Bioprose Blog: Techno-economic analysis leads to a market-responsive biorefinery concept
September 10, 2020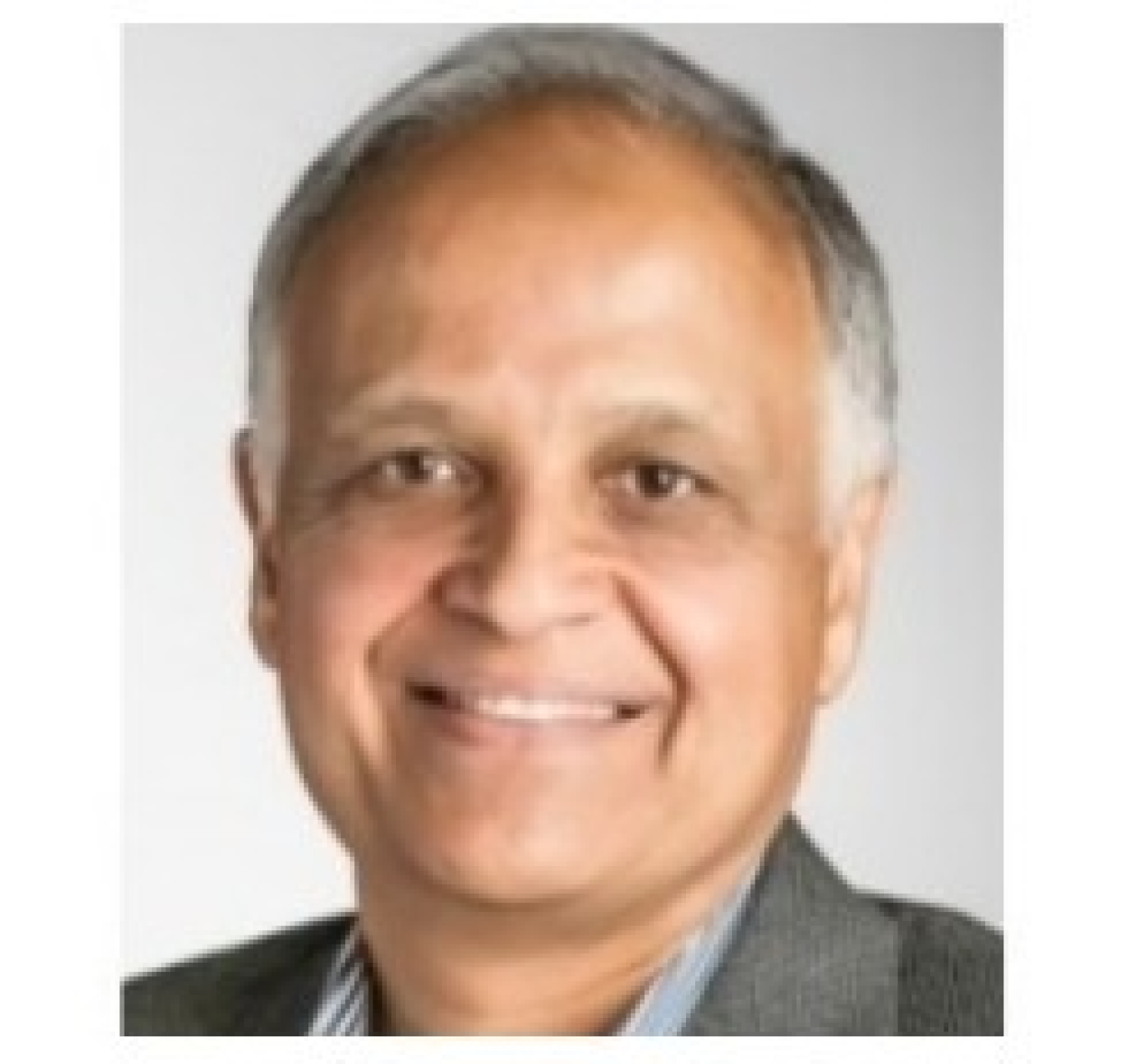
Author: Zia Abdullah, Laboratory Program Manager, National Renewable Energy Laboratory
Read Zia's bio ►
Meet the other bloggers ►
Return to Bioprose blog ►
Bioprose Blog
