While the blades of a turbine may be one of the most recognizable features of any wind installation, they also represent one of the largest physical challenges in the manufacturing process. Turbine blades can reach up to 100 meters (328 feet) in length, and will continue to increase in size as the demand for renewable energy grows and as wind turbines are deployed offshore. Because of their size and aerodynamic complexity, wind turbine blades are skillfully manufactured by hand to ensure the highest level of craftsmanship and to outfit wind turbines with the most reliable and efficient components.
Advanced Manufacturing Initiative
In conjunction with various state and industry partners, the U.S. Department of Energy's Advanced Manufacturing Initiative funded various research projects aimed at dissecting and analyzing the manufacturing process. The research obtained throughout the Initiative is expected to lead to novel and innovative approaches that will streamline the blade manufacturing process.
Examples of Innovations Produced by the Advanced Manufacturing Initiative for Blades
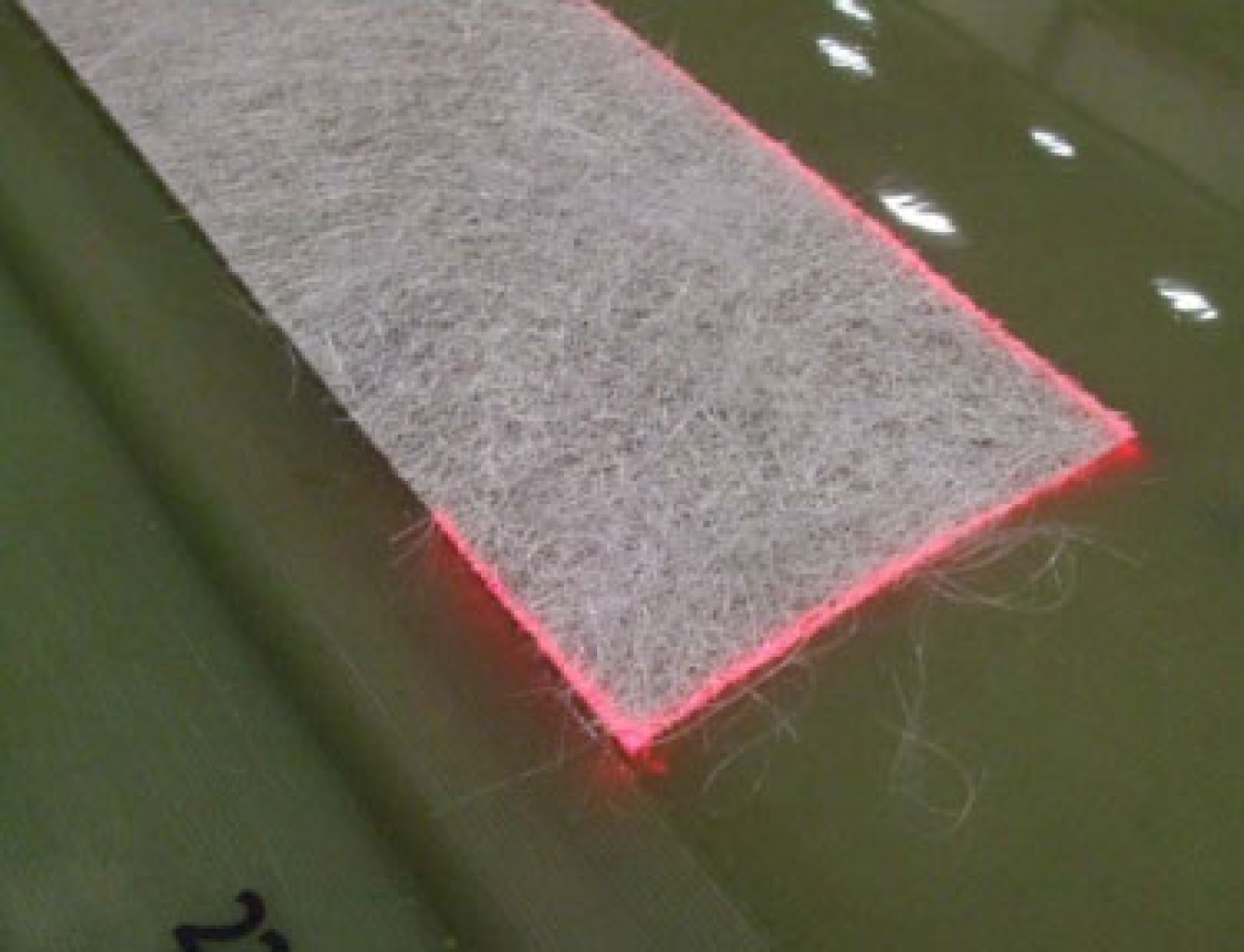
A laser guideline is projected onto a turbine blade during the manufacturing process via a series of ceiling mounted projectors.
