Bioprose Blog: National Renewable Energy Laboratory (NREL) researchers can accurately predict reaction rates and optimal conditions for making biofuels. Their secret? Complex math to sketch the intricate chemistry and physics that drive catalytic fast...
August 6, 2021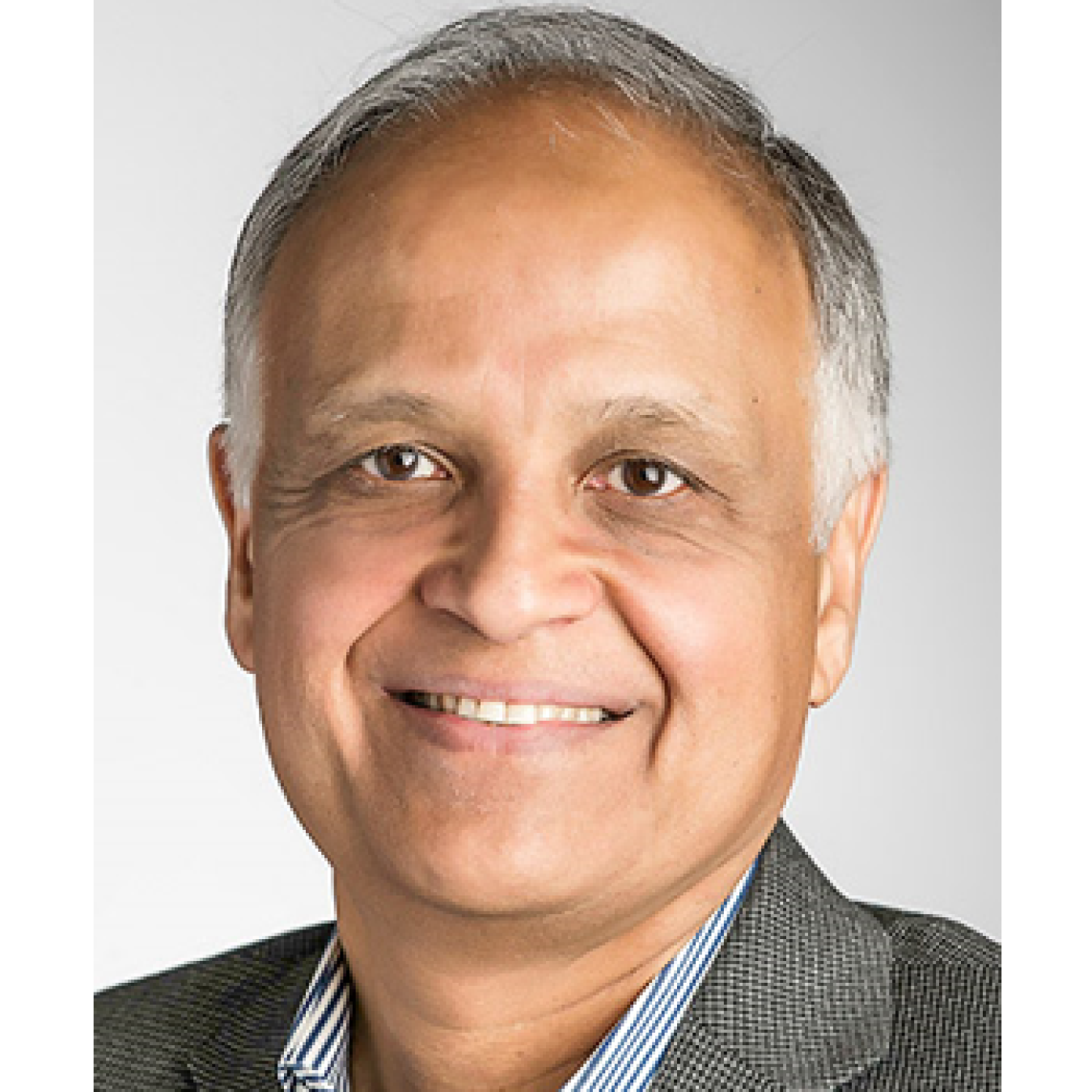
Author: Zia Abdullah, Laboratory Program Manager, National Renewable Energy Laboratory
Read Zia's bio ►
Meet the other bloggers ►
Return to Bioprose blog ►
National Renewable Energy Laboratory (NREL) researchers can accurately predict reaction rates and optimal conditions for making biofuels. Their secret? Complex math to sketch the intricate chemistry and physics that drive catalytic fast pyrolysis.
