An employee at the Savannah River Site recently discovered how 3D printers can create unique objects at a low cost to improve safety and operations.
Office of Environmental Management
September 8, 2020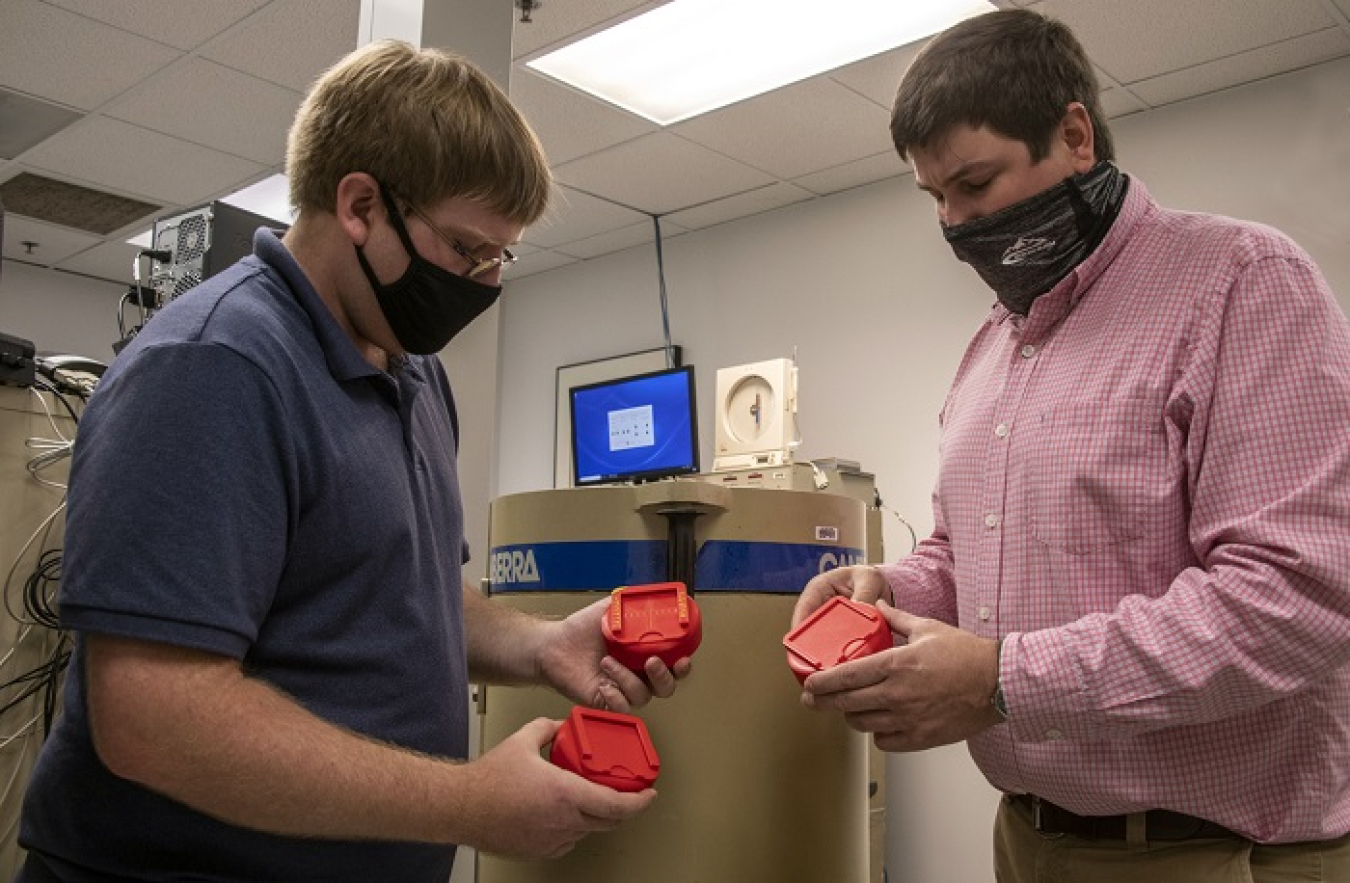
AIKEN, S.C. – An employee at the Savannah River Site (SRS) recently discovered how 3D printers can create unique objects at a low cost to improve safety and operations.
EM and Savannah River Nuclear Solutions (SRNS), the site’s management and operations contractor, analyze about 80,000 industrial air monitoring filters each year for radiological contamination within SRS nuclear facilities.
Known as a high-tech “radiological investigator,” Senior Health Physicist Michael Ratliff operates a laboratory at SRS where those analyses are completed.
Air filter analysis determines the source of radioactive particulates and helps measure possible airborne particulates within an operating facility. The process provides valuable data that can be used to monitor the health and safety of SRS employees working within nuclear facilities.
Ratliff said the circular filters sent to the laboratory for analysis are two inches in diameter on cards that are about three inches wide. Each card is packaged and delivered to the laboratory for analysis.
Recently, Ratliff sought the expertise of Andy Warren, who works at a laboratory within the SRNS environmental bioassay organization. That laboratory is used to analyze samples submitted by workers to assess possible occupational exposure to radiological substances and to ensure implemented hazard controls prevent occupational exposure.
Warren asked Ratliff how the cards are used in the high-volume equipment that processes the estimated 80,000 samples a year.
“I brought him one of the little fixtures used in the automated units,” Ratliff said. “To my surprise, the next day he provided a 3D printed part that fit perfectly on my counting instrument and holds the sample card exactly centered in a reproducible geometry.”
Ratliff noted that Warren’s solution improves the quality of data and reduces the time needed to prepare the analyses, all while enhancing radiological safety at SRS.
“When Michael contacted me and said, ‘I could use your help,’ we were already set up to create unique, one-off products using a computer-aided design program. It took about two hours to draft the part and send the design to the printer. The next morning, I came in, took it off the printer, and gave to Michael,” Warren said.
What use to take months at a design and fabrication shop can now be printed overnight at the site.
According to Warren, costs associated with 3D printing are low — approximately $7,000 for a printer and $2,000 for computer-aided design software.
“The fixtures made for Ratliff cost about $5 dollars each,” Warren said.