Reactor-scale models, developed by the Consortium for Computational Physics and Chemistry (CCPC), enable evaluation of the large-scale conversion of biomass with the objective to scale up the process economically for commercial viability.
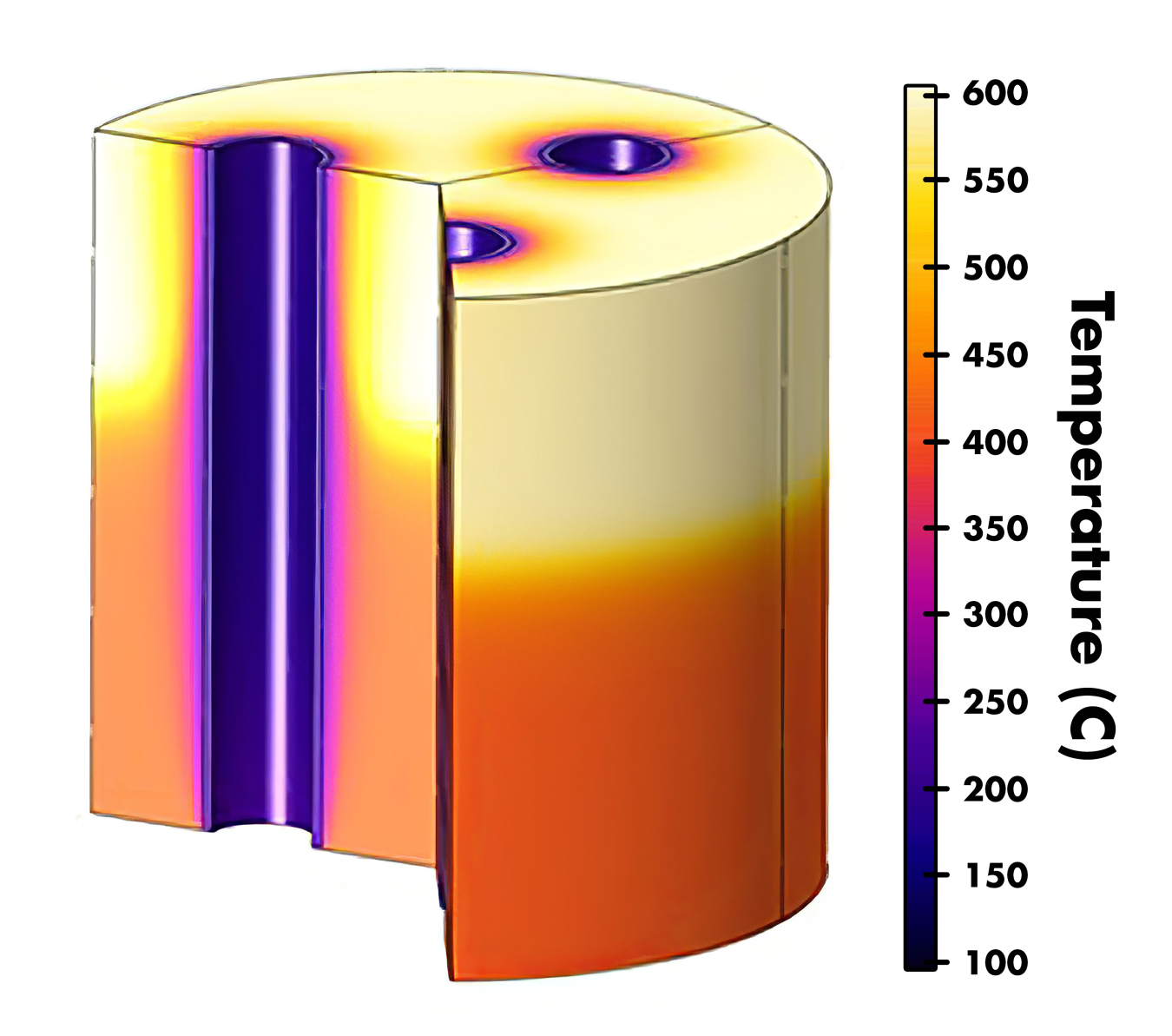
A model of a cylindrical-shaped catalyst bed reactor that shows the temperature distribution along the reactor flow axis during a coke regeneration event. Image courtesy of Bruce Adkins, Oak Ridge National Laboratory.
Due to the large financial funding required to build a biorefinery, it is critical to have accurate reactor-scale models to ensure that the funding in biorefinery construction will lead to reliable and cost-effective operations. Furthermore, reactor models are extremely useful for optimizing the final design of the biorefinery and the associated controls for efficient operation.
Low-Order and High-Order Reactor Modeling at CCPC
The CCPC utilizes both low-order and high-order models of reactors. Low-order models use simplified approximations of complexity to enable more computationally feasible methods. High-order models capture full or near full complexity but require computationally intensive methods.
The complexity of biomass feedstocks is extremely high and very difficult to fully capture in high-order modeling, so the CCPC uses a combination of high-order and low-order modeling to capture the biocomplexity yet produce models that are computationally feasible even for larger-scale reactors. Both approaches to modeling integrate the particle-conversion models developed in the mesoscale efforts of the CCPC.
There are two types of CCPC high-order models:
- Computational fluid dynamics models
- Finite elemental models
Computational fluid dynamics models simulate the mass and heat transfer and chemical reactions occurring in fluidized bed reactors where the catalyst or biomass media physically move or flow in a fluid state inside the reactor while process gases flow through the reactor.
Fluidized bed reactors (Figure 1) are complex and result in dynamic flow or “fluidization” of the catalyst or biomass particles that can vary greatly depending on reactor design, process gas flow rates, temperature, and particle characteristics such as size, shape, and density. However, when designed properly, fluidized bed reactors can provide the optimal mixing of reactant gases and particles to achieve maximum conversion to desired products.