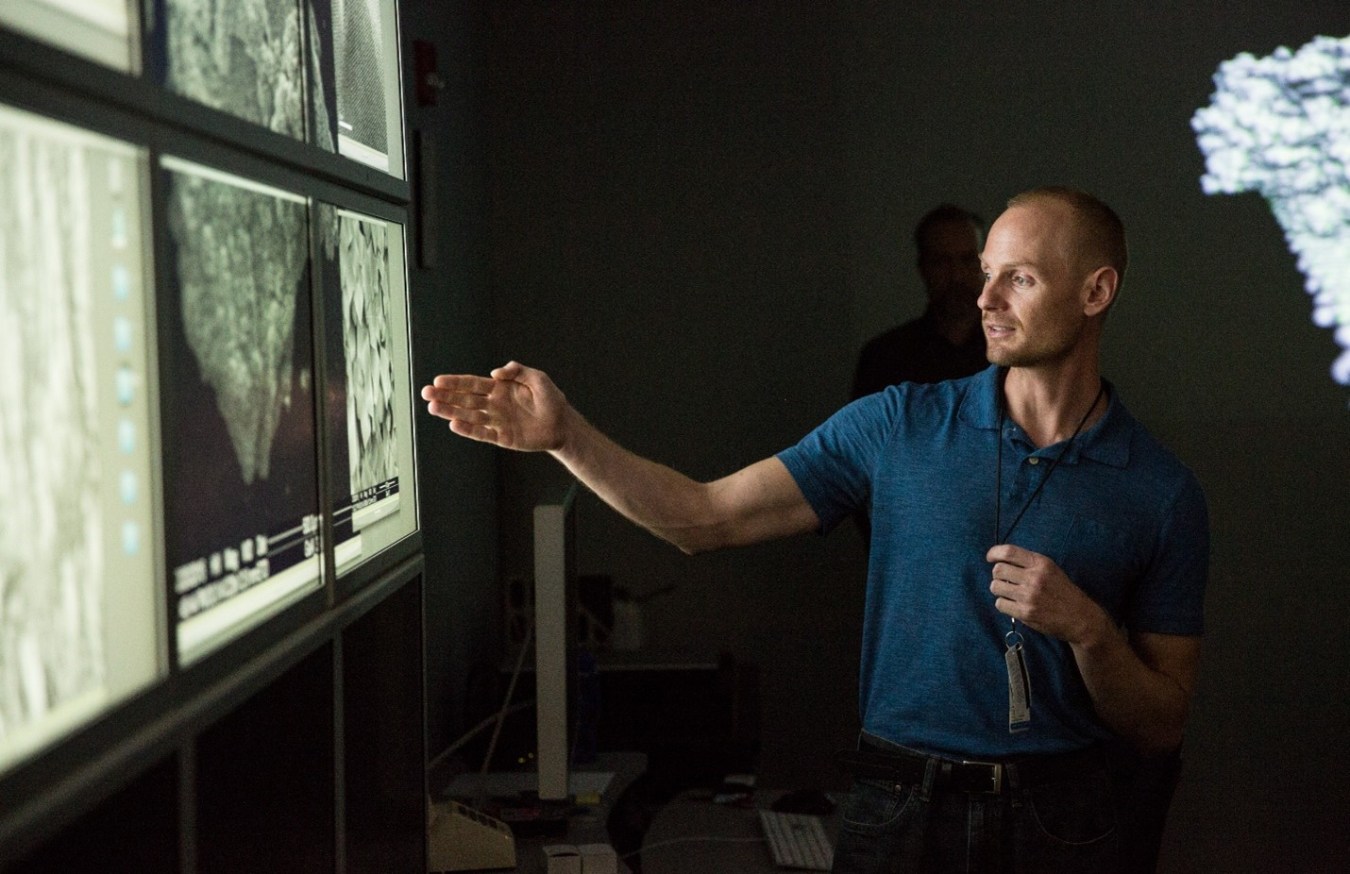
Figure 1: NREL researchers, including Peter Ciesielski pictured here, uncover insights on catalytic fast pyrolysis to help the bioenergy industry improve their processes for producing affordable chemicals and fuels. Photo by Werner Slocum, NREL
Catalytic fast pyrolysis (CFP) reactors transform the renewable carbon in forestry slash, farm waste, and even garbage into a range of renewable fuels, chemicals, and materials.
