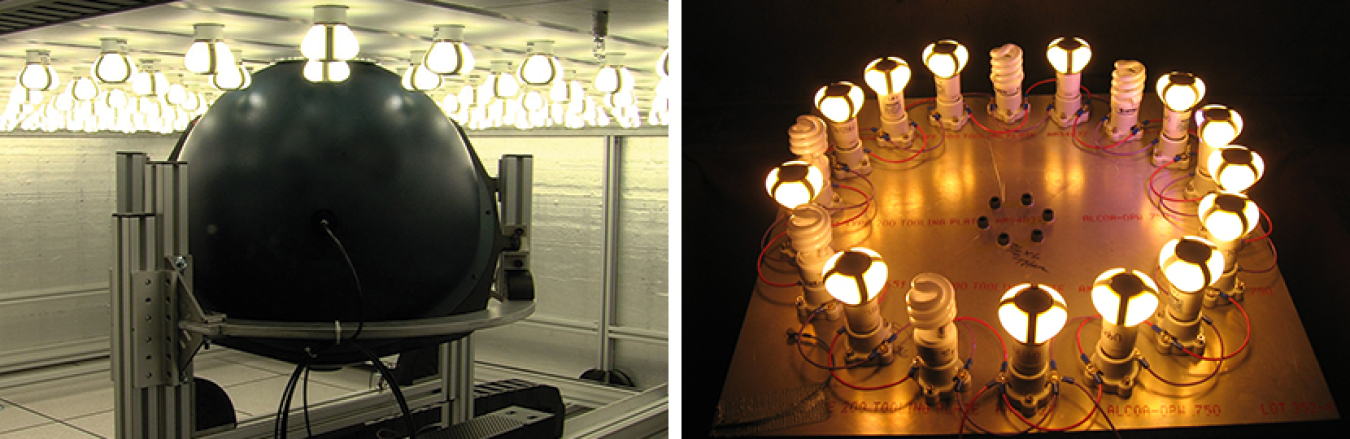
Left: Long-term testing of the L Prize entry was conducted in a specially designed high-temperature test bed. Right: Multi-level stress testing was conducted alongside benchmark CFLs.
The L Prize entry went through an extensive laboratory testing process to ensure that the winning product met the competition's stringent requirements in areas including exceptional efficacy, long life, form factor, and suitability for mass manufacturing. A Technical Review Committee (TRC) reviewed all reports, test results, findings, and documentation for the Philips entry, and determined that it met the requirements.
Short-Term Testing
In Spring 2010, the Philips 60W replacement entry completed the first stage of the evaluation process: photometric testing. More than 200 samples of the product were subjected to LM-79 procedures measuring luminous flux, intensity distribution, correlated color temperature and chromaticity, color rendering index, and power factor. Instrumentation used in the testing included an integrating sphere and goniophotometer. Testing was conducted at two qualified labs: Independent Testing Laboratories, Inc., in Boulder, Colorado, and OnSpeX/CSA International in Atlanta.
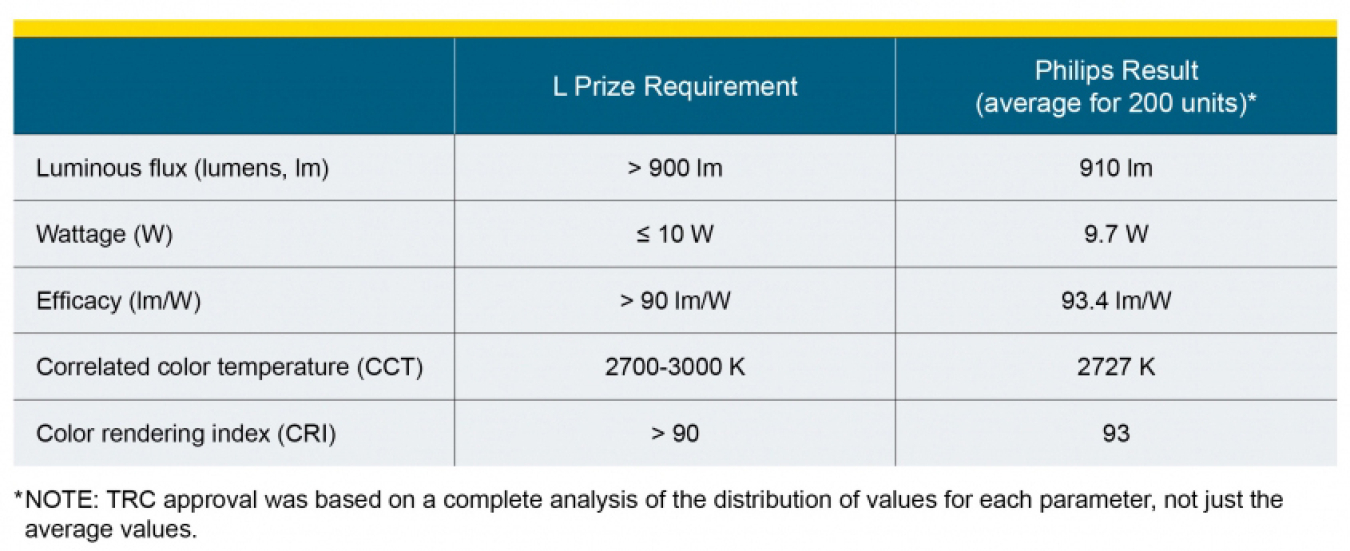
Long-Term Testing
In June 2010, the next stage of evaluation began: long-term lumen maintenance testing. The 200 samples were sent to Pacific Northwest National Laboratory to be tested in a new high-temperature testing apparatus specifically designed for the L Prize competition and built with assistance from Orb Optronix. The test bed was maintained at 45°C to simulate actual operating conditions and the lamps were operated continuously. A movable integrating sphere (light measurement device) took spectral measurements on each lamp every 100 hours for the first 3,000 hours of operation, and every 168 hours (weekly) thereafter. Data for the first 7,000 hours of operation were