confirmatory run this summer. Actual waste treatment will follow after readiness actions are complete.