WPTO is engaging stakeholders engaged in the PacWave project. In this article, WPTO interviews Tom Hickman of Vigor.
Water Power Technologies Office
September 24, 2018In December of 2016, the Energy Department announced up to $35 million in funding for the construction of PacWave, formally known as the Pacific Marine Energy Center, South Energy Test Site. In anticipation of this state-of-the-art wave energy test facility becoming operational around 2021, the Water Power Technologies Office (WPTO) is engaging stakeholders involved in the PacWave project and the broader marine energy community. These discussions offer different perspectives on the significance of the facility's development to the U.S. marine energy industry as well as Oregon's coastal economy. Miles Hall, WPTO's Stakeholder Engagement Specialist, had a recent chat with Tom Hickman of Vigor, a shipbuilding and maintenance company based in Portland, Oregon. As Vice President of Marketing and Sales, Tom shares his thoughts on Vigor's current operations, the company's manufacturing efforts within the marine industry, and local impressions of PacWave.
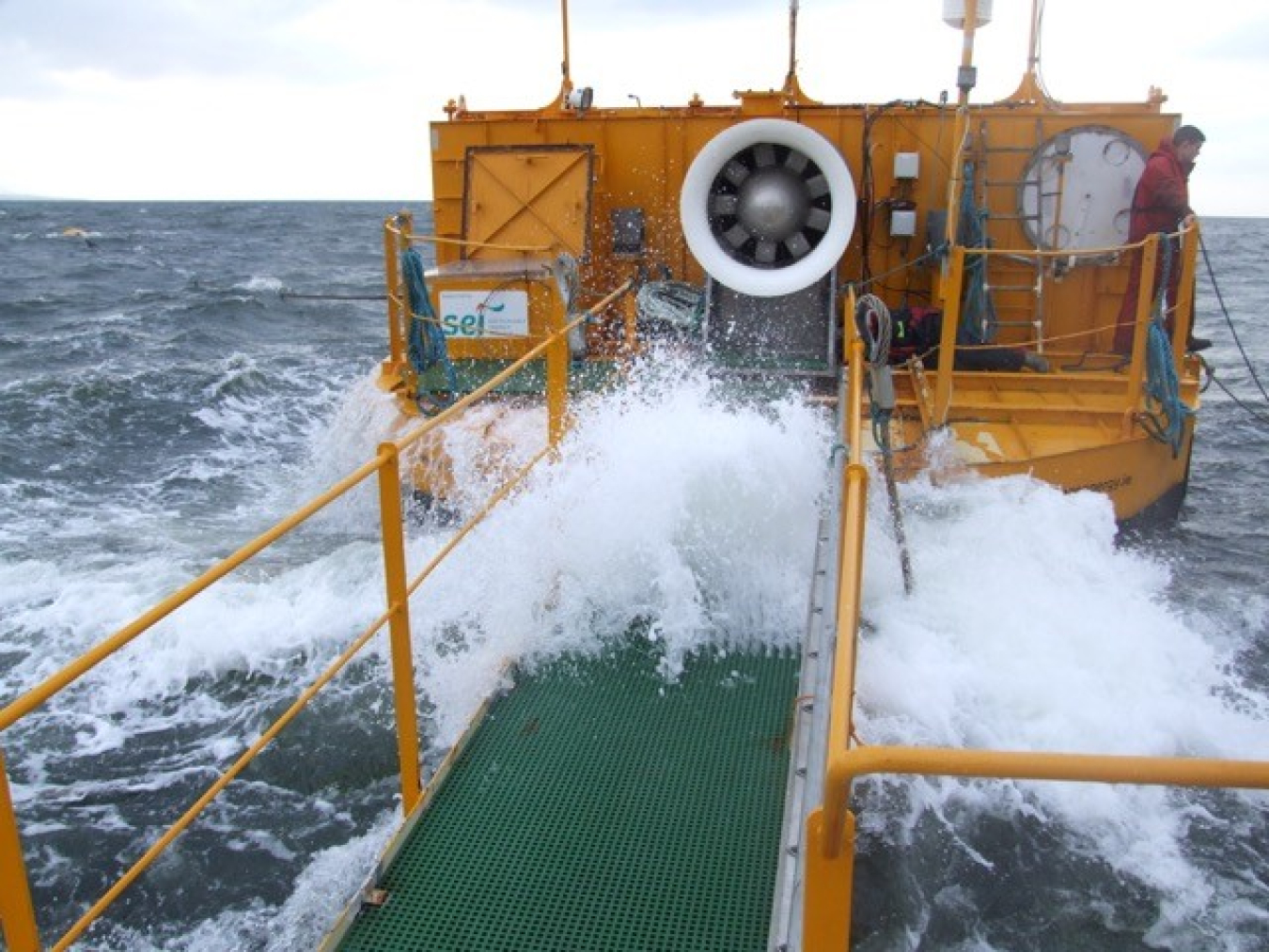
The OE Buoy
What types of shipbuilding services does Vigor provide?
Vigor works primarily in maritime shipbuilding, ship repair, and fabrication and operates facilities in Oregon, Washington, and Alaska. In the maritime industry, we concentrate heavily on the manufacturing and repair of tugboats and barges, and also manufacture high speed boats for the Navy. The company has expertise in the hydropower industry as well—we build dam lift gates used in rivers such as the Mississippi, Ohio, Kentucky, and Columbia, as well as water flow and fish screening materials. We replace, maintain, and transport aging inner-waterway infrastructure, which can be a major asset to barges needing smoother river-based transit. Vigor also does a lot of business in the nuclear and aerospace industries, which can vary from manufacturing platforms used with launch pads to building nuclear containment devices.
How many people work at Vigor?
