Bioprose Blog: DOE's Advanced Biofuels and Bioproducts Process Development Unit at Lawrence Berkeley National Laboratory uses raw materials...
May 8, 2019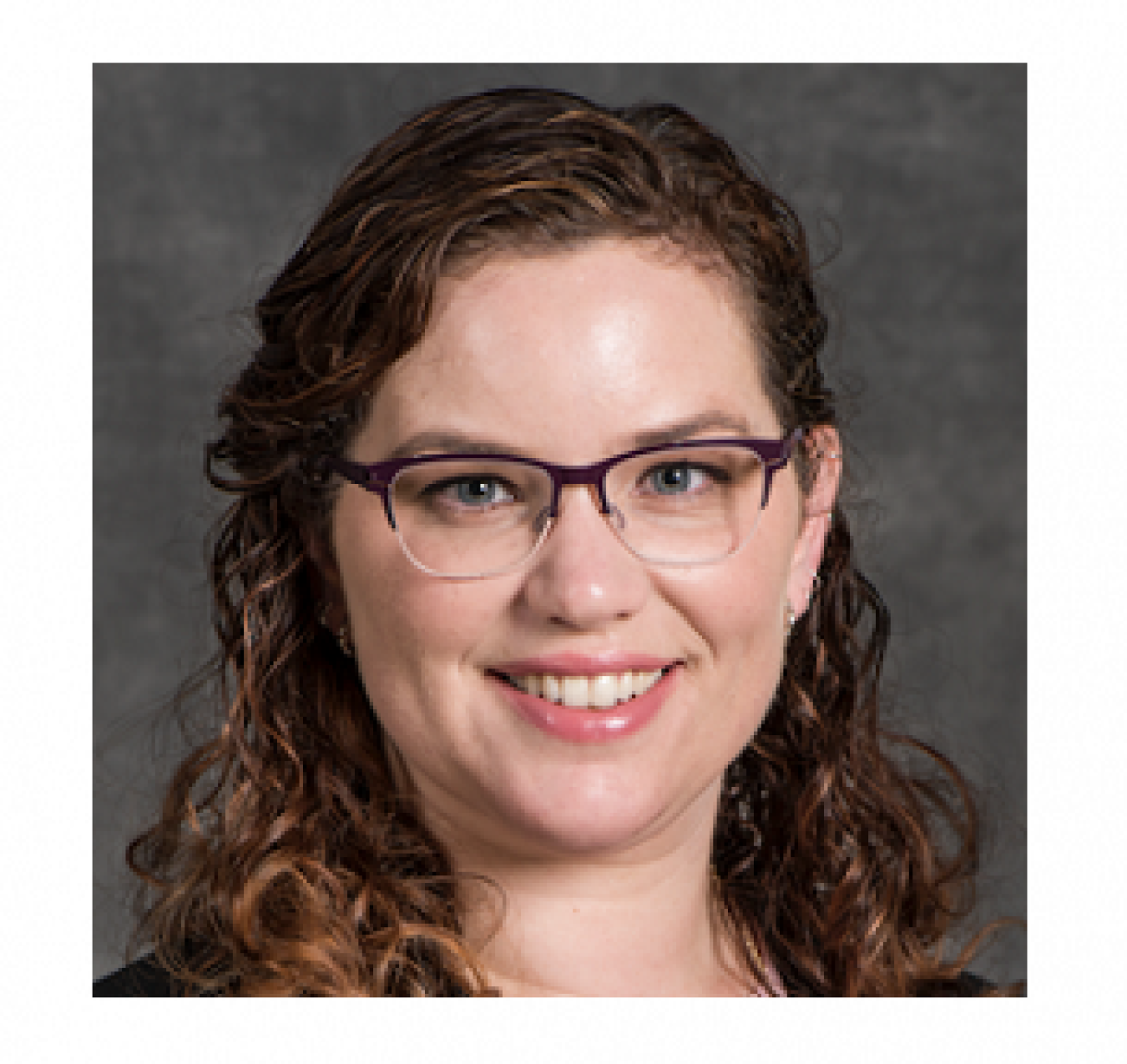
Author: Katy Christiansen, Laboratory Relationship Manager for BETO programs at Lawrence Berkeley National Lab
Read Katy's bio ►
Meet the other bloggers ►
Return to Bioprose blog ►
BIOPROSE BLOG
When the U.S. Department of Energy’s (DOE’s) Advanced Biofuels and Bioproducts Process Development Unit (ABPDU) at Lawrence Berkeley National Laboratory (Berkeley Lab) commenced operations in 2012, its initial focus was overcoming barriers to biofuel commercialization. The 15,000-square-foot facility was designed to provide bench- to pilot-scale test beds for advanced cellulosic biofuel technologies developed by partners from other national laboratories, government agencies, industry, and academia.
