GE's new nuclear fuel designs will soon be tested in a commercial reactor. This is why it's a big deal.
February 16, 2018General Electric recently announced plans to test a pair of nuclear fuel designs in a commercial reactor later this month in Georgia.
This is big news for the U.S. nuclear industry as it continues to develop new technologies to further enhance the safety and performance of its nuclear fuels.
It’s also an important milestone for the U.S Department of Energy (DOE).
GE’s IronClad fuel design will be the first key component tested in a commercial nuclear reactor that was developed through DOE’s accident tolerant fuels program.
This is an important accomplishment made possible by a great collaboration between the government, our labs and industry partners. It’s also what we refer to as a win-win for industry and the nation.
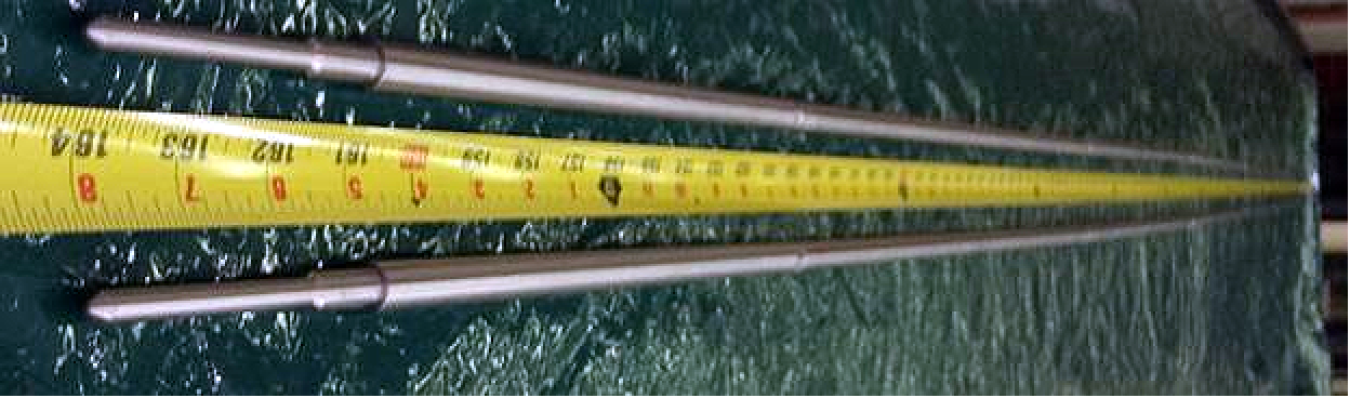
Accident-Tolerant Fuels
An accident-tolerant fuel is an industry term used to describe new technologies that further enhance the safety and performance of nuclear materials. This can be in the form of new cladding and/or fuel pellet designs.
DOE’s program started in 2012 in the wake of the Fukushima accident to support industry in identifying and developing these new advanced fuels.
GE’s Global Nuclear Fuel, Framatome, and Westinghouse are all working with DOE to help bring their fuel concepts to market within the next 10 years. All three companies have been able to save time and money by working with our technical experts, the national labs, and the Nuclear Regulatory Commission on areas ranging from data generation and modeling simulation to the fabrication of their fuels.
The IronClad Fuel Concept

Global Nuclear Fuel’s IronClad concept, developed in cooperation with Oak Ridge National Laboratory, uses a combination of iron, chromium and aluminum for its fuel cladding to improve the fuel’s behavior under severe accident scenarios. The steel material has a much lower oxidation rate when exposed to high temperature steam. This improves the safety margins at higher temperatures over traditional zirconium cladding used today.
The company is also testing a second fuel concept known as ARMOR—a coated zirconium cladding—that was developed outside of the DOE program.
What's Next?
Global Nuclear Fuel and Southern Nuclear Operating Company will load the first lead test assemblies into Georgia’s Plant Hatch later this month. The material will be tested without any fuel this year. The GE team is planning to deploy lead test assemblies with fuel in 2019.
Framatome and Westinghouse both have plans to test their accident-tolerant fuel designs within one year’s time.
