The U.S. Department of Energy (DOE) works with wind energy technology suppliers to promote advanced manufacturing capabilities. The goals are to increase reliability while lowering production costs and promote an industry that can meet all demands domestically while competing in the global market. The Wind Energy Technologies Office supports industry partnerships and targeted R&D funding that integrate new designs, materials, and processes into manufacturing facilities, thus making wind turbines a more affordable domestic energy source for communities around the country.
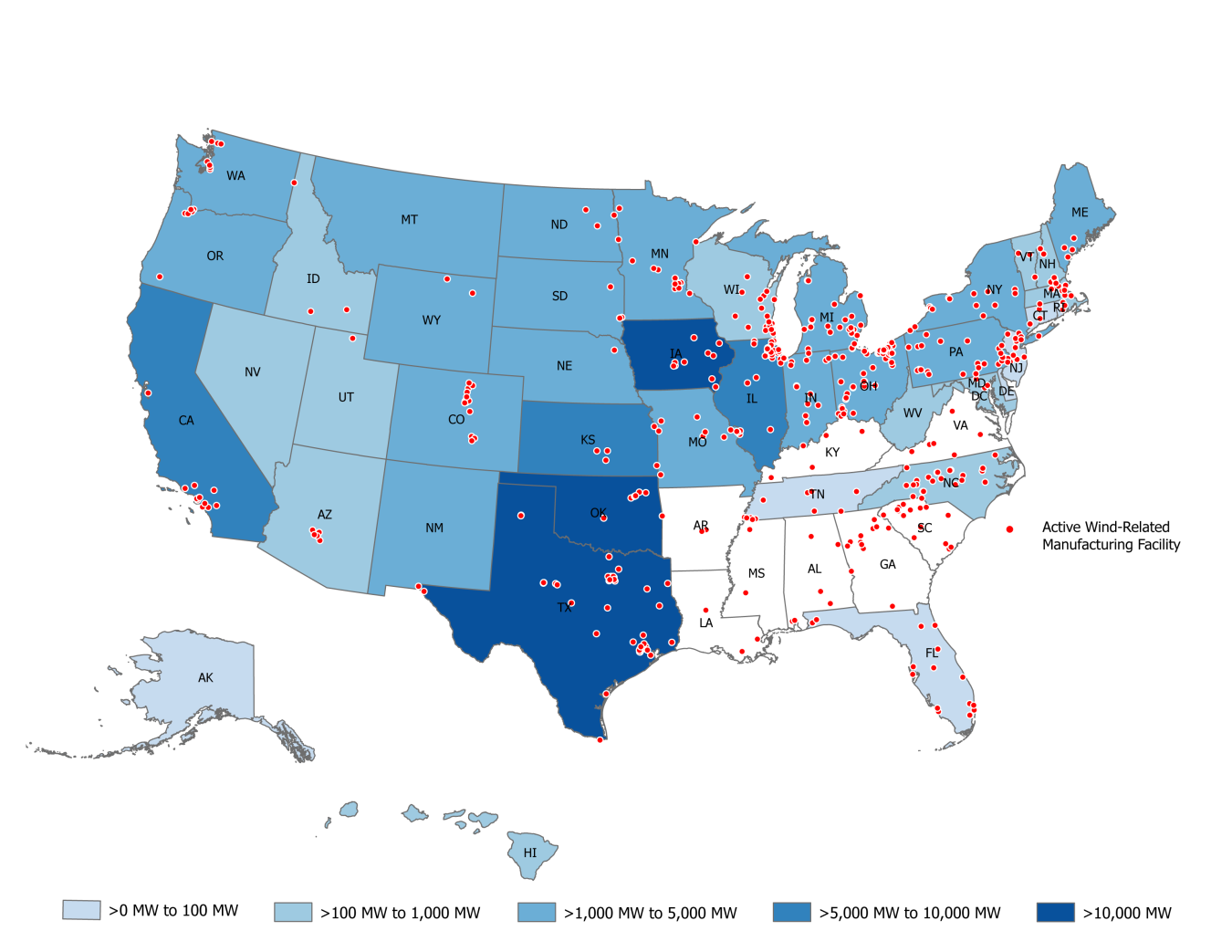
Read more about wind energy manufacturing and the supply chain:
Blades | Drivetrain | Infrastructure and Logistics
Manufacturing Is the First Step in Affordable Wind Energy
The U.S. wind market has grown substantially over the years into an increasingly complex supply chain. There are more than 500 U.S. manufacturing facilities specializing in wind components such as blades, towers, and generators, as well as turbine assembly across the country. In fact, modern wind turbines are increasingly cost-effective, reliable, and have scaled up in size to multi-megawatt power ratings. Since 1999, the average generating capacity of newly installed wind turbines has more than doubled to 3 MW.
Advancements in composite materials, automation, and more efficient manufacturing processes have helped domestic manufacturers dramatically increase productivity throughout the past decade. The wind supply chain that has developed in the United States in recent years has increased the domestic content of wind turbines installed in the United States, with over 80% of nacelle assembly and up to 70% of tower manufacturing occurring in the United States for turbines installed here.
