– EM Hanford and its tank operations contractor, have enhanced safety for workers by installing a new exhauster ventilation system above waste tanks.
Office of Environmental Management
September 8, 2020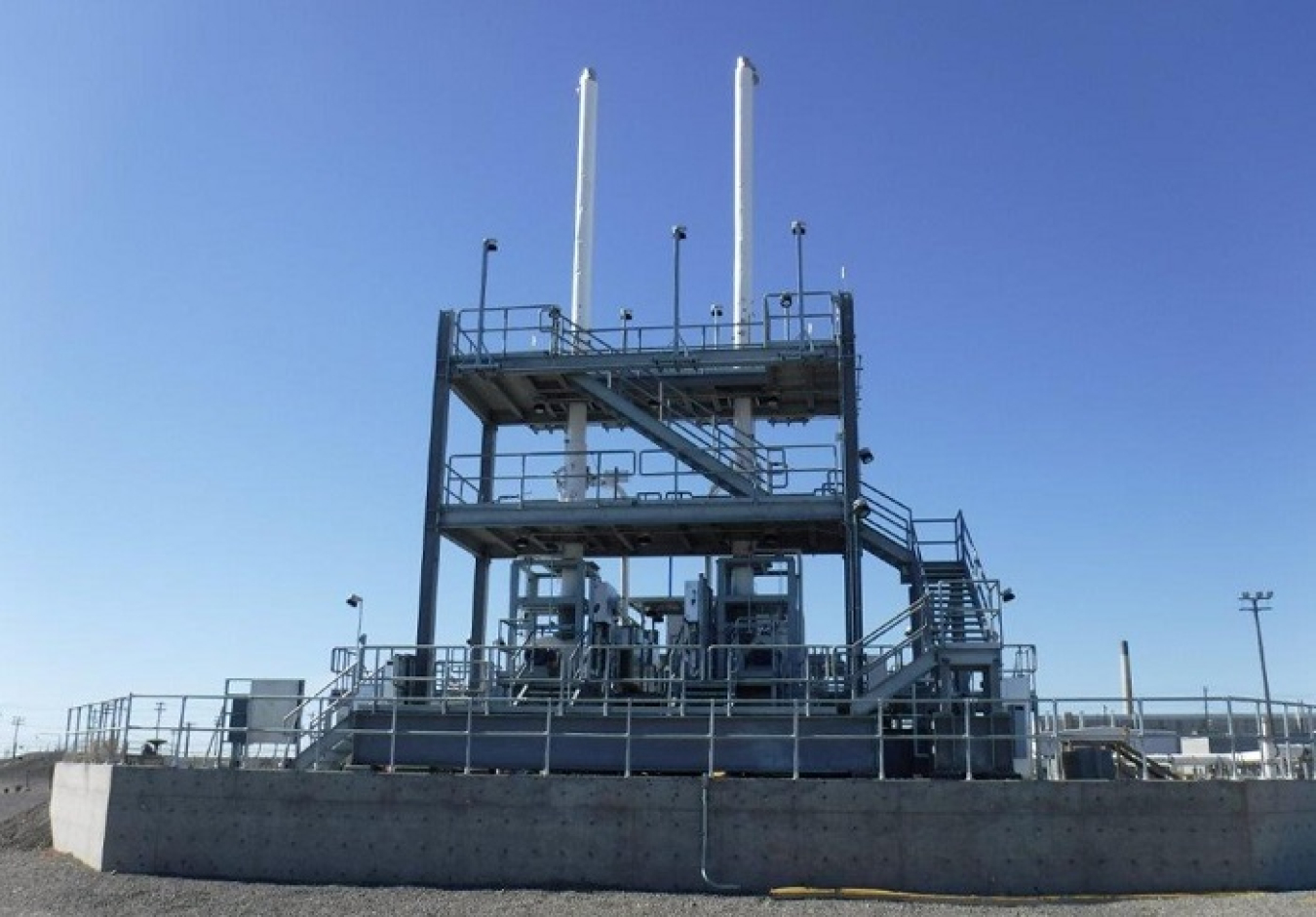
RICHLAND, Wash. – EM Hanford and its tank operations contractor, Washington River Protection Solutions (WRPS), have enhanced safety for workers by installing a new exhauster ventilation system above waste tanks.
The system, located in a group of tanks called the A Farm, continuously draws air from the tanks, separates moisture and radioactive particles, and sends filtered air through 50-foot exhauster stacks, well above workers.
After nearly four years of design, fabrication, installation, and testing, EM and WRPS are operating the new system that ventilates the farm’s six waste storage tanks. Each of the tanks, constructed between 1954 and 1955, has a capacity of 1 million gallons.
“This ventilation project is key to protecting workers against hazards associated with managing Hanford’s tank waste,” said Jim Lynch, with EM’s tank farms operations. “It reduces the risk posed by chemical vapors from the tanks during operations that disturb the waste, such as retrieving waste from the tanks.”
