Bioprose Blog: Since the dawn of the industrial age, petroleum-based chemicals and fuels have driven countless inventions and products used every day.
March 24, 2020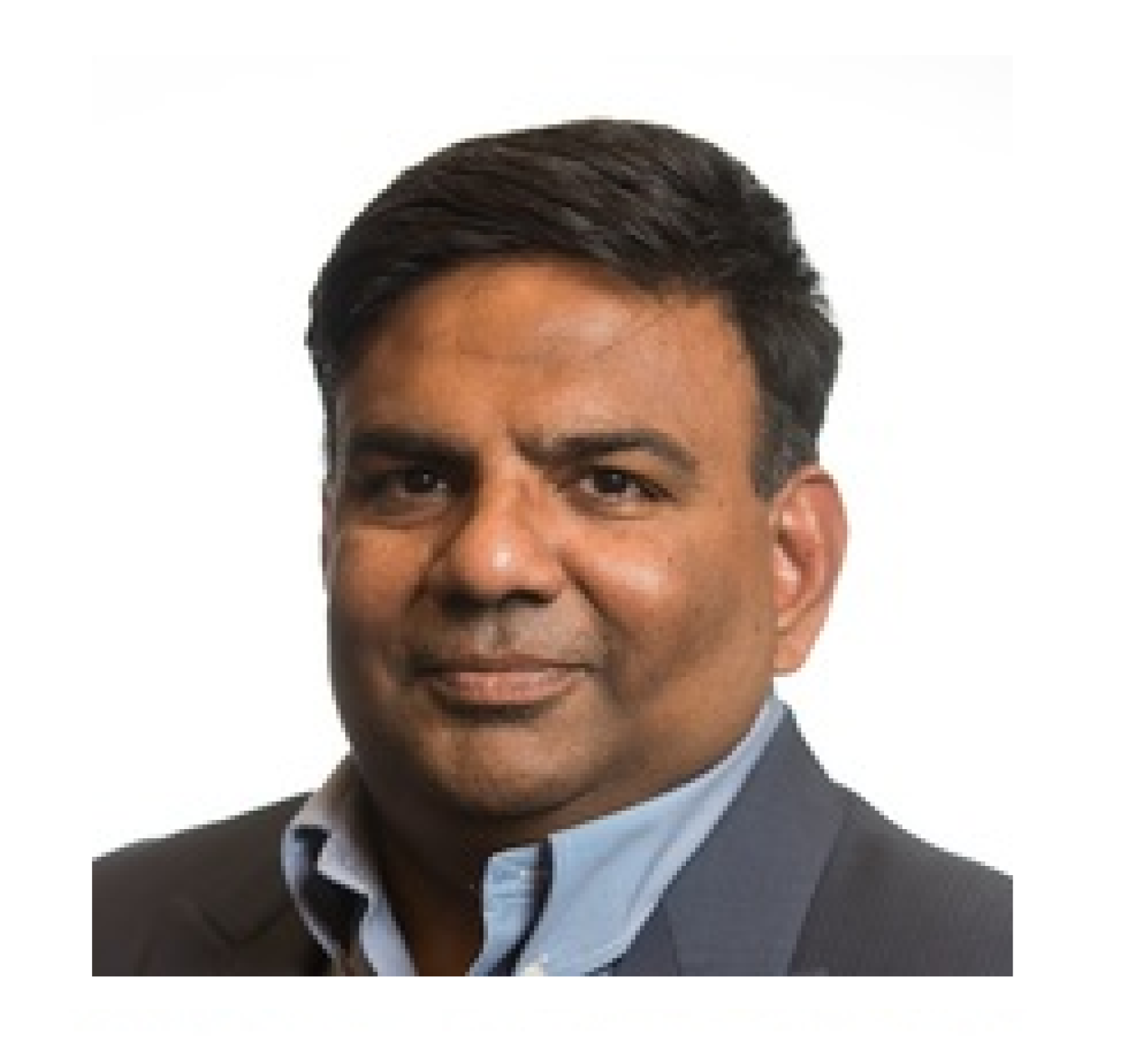
Senior Research Chemist in the Energy Processes and Materials Division at Pacific Northwest National Laboratory
BIOPROSE BLOG
Since the dawn of the industrial age, petroleum-based chemicals and fuels have driven countless inventions and products used every day. Today, U.S. Department of Energy (DOE) national laboratories study the development of chemicals and fuels with the use of cost-effective, renewable carbon sources, while working closely with the bioenergy industry.
