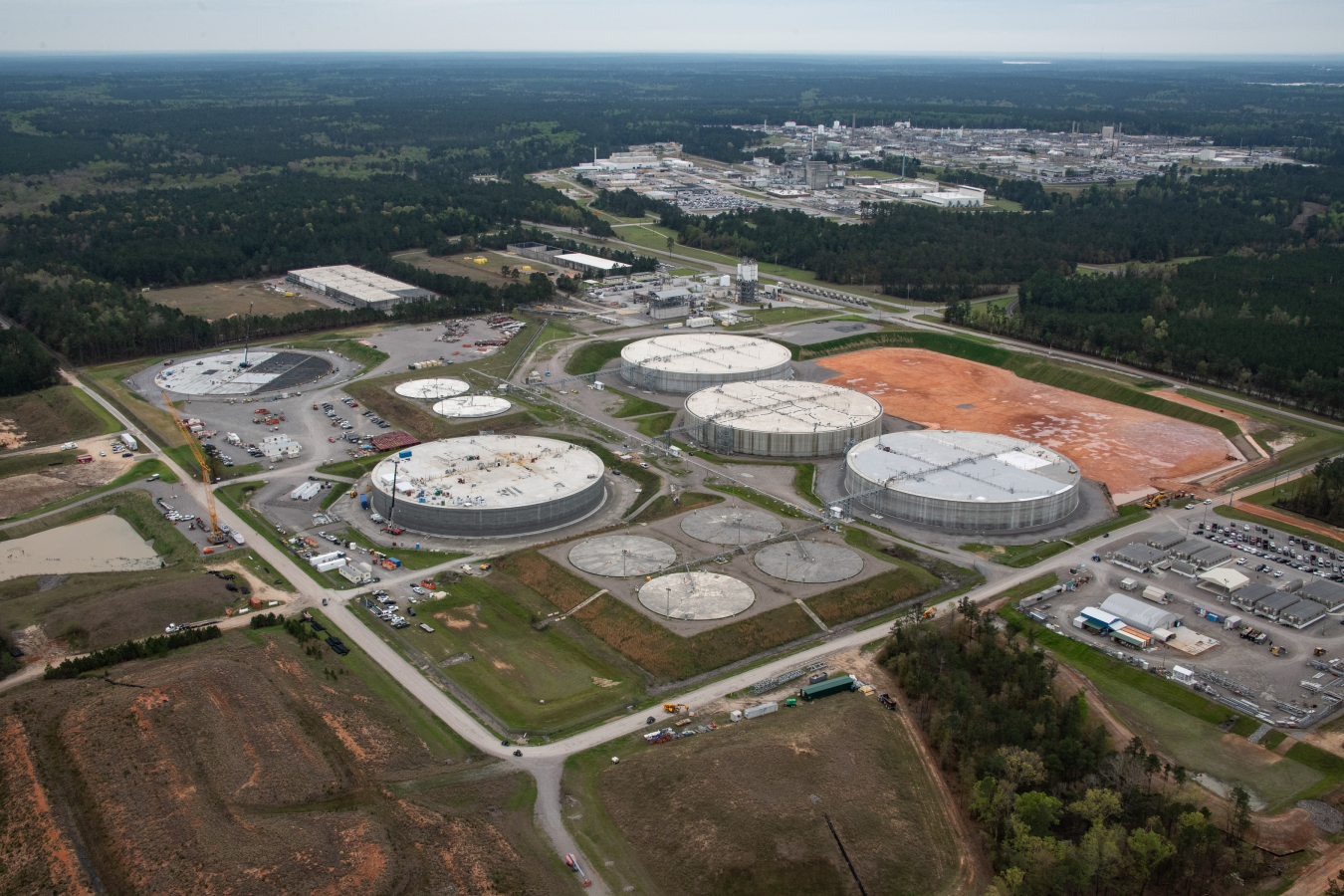
Disposition and Solidification
Radioactive liquid waste is generated at the Savannah River Site (SRS) as by-products from the processing of nuclear materials for national defense, research, medical programs, and outer space missions. The waste, totaling about 35 million gallons, is stored in the remaining 43 underground carbon-steel waste tanks grouped into two tank farms at SRS. The liquid waste program at SRS consists of high-hazard operations, which include complex engineering, operations, construction, waste treatment, grouting, and disposal in order to operationally close the radioactive liquid waste tanks.