Techno-economic analysis leads to a market-responsive biorefinery concept
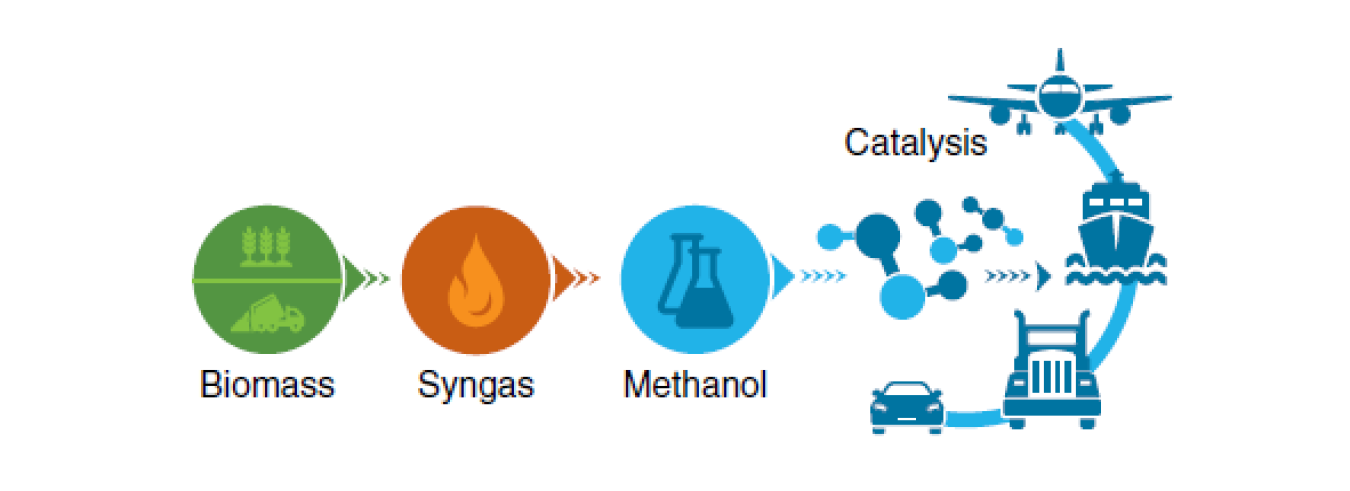
A schematic flow diagram of a market-responsive biorefinery concept based on methanol as the key intermediate. Biomass gasification and methanol production can provide a variety of fuels—gasoline, diesel, marine, and jet—enabled by catalysis. Illustration by NREL.
