The use of concrete support structures for offshore wind turbines offers many potential advantages over towers comprised of only steel, including greater durability, a longer lifespan, increased local labor opportunities, and much quieter installations.
Wind Energy Technologies Office
October 17, 2022The use of concrete support structures for offshore wind turbines offers many potential advantages over towers comprised of only steel, including greater durability, a longer lifespan, increased local labor opportunities, and much quieter installations.
Additional test data and improved models and standards are required to determine ideal concrete structure designs that have a long fatigue life (and thereby lifespan). Fatigue is the weakening of a material—in this case, concrete—due to fluctuating loads that eventually result in damage to the material’s structure. The damage starts at one small location on the structure, propagates with repeated loading, and can end in failure. Fatigue capacity is the number of cycles of repeated loading the material can sustain for a particular range in stresses (e.g. 10,000 cycles before breaking when the stress range was between 500 and 4000 pounds per square inch). The higher the fatigue capacity, the better the material performs over time.
Current fatigue models are somewhat crude, driving researchers at Tufts University and the University of Illinois to investigate new factors affecting fatigue.
Findings from the research conducted to date include:
- The use of steel bars within concrete greatly increases the fatigue capacity (and thereby operational life) of the foundation and tower in comparison to just concrete structures. The steel is also protected against corrosion when encased in marine concrete.
- Higher stresses (such as hurricanes) early in the life of a structure will permanently damage the structure in ways that make subsequent lower-level stresses (i.e. operational loads) more impactful than they would have been otherwise.
- Concrete under water has a significantly shorter lifespan than when above water.
- An effective way to assess how many years of operational life are left in the foundation or tower is to directly measure the strain in the concrete at the locations of highest stress.
“The early results of this research are exhibiting great promise for concrete support structures and their potential advantages over current steel supports, specifically when it comes to offshore structures,” said Daniel Kuchma, professor of civil and environmental engineering at Tufts University. “The preliminary findings and ongoing research are providing evidence to advance the use of concrete foundations for supporting offshore wind turbines.”
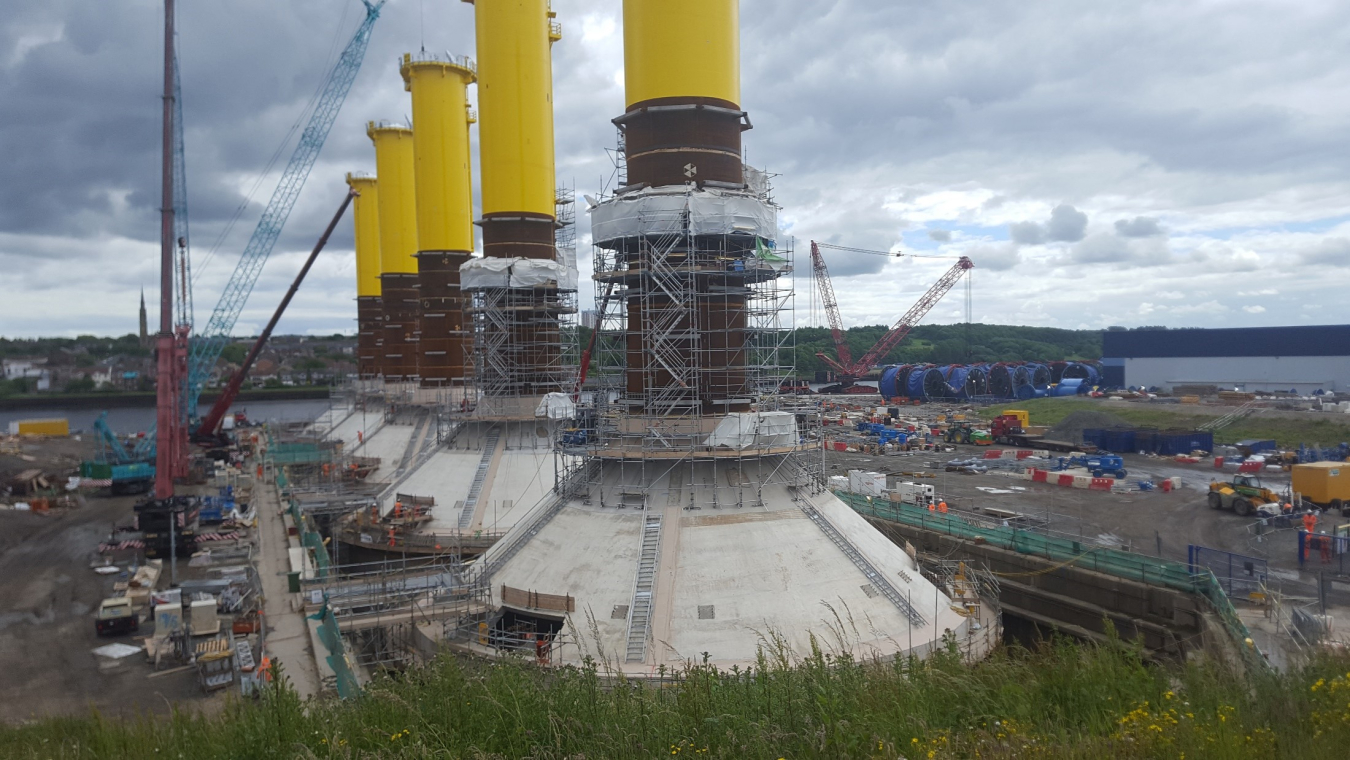
Concrete gravity base foundations for a demonstration project in Blyth, United Kingdom.
As part of this study, researchers compiled a database of results from over 2,500 concrete fatigue tests from dozens of studies. The research team identified some suspiciously low fatigue capacities and are repeating these tests to confirm or challenge these low fatigue capacities. If the fatigue capacities are higher in these repeated tests, then models can be made less conservative which would then predict a longer lifespan for concrete foundations and towers.
The project team is also examining how to assess the fatigue capacity for a particular structure under design using the results of fatigue tests on similarly designed concrete materials. This contrasts with the current practice in which the fatigue capacity of a structure under design is assessed using design standards that were derived from fatigue tests on a very wide range of concrete materials.
While outside the scope of the present study, the next and much more challenging task in concrete fatigue is understanding and improving the fatigue design of joints (aka points of contact) between individual concrete components.
A commonly expressed concern about concrete foundations (which contain cement) for wind turbines is that cement contributes about 8% of the global equivalent (CO2e) emissions. However, the emissions resulting from cement production are minimal when compared to other types of electricity production. The average CO2e impact of cement in foundations for land-based and offshore wind turbine foundations is about 1 gram (g) per kilowatt-hour (kWh) of electricity generation. This accounts for about 10% of emissions for land-based and offshore wind energy—approximately 11 g/kWh and 12 g/kWh, respectively. Conversely, the emissions from producing electricity from natural gas average 490 g/kWh and the average from coal is 820 g/kWh. These comparisons illustrate that the CO2e impact of cement in wind turbine foundations is minimal relative to the potential lifespan and renewable energy potential of the structure. In order to address these concerns, the research team is also investigating the fatigue performance of concretes produced using alternative cement substitutes.
An additional challenge for concrete foundations is the longer production time relative to steel structures. This problem could be addressed by prefabricating concrete foundations. It may also be practical to build foundations and towers as enduring infrastructure, like hydroelectric dams, where only the wind turbines are replaced at the end of their useful life, while the foundations and towers remain intact.
Subscribe to the WETO e-newsletter to stay informed on the latest wind energy news, events, publications, and updates.