As the waste is stored in the tanks, it separates into two primary parts: a dense sludge and a crystallized saltcake. The primary facilities processing and treating the liquid waste are the Defense Waste Processing Facility (DWPF), the Salt Waste Processing Facility (SWPF), and the Saltstone Production Facility (SPF). Water is dispositioned from the tank waste using evaporators and treated at the Effluent Treatment Facility.
The sludge waste, the highly radioactive portion, is dispositioned to the Defense Waste Processing Facility. As the only operating radioactive waste vitrification plant in the United States, DWPF converts the high-level liquid radioactive waste into a solid glass form suitable for long-term storage and disposal. This waste has about 230 million curies of radioactivity and requires permanent isolation from the environment.
Scientists have long considered this glassification process, called “vitrification,” as the preferred option for immobilizing high-level radioactive liquid into a more stable, manageable form. In this vitrification process, a sand-like borosilicate glass (called “frit”) is mixed with the waste and sent to the plant’s 75-ton melter, where the waste/frit mixture is heated until molten. This molten mixture is poured into stainless steel canisters to cool and harden to form a stabilized glass.
The canisters of vitrified waste produced at DWPF are currently stored onsite in two Glass Waste Storage Buildings until a federal repository is established. DWPF is projected to produce approximately 8,500 canisters to complete its waste vitrification mission. Just over 4,300 canisters have been poured as of summer 2022.
The salt waste, the less radioactive portion but majority of the tank waste, is dispositioned to the Salt Waste Processing Facility. SWPF is designed to significantly increase the site’s ability to empty and close the waste tanks and dramatically reduce the legacy environmental risk.
The SWPF separates and concentrates the highly radioactive waste—mostly cesium, strontium, actinides, and waste slurry—from the less radioactive salt solution. The process begins by transferring the waste from H Tank Farm to SWPF where it undergoes a two-step cleanup process. The first step removes strontium and actinides (uranium, plutonium, etc.) from the waste. The second step, known as Caustic Side Solvent Extraction (CSSX), is designed for the removal of radioactive cesium.
After the separation process is completed, the concentrated high-activity waste is sent to DWPF to be combined with the sludge waste and go through the vitrification process. The decontaminated salt solution (DSS) is sent to the Saltstone Production Facility for final treatment before disposal.
The DSS processed at SWPF is sent to the Saltstone Production Facility for safe treatment and disposal. After the waste is received at SPF, the salt solution is mixed with dry materials – fly ash and blast furnace slag – to form grout. The grout is pumped from SPF into above-ground saltstone disposal units, where it solidifies into a non-hazardous, concrete-like form called saltstone.
The Saltstone Disposal Units (SDU) are large concrete structures used for permanent disposal of the DSS. Generally, there are two types of SDUs at SRS. The early vaults were rectangular, and no more disposal is planned for these vaults. Subsequent SDUs were cylindrical and based on a design used commercially for storage of water and other liquids. The early cylindrical SDUs held approximately three million gallons of saltstone. The new era of SDUs, considered mega-volume units, are 10 times larger than the previous SDUs. They are designed for the larger quantities of DSS that will be produced by SWPF. The larger design will result in substantial cost savings over the life of the project because of economies of scale, requiring less infrastructure and materials to design and build.
In the waste tanks, water sits on top of the waste and is dispositioned through an evaporation process. The evaporators reduce the waste to about 30 percent of its original volume, making tank space available for continuing liquid waste operations. Creating tank space supports cleaning and closure of the tanks, as well as other SRS missions. The condensed evaporator “overheads" are transferred to the Effluent Treatment Facility (ETF) for final cleanup prior to release to the environment.
Tank Closure
After the bulk of the radioactive waste is dispositioned from the tanks for stabilization through DWPF and SWPF, the operational closing of the tanks can begin. Once the bulk waste is removed, tank closure activities continue with removal of the remaining heel waste material. The heel removal process uses either mechanical or chemical cleaning methods to the extent practical in accordance with federal requirements and closure plans established with the state regulator. The small amount of waste that remains is characterized and documented.
The final operational closure activity begins with workers pouring specially formulated grout into the tank. Over several months, the approximately one-million-gallon tank fills with grout, and tank top openings are sealed. This special grout stabilizes the tank and its surroundings, as it fills the tank with a solid material that will not collapse. The solidified grout also impedes the migration of any residual waste, which reduces risks to people and the environment by minimizing the potential for groundwater contamination.
Liquid Waste System Plans