They accomplish this with high heat that vaporizes, or “pyrolyzes,” biomass in the absence of oxygen, as well as tubes filled with millions of catalyst particles—which greatly accelerate desired chemical reactions.
But the chemistry behind such transformations can be astoundingly complex. Understanding the basic chemical and physical interactions between vaporized biomass and CFP catalysts is critical to answering industry questions on the best methods to build cost-effective biofuel refineries.
What sets a highly effective CFP reactor apart from its peers? Why might one CFP catalyst help yield barrels of low-carbon biofuel when another produces only a trickle?
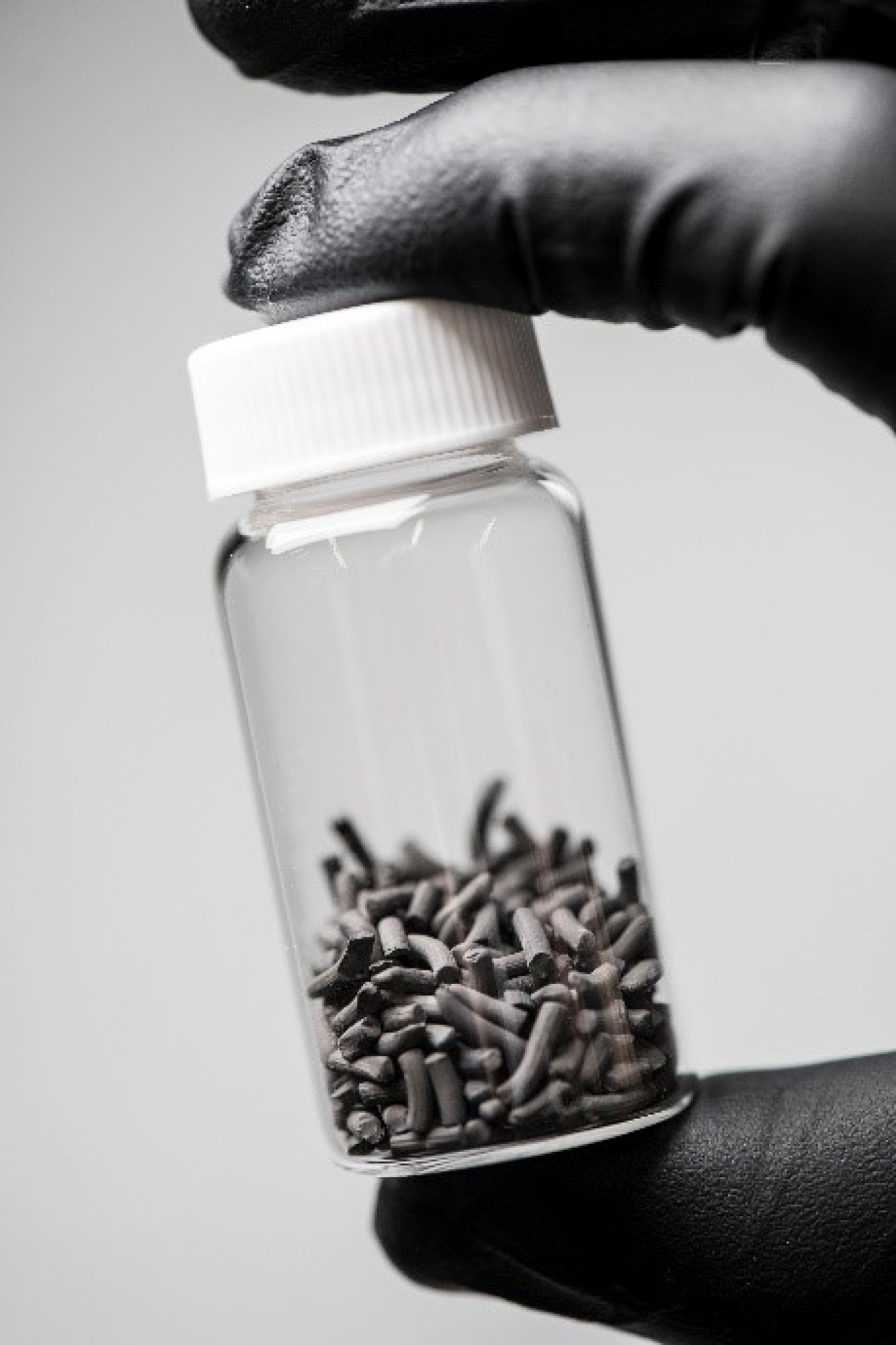
Figure 2: Platinum on titania (Pt/TiO2) catalysts use tiny amounts of platinum deposited on porous titanium oxide particles. Photo by NREL
Some metal-acid catalysts like platinum on titania (Pt/TiO2) are especially effective at converting the vapors made from pyrolysis into precursors for liquid hydrocarbon fuels, such as aviation and marine fuels. Still, even small changes to the design of a CFP reactor—or the arrangement and chemical makeup of the Pt/TiO2 catalysts inside—can lead to big changes in the composition and quantity of the final fuel.