In support of the DOE mission, Pacific Northwest National Laboratory (PNNL) experts in fungal biotechnology and catalysis targeted their research on chemicals and fuels made from renewable and underutilized carbon, such as biomass, to supplement petroleum. In just over a decade, PNNL developed new catalysts and processes to:
- Produce a common chemical, propylene glycol, from biodiesel waste. Archer Daniels Midland Company churns out the product at their 35,800,000-gallon (100,000-metric-ton) capacity manufacturing plant in Decatur, Illinois.
- Make high-quality biocrude in minutes using wet plant and waste sources. Genifuel Inc. licensed the technology for a pilot plant in California, and Metro Vancouver (Canada) is scoping the technology for treating wastewater as part of a $2 billion infrastructure upgrade for the region.
- Create diesel and jet fuel blends out of ethanol from captured industrial gas emissions. Virgin Atlantic Airlines flew from Florida to London using the jet fuel blend created by PNNL and industrial partner LanzaTech. LanzaTech plans to integrate the process into their refinery in Soperton, Georgia, producing up to 3 million gallons (~11.3 million liters) of the fuel for Atlanta International Airport.
Working closely with industry partners—early and often—was a key factor in determining the critical science questions and achieving incremental advances at various scales.
Propylene Glycol from Waste Glycerol
Archer Daniels Midland Company (ADM) teamed with PNNL to develop a catalyst for converting glycerol—a byproduct of making biodiesel—into bio-based propylene glycol. Propylene glycol is a chemical used in everyday products ranging from fiberglass to cosmetics. ADM was one of the largest biodiesel producers at the time and needed a method to convert the accumulating glycerol byproduct into something useful.
Prior to this partnership, PNNL had been developing a new catalytic process to convert corn fiber, an underutilized byproduct from making ethanol, into propylene and ethylene glycols. PNNL researchers noticed that the corn fiber first formed glycerol before producing the desired glycols. This observation provided researchers with an “aha” moment: PNNL's new catalytic process could be used to solve ADM’s need to convert its excess glycerol into something valuable.
PNNL quickly adapted their catalyst to meet the speed, selectivity, and stability needed in hot water to convert glycerol to propylene glycol. In just two years—with co-funding from DOE’s Bioenergy Technologies Office (BETO), ADM, and UOP LLC (a Honeywell company)—PNNL researchers improved the catalyst to increase the amount of glycerol converted to propylene glycol from 40%–60% to well over 90%. They also showed the catalyst had the ability to last more than a year. The catalyst was now ready for ADM to extend to commercial scale. ADM scaled up the process for industrial production in Decatur, Illinois, creating 140 jobs.
The project earned a Federal Laboratory Consortium (FLC) Excellence in Tech Transfer Award, and researchers involved in the project received the American Chemical Society's Green Chemistry Award in 2014. ADM continues to manufacture propylene glycol at plant capacity—100,000 metric tons.
Diesel from Wet Waste
DOE formed the National Alliance for Advanced Biofuels and Bioproducts to work on reducing the cost of growing and processing algae for fuels and chemicals. Around the same time, PNNL was working on a process to convert wet biomass from wood and stover into a biocrude oil using hot water and pressure.
The process, called hydrothermal liquefaction, mimics how nature creates fossil fuels, but in minutes as opposed to eons. It works like a pressure cooker, using both high pressure and temperature to turn algae into an ooze that readily separates from water. The high-quality biocrude can be refined to make diesel as well as fuel gas and other useable byproducts.