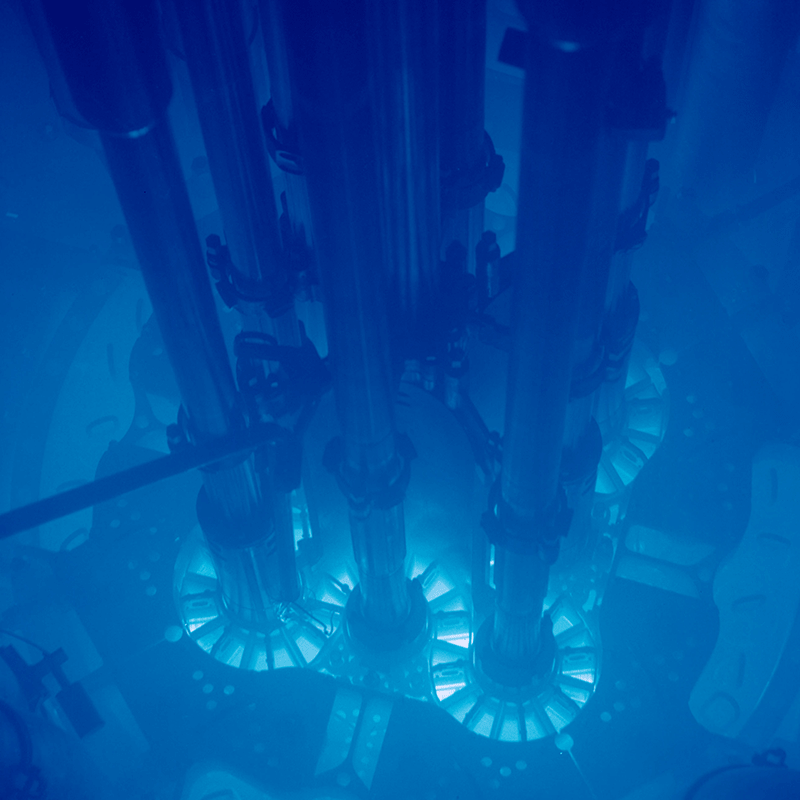
Explore More
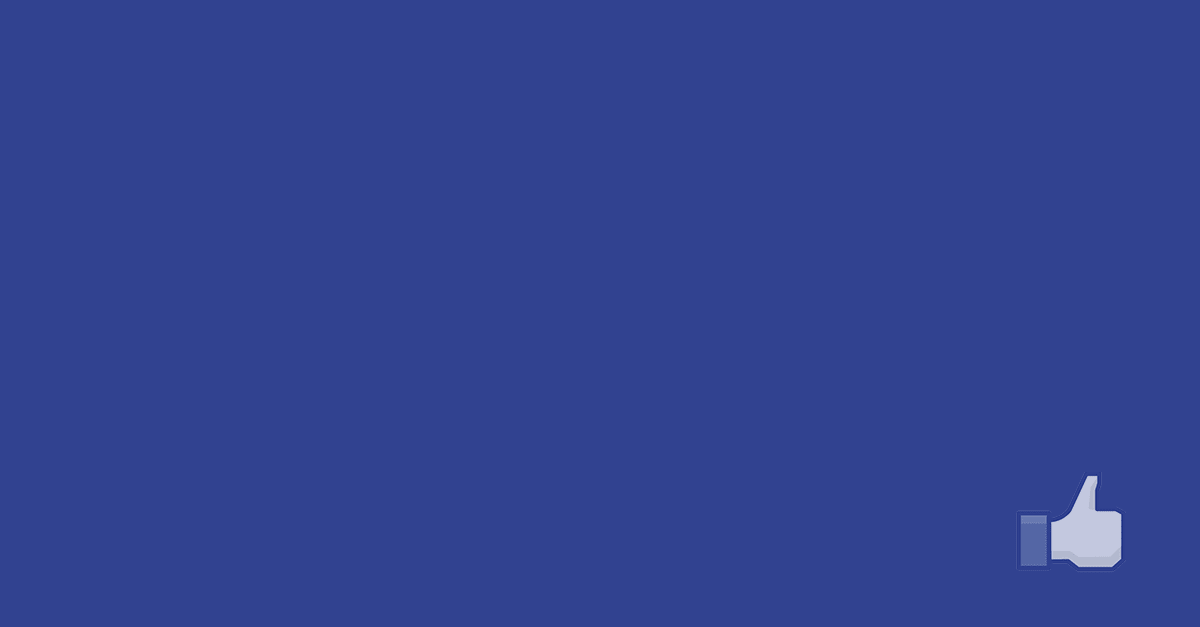
Join the Conversation
Edward McGinnis
Edward McGinnis was formerly the acting Assistant Secretary for the Office of Nuclear Energy. Prior to that role, he served as the Principal Deputy Assistant Secretary for Nuclear Energy and the Deputy Assistant Secretary for International Nuclear Energy Policy and Cooperation. As Deputy Assistant Secretary, he was responsible for the Department of Energy's international civilian nuclear energy activities, including international nuclear energy research, development and demonstration cooperation, multilateral nuclear energy cooperation, international nuclear energy policy, international nuclear safety cooperation, and advocacy for U.S. civil nuclear exports and industry. As part of these responsibilities, Mr. McGinnis served as Steering Group Chairman of the International Framework for Nuclear Energy Cooperation that consists of more than 65 countries and 4 international organizations. He also served as the Departmental Representative in the U.S. interagency for civil nuclear energy trade and promotion. Mr. McGinnis has also served as a Vice Chairman and Principal U.S. Representative to the Generation IV International Forum and was responsible for U.S. domestic nuclear fuel assurance matters, including technical oversight activities regarding the United States Enrichment Corporation, uranium inventory management matters, as well as U.S. nuclear energy security matters.
