Crew members used ingenuity and lessons learned to develop a conveyor system to safely remove material containing asbestos from inside a building.
Office of Environmental Management
July 2, 2019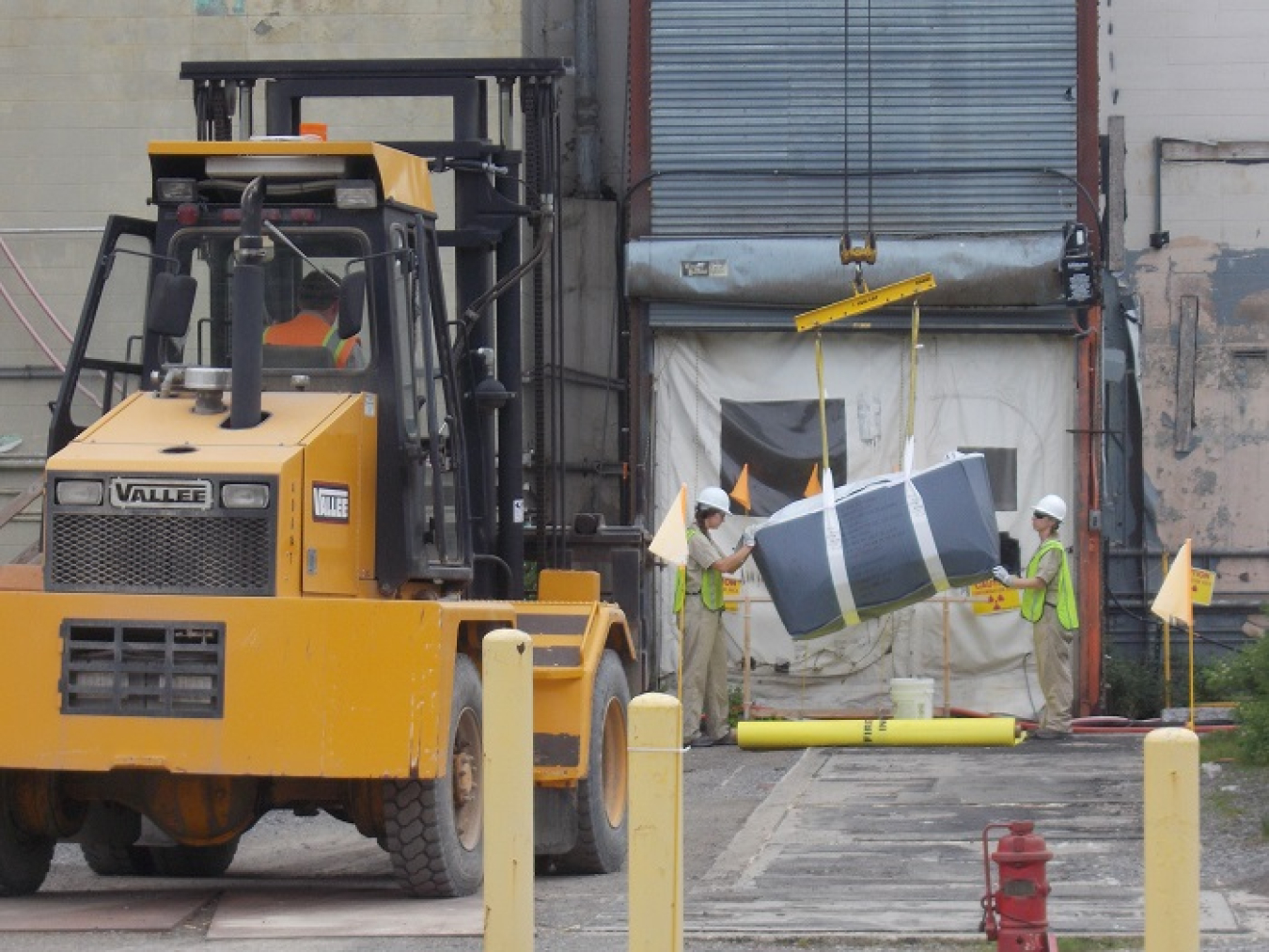
WEST VALLEY, N.Y. – EM deactivation and decommissioning (D&D) crew members used ingenuity and lessons learned to develop a conveyor system to safely remove material containing asbestos from inside a building at the West Valley Demonstration Project.
Workers used the conveyor system to get rid of about 56,000 pounds of plaster containing asbestos material from the walls of a control room on the fourth floor of the Main Plant Process Building. They are clearing away asbestos material to prepare the structure for demolition.