Hydrothermal liquefaction provided an exciting solution to make diesel fuel from algae, because the lipids—long-chain carbon molecules that make up fat—could be extracted and converted in a single step. This happens after the algae is harvested from the outdoor ponds where it grows. PNNL developed a more efficient solution to this challenge by converting the biomass as a whole—both the algae itself and the fat cells.
PNNL teamed with Genifuel Corporation to prepare the technology for industry, starting with a pilot plant to test industrial-scale production in Colorado. The technology earned an FLC Award for excellence in technology transfer as well as the attention of Metro Vancouver, a regulatory and public service district in British Columbia that is scoping the technology for treating wastewater.
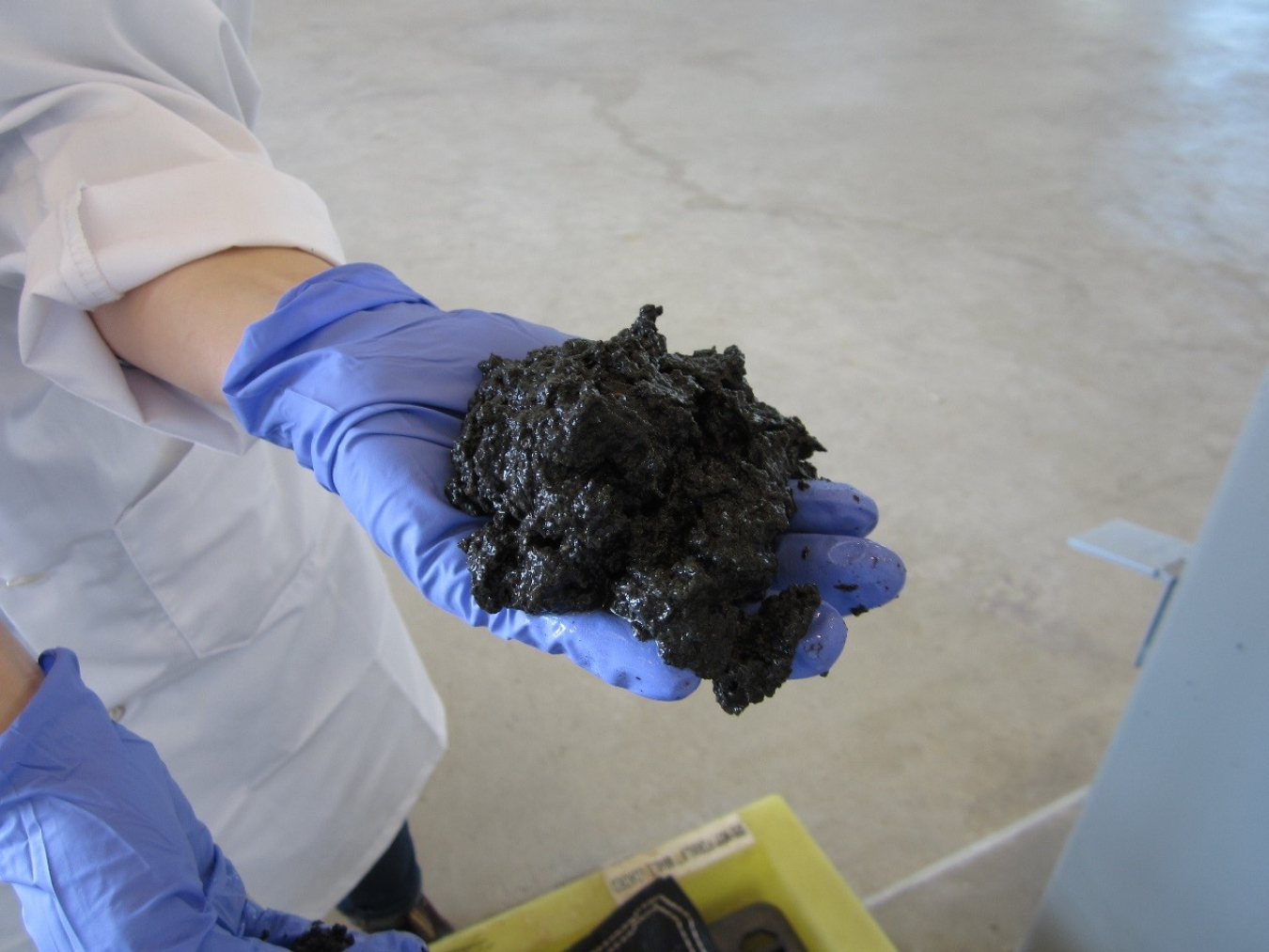
Sludge from Metro Vancouver’s wastewater treatment plant has been dewatered prior to conversion to biocrude oil at Pacific Northwest National Laboratory. Photo: WE&RF
Today algae remains expensive to grow, but PNNL demonstrated that other wet feedstocks also make great biocrude oil. These feedstocks include wastewater sludge from local water treatment plants, food wastes, manures, and mixtures of all these with wood. Notably, the more carbon and fat in the waste, the better the product. Converting such wet waste into biocrude oil solves pressing environmental problems and turns energy-intensive processes, like water treatment, into small bio-oil refineries that produce a high-quality energy product.
