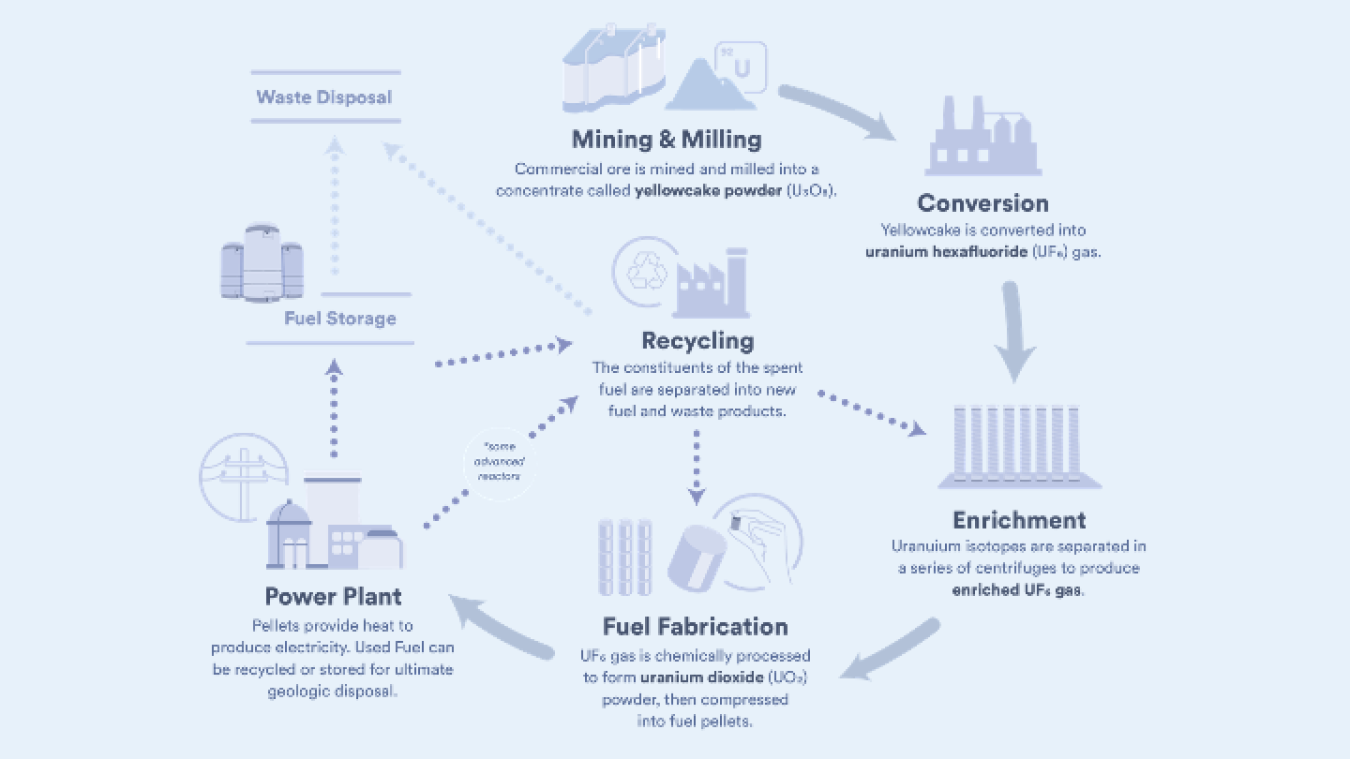
The nuclear fuel cycle is made up of two phases: the front end and the back end.
The front end prepares uranium for use in nuclear reactors. These steps include mining, milling, conversion, enrichment, and fuel fabrication. The back end ensures that the used nuclear fuel is safely managed, recycled, or disposed of. These steps include fuel storage, recycling, and waste disposal.
