Advanced control of LED lighting systems in parking lot applications offers the promise of energy savings and other operation benefits. However, NGLS evaluations of six different systems identified that there are significant challenges to successful installation and operation of these systems, particularly with presence detection.
INSTALLATION AND COMMISSIONING
Overall, installation and commissioning were complicated by the complexity of the systems and the level of manufacturer support needed. System installation and configuration ranged from reasonably successful to outright failure. While it should be noted that several of the systems incorporated new technologies and were not standard product offerings, all six systems had configuration issues, as well as issues with either wiring or programming the occupancy sensors. Two systems required replacement of failed hardware, and two had problems with gateway communications.
All six systems were found to be problem-free as far as scheduling was concerned. Four of the systems dimmed adequately by the time NGLS formally evaluated system performance, although only two did so at initial startup. However, many of the systems required multiple electrical contractor callbacks, which included multiple rides in a bucket truck to reach the luminaires and get the systems working – potentially adding considerable time and expense for building owners.
System |
Number of Luminaires |
Number of Occupancy Sensors |
Call Backs |
Bucket Truck Lifts |
Lift/ Luminaire |
Estimated Troubleshooting Hours by Owner |
Number of Days from Installation to Full Function |
1 | 6 | 6 | 2 | 9 | 1.5 | 3 | 3 |
2 | 8 | 8 | 4 | 19 | 2.4 | 20 | 40 |
3 | 5 | 3 | 5 | 8 | 1.6 | 16 | 50 |
4 | 11 | 14 | 2 | 3 | 0.3 | 30 | 15 |
5 | 11 | 11 | 6 | 50 | 4.5 | 32 | unknown |
6 | 8 | 4 | 3 | 12 | 1.5 | 16 | 60 |
Configuration of the occupancy sensors (as distinct from the central control functionality of scheduling and dimming) was a major challenge. In fact, the majority of installation and configuration issues encountered related to presence-detection hardware. The sensors and their nodes did not always work together, and system integration was typically problematic.
OPERATION
Overall, once installed and fully configured, the control systems worked for the most part, doing a good job of scheduling, dimming, monitoring, and reporting. However, none of the six presence-detection systems performed successfully. Initial startup was an issue with most of the systems. There were wiring issues and false triggering, and occupancy groups were either not configured or were not saving correctly in the system software. In some cases, sensitivity levels were not set correctly.
All six systems had issues with occupancy sensitivity or latency; again, it was often difficult to tell which issue was the culprit. Only one system had fully functioning occupancy sensors at startup, and none of the systems showed reliable, consistent presence detection during the performance evaluations.
Infrared technology appears to have significant limitations in outdoor applications, and issues related to latency, sensitivity, and coverage are intertwined, which creates a “perfect storm.” In many cases, the measured detection range did not meet the range predicted by manufacturer sensor specification sheets.
The outdoor environment poses challenging real-world conditions for passive infrared (PIR) sensors. Mounting heights can range from 20 to 40 feet. Both pedestrians and vehicles need to be detected, but these move at very different speeds. Outdoor temperatures can vary from very hot to very cold throughout the year, and the differential temperature between the environment and cars and pedestrians will vary accordingly. With these significant challenges, it is fair to ask if infrared technology can be successfully and reliably used in the outdoor environment.
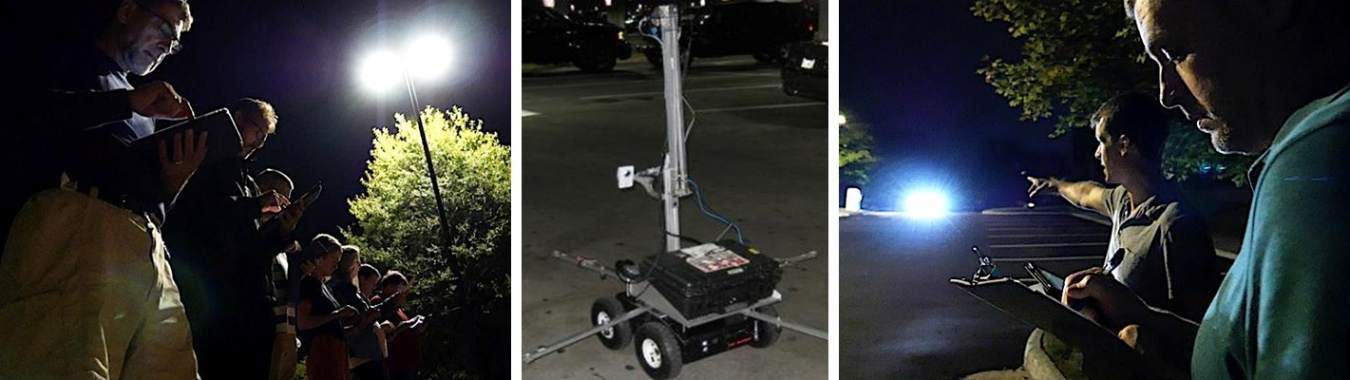
USER ACCEPTANCE
While all working systems successfully provided monitoring capabilities, the user interfaces could use improvements in order to meet users’ actual needs, especially in the case of more-advanced users who need more engineering data or detailed status indications. In order to ensure that these systems continue to work properly, manufacturer support is not only necessary, it is critical – as it is throughout installation and configuration.