Workers have successfully deactivated another high-hazard cell of the Main Plant Process Building, moving the facility closer to demolition, an EM 2022 priority at the West Valley Demonstration Project (WVDP).
Office of Environmental Management
August 16, 2022WEST VALLEY, N.Y. – Workers have successfully deactivated another high-hazard cell of the Main Plant Process Building, moving the facility closer to demolition, an EM 2022 priority at the West Valley Demonstration Project (WVDP).
EM and cleanup contractor CH2M HILL BWXT West Valley (CHBWV) finished deactivating the Ventilation Wash Room (VWR), which housed a ventilation "scrubber” that removed airborne particulates resulting from fuel reprocessing operations that ceased in 1972.
The scrubber will be removed during the Main Plant demolition. Crews have prepared that equipment for removal.
“The safe execution of this work is due to the combination of extensive planning, deliberate speed and use of worker feedback throughout the deactivation,” said Steve Bousquet, EM WVDP federal project director for the Main Plant demolition. “The WVDP team continues its strong commitment to safely protecting its workers, the public and the environment while reducing legacy risks at the site.”
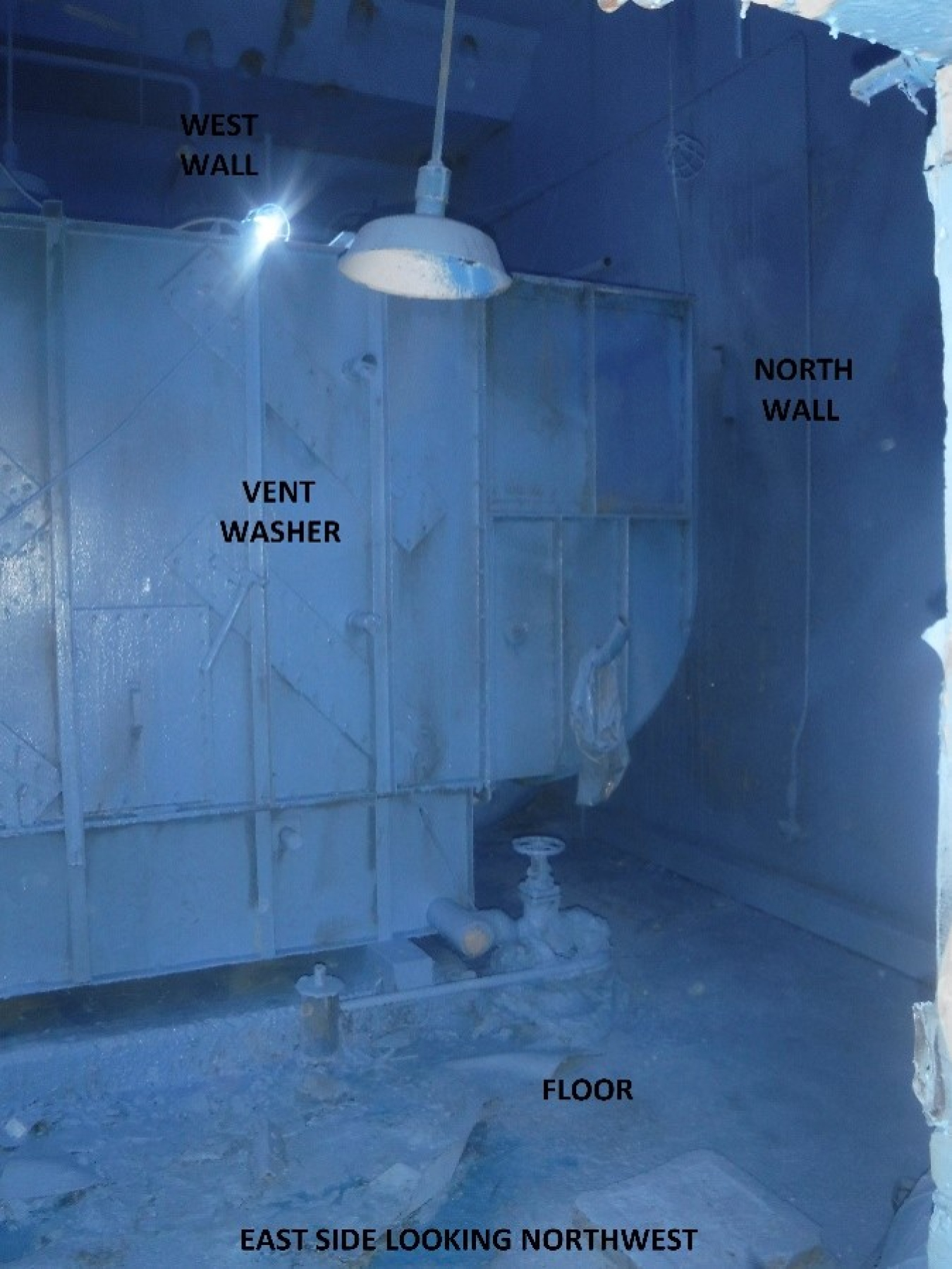
Workers have completed the deactivation of the Ventilation Wash Room within the Main Plant Process Building at the West Valley Demonstration Project. The cell housed a ventilation “scrubber” that removed airborne particulates resulting from fuel reprocessing operations that ceased in 1972. A crew applied fixative to the room for contamination control to prepare for the Main Plant demolition.
Successful deactivation of the Vent Wash Room comes on the heels of another safe deactivation of a cell within the Main Plant that reduced radiological hazards to support the facility’s demolition. Crews recently overcame unique challenges and finished deactivating the Product Purification Cell-South, a highly contaminated cell resembling an elevator shaft.
For the Vent Wash Room deactivation, project leaders incorporated feedback from workers, further enhancing safety. The workers recommended performing the cleanup remotely to keep potential exposure to radiation as low as reasonably achievable.
Operators created openings in the cell to allow for a diamond wire saw to be placed outside the cell. Workers made short trips into the cell to adjust the diamond wire as they cut through a ventilation duct for removal. As a result, the operators limited their potential exposure.
“Working in the Vent Wash Room was physically challenging when you include radiological and industrial hazards, layers of protective clothing, limited mobility and COVID protocols,” said Tom Dogal, CHBWV facility disposition manager. “This crew used lessons learned to enhance safety, improve efficiency and reduce exposure to job-related hazards. They put their collective knowledge into practice.”
During fuel reprocessing activities in the 1960s and 1970s, several areas within the Main Plant, including the product purification and chemical process cells, and a fuel-receiving and storage facility, sent exhaust to the Vent Wash Room through the ductwork. The exhaust was then directed to a ventilation exhaust cell where it was filtered before being discharged to the plant’s stack.
To receive the latest news and updates about the Office of Environmental Management, submit your e-mail address.