Energy modeling is often used to evaluate ECM payback, calculating the operational energy savings that accrue after an initial capital investment. One
May 23, 2016Energy modeling is often used to evaluate energy conservation measure (ECM) payback, calculating the operational energy savings that accrue after an initial capital investment. Energy modeling itself can also be viewed as an ECM, with an upfront cost during design that leads to operational savings. Given that viewpoint, it is interesting to evaluate the cost-effectiveness of modeling. Simple payback analysis has shortcomings—for one, it ignores the fact that an ECM typically provides ongoing returns—but is still commonplace, as is the rule of thumb that a three year or shorter payback is required to make an ECM cost-effective or attractive. What is the typical payback of modeling?
Anica Landreneau, director of sustainability consulting at global architecture and engineering firm HOK, decided to find out. Over the course of several years, HOK tracked both modeling costs and predicted energy savings for a large number of HOK projects. The answer—energy modeling payback is typically 1 or 2 months!—is surprising at first. But it shouldn’t be. For large buildings, modeling costs run from $30,000 to $200,000 depending on the ECMs considered and the tools required to evaluate them. Even the high side of that figure is a fraction of the annual energy costs of a typical large building. If modeling can help designers quantify the energy savings of ECMs and get them accepted into the design it can pay for itself very quickly. In fact, modeling can sometimes pay for itself immediately—before construction ends and the building is occupied—by identifying unnecessary costs, the most common example being oversized, and unnecessarily expensive, HVAC systems.
Landreneau presented HOK’s findings along with several case studies at last week’s Better Buildings Summit in Washington, D.C. The first project, DC’s own Consolidated Forensics Lab (CFL), opened in 2012 as the first LEED Platinum building of its kind—a combined morgue, forensic lab and public health lab combined. Energy modeling was critical to getting the CFL built in the district. By using hydronic HVAC systems—i.e., HVAC systems that rely on circulating hot and cold water rather than hot and cold air—the CFL can accommodate shorter plenums and shorter floor-to-floor heights, which in turn allowed the 350,000 square foot building to fit both within its intended downtown site and under the district’s building height restrictions. The CFL also includes a dynamic façade that is controlled by an on-site weather station. Modeling costs for the project were $60,000 and payback was 1.3 months.
A second project, the Daniel Inouye Regional Center in Honolulu, Hawaii, opened in 2014. For this project, the HOK team used a more comprehensive modeling package that included an energy model, a daylight model, and a computational fluid dynamics (CFD) model, which cost $170,000. The CFD model was needed to evaluate a cooling and ventilation system that uses rooftop projections to capture the trade winds and cool the outside air with sea water pumped up to the roof from a deep sea well. Even this more expensive modeling package was able to pay for itself in 4.4 months.
According to Landreneau, modeling is critical to HOK’s mission and a key tool in maintaining the firm’s global standing as a high-performance leader. HOK also sees modeling as a mechanism for shifting investment from a building’s active, mechanical systems to its passive, architectural elements, benefiting not only energy-efficiency, but also durability and aesthetics. HOK uses a combination of in-house and contract modeling services, and its modeling contract language specifies the times during the design process when models must be delivered.
“Energy modeling is a no-brainer for HOK, and we believe for our clients,” Landreneau said. “It’s like reading the MPG (miles per gallon) rating before you buy a car. It’s basic performance information every building investor should know. Energy modeling on all our projects helps HOK meet our internal energy and carbon commitment (AIA 2030), helps our clients find cost-effective ways to meet their sustainability goals, and supports a more creative, beautiful and resilient design outcome.”
A frequent question about the value of energy modeling—and one that came up again during the Summit session—is how much energy savings should be attributed to the modeling process, as good engineers can create energy-efficient designs using simple calculations plus experience and professional judgment. According to Landreneau, modeling is critical to getting ECMs accepted into the final design and finding first cost trade-offs like system size reduction or elimination: “Owners and project managers do not accept reduced HVAC systems based on engineering judgment—they demand to see numbers!” Modeling may not be necessary to designing an energy-efficient building, but it is necessary to getting that energy-efficient design built.