NREL’s Clever Math Reduces Biofuel Production Uncertainty
For industries looking to scale fuel production with CFP technologies, fuel composition uncertainty could shut the door on prospects of building a solid biofuel business. After all, to guarantee consumers a dependable price point for their fuel, biofuel companies need reliable processes verified with precise science.
NREL scientists, including Brennan Pecha and Peter Ciesielski, are giving industry engineers a helping hand with a powerful computer model to guide biomass-to-fuel reactor designs. As described in a Reaction Chemistry and Engineering article, this math-intensive model proves highly accurate at predicting the reaction rate of CFP reactors that use Pt/TiO2 catalysts.
The breakthrough can enable engineers to refine CFP technologies to harness the full potential of the specialized catalysts, a steppingstone toward better, more affordable biofuels.
On a more fundamental level, the knowledge gained from building and validating the model can be brought to other processes and catalysts in the future.
One Model Describes a Cascade of Chemical Reactions
The team leveraged a powerful scanning electron microscope to “map” the structure of the Pt/TiO2 catalyst at a scale many times smaller than the width of a human hair. Having noted the microscopic architecture of the catalyst, they conducted experiments with it in a lab-scale CFP reactor, feeding the vapors from pyrolyzed pine slash through the catalyst to observe its transformation into “upgraded” bio-oils.
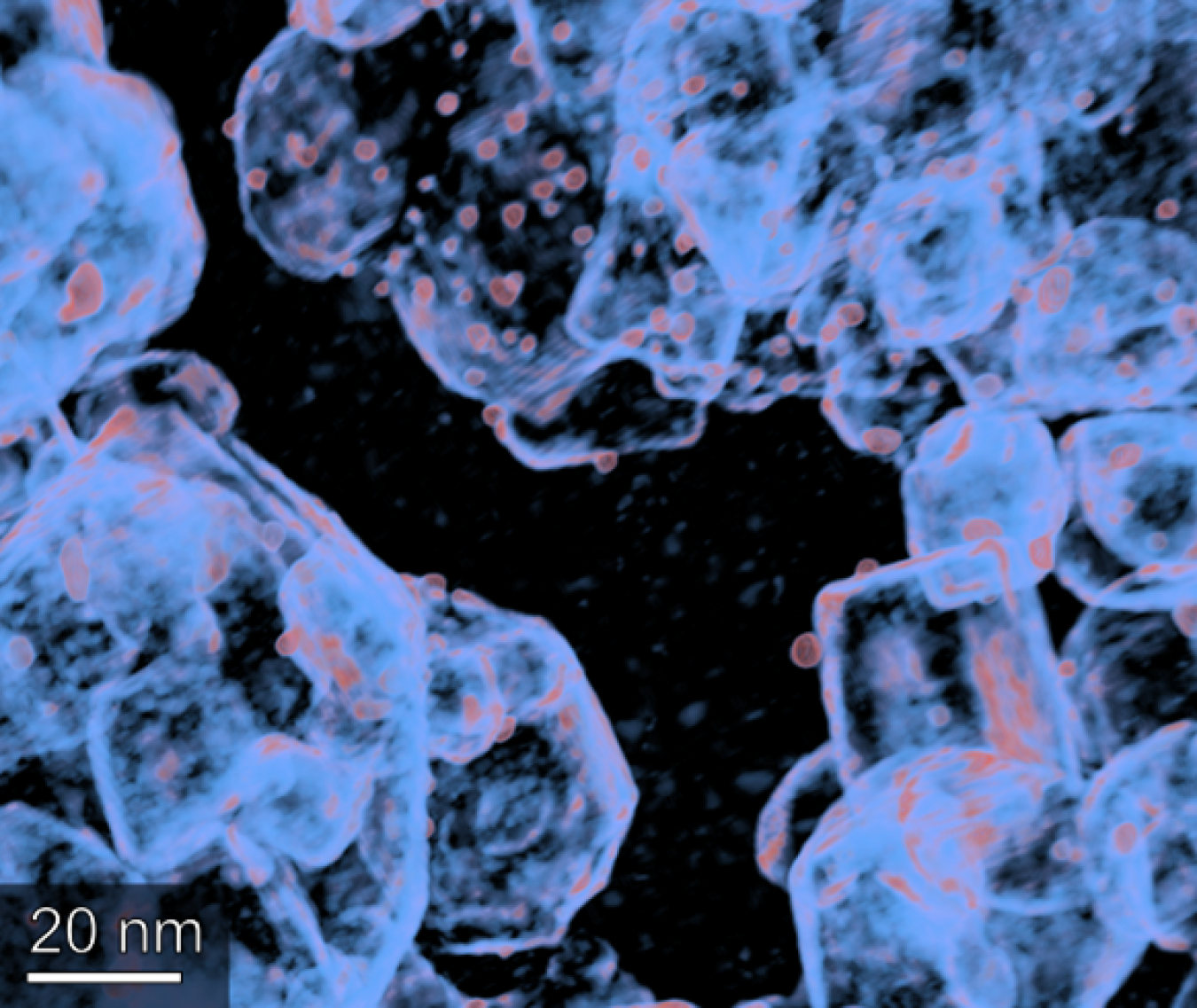
Figure 3: NREL researchers used transmission electron tomography to capture the 3D nanostructure of a Pt/TiO2 catalyst. By examining the architecture of TiO2 (shown in light blue) and Pt particles (shown in orange), the team could construct a more accurate model. Photo by Peter Ciesielski, NREL
