Workers recently performed a series of precision crane lifts to safely place and assemble a 111-ton electrical powerhouse.
Office of Environmental Management
June 4, 2019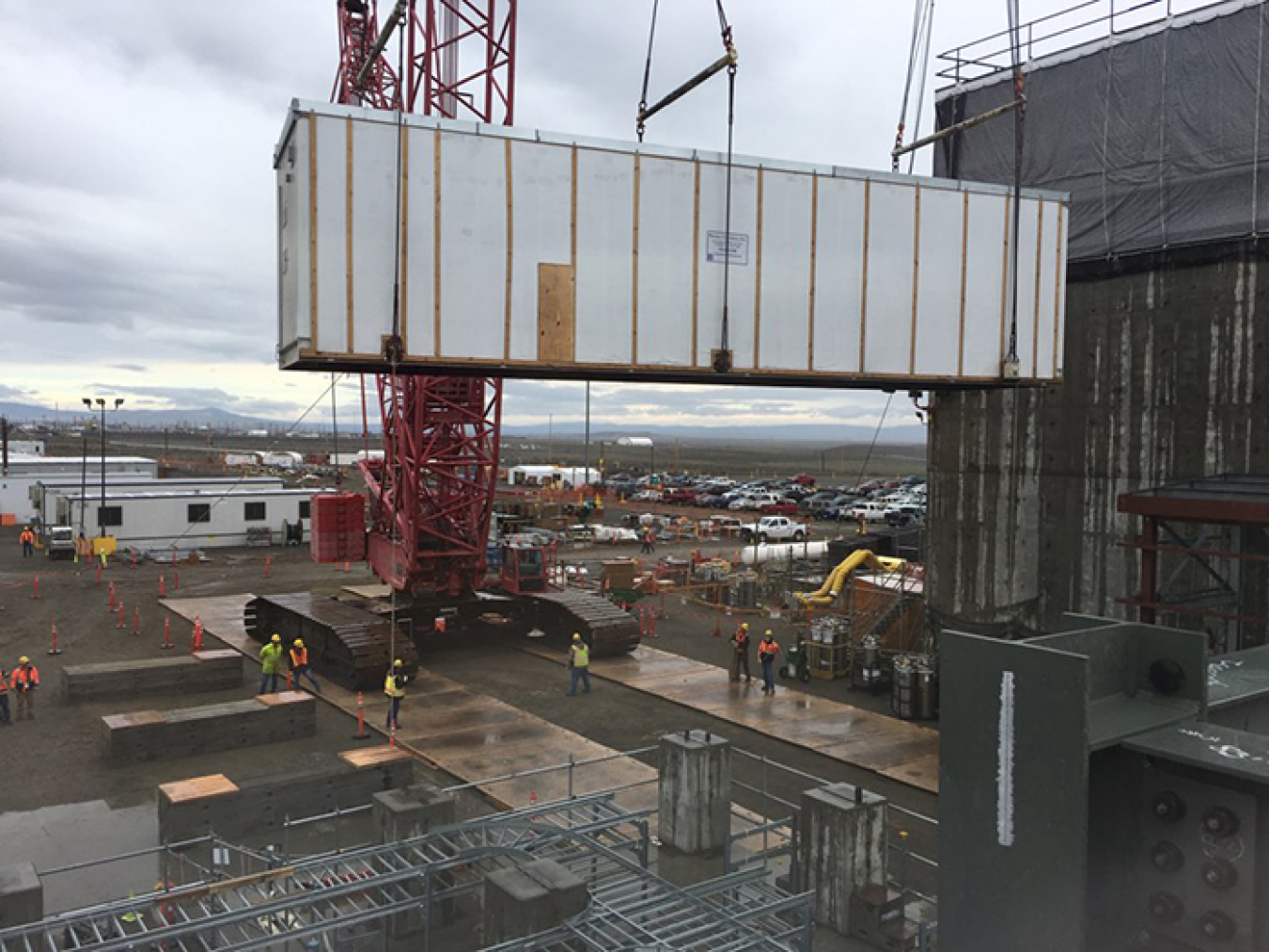
RICHLAND, Wash. – Workers recently performed a series of precision crane lifts to safely place and assemble a 111-ton electrical powerhouse for the Effluent Management Facility (EMF) at EM’s Office of River Protection (ORP) Waste Treatment and Immobilization Plant (WTP).
