Growing America’s Energy Future: Bioenergy Technologies Office Successes of 2014
Building on 2013 successes, 2014 was a year of many BETO achievements, including cellulosic ethanol biorefinery openings and reductions toward cost goals for hydrocarbon fuels.
2014 built on previous BETO successes:
- In 2012, BETO successfully demonstrated two biofuel pathways that can produce cellulosic ethanol at a modeled nth plant cost of approximately $2 per gallon—a 77% reduction in cost from an estimated $9.16 in 2001. This milestone was accomplished through DOE support of research and development (R&D) at national laboratories, academic institutions, and industry.
- In 2013, the nation’s first cellulosic ethanol biorefinery, INEOS Bio’s Indian River BioEnergy Center in Vero Beach, Florida, held its grand opening, made possible by $50 million in cost-shared DOE funding.
POET-DSM and Abengoa: Grand Openings of Cellulosic Ethanol Biorefineries
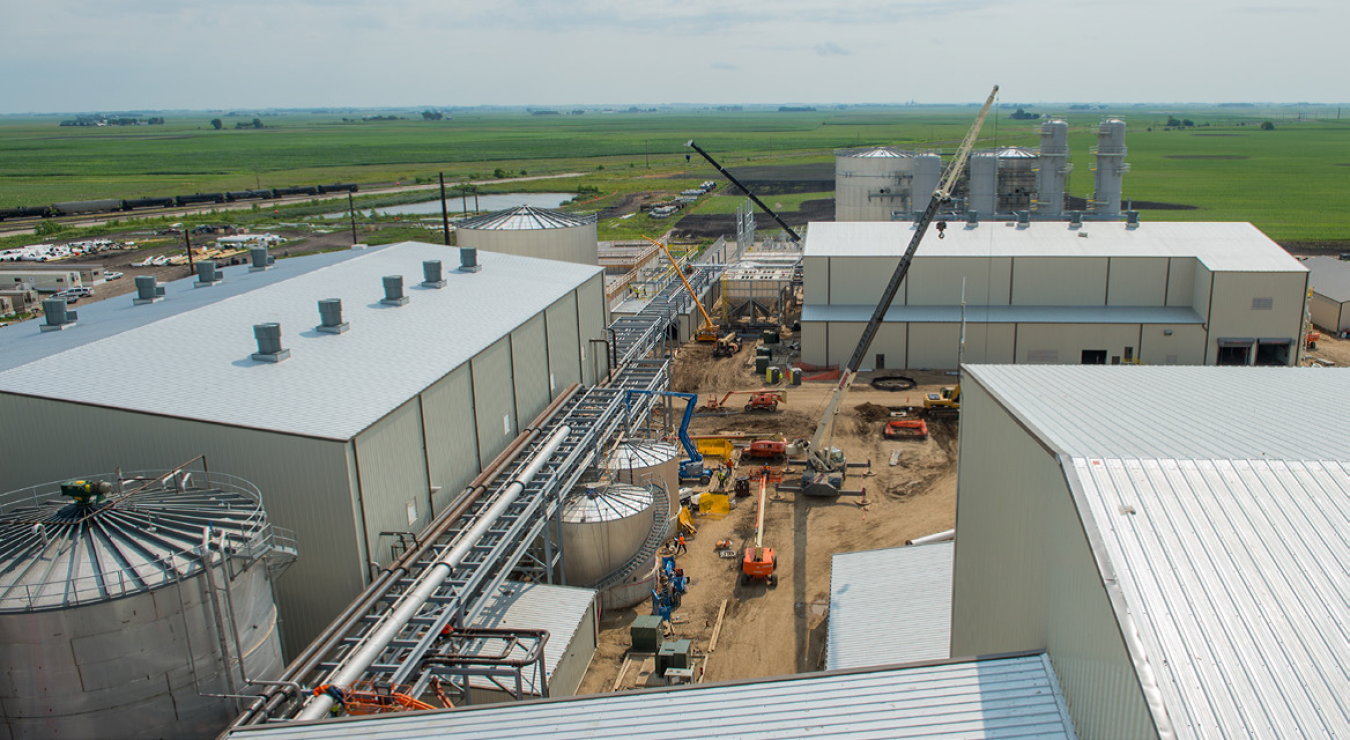
POET-DSM’s Project LIBERTY cellulosic ethanol biorefinery in Emmetsburg, Iowa, was made possible with $100 million in BETO cost-shared funding.
In September and October 2014, POET-DSM’s Project LIBERTY in Emmetsburg, Iowa, and Abengoa’s Bioenergy Biomass of Kansas facility in Hugoton, Kansas, held their grand openings, becoming the first U.S. biorefineries to use corn stover (corn husks, cobs, stalks, and residue), as a feedstock and the second and third commercial-scale cellulosic ethanol plants in the nation. POET-DSM and Abengoa each received $100 million in BETO cost-shared funding over seven years to design and construct their facilities. Abengoa also received a $132 million loan guarantee from the DOE Loan Programs Office. These two biorefineries have the combined capacity to produce 50 million gallons of cellulosic ethanol per year—enough to avoid 400,000 tons of carbon dioxide emissions annually. During the construction of Project LIBERTY, POET employed approximately 300 workers and now employs 56 permanent workers at the facility. Abengoa employed approximately 1,200 temporary workers during construction and created 65 permanent jobs at the plant. Both facilities use feedstocks harvested by local farmers.