Uranium Mining
Uranium ore is recovered through conventional open pit, underground mining, and in situ techniques. In open pit mining, where deposits are close to the surface, overlying rock is stripped out, creating the open pit. For deeper deposits of uranium, underground mines are dug, with smaller surface disturbance and much less material being removed to access the ore. Underground mines require special precautions for increased ventilation to protect against airborne radon exposure.
In situ recovery (ISR) is now used more frequently to recover uranium globally. Oxygenated groundwater is circulated through a very porous orebody to dissolve the uranium oxide before it’s pumped to the surface treatment plant for recovery. ISR may be with slightly acid or with alkaline solutions to keep the uranium in solution. The uranium oxide is then recovered from the solution as in a conventional mill. ISR mining reduces the ground disturbance and is less operator/personnel-intense compared to conventional mines.
Links
Nuclear Fuel Cycle
Nuclear Fuel Facts: Uranium
Policy Documents
November 15, 2016
Excess Uranium Management
July 1, 2016
Request for Information - July 2016
May 1, 2015
2015 Secretarial Determination
March 1, 2015
Notice of Issues for Public Comment - March 2015
May 15, 2014
Secretarial Determination of No Adverse Material Impact for Uranium Transfers
Uranium Milling and Processing
Once the ore is mined, it is typically milled on site into a uranium oxide concentrate, often known as “yellowcake”. In the milling process, uranium is extracted from the crushed and ground-up ore by leaching, in which either a strong acid or a strong alkaline solution is used to dissolve the uranium oxide. The uranium oxide is then precipitated and removed from the solution. After drying and usually heating, it is packed in drums as a concentrate.
The remainder of the ore, nearly all the rock material, becomes tailings, which are emplaced in engineered facilities near the mine (often in a mined-out pit). Tailings are isolated from the environment because they contain long-lived radioactive materials in low concentrations and toxic materials such as heavy metals. The tailings are placed into a pond in the ground on top of a plastic liner to prevent leakage. The waste is then covered with a layer of soil and then water. In ISR facilities, uranium is concentrated and extracted from solutions into uranium oxide concentrate at a processing plant. As in conventional mining, one processing facility may serve a number of ISR operations. See the U.S. Energy Information Administration website for more information on uranium production.
Conversion
For most types of reactors, the concentration of the fissile 235U isotope in natural uranium must be enriched typically to between 3 percent and 5 percent. Natural uranium oxide from mines and processing plants is chemically converted into uranium hexafluoride (UF6), a compound that when heated forms a gas that can be fed into enrichment plants. There are only three conversion facilities outside of Russia and China. These are located in the United States, Canada, and France.
Enrichment
The enrichment process separates gaseous uranium hexafluoride into two streams, one being enriched to the required level known as low-enriched uranium (LEU); the other stream is progressively depleted in 235U and is called “tails," or simply depleted uranium.
Gas centrifuge technology using uranium hexafluoride gas as feed is the sole method of commercial enrichment.
This process uses the physical properties of molecules, specifically the 1 percent mass difference between the two uranium isotopes, to separate them. Another technology that can be used to enrich uranium is called laser enrichment. This technology has not been utilized at the commercial level and is undergoing technology development.
Gas Centrifuge Enrichment
The gas centrifuge like the diffusion process uses UF6 gas as its feed and makes use of the slight difference in mass between 235U and 238U. The gas is fed into a series of vacuum tubes rotated at very high speeds to obtain efficient separation of the two isotopes. The slightly heavier 238U isotope is concentrated closer to the cylinder wall with the lighter 235U increasing toward the center of the cylinder where it can be drawn off. Although the capacity of a single centrifuge is much smaller than that of a single diffusion stage, its separative capability is significantly greater. In the centrifuge process, the number of stages may only be 10 to 20, instead of a thousand or more for diffusion. Centrifuge stages are arranged in parallel into cascades. The gas centrifuge technology consumes only about 5 percent as much electricity as the gaseous diffusion technology to produce a given amount of product.
