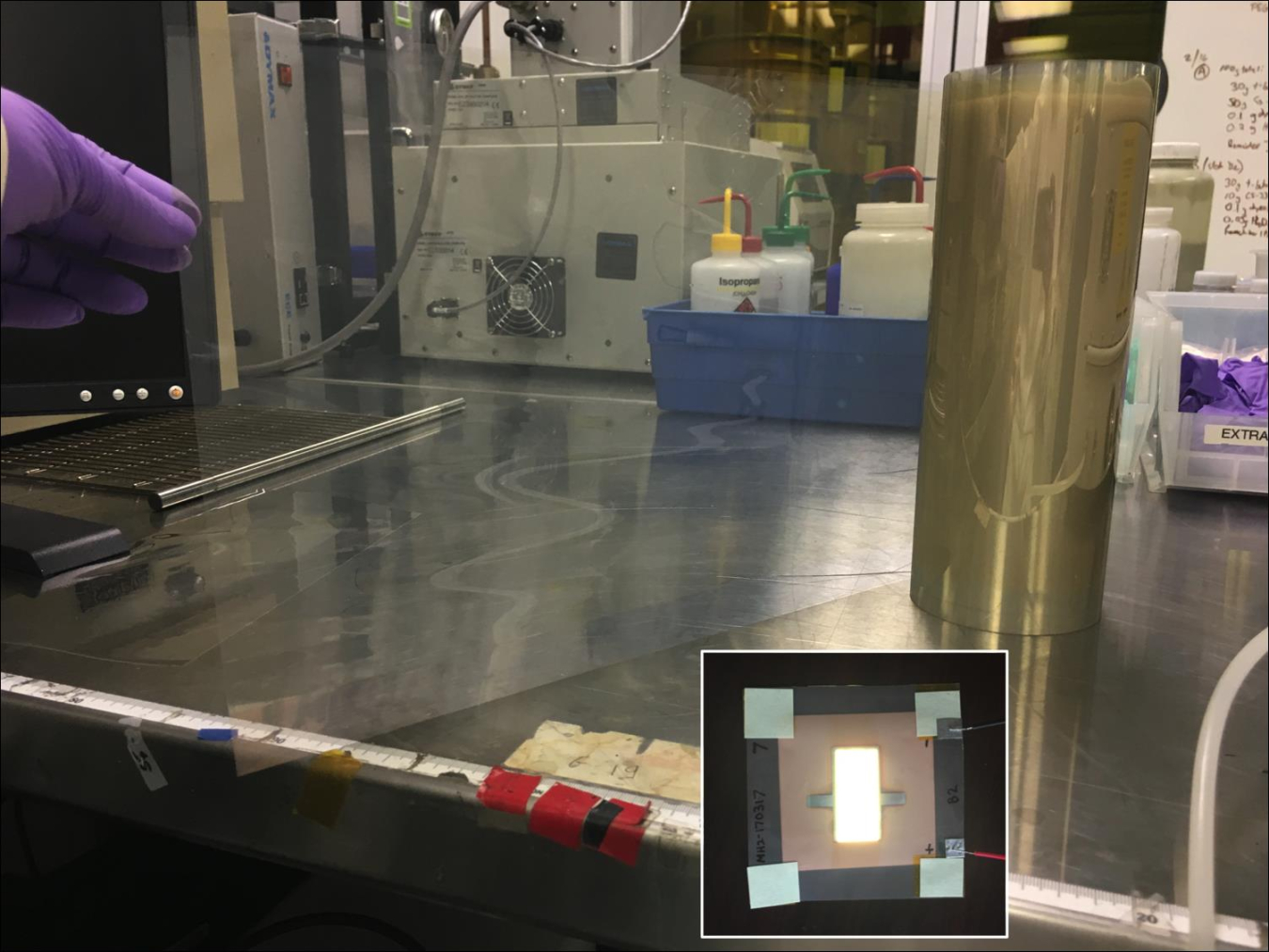
Integrated substrates perform multiple functions in OLED lighting. They act as a support for fabrication, protecting the OLED from oxygen and moisture, serving as a transparent conductive anode for the stack, and aiding light outcoupling from the device to enhance efficiency. With the help of DOE funding, Sinovia Technologies, in collaboration with Vitriflex, Inc., is developing integrated plastic substrates that combine Vitriflex’s multilayer barrier-film technology and Sinovia’s composite transparent conductive film to allow OLED fabricators to easily transition from glass indium tin oxide (ITO)-based designs to flexible OLED panels, enabling new luminaire designs.
The integrated substrate has low water-vapor transport of 10-6 g/m2/day, meeting the DOE specification. The conductive top layer has sheet resistance tunable between 1 and 10 ohms/square, with total film transparency over 75% at the highest conductivities, suitable for large-area devices. The transparent conductive film itself is comprised of a silver nanowire mesh embedded into the surface of a barrier-enhancing polymer. The top surface has an average roughness under 3 nm, which is critical to prevent shorting through the nanometer-scale-thick OLED layers.
In addition, the nanowires are placed exactly at the interface between the high-index organic layers and the lower-index substrate layers, acting as light-scattering centers for internal light extraction. This introduces a 20% – 45% haze that aids light out-coupling and increases white OLED efficiency. Preliminary results show 30% – 50% increases in all white OLED efficiency metrics, with L70 lifetimes of 80% compared to control devices built on ITO and glass.
Throughout the project, the team has also tested and established techniques for high-throughput, reliable, large-scale manufacturing techniques for these substrates, resulting in the ability to coat thousands of feet without visible defects. Cost analyses of these techniques show that at scale, these substrates meet current DOE cost targets and will meet future targets for lowering the cost of OLED lighting. (September 2017)
Return to Research Highlights.