With the powerhouse in place, crews can begin routing permanent plant electricity to the effluent facility, the last major construction project to support the Direct Feed Low-Activity Waste (DFLAW) approach. Through the DFLAW vitrification approach, ORP will begin treating tank waste no later than 2023.
“Receiving the powerhouse is an important step for EMF progress as it allows us to route electrical cables to the building and sets the stage for its first construction turnover to the startup testing phase,” said Jason Young, EM’s ORP Balance of Facilities federal project director.
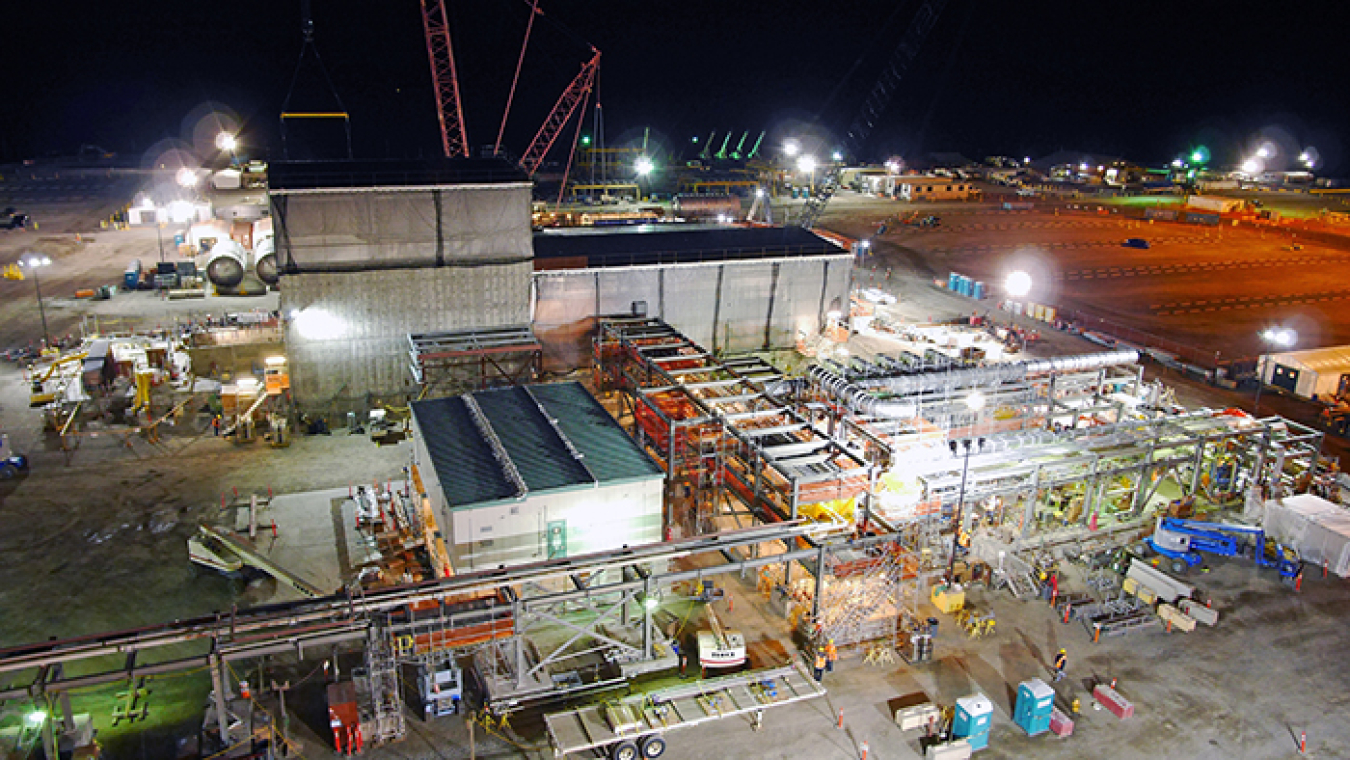
The powerhouse contains transformers, motor control centers, and more than 11,000 feet of electrical raceway and cable. The 13.8-kilovolt powerhouse will provide electricity to EMF systems and processing equipment.
The modular-style powerhouse was fabricated in Texas and transported atop a specialized semi-trailer truck to Washington. It arrived in three pre-fabricated sections, which crews then assembled.
“This was an outstanding effort by the entire team,” said Scott Monson, area manager for DFLAW at Bechtel National, Inc., the WTP Project contractor. “The team worked seamlessly from the design phase to working with the fabricator in their shop, then coordinating a 2,100-mile journey to final assembly at the jobsite.”