We employ roughly 2,300 staff total, mostly based on the West Coast. As one of nine company locations, our facility in Portland, Oregon can have anywhere between 400-900 workers onsite on a given day. This can vary based on whether we have a large ship onsite needing repairs, customizations, or other types of fabrications and modifications.
Can you describe some of the key components of Vigor's workforce? What kinds of education and training are needed?
On the shop floor where production is carried out, the workforce is primarily composed of welders, ship fitters, machinists, and mechanics, most of whom receive extensive on the job training. We have a number of machinists and certified quality control inspectors who have graduated from the four year apprenticeship programs at Portland Community College (PCC). The local Ironworkers Union has a diversified apprenticeship program as well, which offers education for ironworkers, carpenters, boilermakers, electricians, welders, and more.
Apart from the shop floor, there's a large focus on the project management development where we mostly employ engineers or designers. We have a lot of Oregon State University graduates, many of whom participated in the Multiple Engineering Cooperative Program, which provides internships for students in a number of engineering disciplines. We pull in mechanical and civil engineering students for up to six months who are paired with senior engineers that guide their work and offer career advice and insights into what an engineering project manager does on a daily basis.
Which kinds of expertise are needed for the Ocean Energy buoy that Vigor is currently constructing?
The Ocean Energy wave buoy design requires expertise from a number of different engineering and manufacturing disciplines. We brought together competencies in machining and highly complex fabrication with our work in the marine industry, the aerospace industry, and the electrical industry in order to build complex structures like the 35-meter hull of Ocean Energy's wave energy converter buoy. Because of the diversity in our workforce, we do not have to outsource any of the electrical, mechanical, or machining work for that project.
How does the process unfold after you have received a request to build from a client?
Customers will usually approach us with what they believe to be a complete design for the type of infrastructure they need built. Design drawings must then be rendered into shop drawings that include dimension specifications, design layouts, assembly procedures, and other details that someone on the shop floor needs to construct the piece. Transitioning from the initial design to shop floor drawings that can lead to the final state of the piece is a challenge. A design may appear to be complete on paper or in the software being used to produce it, but when we are moving into physical construction, significant modifications may still be needed to complete the final fabrication and welding processes. Detailers who specialize in transitioning from design to the shop look for solutions to any irregularities that might occur.
What kind of marine manufacturing standards does Vigor need to comply with?
There are numerous standards that we need to comply with, many of which are driven by the variety of customers we have. For products used in the United States, we will typically manufacture in accordance with domestic standards developed and published by major accreditation groups such as the American Bureau of Shipping, the American Welding Society (AWS), DNV-GL, and Lloyd's Register. Depending on what we are contracted to build, where it is being shipped, and the types of applications it is expected to have, we will build based off of certifications from certain groups rather than others—for example, we will need to build the hull of Ocean Energy's buoy based off of structural code delineated from AWS. Other times we may need to not only follow international standards, as well as domestic guidelines. If we build a vessel that will be sailing into a foreign country's harbor, we may need to abide by the standards of that country—in this case, we will pull in third-party certification inspectors to oversee the work.
What kind of lessons can marine energy developers take away from commercial vessel construction and deployment?
I would strongly encourage developers to try to keep it simple—stick as close as possible to traditional construction methodology. Deploying in the open ocean exposes technology to many variables, so sometimes it might make sense to design something that is slightly less efficient but more robust to unforeseen circumstances. We have had prior experiences where designs have been excessively complicated, which has led to increased costs. It is also important to focus on where the device is going to be deployed and how specific locations might affect design. One of the best things about Ocean Energy's wave energy converter is that it features a bi-directional turbine that can generate electricity whether the waves are going in or out.
What changes have you seen in the marine industry during the past 10 years?
The last decade has been challenging for the Pacific Northwest marine industry, which was greatly affected by the 2008 financial crisis. We noticed a decline in customer financing necessary for new manufacturing, so a lot of companies were using older equipment and leasing vessels instead of constructing new ones. However, 2017 has brought some encouraging signs of growth in new business and manufacturing contracts, such as the Ocean Energy Buoy. I'm personally optimistic about marine energy and the ties that it has with the state. I think that once there is a system in place that can consistently harness the power from our oceans, it will make for a fantastic addition to Oregon's energy mix, especially if we can get the price down to somewhere in the 15-25 cents/kilowatt-hour range.
What is your understanding of the community support for renewable energy as well as for PacWave?
Through our connections with the Oregon Wave Energy Trust, we have been exposed to a lot of community support from different vantage points. We have seen positive reactions from academics, fishermen, and various members within different institutions for the site, as well as for marine energy more broadly. There was a similar reaction several years back when Ocean Power Technologies tested in Oregon, which is also reflective of the state's pro-renewables stance. Outside of Oregon, I have also heard enthusiastic responses from colleagues across the country in Florida and Maine in particular. Job opportunities will become an increasingly important factor for the site, especially when the technology becomes scalable. Transporting equipment, facility maintenance, connections to the grid, and monitoring deployed devices are just a few aspects of the test site that will drive job growth. I remember when the wind industry started growing at an accelerated rate—a whole new demand for jobs based on maintenance alone was created to support wind, so I think the same thing could certainly happen with marine energy as well.
PacWave is being designed and constructed by Oregon State University and is being co-funded by the U.S. Department of Energy. When completed, PacWave will be a utility-scale, grid-connected, open-ocean test facility located off the coast of Newport, Oregon. The site will be able to accommodate up to 20 wave energy converters (WECs) across four test berths at any one time. Each of the four test berths will have a dedicated transmission cable and the site will be mostly pre-permitted for known WEC technologies. PacWAVE will enable technology developers to prove device performance in robust wave environments for extended periods of time, thereby demonstrating technical viability, determining methods for cost reduction, and advancing technologies toward commercial readiness and cost-effective power delivery.