Prior to working in the Office of Nuclear Energy, Mr. McGinnis led a number of other high-priority U.S. government initiatives at DOE, including having served as the senior director for the Office of Global Radiological Threat Reduction where he managed global operations involving the search, recovery, security, and disposal of high-risk radiological and nuclear sources in cooperation with over 40 countries, including within the United States. These activities included recovery of high-risk radiological sources from Iraq, establishment of a Global Radiological Regional Partnership Program, and the first-of-its-kind repatriation of high-risk U.S.-origin plutonium-239 sources. Mr. McGinnis also established and served as the director of the Nuclear and Radiological Threat Reduction Task Force, which was created to carry out a number of key Secretarial national security initiatives, including the development of a global nuclear materials removal and research reactor security study that included the identification of nuclear research reactors throughout the world by level of vulnerability and an action plan to effectively mitigate such vulnerabilities.
Mr. McGinnis also served as senior advisor and special assistant to four Assistant Secretaries and Deputy Administrators for nonproliferation and national security at the Department of Energy where he served as a senior advisor for all aspects of the Department's nonproliferation missions, including nonproliferation research and development, materials protection, control and accounting, and warhead security.
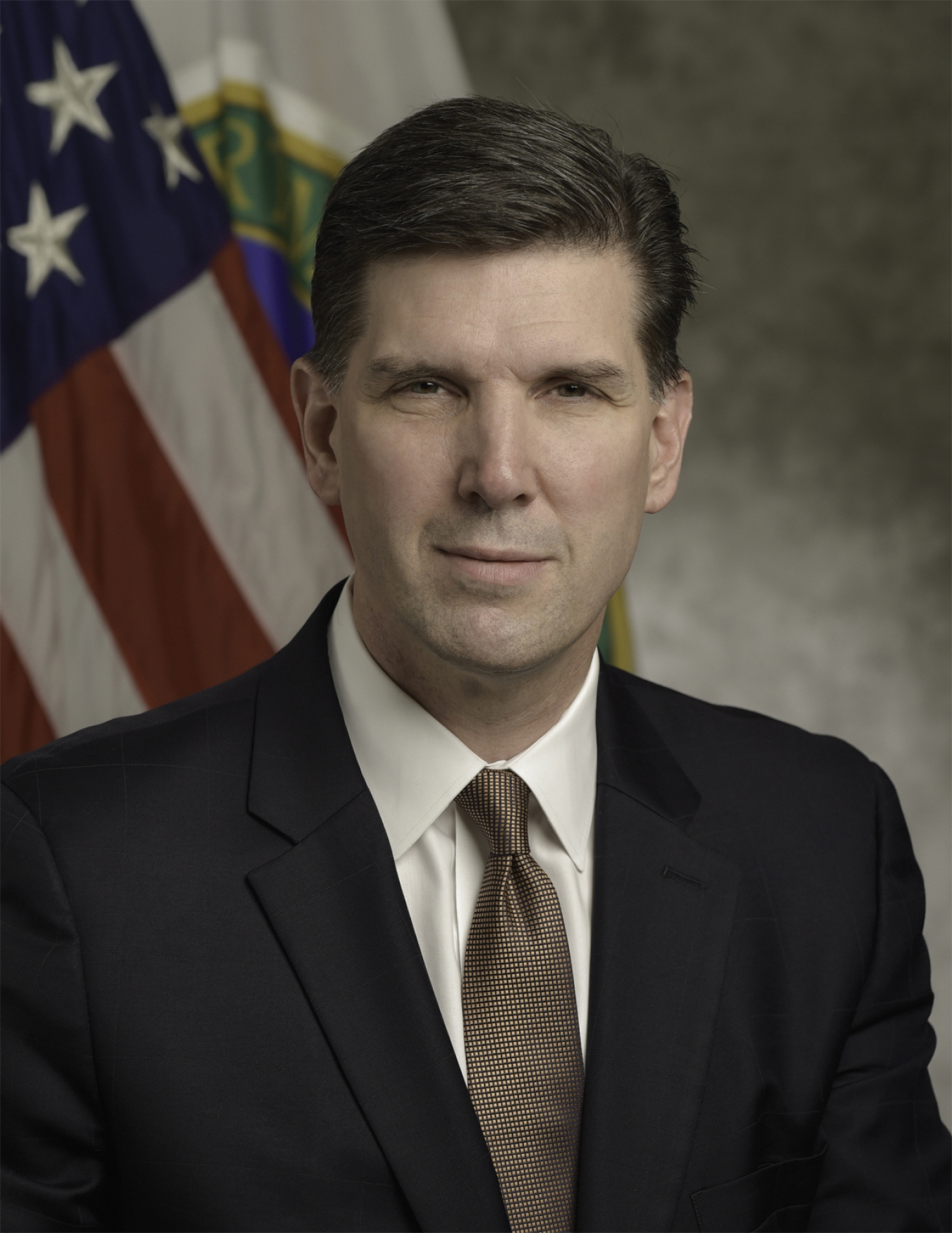
Edward McGinnis is the acting Assistant Secretary for the Office of Nuclear Energy. The Office is responsible for conducting research on current and future nuclear energy systems, maintaining the government’s nuclear energy research infrastructure, establishing a path forward for the nation’s spent nuclear fuel and high-level nuclear waste management program, and a host of other national priorities.
Prior to this role, he served as the former Principal Deputy Assistant Secretary for Nuclear Energy and the Deputy Assistant Secretary for International Nuclear Energy Policy and Cooperation. As Deputy Assistant Secretary, he was responsible for the Department of Energy's international civilian nuclear energy activities, including international nuclear energy research, development and demonstration cooperation, multilateral nuclear energy cooperation, international nuclear energy policy, international nuclear safety cooperation, and advocacy for U.S. civil nuclear exports