Even well-established industries have room for innovation.
October 4, 2017Even well-established industries have room for innovation. Take aluminum alloys for example. Traditional aluminum alloys have more than 150 years of research history, yet even in 2017 scientists are discovering new mechanisms in the most researched aluminum-alloy systems such as aluminum-copper (Al-Cu). In fact, two light-weight aluminum alloys developed through Energy Department partnerships are finalists for the R&D 100 Awards, which honor revolutionary ideas in science and technology.
One of these finalists is an aluminum cerium alloy (Al-Ce) that has been developed through a partnership with the Energy Department’s Critical Materials Institute (CMI) members including Oak Ridge National Laboratory (ORNL), Lawrence Livermore National Laboratory (LLNL), Ames National Laboratory, and private sector partners. Recently, Eck Industries, an aluminum foundry in Wisconsin and private-sector partner of CMI, signed an exclusive license to commercialize the Al-Ce alloy, and together the public- and private-sector partners will continue to collaborate to effectively scale up manufacturing of the alloy. This partnership brings together the R&D expertise of CMI and the labs with Eck’s intimate knowledge of market needs and full-scale manufacturing challenges.
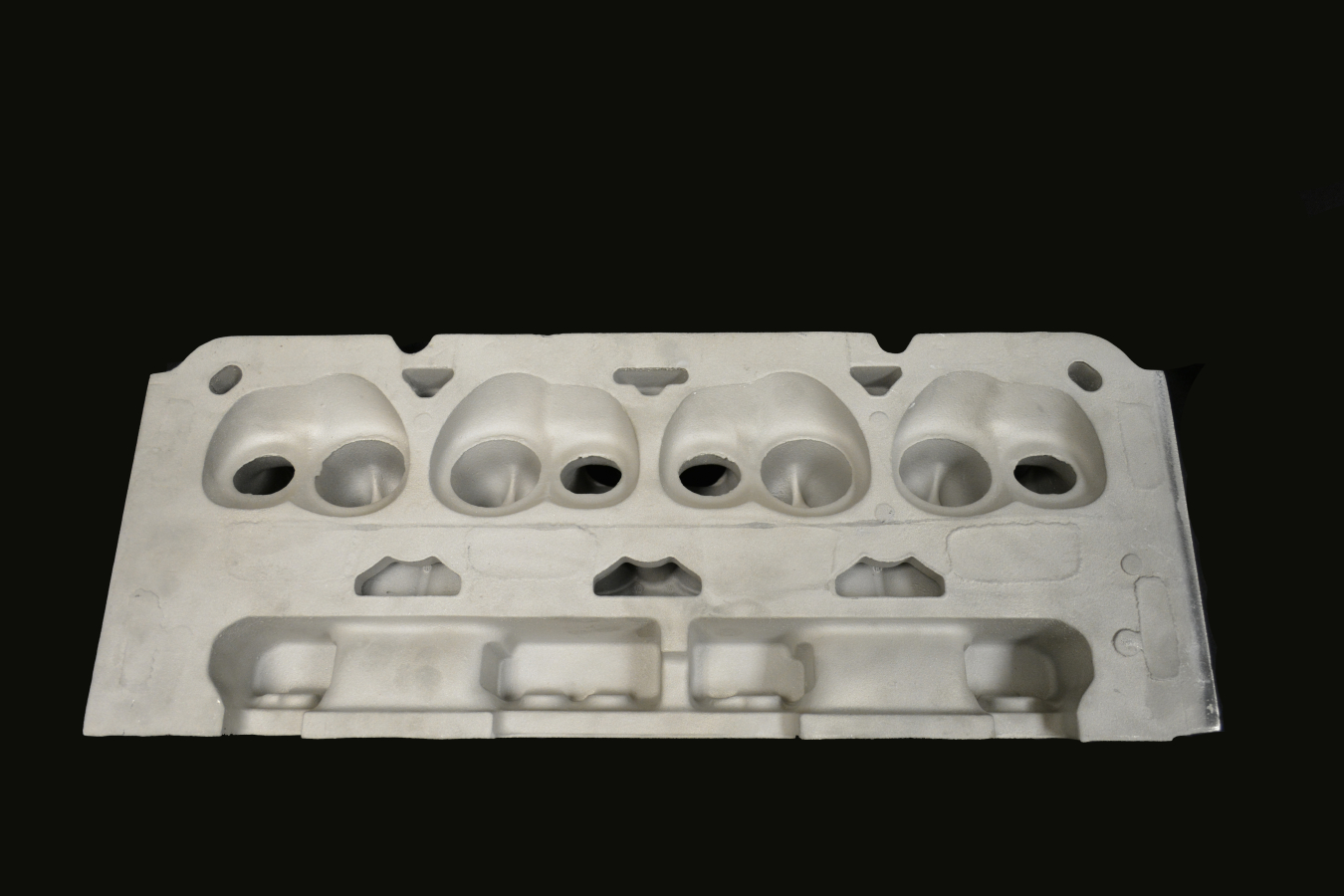
Aluminum cerium alloy (Al-Ce) | Photo Courtesy: Oak Ridge National Laboratory
“It’s been incredible trying to do materials development,” said David Weiss, Vice President of Engineering/R&D at Eck Industries. “When trying something new in the materials space, there needs to be a lot of theoretical understanding, experimental development, and testing work that must get done. Some comes from ORNL, some from us, it’s been a pretty equal partnership on what needs to be done. For example, we’re able to give guidance on what’s needed commercially. It’s been an extraordinary collaboration and that’s why we’ve been able to make so much progress over the last three years.”
Eck is already setting up commercial sales and manufacturing operations. Components cast from heat treat-free compositions are in service and pilot scale production has been ramped up to small-scale manufacturing.
All of this has allowed the team to accelerate development across all institutions and focus areas.
Why Cerium?
Cerium is soft, malleable material, and reportedly the most abundant rare-earth element. According to Orlando Rios, a researcher at ORNL, it is overproduced, inexpensive, and finding new uses for it supports domestic rare-earth mining operations and provides innovative resource materials to U.S. manufacturers.
For these reasons, CMI was looking for useful applications for cerium. What they found was a desire for aluminum alloys that perform at better temperatures for a long time. Copper is commonly used because it gives high temperature strength, but the problem is when elements like copper, zirconium, cobalt, and other heavier alloys are loaded on, there are negative side effects like decreased casting ability and reduced corrosion performance.
The team found the aluminum cerium alloy easy to work with, lightweight, corrosion resistant, and stable at very high temperatures, up to 500 °C. For many uses, a heat treat is not required, which enables many new applications. The Al-Ce alloy has been used for applications including cylinder heads, turbo chargers, and turbine blades for hydroelectric turbines, pistons, and rotors.
What’s Next?
While Eck Industries focuses on commercial scale-up of Al-Ce production and applications, CMI is continuing to look for new scientific challenges that can be solved with early-stage R&D. Public-private partnerships with manufacturers help identify opportunities to close knowledge gaps and enable manufacturers to innovate and make quality products here in the U.S. while effectively utilizing critical materials resources.
CMI and research partners focus on understanding the basic mechanisms to further develop new alloys and enhance properties of existing alloys, and the industry partnerships they forge are crucial to ensuring that new knowledge is translated into efficient commercial processes and products.