used to predict lumen maintenance of the lamps at 25,000 hours. With 95 percent confidence, lumen maintenance was predicted to be 97.1 percent* at 25,000 hours, which significantly exceeded the 70 percent L Prize requirement. DOE continued testing of the 200 samples through the 25,000 hour mark, to take advantage of the first public opportunity to confirm actual performance of a high-quality LED lighting product. At 25,000 hours of testing, the actual lumen maintenance was 100%, and chromaticity change remained less than .002.
A selection of 31 of those lamps passed the 60,000-hour point of continuous operation in September 2017. Their average lumen maintenance was 95.0%, with no failures, and the average chromaticity change was 0.002. These results show that well-designed LED integral lamps can operate very reliably over long periods of time, with excellent lumen and chromaticity maintenance, and validate the methods being used for predicting performance.
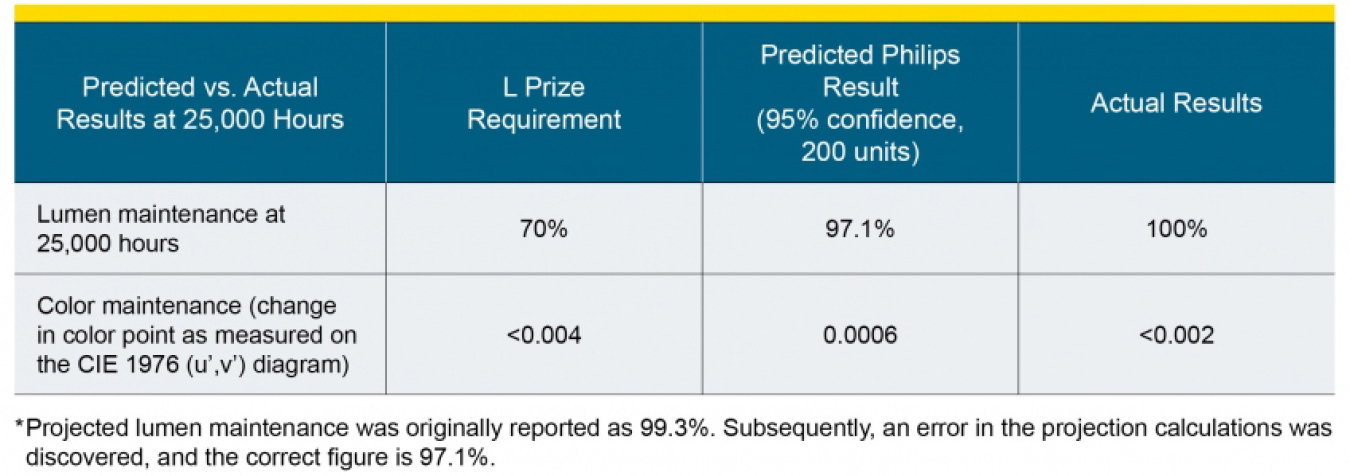
Stress Testing
Independent stress testing was conducted by Intertek Laboratories using a proprietary method called Failure Mode Verification Testing (FMVT). This stress testing consisted of a simultaneous combination of electrical, thermal, vibration, and humidity stresses which were increased over 14 stress levels. Tests were benchmarked against good-quality, commonly available 60W replacement compact fluorescent (CFL) lamps. Throughout the testing, photometric performance was conducted to assess any changes in performance as well as failures.
During 10 levels of increasing stressors, including extreme maximum and minimum temperatures, vibration, high and low voltage, high humidity, and various electric waveform distortions, two-thirds of the CFLs included in the tests failed, but none of the Philips L Prize lamps failed. The remaining CFLs failed upon additional incremental stressing, while the Philips L Prize lamps continued to operate.