A total of 14 connected lighting systems were installed in functioning classrooms at The New School, Parsons School of Design, with each system lighting its own classroom to a common lighting and control specification. The systems provided lessons and insights, from installation and commissioning challenges through ongoing performance, system maintenance, and user feedback.
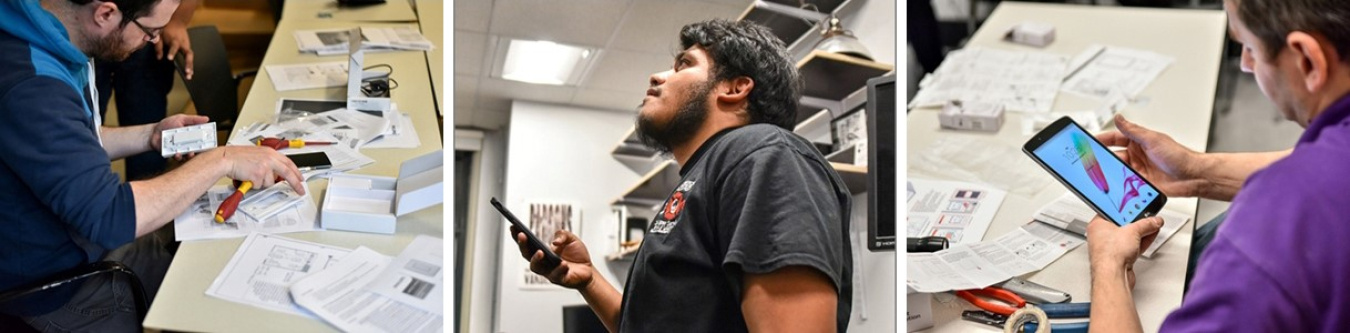
Key observations:
Marketing claims of “easy to install and configure” are overstated. For the small- to mid-size market – especially retrofit applications – simplicity is key. To a remarkable degree, the simplest systems installed more easily, configured more reliably, and operated more intuitively than those with more functionality and complexity.
Communication is critical. Success in installation, configuration, and operation benefits significantly from good communication. This is all-encompassing and includes complete specifications, clear installation and configuration instructions, coordinated jobsite teamwork, readily available tech support, and intuitive labeling. The area of communication offers an opportunity for rapid improvement.
Standards are needed. We have yet to see products coalesce around common forms, configuration methods, or even wall controls. The lack of commonality slows learning, adoption, and energy savings.
Information conveyed during preconstruction collaboration often does not get communicated to the installers who are doing the work. Even when the information is there, much of the time it is not carefully read, especially when it comes to seemingly familiar tasks such as wiring or installing a luminaire.
Troubleshooting connected lighting systems is essentially an IT task. Multiple devices (luminaire, switch, gateway), software/firmware updates, system versions, and connectivity all play a role in the process.
Installers rely on experience rather than on printed instructions. However, they quickly learn new ways to do things.
Installer training increases the likelihood of successful system installation and configuration. But even so, manufacturer assistance may still be needed, even on “easy-to-install” systems.
The systems don’t always perform to specification. Light levels and manual dimming are easy to measure, and most systems succeeded in those areas. But verifying vacancy operation and daylight harvesting takes more – and careful – evaluation, and the results to date leave much to be desired. This is not only a question of return on investment and code compliance; it’s also crucial to energy savings.
Performance is often difficult to verify. That’s because a programming issue can be hard to differentiate from a hardware issue.
A common vocabulary is needed. Everyone involved – including owners, designers, contractors, manufacturers, IT engineers, and facility managers – is speaking a different language, which makes it hard to communicate.
Wall control design should be carefully considered by manufacturers, keeping the user in mind. Users are often confused by the wall controls of their systems.
Replacement parts are not readily available. Replacement parts are not available at your local distributor/retailer, so it can take a long time to get a system back to full operation.
Reconfiguring a system can be as difficult as initial configuration. Often a specific sequence is required to delete or add new equipment, and any deviation from the sequence can throw off the entire system.