Image from Sandia National Laboratories
- The time it takes to produce a single turbine blade will be reduced by 37% (38 to 24 hours)
- Advanced carts and material handling systems were designed to rotate a blade 270 degrees, reducing the number of times a blade must be moved throughout the manufacturing process
- New heating techniques were developed to reduce the amount of time that composite materials take to cure
- New component handling systems were designed to aid in the installation of large, cumbersome parts
- New 3D-projected blueprints will be implemented in order to reduce the amount of time it takes for workers to identify the correct location for the installation of fixtures and connecting hardware. These blueprints will be displayed from overhead through a unique system of projectors and lasers.
Strength and the Need for Stronger Composite Materials
An increase in the demand for renewable energy has led to the production of larger turbine blades capable of harnessing more wind energy. This increase in size has brought with it a need for stronger composite materials that effectively retain their shape and strength when subjected to varying wind conditions, as well as other physical and environmental stressors. As the total electrical output of a turbine partially relies upon the efficiency at which air is able to move across a turbine blade — causing the blades to rotate and the gears to spin — it is crucial that the surface quality of each blade stays pristine throughout its lifetime. While an installation site may present a unique obstacle such as ice and frigid temperatures, all blades are typically designed to stand up to constant exposure from the sun, sea, sand, and wind. New composite materials are currently being developed that will increase the lifespan of a turbine blade, improve the manufacturing process, and contribute to the overall efficiency of turbine systems. This is just another example of how a successful turbine begins with the manufacturing process.
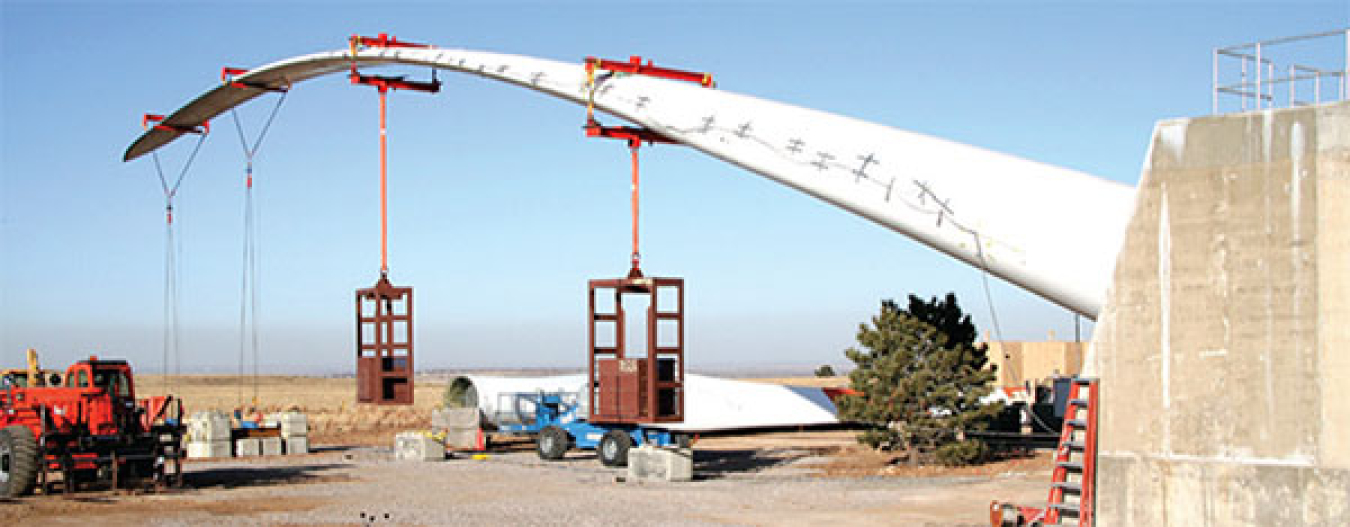
A 44.5-m wind turbine blade undergoes stress testing at the National Wind Technology Center. Image from NREL
Blade Reliability Collaborative
The Blade Reliability Collaborative (BRC) collects data from blade manufacturers and other industry professionals, and organizes the data in a central database accessible by component manufactures, researchers, and developers. Maintaining a central database for blade research has allowed manufacturers to collaborate and produce a more efficient and reliable wind turbine blade. The BRC is composed of educational institutions, government labs, over 40 manufacturers, and service providers.