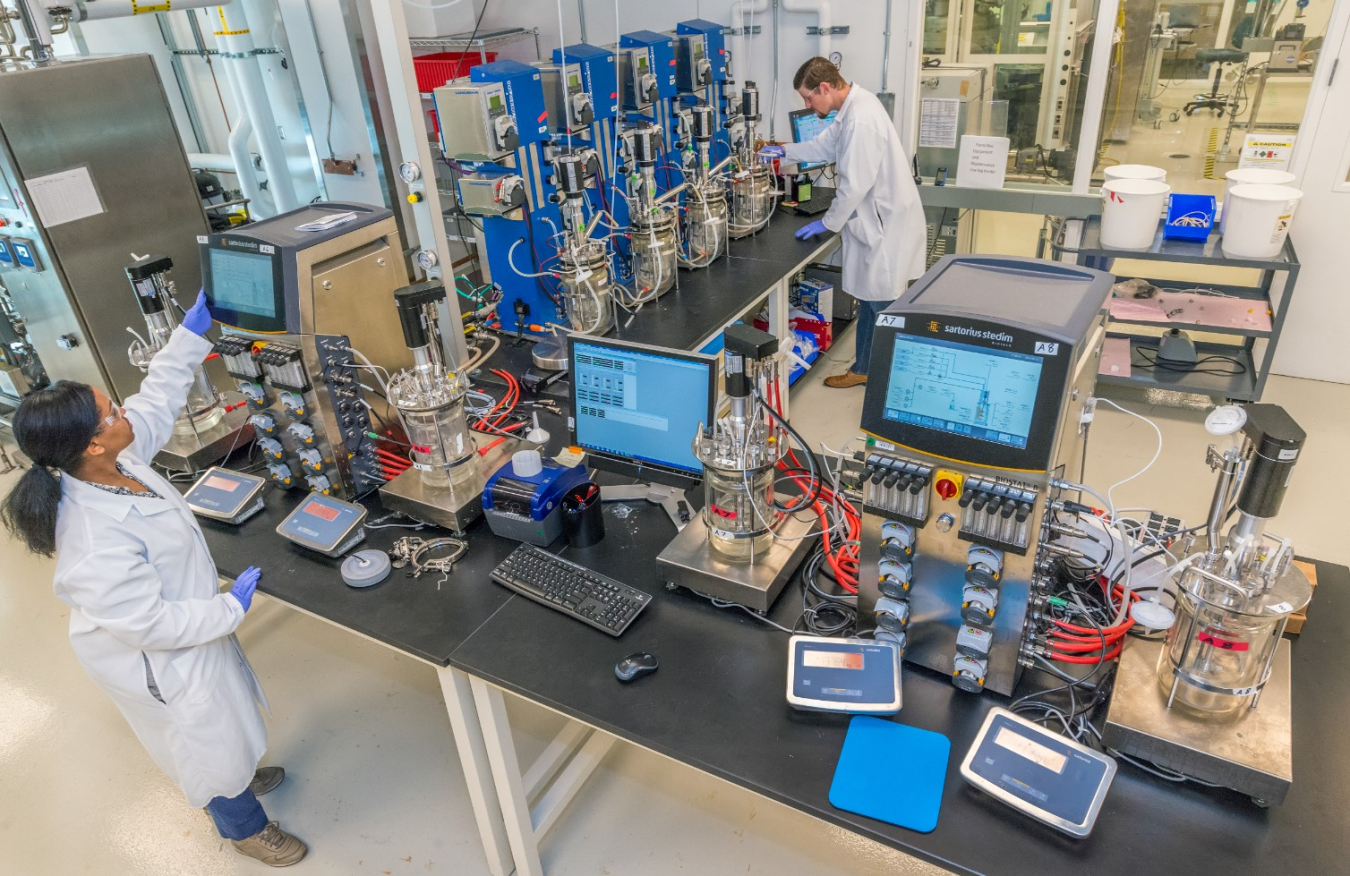
Converting biomass to biofuels often requires the process of fermentation, in which microorganisms metabolize organic matter, and this remains one of the ABPDU’s core capabilities. However, in recent years, the facility’s scope has expanded to utilize a broader range of raw materials to produce a variety of biobased material, chemical, and protein end products.