The Challenge: Reduce Biomass to Biofuel Conversion Costs
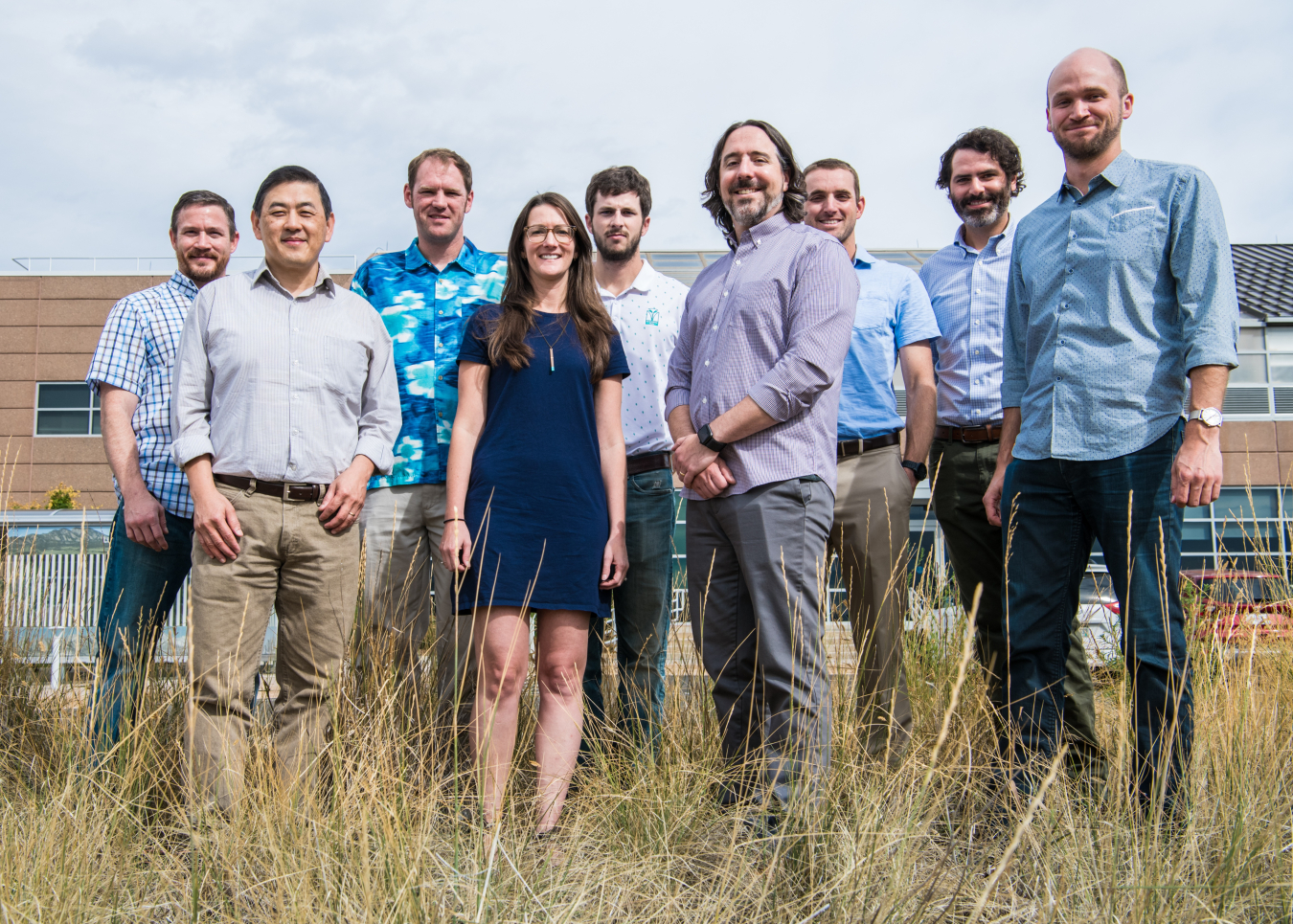
NREL researchers developed a more efficient pathway for the generation of high-octane gasoline and jet fuel blendstocks from biomass. Photo by Dennis Schroeder/NREL.
The production of biofuels from lignocellulosic biomass is hindered by high conversion costs, creating a need for new pathways with less severe conditions, higher yields, and higher-quality products.
In response to this challenge and with support from the U.S. Department of Energy's Bioenergy Technologies Office, principal investigator Daniel Ruddy and his team at the National Renewable Energy Laboratory (NREL) have developed a market-responsive biorefinery concept based on methanol as the key intermediate. The process was shown to generate high-octane gasoline (HOG) and jet fuel blendstocks from biomass.
This detailed process was published in the journal Nature Catalysis in a study titled, "Methanol to High-Octane Gasoline within a Market-Responsive Biorefinery Concept Enabled by Catalysis."