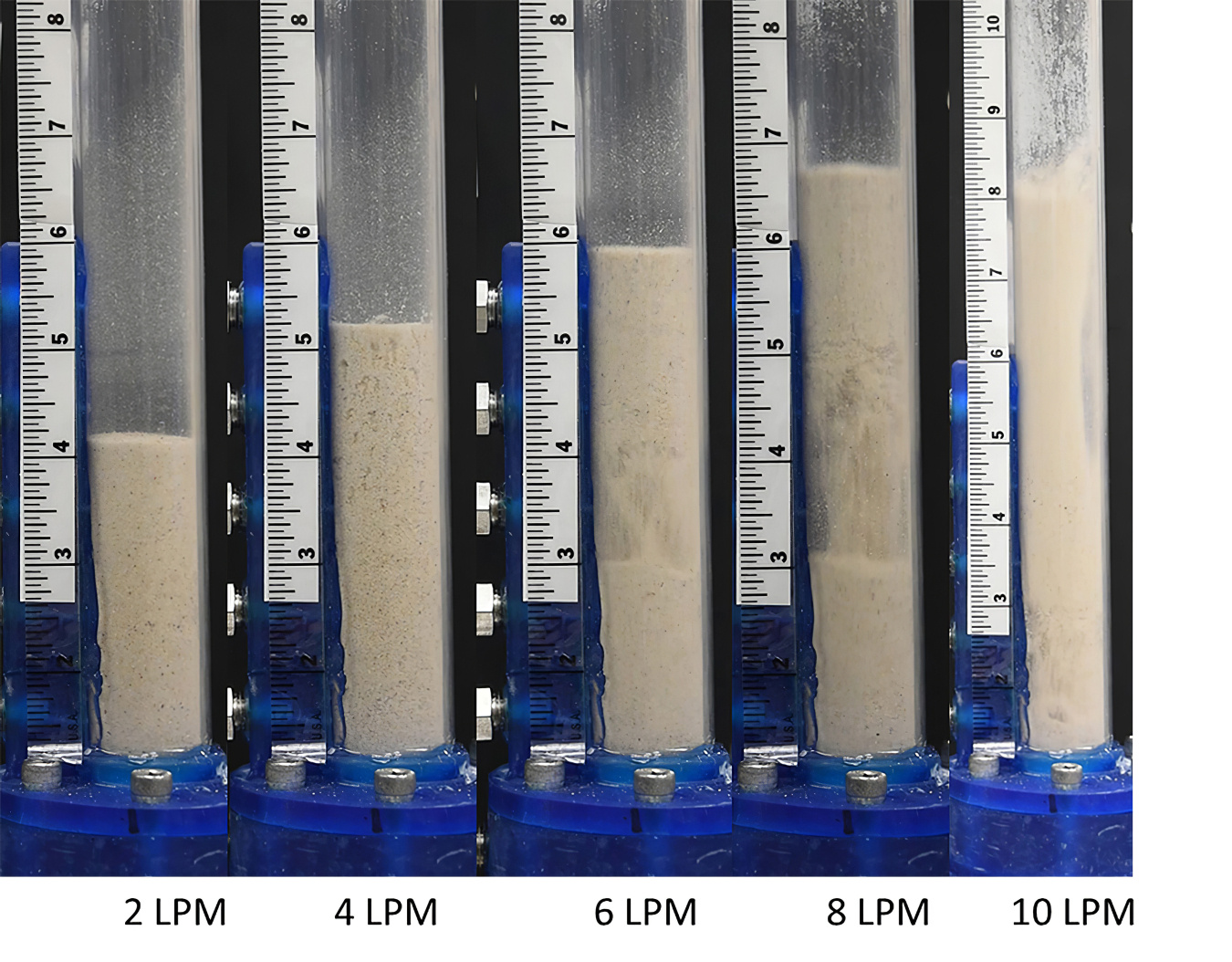
Figure 1: Images showing a “cold flow” fluidized bed reactor with process gas flowing through a sand and biomass mixture at flow rates from 2 to 10 liters per minute (LPM). Cold flow reactors are used by the CCPC to observe fluidization of particles through the glass or plexiglass walls of the reactor. As the process gas flow rate increases, the bed of sand and biomass increases in height as more bubbling occurs in the bed and the movement of solids increases. Note that the 10 LPM case was captured from a different camera angle to observe the full bed expansion. Image courtesy of Bill Rogers, National Energy Technology Laboratory.
Finite element models simulate the mass and heat transfer and chemical reactions occurring in fixed-bed reactors where the catalyst or other reactor materials are stationary and the process gases flow over the catalyst “fixed bed.”
In both modeling approaches, close collaboration with experimentalists is necessary to ensure that the models accurately describe the physical experiments so that model-based predictions about future performance scenarios can be trusted. The process of comparing model-based results to experimental results is known as “model validation.”
Modeling Reactors for Converting Biomass to Fuels
In the process of converting biomass to fuels, multiple steps are involved depending on the conversion pathway. The CCPC has developed models of two reactors that are used in series in a biomass-to-fuel pathway known as ex situ catalytic fast pyrolysis.
The first reactor is a fluidized bed reactor where biomass is thermochemically converted into pyrolysis oil vapors, char, and light gases. The oil vapors are the primary product of interest, but the oil contains high levels of oxygen and needs to be deoxygenated in a downstream catalytic reactor.
Thus, a second reactor called a catalytic upgrading reactor utilizes a catalyst to remove oxygen from the oil for further refining into transportation fuels readily compatible with U.S. fuel infrastructure.