U.S. Department of Energy (DOE) awardee EcoCatalytic has successfully demonstrated the viability of a pilot-scale plant for a new, energy-efficient method to produce ethylene.
Industrial Technologies Office
July 31, 2020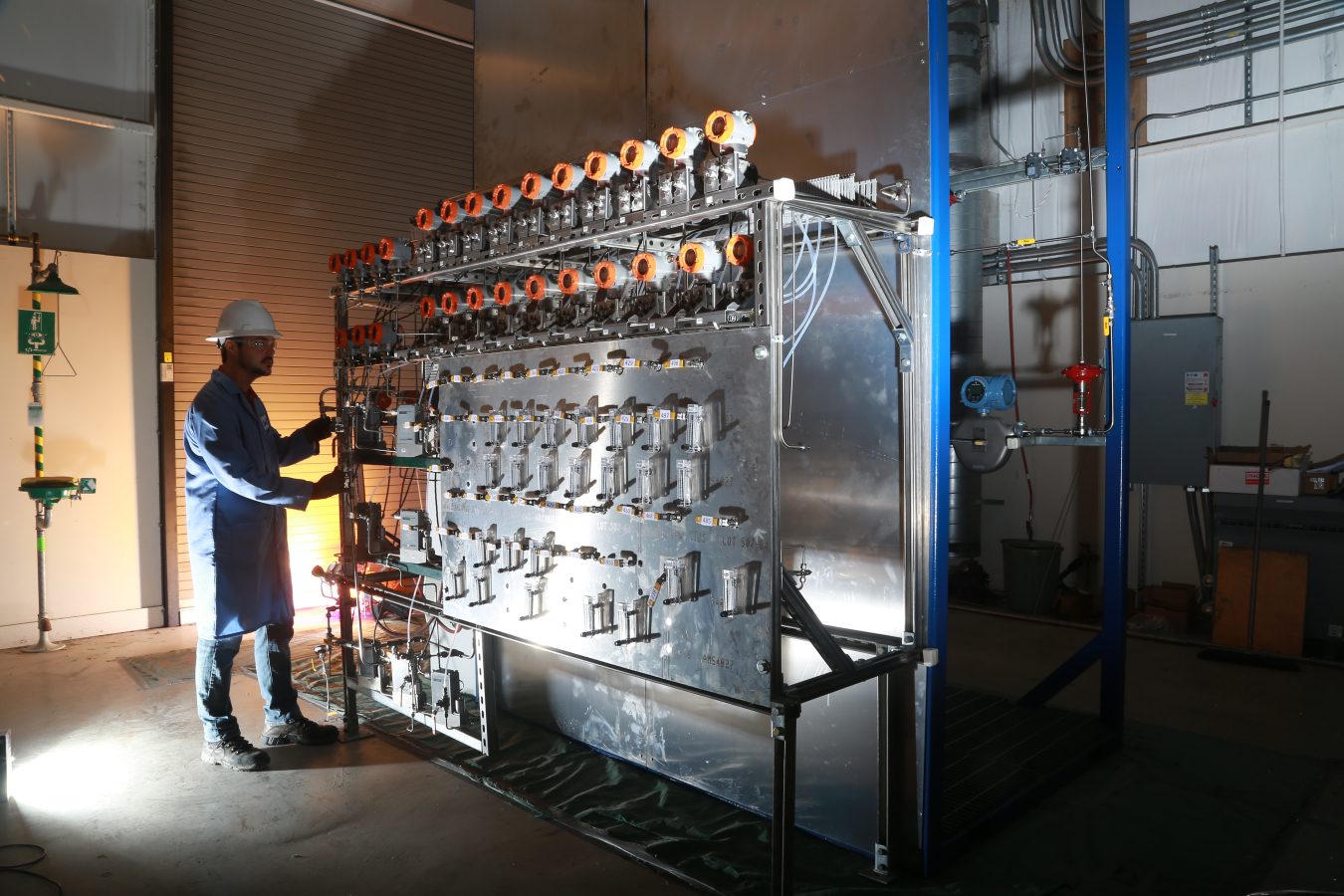
U.S. Department of Energy (DOE) awardee EcoCatalytic has successfully demonstrated the viability of a pilot-scale plant for a new, energy-efficient method to produce ethylene. This process is approximately 50% more energy efficient than conventional methods and can improve the competitiveness of chemical manufacturers.
Ethylene is foundational to modern life and a fundamental building block for plastics, paints, adhesives, and solvents. As a result, ethylene is one of the most commonly manufactured chemicals worldwide. In 2018, the United States produced nearly 30 million metric tons of ethylene.1
Ethylene is conventionally produced through steam cracking, a process that uses a series of boilers requiring very high heat. As a result, ethylene is one of the most energy-intensive chemicals to manufacture.
Results from EcoCatalytic’s pilot-scale testing indicate that a single Integrated Fluidized Bed Hydrogen Combustion (IFBHC) unit may be able to replace several traditional boilers at the commercial scale. The improved process requires approximately 50% less energy and lowers emissions. It also has the potential to reduce overhead for chemical manufacturers by lowering energy and capital costs.
“EcoCatalytic is enthusiastic about the outcome of pilot scale testing for IFBHC,” said John Sofranko, CEO of EcoCatalytic, Inc. “These results show the potential for the U.S. chemical manufacturing industry to improve the energy use and environmental impacts associated with ethylene production.”
Additional details about ethylene production and the IFBHC process can be found in a fact sheet.
DOE’s Advanced Manufacturing Office (AMO) awarded EcoCatalytic $2 million in 2018, with $2 million in company matching contributions, to verify laboratory-scale results in a 1,000-fold scale-up in a pilot unit at Southwest Research Institute (SwRI) in San Antonio. With successful results at the pilot scale, EcoCatalytic will continue to work with SwRI to take this production method from pilot to the commercial scale. The technology, which was initially developed through an ARPA-E award in 2013, is an excellent example of inter-office collaboration within DOE.
Within the Office of Energy Efficiency and Renewable Energy, AMO supports the development of innovative, energy-efficient production methods for ethylene as part of its chemical manufacturing portfolio. Additional information about the opportunities AMO has identified for energy savings around ethylene production can be found in the office’s Chemical Bandwidth Report (2015). Pages 42 and 57 provide more details.
More than 60% of ethylene produced worldwide is used to manufacture precursors to plastics.2 Innovation in ethylene production supports the goals of DOE’s Plastics Innovation Challenge. This Department-wide effort seeks to dramatically reduce plastic waste in oceans and landfills and position the U.S as global leader in advanced plastics recycling technologies and in the manufacture of new plastics that are recyclable by design. Visit the Plastics Innovation Challenge website to learn more.
1 "Ethylene Oxide and the Potential Cost of Deselection." American Chemistry Council, 2019.
2 "Commodities – Ethylene, Plastics, and their Supply Chain." Spendmatters.com, April 2, 2012.