These end products—called bioproducts—are everyday products derived from domestic renewable biomass resources like plants, algae, and waste streams. When bioproducts are produced alongside biofuels, profits from the sale of bioproducts can help offset the costs of producing biofuels—leading to more affordable and reliable energy choices for Americans.
To enable the cost-effective production of biofuels, the ABPDU develops more efficient manufacturing processes with biobased inputs—including waste feedstocks like garbage and agricultural residue—while also growing the manufacturing base for the U.S. bioeconomy.
The ABPDU’s capabilities and resources can give a boost to industry. By leveraging the ABPDU’s capabilities, companies avoid the significant cost and timelines associated with building their own dedicated pilot facilities, allowing them to focus their efforts on product development, later-stage manufacturing facility deployment, and near-term job growth.
To date, the ABPDU has engaged with more than 40 partners--from industry and academia--to develop, scale, and validate processes for transforming a variety of non-food plant-, algae-, and waste-derived materials into a useful products.
So, who are these companies the ABPDU has helped develop and validate processes to create bioproducts? Below are a few diverse examples:
Kalion
Through DOE’s Bioenergy Technologies Office Industrial Seeding Program and the Energy Efficiency and Renewable Energy Small Business Voucher Program, Massachusetts-based Kalion received support to work with the ABPDU to reach full manufacturing-scale production of biobased glucaric acid. One of the “Top Value-Added Chemicals from Biomass” identified in a 2004 report, glucaric acid has been identified as an effective substitute for a corrosion inhibitor over less environmentally friendly phosphates and particularly better for water treatment environments where “white rust” is problematic.
Scaling up manufacturing processes is a common obstacle for small companies like Kalion. By working with the ABPDU, Kalion went from a 2-liter to a 300-liter run via fermentation and provided another point of validation to its investors.
Bolt Threads
Bolt Threads is also working with the ABPDU to investigate the biophysical characteristics of their engineered silk proteins and to refine methods for separating and purifying them. The proteins are produced in liquid form through a fermentation process with modified yeast, then wet-spun into fibers, which can be knit or woven into textiles.
For Bolt Threads, the ABPDU has provided expertise, specialized equipment, flexibility, and ease of access. The scientific conclusions resulting from this partnership have accelerated Bolt Threads’ in-house research program, improving their timelines and providing real impact toward meeting their business objectives. Bolt Threads has begun transferring its laboratory-scale process into commercial-scale operations for three customers, including outdoor apparel maker Patagonia.
Indie Bio
Fermentation has become a vital technology in the 21st-century economy, and Indie Bio, another ABPDU partner, finds that there are almost no resources to help small companies doing fermentation to develop their business. ABPDU is fulfilling a vital role in making that a reality.
About 7 startups (Ardra, Clara Foods, Geltor, Perfect Day, Sugarlogix, Zymochem, and Tinctorium) that have participated in Indie Bio’s intensive four-month bench-to-product program have also collaborated with ABPDU. In 2017, Indie Bio formalized an umbrella agreement to get companies in its residency program off and running with ABPDU more quickly.
The ABPDU has worked with many types of partners and is invigorated by the unique challenges and opportunities presented by each one. Whether it is producing specialty bio-based chemicals used in flavorings, fragrances, and cosmetics, or polymers used in packaging, coatings, and adhesives, the ABPDU is excited to play a part in moving these bioproduct innovations from the bench to the marketplace.
DOE’s Bioenergy Technologies Office (BETO) supports the ABPDU’s collaborations with industry, which further BETO’s mission to advance early-stage applied research and development of biofuels, bioproducts, and biopower. Through advances in scientific research and innovation, everyday products, materials, and chemicals can be produced from domestic, renewable resources like plants, algae and wastes, enabling the production of price-competitive biofuels.