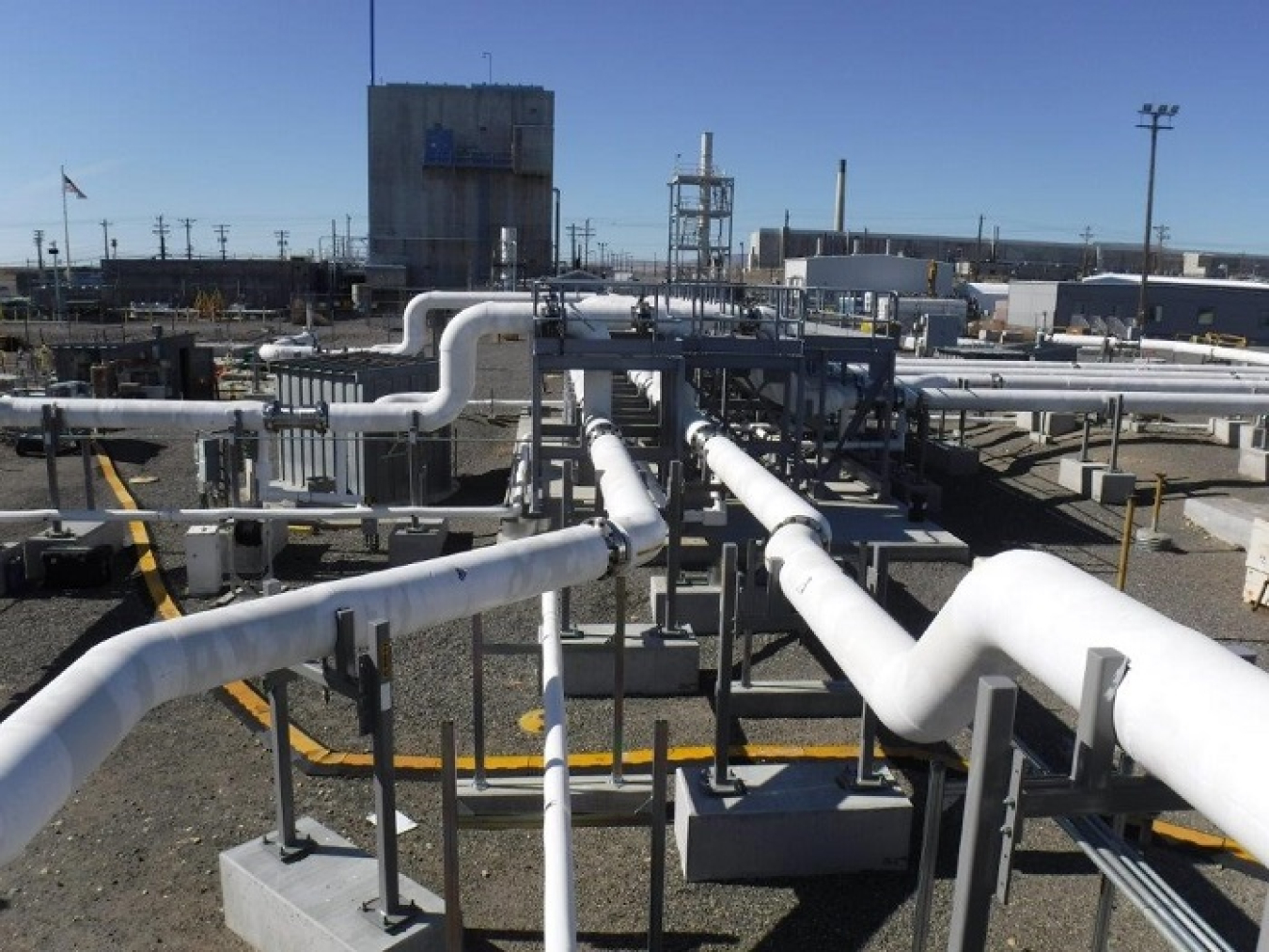
The new ventilation system has other benefits, too.
“Active ventilation also increases the margin of safety for workers when we are removing old, highly contaminated pieces of equipment from the tanks,” said Garth Stowe, WRPS project manager. “This clears the way for crews to install new equipment that will be used to retrieve waste. In addition, the ventilation system clears fog that forms in the tanks due to the heat generated by the waste, so operators get a better view when retrieving waste.”
Hanford’s tank ventilation systems also function to prevent the buildup of flammable gas in the tanks. The system features two exhausters with 50-foot-tall stacks; a 50-foot-by-20-foot valve manifold; and approximately 700 feet of ducting, piping, electrical lines, and insulation.
“The whole construction team did an amazing job,” Stowe said. “Assembling a system like this with air bottles on your back, inside a small tank farm with different elevations and other work going on around you, is a tremendous accomplishment. And, most important, the team completed all work safely.”