Jet Fuel from Alcohol
PNNL’s jet fuel journey began with a partnership between UOP LLC, a Honeywell company, and Boeing. Upgraded pyrolysis oil, used in combination with synthetic paraffinic kerosene, produced the world’s first biomass-derived jet fuel that was demonstrated in a hydroplane at Seattle’s Seafair race. But the challenge with jet fuel made from vegetable oil or animal fat is there just isn’t enough feedstock to meet aviation needs.
This challenge led to an exploratory project between PNNL and Seattle-based Imperium Renewables to produce jet fuel which are rich in the isoalkanes that burn clean, pack a lot of energy, and stay liquid at low temperatures. The team needed to find an inexpensive alcohol that wasn’t produced from food crops. They found their answer in an industrial partner, LanzaTech, headquartered in Skokie, Illinois. The company captures carbon monoxide produced during steel production and, rather than letting it escape into the air, feeds it to microbes that consume the gas and produce ethanol.
With the partnership sealed and backed by $2.5 million in funding from BETO, researchers began working on the process to convert ethanol into an aviation-approved jet fuel. The integrated process starts with dehydration, running LanzaTech’s ethanol through a reactor with a catalyst to remove water. The resulting ethylene hydrocarbons are then combined using PNNL’s specialized catalyst to build the range of carbon chains needed for jet fuel; this process is called oligomerization. A metal catalyst hydrogenates the carbon chains, which are fractionated into synthetic paraffinic kerosene (SPK) for both diesel and jet fuel.
The PNNL team ran their catalyst experiments with ethanol, verified the critical fuel properties, and provided data to support scale-up. Meanwhile, LanzaTech scaled up their plant in Freedom Pines, Georgia, to start producing ethanol-derived diesel and jet fuel at industrial scale. They also took on the costly and lengthy fuel-approval process. More than 2,500 tests were used to evaluate 100 properties that would show how the new fuel would function in a jet engine.