Dr. Amir Roth
Dr. Amir Roth is the technology manager for BTO’s Building Energy Modeling (BEM) subprogram and has served in that role since 2010. From 2001 to 2010 he was first an assistant and then an associate professor with tenure of Computer and Information Sciences at the University of Pennsylvania in Philadelphia. He graduated magna cum laude with a B.S. in physics from Yale University and holds a Ph.D. in computer science from the University of Wisconsin—Madison where he won a dissertation award in 2001. He is a member of the American Society of Heating, Refrigeration, and Air-Conditioning Engineers (ASHRAE), and the International Building Performance Simulation Association (IBPSA).
Email Amir Roth ►
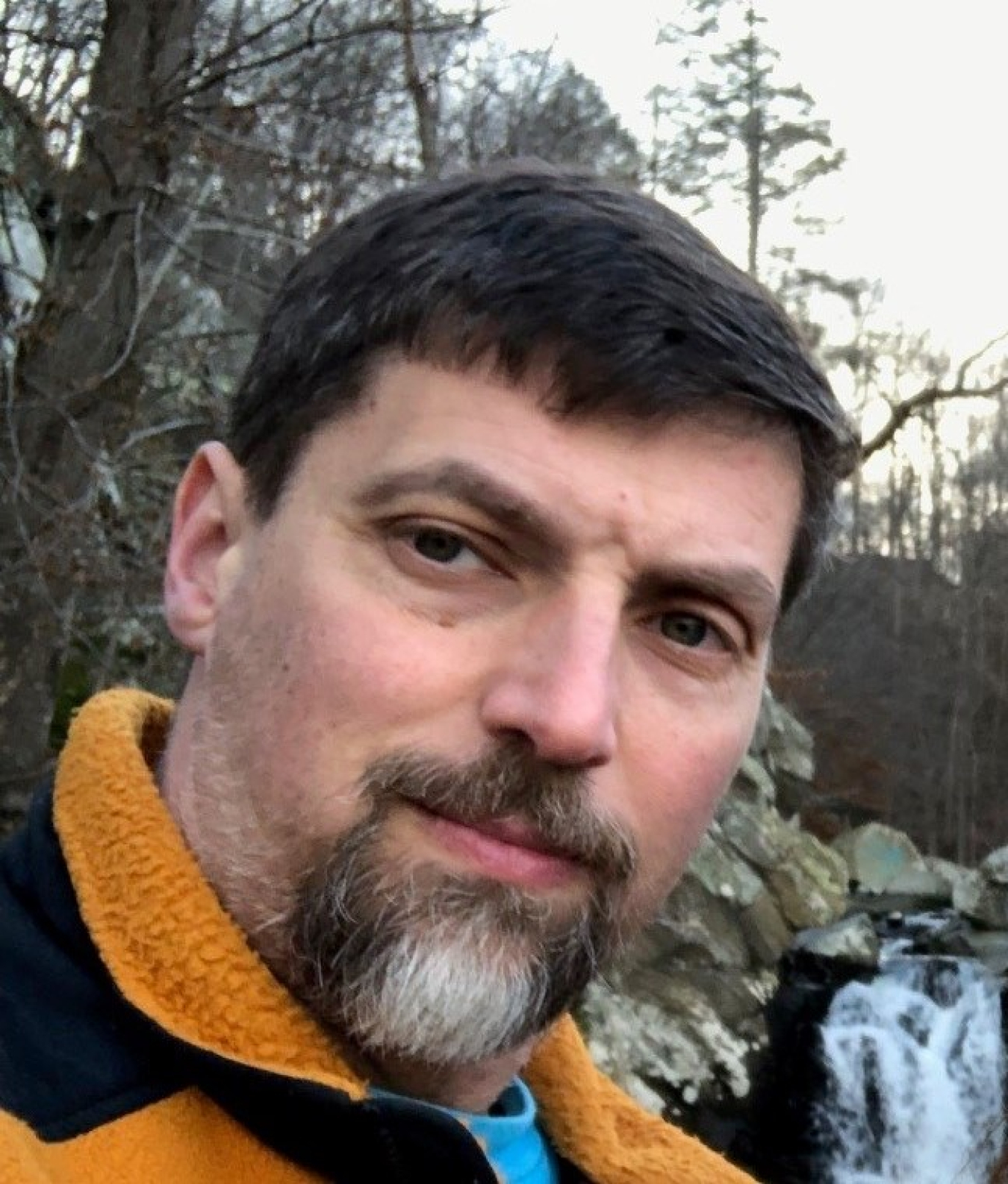