Laser Separation Enrichment
Laser separation uses laser technology to selectively excite 235U, the fissile isotope, from the much more abundant 238U isotope. This technology promises to provide improved enrichment method as compared to first generation gaseous diffusion and second generation gaseous centrifugation methods.
No laser separation uranium enrichment plants are currently operating in the United States.
Fuel Fabrication
Enriched UF6 is shipped to a fuel fabrication facility where it is heated back to a gas and chemically processed to uranium dioxide powder. The powder is pressed into ceramic pellets and sintered (baked) at a high temperature (over 2550 F).
The pellets are then encased in metal tubes to form fuel rods, which are arranged into a fuel assembly ready for introduction into a reactor. The dimensions of the fuel pellets and other components of the fuel assembly are precisely controlled to ensure consistency in the characteristics of the fuel. Nuclear fuel assemblies are specifically designed for particular types of reactors and are made to quality assurance specifications. The most common reactor, the pressurized-water reactor (PWR), contains 150-200 fuel assemblies, whereas the boiling-water reactor, the second most common reactor, contains 370-800 fuel assemblies.
In a fuel fabrication plant great care is taken with the size and shape of processing vessels to avoid criticality (a limited chain reaction releasing radiation). With low-enriched fuel criticality is most unlikely, but in plants handling special fuels for research reactors this is a vital consideration.
There are currently three fuel fabrication plants in the U.S.
Power Reactor
Generation of electricity in a nuclear reactor is similar to a coal-fired steam station. The difference is the source of heat. Fissioning, or splitting, of uranium atoms produces energy in the same way burning coal, gas, or oil is used as a source of heat in fossil fuel power plants. The fuel used in nuclear generation is 235U. The process of producing electricity begins when uranium atoms are split (i.e., fission) by particles known as neutrons. 235U has a unique quality that causes it to break apart when it collides with a neutron. Once an atom of 235U is split, neutrons from the uranium atom collide with other atoms of the 235U. A chain reaction begins that produces heat. This heat is used to heat water and turn it into steam. The steam is used to drive a turbine connected to a generator that produces electricity.
Recycling
Spent nuclear fuel can be recycled to make new fuel and byproducts. More than 90% of its potential energy still remains in the fuel, even after five years of operation in a reactor. The United States does not currently recycle spent nuclear fuel but foreign countries, such as France, do. There are also some advanced reactor designs in development that could consume or run on spent nuclear fuel in the future.
The Office of Nuclear Energy currently supports research and development activities to evaluate the options for recycling valuable components of irradiated nuclear fuel aimed to achieve a circular economy and reduce the ultimate volume of high-level nuclear waste to be dispositioned.
Fuel Storage
Spent fuel refers to the nuclear fuel that has been used in a reactor. The fuel is a solid when it goes into the reactor and a solid when it comes out. The nation’s spent nuclear fuel is initially stored in steel-lined concrete pools surrounded by water. It’s later removed from the pools and placed into dry storage casks that are made of steel and concrete or other materials used for protective shielding. Most of the nation’s spent fuel is safely and securely stored at more than 70 reactor sites across the country. Roughly a quarter of these sites no longer have a reactor in operation.
The U.S. Department of Energy is now exploring the possibility of consolidating this spent nuclear fuel at one or more federal interim storage facilities using a consent-based siting process. For the foreseeable future, the spent fuel can safely stay at the reactor sites or a future consolidated interim storage facility until a permanent disposal solution is determined by the federal government.
Waste Disposal
The Office of Nuclear Energy is responsible for ongoing research and development related to long-term disposition of spent nuclear fuel and high-level radioactive waste.
The mission of the Office of Spent Fuel and Waste Disposition (SFWD), which manages this work, is to protect people and the environment, now and in the future, by establishing an integrated system for storage, transportation, and disposal of the nation’s spent nuclear fuel and high-level radioactive waste.
Learn more- Spent Fuel and Waste Disposition | Department of Energy