Company Commercializes the Only Currently-Available Technology that can Recycle Fiberglass From Decommissioned Wind Turbine Blades
Wind Energy Technologies Office
October 17, 2022Company Commercializes Technology That Can Recycle Fiberglass From Decommissioned Wind Turbine Blades
A new fiberglass recycling technology is helping to develop a reuse and recycling wind turbine economy while creating jobs and revitalizing a historic site.
Carbon Rivers, a company that produces advanced material and energy technologies, has commercialized a process to recover renewable, mechanically intact glass fiber from decommissioned wind turbine blades. Glass fibers are a key part of the composite—a material made up of multiple constituents such as polymers and fibers—used to create wind turbine blades. Typically, turbine blades are 50% glass or carbon fiber composite by weight. However, Carbon Rivers upcycles all components of the blade, including the steel.
Funded by the U.S. Department of Energy’s (DOE) Wind Energy Technologies Office, the Carbon Rivers project team, led by Ryan Ginder, Bowie Benson, and Eva Li in collaboration with the University of Tennessee, Knoxville, successfully scaled up a recovery process that has the capability to divert thousands of tons of waste that would otherwise be destined for landfills. To date, Carbon Rivers has upcycled a few thousand metric tons and is building capacity in their new facility to take in over 50,000 metric tons annually.
“This is an extraordinary leap for upcycling materials from wind turbines and closing the loop on a reuse and recycling energy economy,” Li said. “This research will have an enormous global impact on wind energy.”
Reuse and recycling for the wind energy industry means that materials that previously ended up in post-consumer waste streams can go directly into next-generation turbine blade manufacturing.