NREL Catalysis Team Increases HOG Yield and Reduces Conversion Costs with a Modified Catalyst
Considering the challenges of conventional methanol to gasoline technologies—they’re expensive, and the fuel product typically contains high concentrations of soot-forming aromatic molecules—the NREL team had their work cut out for them.
The team started with a recent development discovered during the conversion of methanol to fuels, i.e., the production of branched C4–C7 hydrocarbons while using beta zeolite catalysts. The branched structure of these fuel-range (C5–C7) hydrocarbons indicated that the molecules were exhibiting high research octane numbers, which promised possibility as a high-quality gasoline blendstock. This methanol-to-HOG process, using beta zeolite catalysts, operates at significantly lower temperatures and pressures as compared to the traditional ExxonMobil Methanol-To-Gasoline (MTG) process and the Mobil olefins to gasoline and distillate (MOGD) process.
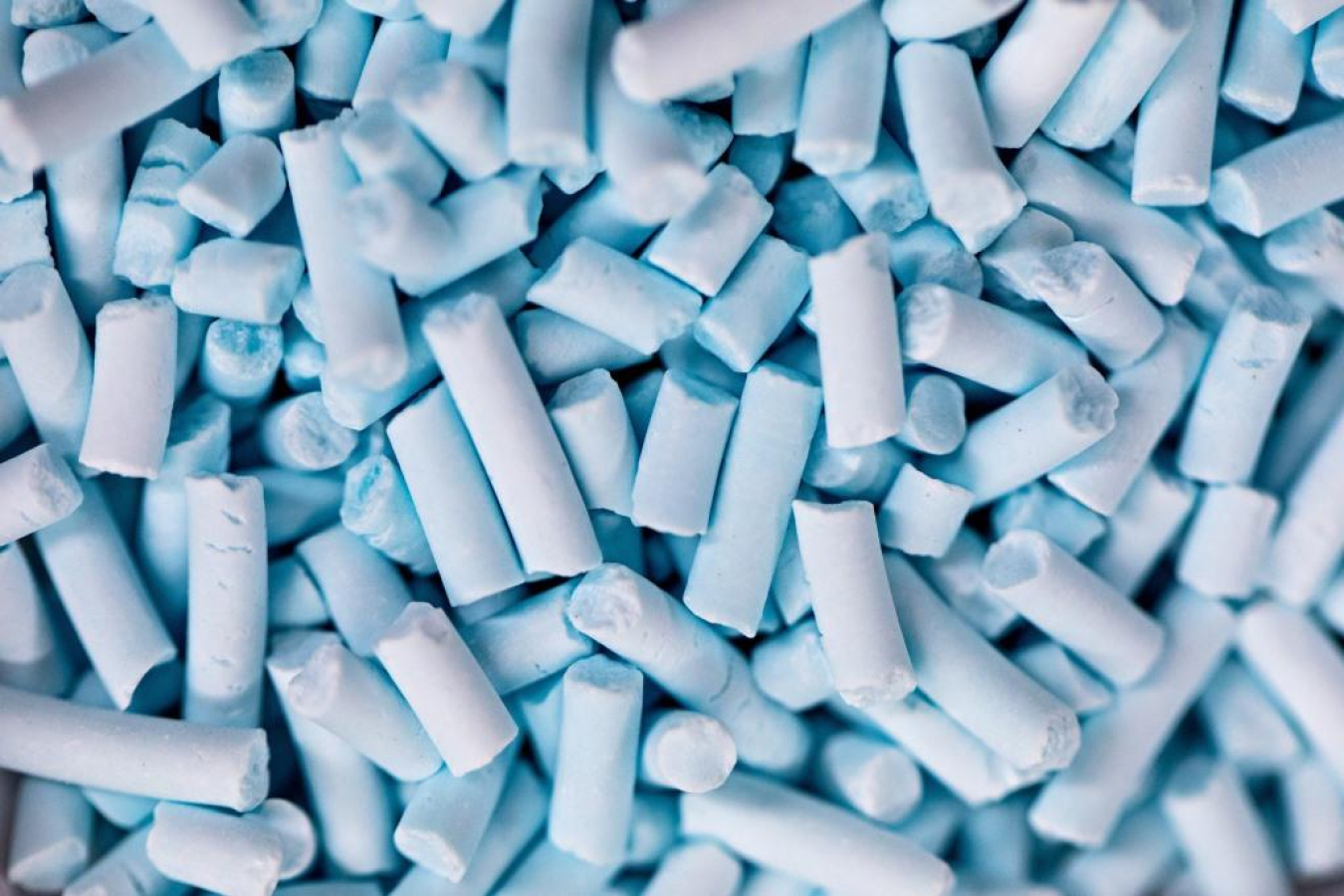
Researchers used a copper-modified beta zeolite catalyst to produce high-octane gasoline. Photo by Werner Slocum/NREL.