With this understanding of the catalyst’s physical structure and comprehensive data from the CFP experiment, the team derived mathematical equations to describe the physical transport of vapors within the reactor as they underwent a cascade of chemical reactions.
The math accounts for static parameters like reactor bed length and catalyst bead diameter. It also considers less predictable factors, such as the dance of gases as they move through the latticework of atoms in the porous catalyst.
It’s no surprise—the math is as complex as the reaction itself. But that intricate model yields simple answers about the tunability of the chemical reactions.
Accuracy the Biorefinery Industry Can Depend On
In what could help the biorefinery industry, the model enabled NREL researchers to predict the reaction results, such as how many energy-dense fuel molecules formed and the quantity of carbon deposits on the surface of the catalyst.
In fact, NREL’s mathematical model was so effective that the team could modify a range of process conditions—the arrangement of catalysts in the reactor and variations in the biomass—and still predict the reactor output. A follow-up paper took these results a step further to predict how a much larger reactor would behave and how to properly burn off the carbon deposits, commonly called “coke,” that built up during the reactions.
This advance is critically important for an industry that measures success in barrels of biocrude, liters of chemical byproducts, and dollars per gallon of fuel. Biofuel companies need a clear understanding of CFP chemistry to confidently grow a business in affordable, low-carbon biofuels.
With this robust, reliable model in hand, NREL can continue laying a scientific foundation that helps the bioenergy industry tailor their CFP technologies to produce affordable chemicals and fuels.