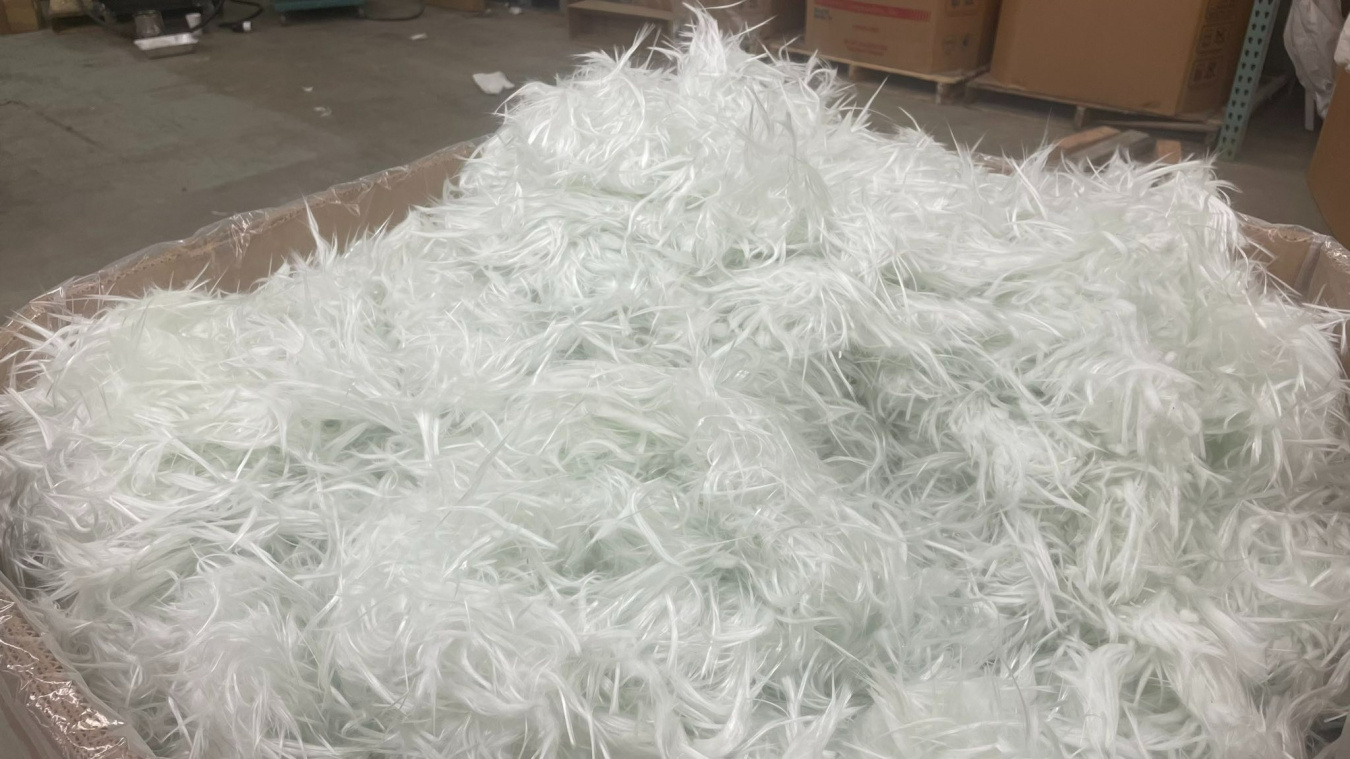
Carbon Rivers has achieved 99.9% recycled glass fiber purity from different end-of-life waste streams like wind turbine blades. The complete elimination of contaminants, along with high recoverable fiber aspect ratio and performance allows recycled glass fiber to displace virgin fiberglass in different composite applications. The high purity also opens the potential for remelting—allowing recycled glass fiber to be incorporated into virgin fiberglass, thereby closing the material loop and creating reuse and recycling.
Turning Up the Heat: How the Recycling Works
Carbon Rivers’ recycling uses pyrolysis—a process during which organic components of a composite (e.g., resins or polymers) are broken down with intense heat in the absence of oxygen and separated from the inorganic fiberglass reinforcement. The process converts organic products back into raw hydrocarbon products called syngas and pyrolysis oil, which can be used for energy production.
The separated recycled glass fiber can then be collected for direct reuse in the manufacturing of new products.
“By converting the original composite scrap back into reusable raw materials, mechanically intact glass fiber and pyrolysis oil, we’ve developed a recycling process,” Ginder said. “This will help create jobs in recycling.”
While this process was originally created for material from decommissioned wind blades, it has since been adapted for automotive, marine, structural, and glass waste materials and other future uses. This includes making recycled glass fiber into nonwoven fabrics, continuous textile yarns, automotive sheet molding compounds, and plastic injection molding pellets. Recycled glass fiber can also be remelted and mixed with virgin fiberglass for additional uses.
