Using, reusing, recycling, and remanufacturing wind turbine materials—combined with technology engineered to use fewer materials and resources—will produce components that can easily be broken down for use in other applications.
Wind Energy Technologies Office
June 2, 2021Emerging technologies promise to increase opportunities for reuse and recycling
Wind energy is one of the fastest-growing sources of electricity generation—growth that is vital for reducing carbon emissions from electric power. However, building wind turbines requires large quantities of materials and components. These components will eventually reach the end of their design lifetimes and could go to landfills—unless innovation provides an answer.
Using, reusing, recycling, and remanufacturing wind turbine materials will reduce waste using technology engineered from the start to require fewer materials, resources, and energy while lasting longer and having components that can easily be broken down for use in subsequent applications.
“The earliest point in a product lifecycle that reuse and recycling strategies can be applied is in the design of products from the ground up—literally,” said Tyler Christoffel, Oak Ridge Institute for Science and Technology Fellow at the Department of Energy (DOE). “Wind turbines must be designed from the concrete base, through the tower and nacelle, all the way to the blade tips.”
According to a recent NREL publication, as renewable energy generation and storage become central components to reuse and recycling new materials and manufacturing strategies will be necessary to ensure that such technologies are not contributing to end-of-life challenges. Shifts in recycling technologies, new materials, extended useful life, and innovative reuse are needed to move toward reuse and recycling for wind turbine blades.
The Wind Energy Technologies Office (WETO) is working with researchers across industry, academia, and DOE national laboratories to focus on wind blade recycling and enable reuse and recycling for the entire wind turbine.
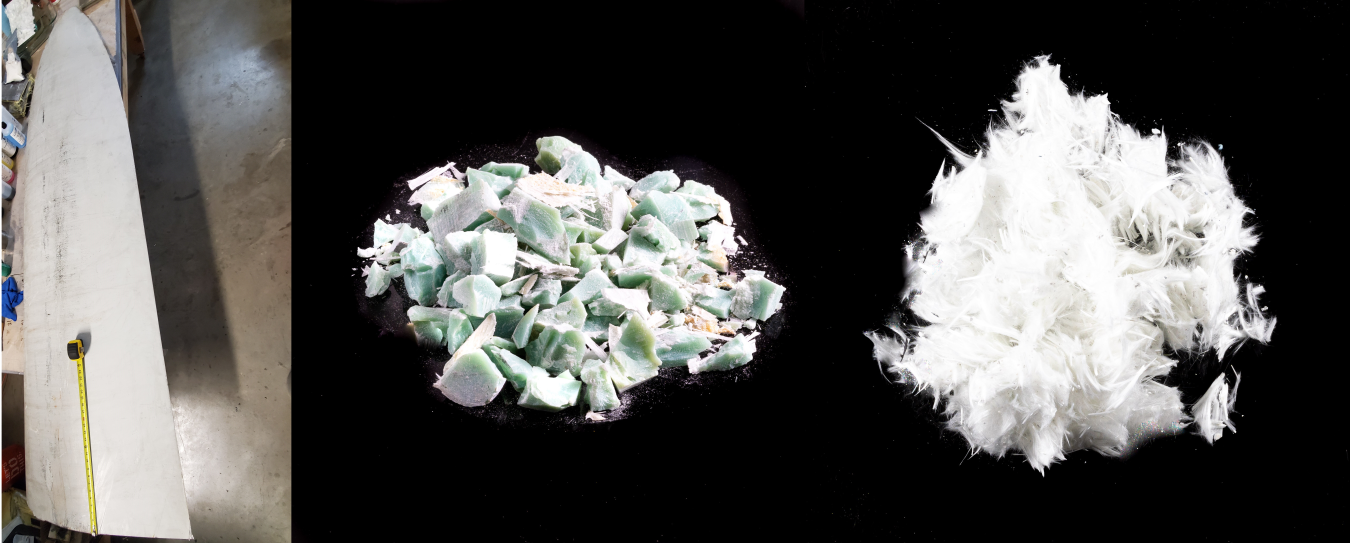
The Carbon Rivers and University of Tennessee, Knoxville, blade recycling process takes decommissioned wind turbine blades (left), mechanically reduces them into small pieces (middle), and then uses a novel pyrolysis technique to recover high-quality glass fiber (right). Images courtesy of Carbon Rivers
Recycling and upcycling. Wind turbine blade materials, such as fiberglass or carbon fiber, are difficult to separate from other components and their value is often degraded even when successfully extracted.
- With WETO funding, researchers from the University of Tennessee and Carbon Rivers are developing a novel pyrolysis, or thermal decomposition, method of reclaiming fiberglass from retired wind turbine blades. The recovered fiberglass will be used to manufacture second-generation composites for the automotive, consumer products, marine, and aerospace industries.
Extending life cycles. Wind turbine components like blades can fail and require replacement earlier than expected, indicating a need for manufacturing methods and materials that optimize longer life cycles.
- National Renewable Energy Laboratory (NREL) researchers recently assessed the current end-of-life treatment for wind turbine blades and identified methods for achieving reuse and recycling for wind energy, including design for circularity, lifetime extension, mechanical recycling/upcycling, and uses in cement production.
- Advanced drone and robotic maintenance and repair strategies for older blades, as well as diagnostic and inspection techniques that support certifying wind turbines to operate for an extended lifetime. With WETO funding, Sandia National Laboratories is developing advanced blade inspection techniques and improving repair capabilities as part of its Blade Reliability Initiative.
Incorporating new and fewer materials. Innovative materials, such as carbon fiber, are making wind turbine blades lighter, more durable, and easier to recycle. As part of this effort, DOE is supporting the following:
- Arctura’s development of a blade coating that can mitigate lightning strike damage.
- Resodyn Corp.’s development of a blade coating that resists erosion.
- Joint research by Oak Ridge National Laboratory and NREL into advanced manufacturing processes to make blades and generators with fewer materials.
“WETO efforts will continue to reduce material and energy usage and cost, supporting expansion of cost-effective, wind energy deployment,” Christoffel said.
Subscribe to learn more about WETO R&D projects, news, accomplishments, and recent publications.
Subscribe to the WETO e-newsletter to stay informed on the latest wind energy news, events, publications, and updates.