Tennessee Valley Authority recently installed first-of-a-kind 3D-printed fuel assembly brackets at its Browns Ferry nuclear power plant.
August 23, 2021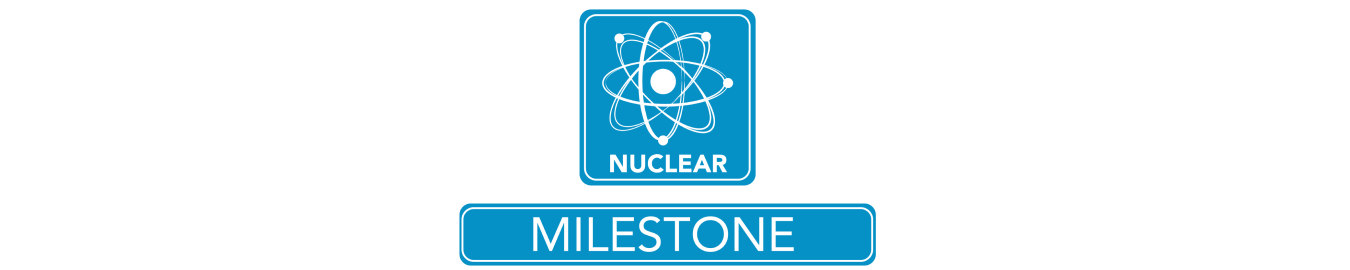
Tennessee Valley Authority (TVA) recently installed four 3D-printed fuel assembly brackets at its Browns Ferry nuclear power plant. The brackets are the first safety-related 3D-printed components to be placed in a commercial reactor.
The first-of-a-kind brackets were installed during a planned refueling outage that ended in April and will remain in the reactor for six years, with regular inspections during planned outages.
Delivering 3D-Printed Components
Oak Ridge National Laboratory (ORNL) additively manufactured the channel fasteners for Framatome’s boiling water reactor fuel assembly using a micro-welding process. The team created a 3D-printed part compliant with reactor safety regulations for deployment in a commercial reactor. The lab also provided the 3D digital data captured during the manufacturing process that details each layer of the print, which can then be used to certify the quality of the bracket.
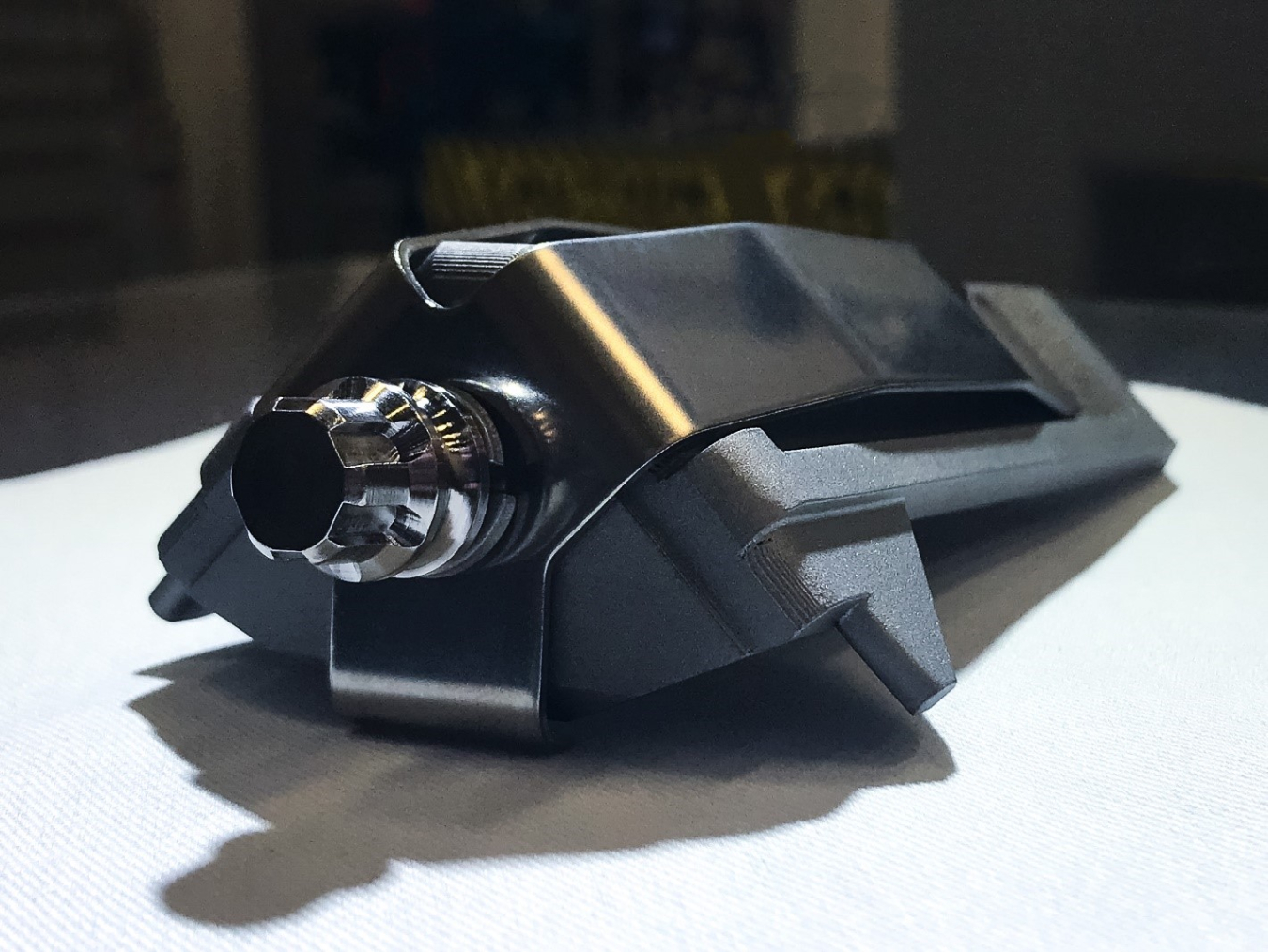
ORNL manufactured the components in a joint project with TVA and the utility’s fuel supplier, Framatome, as part of the lab’s Transformational Challenge Reactor (TCR) program. The demonstration program is designed to introduce new manufacturing techniques and approaches to industry partners in order to speed up the deployment of nuclear systems.
“Deploying 3D-printed components in a reactor application is a great milestone,” said Ben Betzler, ORNL’s TCR program director. “It shows that it is possible to deliver qualified components in a highly regulated environment. This program bridges basic and applied science and technology to deliver tangible solutions that show how advanced manufacturing can transform reactor technology and components.”
A New Manufacturing Approach
Additive manufacturing and artificial intelligence techniques eliminate conventional manufacturing limitations by providing rapid prototype production and testing. Introducing this innovative manufacturing approach could lay the groundwork for use across the existing nuclear fleet and new reactor technologies.
The TCR program’s approach is informed by high fidelity modeling and simulation and predictive analytics. The channel fasteners developed for this project perform an essential function in the fuel assembly to assure its proper positioning in the reactor core. They are easy to fabricate using the new manufacturing techniques, making them an ideal match to demonstrate this novel process. The knowledge gained from this project could open the door to additively manufacturing more complex parts moving forward.
“Collaborating with TVA and ORNL allows us to deploy innovative technologies and explore emerging 3D printing markets that will benefit the nuclear energy industry,” said John Strumpell, manager of North America Fuel R&D at Framatome. “This project provides the foundation for designing and manufacturing a variety of 3D-printed parts that will contribute to creating a clean energy future.”
The TCR program is funded by the Office of Nuclear Energy within the U.S. Department of Energy. The program aims to accelerate design, manufacturing, qualification, and deployment of advanced nuclear energy systems. Learn more about TCR program goals and the office’s work in advanced manufacturing.