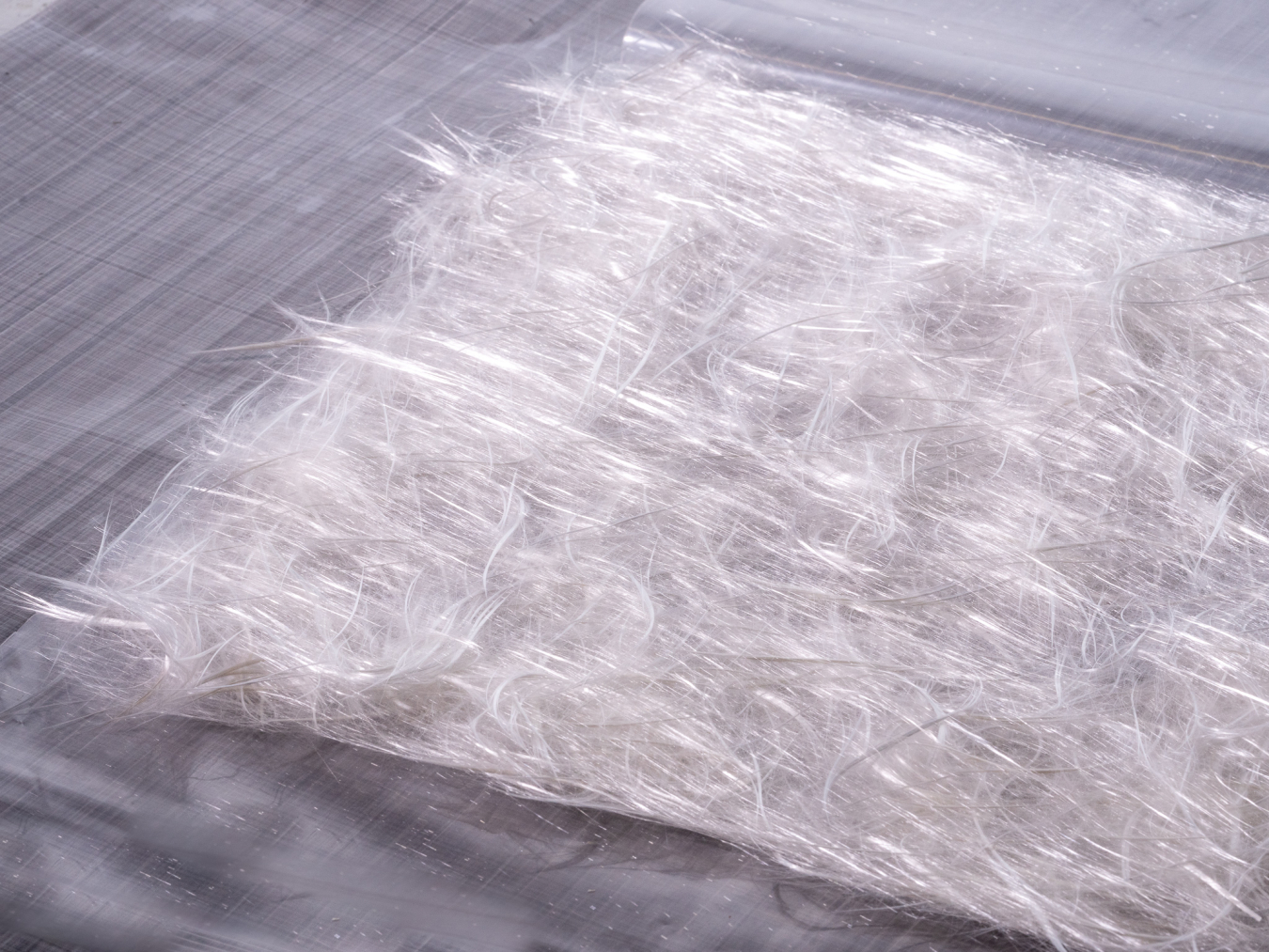
Recycled glass fiber mats and veils can be used in marine and wind energy technology manufacturing as well as in construction materials like roofing, insulation, and flooring.
Coming Soon: The United States’ First Wind Turbine Blade Recycling Center in a Historic Location
Carbon Rivers is now in the process of separating part of its business into a stand-alone entity called Windfall Inc. which will develop the first full-scale U.S.-based glass fiber recycling facility. This is, however, not the only historic thing about the future Windfall plant: their site located outside Knoxville, Tennessee originally supported nuclear weapons production as part of the Manhattan Project.
The original technology demonstration of this circulate process was made possible through the U.S. Department of Energy’s Small Business Technology Transfer program, which provides grants to small businesses.
“The emergence of a fiberglass industry will provide a supply chain for the renewable energy sector and produce hundreds of new jobs focused on domestic materials production to support our energy infrastructure and decrease the United States’ dependence on foreign imports for fiberglass products,” Benson said.
The planned facility is expected to process approximately 200 metric tons, or 5,000–7,000 fiberglass wind turbine blades each year, depending on blade size and generation. The recovered fiberglass can then be directed into new composites production.
“With Carbon Rivers’ novel process, today’s decommissioned blades can become tomorrow’s wind turbine blades and electric vehicles,” Benson said.
Subscribe to the WETO e-newsletter to stay informed on the latest wind energy news, events, publications, and updates.