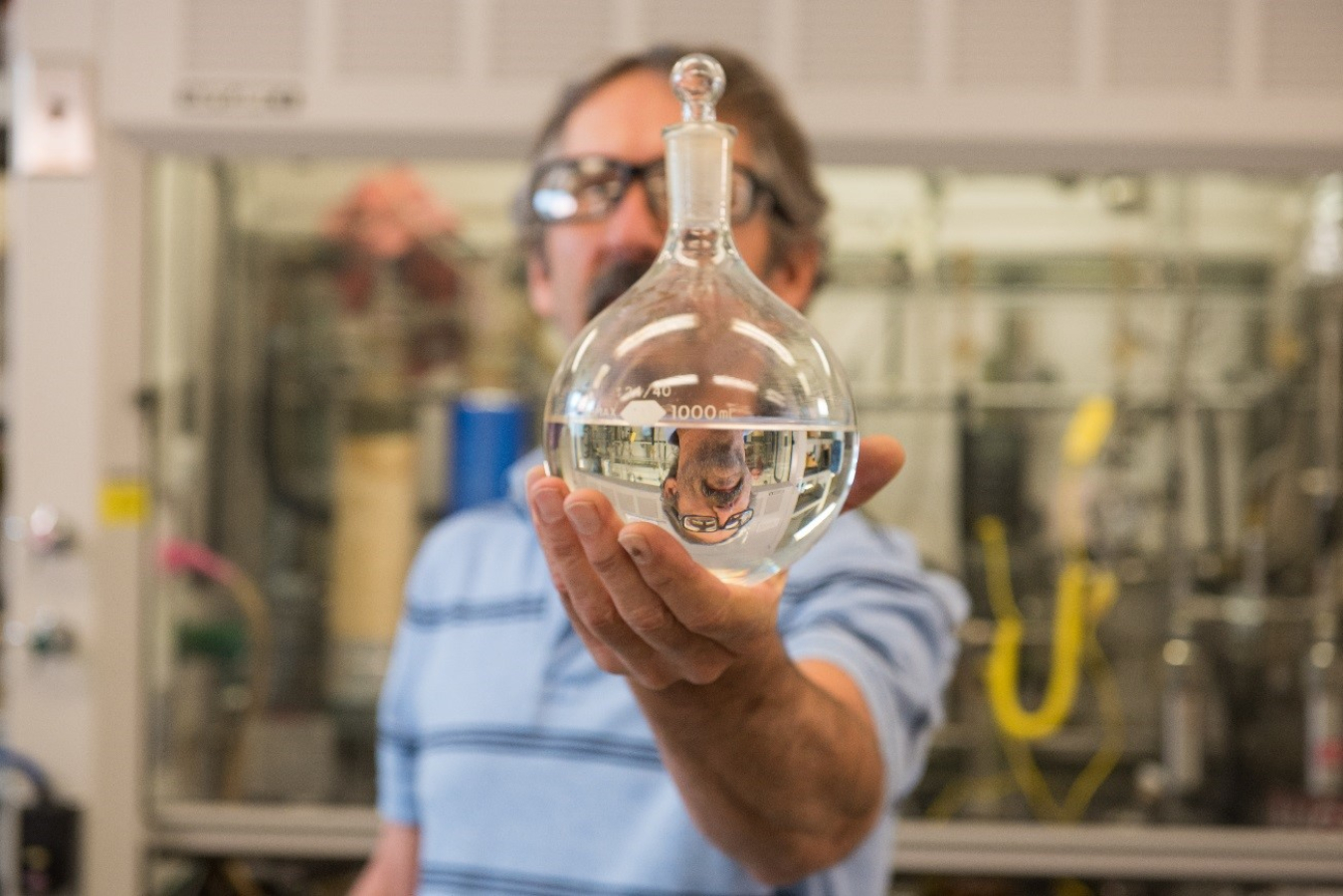
PNNL researcher Rich Hallen helped develop a process that converts ethanol to jet fuel. Photo: Andrea Starr/PNNL
The product subsequently met BETO’s goals under the Government Performance and Results Act, achieving a minimum fuel selling price of $3.00 per gallons gasoline equivalent. This goal was soon followed by review of aircraft and engine manufacturers, and eventually a revised ASTM International standard for the ethanol-to-jet fuel blend. Virgin Atlantic Airlines stepped up to the plate and flew from Orlando, Florida, to London, England, on engines powered by the SPK jet fuel blend. LanzaTech plans to integrate the process into their refinery in Soperton, Georgia, eventually producing up to 3 million gallons (~11.3 million liters) of the fuel for nearby Atlanta International Airport.
The team’s patented catalytic process can also produce a high-quality, low-temperature diesel fuel for heavy-duty trucks, ships, and trains that can be used in the most extreme environments, like the Arctic. The technology earned an FLC Award for excellence in technology transfer.
The speed and success of these advances was a result of the commitment of industry partners and federal sponsors who saw the promise of—and need for—renewable bioenergy technologies.
PNNL's industry partnerships have resulted in commercially available chemicals and fuels made from renewable resources. For more information on how PNNL continues to build on these scientific advances toward a vision of a no-waste economy, check out this video.