As the size and complexity of wind turbines grow, so do the manufacturing process requirements and component transportation costs which, in turn, increase the need for local manufacturers who can overcome technical and logistical challenges. Currently, the average utility-scale wind turbine contains roughly 8,000 parts, including blades up to 100 meters (over 300 feet) in length and towers around 94 meters (308 feet) high, roughly the height of the Statue of Liberty. New towers are being made even taller to capture stronger winds at higher elevations.
In February 2022, DOE released a series of 13 reports on American manufacturing supply chains, reviewing both the obstacles to a reliable supply of key materials and opportunities for improvement. The wind report covers components, processed and raw materials, recycling, digital products, and the wind industry workforce. It discusses U.S. wind industry competitiveness, includes a supply-chain risk assessment, and lists opportunities for private-sector collaboration to address vulnerabilities and enhance competitiveness.
The open-source Renewable Energy Materials Properties Database, released in August 2023, provides a comprehensive compilation of the type, quantity, country of origin, source, significant uses, projected availability, and physical properties of materials used by wind (as well as solar) power technologies.
The Manufacturing Process
BLADES
Due to the size and complexity of turbine blades, each blade must be crafted to the highest quality standards in order to ensure reliability. This fabrication process can be very costly and labor intensive, but a partnership between DOE, Sandia National Laboratories, TPI Composites, and Iowa State University helped establish advanced techniques that reduce the time it takes to produce a single blade by approximately 37% (from 38 to 24 hours). DOE is also funding 3D printing of blade molds, which could save time and money during the blade development process. Turbine blades must be able to maintain their strength and aerodynamic structure during virtually non-stop operations over twenty years.
ADVANCED DRIVETRAINS
The tower-top components inside the nacelle that convert the force of the wind-driven rotor blades into electricity are called the drivetrain. Advanced designs and related manufacturing techniques developed in conjunction with DOE's Next-Generation Drivetrain projects are expected to produce more efficient, reliable, and affordable drivetrains. These advancements include new single-stage gearboxes, permanent magnet generators, high efficiency power electronics, and superconducting generators. In 2021, DOE awarded GE over $20 million in follow-on funding to build and test a prototype of their high-efficiency ultra-light low temperature superconducting general (SCG) on a wind turbine. New and innovative approaches to drivetrain manufacturing will continue to be necessary as turbine components continue to increase in size and energy capacity in response to market demand.
INFRASTRUCTURE AND LOGISTICS
As the demand for renewable energy increases and wind turbines are "scaled-up" to ever larger sizes, American manufacturers must find ways to overcome infrastructure and logistics constraints to lower the cost of wind energy. These constraints include highway underpass heights limiting the size of wind towers, availability of cranes able to lift and install nacelles, and the trucking fleet's difficulty in transporting longer wind blades. A study released by the Energy Department, Enabling Wind Power Nationwide, concluded that the technological innovations enabling development of very large wind turbines have significant potential to reduce the cost of wind energy. However, transportation and logistics challenges are limiting the size and height of towers and turbines that can be deployed throughout the country. Two companies are addressing these challenges by developing innovative manufacturing techniques, with the help of funding from DOE: Keystone Tower Systems uses spiral-welding in order to minimize the need for costly steel, and GE Renewables is experimenting with 3D printing to create customizable tower bases.
Supply Chain
The National Renewable Energy Laboratory led the 30 GW by 2030: A Supply Chain Road Map for Offshore Wind in the United States project to create a road map that identifies challenges and solutions to developing a nationally focused offshore wind energy supply chain that has the potential to manufacture all major components domestically by 2030.
Stay informed by receiving the latest wind energy news, events, and updates.
Wind Manufacturing and Supply Chain News
-
Report suggests investing in strategies and innovations to process the remaining 10%, supporting reuse and recycling.
-
The Small Business Innovation Research (SBIR) and Small Business Technology Transfer (STTR) programs offer competitively awarded grants to small businesses to support scientific excellence and technological innovation.
-
The U.S. Department of the Treasury and the IRS released final rules for the Advanced Manufacturing Production Credit (Section 45X of the Internal Revenue Code), to spur continued growth of U.S. renewable energy manufacturing.
-
Six teams were selected for creating cost-effective recycling technologies for U.S. wind energy systems.
-
While studying mechanical engineering at the University of Texas in Austin, Paquette became interested in structural components and composite materials. Although he originally planned to pursue work in the aerospace industry, he jumped at the opportunity to work at Sandia on wind turbine blades—the largest composite structures in the world.
-
The Wind Energy Technologies Office (WETO) has funded the blade and drivetrain testing facilities since the 1990s, providing crucial knowledge and expertise to the ongoing expansion of commercial wind power—both domestically and globally.
-
The U.S. Department of the Treasury and Internal Revenue Service released additional guidance on the domestic content bonus provision enacted by the Inflation Reduction Act.
-
The Office of Manufacturing and Energy Supply Chains requests information on renewable energy supply chain data and analysis methods.
-
This proposed funding opportunity aims to improve mooring technologies and methods, which are used to secure floating platforms to the sea floor, for both the U.S. and Denmark.
-
Learn about recent guidance from the Internal Revenue Service on the advanced manufacturing production credit, which includes a new section that that offers benefits for wind energy technology manufacturers.