The NREL team discovered that a copper-modified beta zeolite catalyst facilitated the reincorporation of C4 byproducts—such as isobutane —enabling a 38% increase in yield of the HOG product and a 35% reduction in conversion costs compared to the benchmark unmodified beta zeolite catalyst. The copper-modified beta zeolite catalyst from NREL exhibited a twofold improvement:
- Increased hydrocarbon productivity, resulting in smaller reactor volumes and higher throughput
- Extended time on stream operations due to reduced aromatic selectivity, resulting in less down-time for catalyst regeneration.
As an alternative to using the C4 byproducts for increased HOG yield, those same byproducts were also directed to a synthetic kerosene product that was shown to meet several specifications for a typical jet fuel. A techno-economic analysis (TEA) of producing both HOG and jet fuels revealed only a minor increase in the total fuel synthesis cost versus the HOG-only case.
Advancements in Catalyst Performance Guided by NREL TEA Provide Possible Boost for Existing Methanol Plants
NREL has linked biorefinery process models, TEA, and catalyst manufacturing costs through CatCostTM with both fundamental and applied catalyst development research to quantify the impact of catalyst advancements on process economics. TEA-guided research and foundational catalysis science contributes to the advancement of the technology toward commercially relevant performance.
The NREL HOG pathway, described above, also represents a bolt-on technology for existing methanol plants that utilize natural gas, biogas, or municipal solid waste to generate syngas. This technology could enable U.S. methanol producers to enter the fuel production industry with a high-value, high-octane gasoline blendstock and a jet fuel blendstock, and pursue renewable fuel credits if the carbon was sourced from biogas and/or municipal waste.
The conversion costs of the HOG pathway equate to $0.66–$0.69 per gallon gasoline equivalent (GGE). This compares favorably with an assessment of ethanol-to-jet fuel technologies, where the conversion costs of ethanol to jet fuel ranged from $0.89–$1.19/GGE, depending on the biomass source and corresponding feedstock cost.