The crew helped design, test, and build the conveyor system to further improve safety and limit contact with asbestos material during the project. Drawing from lessons learned from previous work, the team built the system with readily available equipment, saving time and money.
“This team took an issue and turned it into an opportunity by putting their knowledge into practice,” EM WVDP Federal Project Director Dan Sullivan said. “The safe and compliant disposition of asbestos-containing material is another important step in the progress towards the future demolition of the Main Plant.”
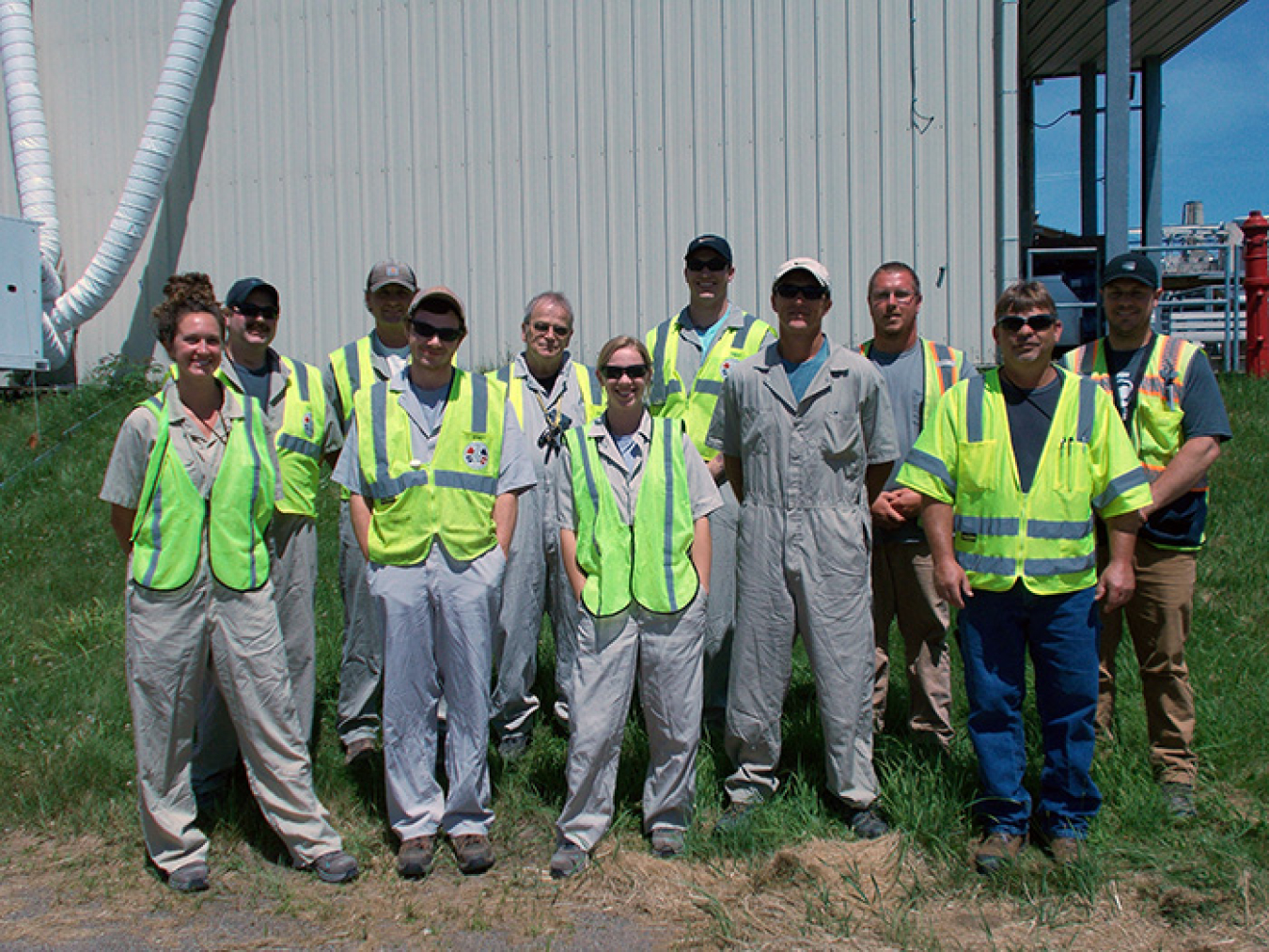
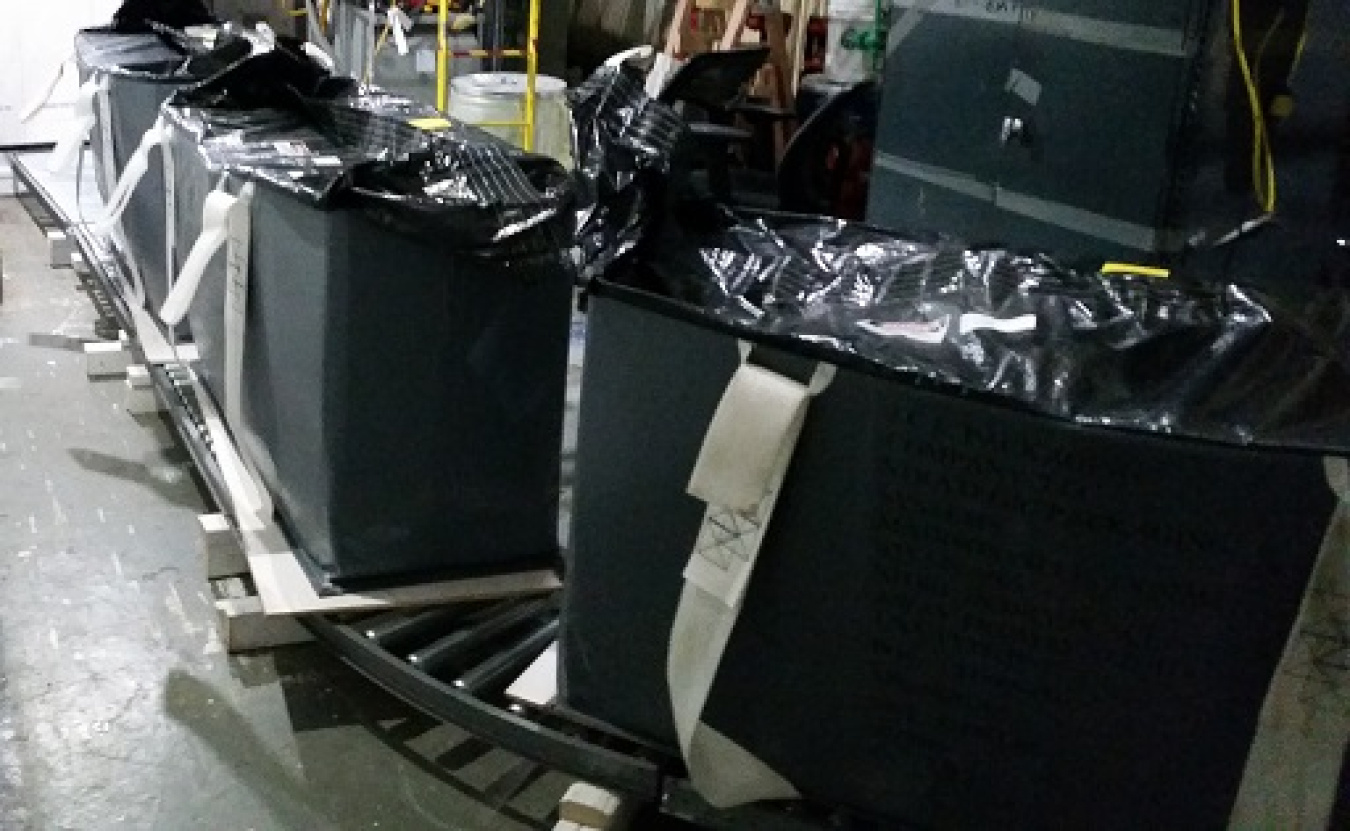
Crew members filled 25-pound-capacity bags with the asbestos material and placed them into 900-pound-capacity lift bags. They transported the lift bags on the conveyor system from inside the building to an outside overhead crane. The crane lowered each lift bag to the ground where a fork truck added them to a waste container for off-site disposal.
Dale Macklem, D&D manager with EM cleanup contractor CH2M HILL BWXT West Valley, commended his crew for the creativity to turn an idea into reality.
“Working with asbestos-containing material is the most physically challenging work at the site when you include radiological and industrial hazards, layers of protective clothing, and warm temperatures,” Macklem said. “This crew used lessons learned to enhance safety, improve efficiency, and reduce exposure to job-related hazards. They put their collective knowledge into practice, and that’s to be commended.”
Constructed in the 1960s, the Main Plant, a commercial reprocessing facility, was used to recover reusable plutonium and uranium from spent nuclear reactor fuel.
The crew will use the conveyor system to remove asbestos-containing material from the three-story Main Plant Office Building before demolishing that structure later this year.