First U.S. Cellulosic Ethanol Commercial Shipment and Woody Biomass RINs
In the spring of 2014, INEOS made the first U.S. commercial shipment of cellulosic ethanol to the International Motor Sports Association Green Racing Series. Also in the spring, American Process Inc. began producing at pilot scale renewable identification number (RIN)-qualifying quantities of cellulosic ethanol, marking the first production of cellulosic ethanol from mixed forest residue. Both companies received BETO funding.
Three Years of Algae Research Published
The National Alliance of Advanced Biofuels and Bioproducts released its close-out report, culminating three years of research from $50 million in funding from the American Recovery and Reinvestment Act of 2009. Advancements included higher algae productivity, 30 new algae strains, a higher-efficiency filtration system for harvesting algae from open pond systems, and a hydrothermal liquefaction conversion process to convert whole algae to biofuels. If combined, these innovations could reduce the price of algae-based biofuels to $7.50 per gallon, compared to a starting cost estimate of more than $20 per gallon in 2010.
Completed Feedstock Logistics Projects Demonstrate Significant Cost Reductions
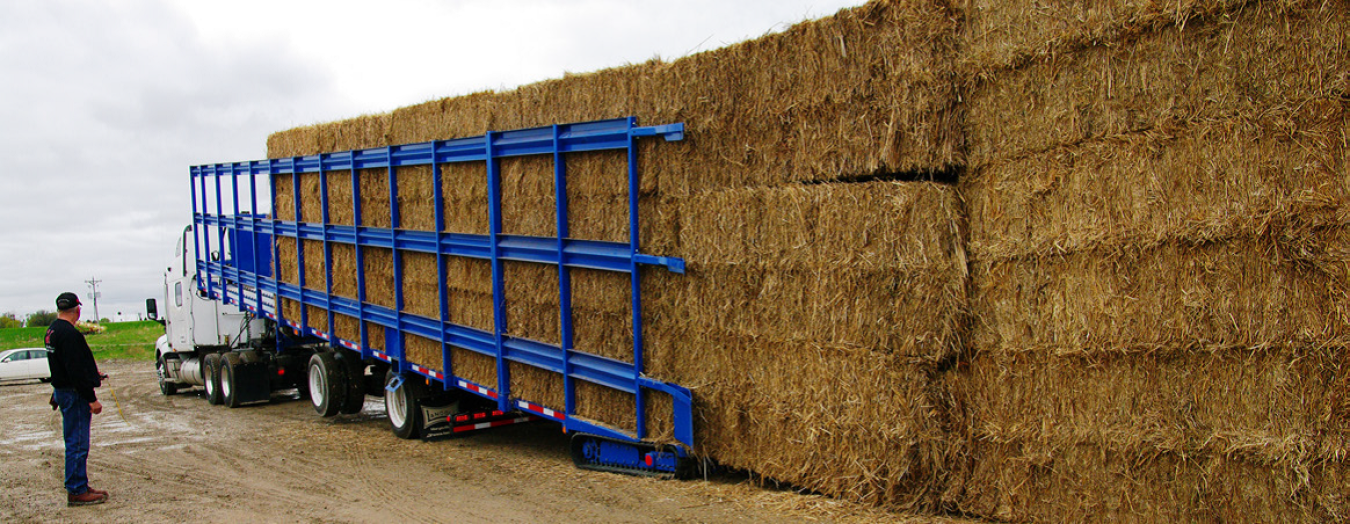
FDC Enterprises’ self-loading/unloading trailer, developed with BETO funding in partnership with Kelderman Manufacturing, can pick up a stack of 36 corn stover bales in five minutes.
As of late 2014, all five BETO-funded high-tonnage feedstock logistics projects (2010 funding) have been completed, demonstrating significant cost reductions ($13 per dry matter ton on average) for collecting, storing, and transporting cellulosic feedstocks. AGCO Corporation, FDC Enterprises, TennEra LLC, the State University of New York College of Environmental Science and Forestry, and Auburn University worked in partnership with original equipment manufacturers to develop commercial harvesting equipment for corn stover, switchgrass, and woody biomass feedstocks. Some of these technologies are already on the commercial market. Demonstrated cost reductions include:
- AGCO Corp.: 29% reduction ($51.54 per dry ton to as low as $36.75 per dry ton) for single-pass harvesting, high-density baling, and modified trailers.
- FDC Enterprises: 25% reduction ($50.78 per dry ton to as low as $37.89 per dry ton) for self-propelled balers, high-density balers, self-propelled bale pickup trucks, and self-loading/unloading trailers.