and industry. As part of these responsibilities, Mr. McGinnis served as Steering Group Chairman of the International Framework for Nuclear Energy Cooperation that consists of more than 65 countries and four international organizations. He also served as the Departmental Representative in the U.S. interagency for civil nuclear energy trade and promotion. Mr. McGinnis has also served as a Vice Chairman and Principal U.S. Representative to the Generation IV International Forum and was responsible for U.S. domestic nuclear fuel assurance matters, including technical oversight activities regarding the United States Enrichment Corporation, uranium inventory management matters, as well as U.S. nuclear energy security matters.
Prior to working in the Office of Nuclear Energy, Mr. McGinnis led a number of other high-priority U.S. government initiatives at DOE, including having served as the senior director for the Office of Global Radiological Threat Reduction where he managed global operations involving the search, recovery, security and disposal of high-risk radiological and nuclear sources in cooperation with over 40 countries, including within the U.S. These activities included recovery of high-risk radiological sources from Iraq, establishment of a Global Radiological Regional Partnership Program, and the first-of-its-kind repatriation of high-risk U.S.-origin plutonium-239 sources. Mr. McGinnis also established and served as the director of the Nuclear and Radiological Threat Reduction Task Force, which was created to carry out a number of key Secretarial national security initiatives, including the development of a global nuclear materials removal and research reactor security study that included the identification of nuclear research reactors throughout the world by level of vulnerability and an action plan to effectively mitigate such vulnerabilities.
Mr. McGinnis also served as senior advisor and special assistant to four Assistant Secretaries and Deputy Administrators for nonproliferation and national security at the Department of Energy where he served as a senior advisor for all aspects of the Department's nonproliferation missions, including nonproliferation research and development, materials protection, control and accounting, and warhead security.
Mr. McGinnis holds a master's degree from The American University's School of International Service in Washington, D.C., and is a graduate of the Kennedy School's Senior Executive Fellows Program as well as the Program for Senior Executives in National and International Security at Harvard University.