Dr. Zia Abdullah
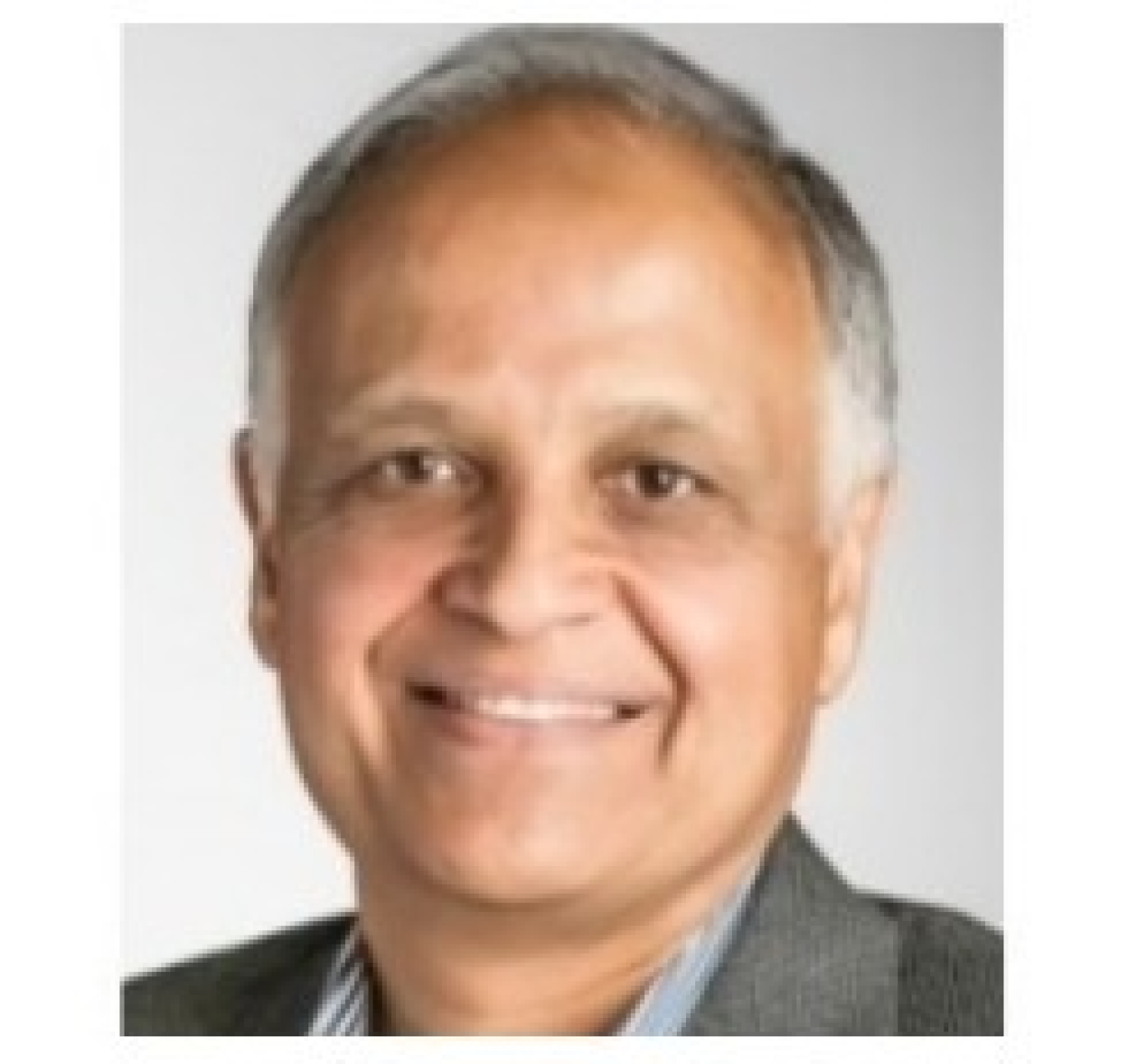
Dr. Zia Abdullah is laboratory program manager for the National Renewable Energy Laboratory’s (NREL’s) Bioenergy Technologies Office program.
Zia has extensive experience and accomplishments in thermochemically and biochemically converting biomass to fuels and chemicals. His experience includes more than 25 years of industrial research and development in biomass conversion, as well as problem solving, new product development, business development, and project management.
Prior to joining NREL, Zia was chief technology officer at Versa Renewables LLC, where he developed and commercialized biomass pyrolysis and biopolyol technologies. Before Versa, Zia served as one of the Battelle Memorial Institute’s 11 fellows, leading the development of technology and commercial application for fuels, chemicals, and materials from the thermochemical and biochemical conversion of biomass. Prior to working at Battelle, Zia was a research advisor (fellow) at Weyerhaeuser Company, where he worked on challenges related to manufacturing and biomass valorization.
Meet our other bloggers ►
Return to Bioprose blog ►