- TennEra LLC: 7% reduction ($56.38 per dry ton to $52.34 per dry ton) for field chopping, bulk handling, and storage.
Defense Production Act Biorefineries Progress to Construction Stage
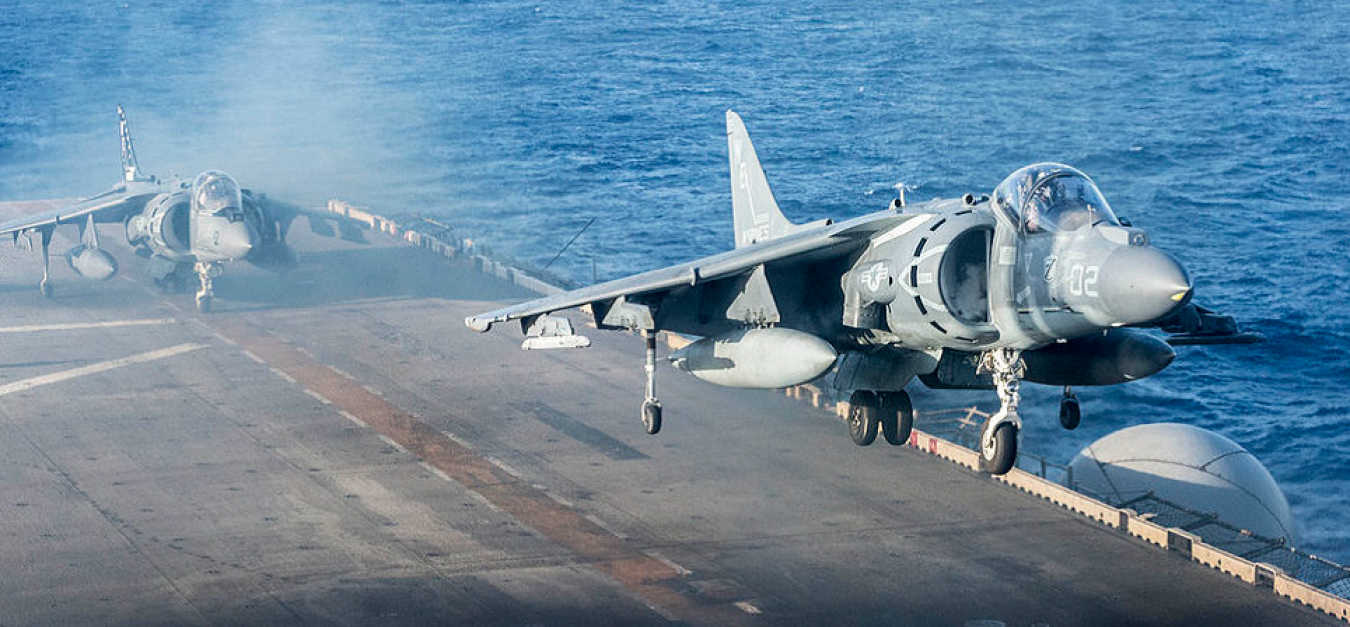
Three new biorefineries will produce renewable jet and diesel fuel for the military.
In 2011, the Secretaries of Agriculture, Energy, and Navy signed a memorandum of understanding to commit $510 million ($170 million from each agency) to produce renewable jet and diesel fuels in the near term. In September 2014, three biorefinery projects were selected to continue to construction stage with Phase II funding (up to $70 million each): Emerald Biofuels (82 million gallons per year capacity from waste fats); Fulcrum BioEnergy (10 million gallons per year capacity from municipal solid waste); and Red Rock Biofuels (12 million gallons per year capacity from woody biomass).
Tool Quantifies Biofuel Water Footprint
In partnership with BETO, Argonne National Laboratory released WATER, version 2.0, the first national-scale, U.S.-centered model for quantifying the water footprint of various biofuel pathways. This tool advances responsible deployment of bioenergy technologies under water constraints by providing analytical and decision-making support to researchers, feedstock producers, biorefineries, and federal and state policymakers. Sustainable bioenergy production relies on aligning water demands with water availability, protecting water supplies and aquatic ecosystems, and maximizing the use of impaired—rather than pristine—water for growing feedstocks. WATER 3.0 has since been released with additional features.
Conversion Cost Target Reached
BETO’s thermochemical conversion R&D achieved a $4.09 per gallon gasoline equivalent (GGE) modeled mature conversion cost of advanced biofuels, which translates to a fuel selling price of $5.26 per GGE, based on an nth plant modeled price (a reduction of $0.51 from fiscal year 2013). Reaching this milestone keeps BETO on track to validate a modeled mature price of $3 per GGE for advanced biofuel by 2017 for one technology route, reducing GHG emissions by at least 50% compared to gasoline.
Looking ahead, BETO will continue to support activities to advance the sustainable, nationwide production of advanced biofuels.