Dr. Zia Abdullah
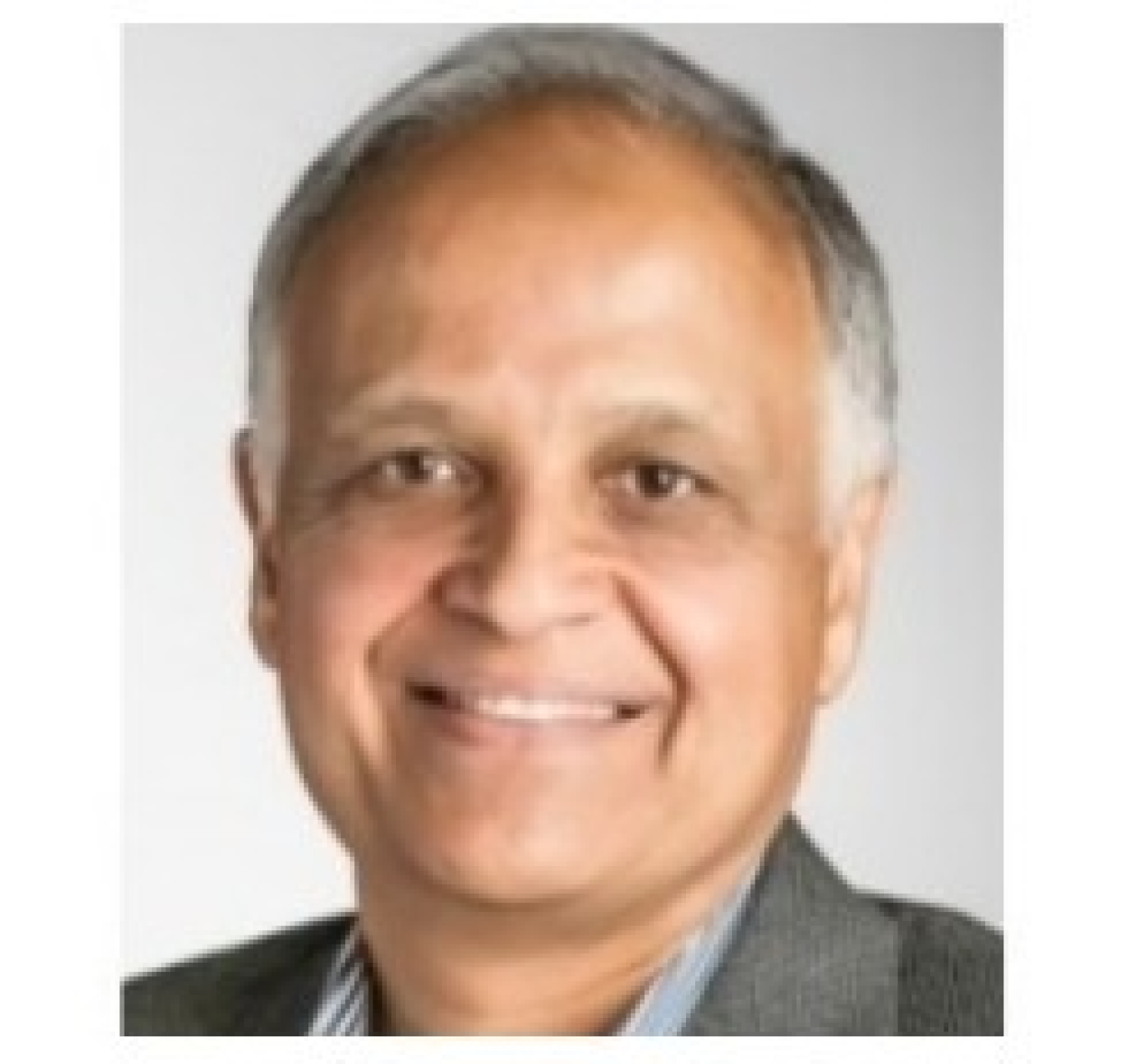
Dr. Zia Abdullah is laboratory program manager for the National Renewable Energy Laboratory’s (NREL’s) Bioenergy Technologies Office program.
Zia has extensive experience and accomplishments in thermochemically and biochemically converting biomass to fuels and chemicals. His experience includes more than 25 years of industrial research and development in biomass conversion, as well as problem solving, new product development, business development, and project management.
Prior to joining NREL, Zia was chief technology officer at Versa Renewables LLC, where he developed and commercialized biomass pyrolysis and biopolyol technologies. Before Versa, Zia served as one of the Battelle Memorial Institute’s 11 fellows, leading the development of technology and commercial application for fuels, chemicals, and materials from the thermochemical and biochemical conversion of biomass. Prior to working at Battelle, Zia was a research advisor (fellow) at Weyerhaeuser Company, where he worked on challenges related to manufacturing and biomass valorization.
Meet our other bloggers ►
Return to Bioprose blog ►