Bioprose Blog: New flow chemistry methods from UCSD enable 100% renewable foam made from algae feedstocks.
July 16, 2020Author: Daniel B. Fishman, Technology Manager, Advanced Algal Systems
Read Daniel's bio ►
Meet the other bloggers ►
Return to Bioprose blog ►
Foams are a ubiquitous consumer product, supporting people in many different ways – think yoga mats, seat cushions, mattresses, insulation, footwear, and more. These diverse products all have one thing in common: they’re made from polyurethane.
Most polyurethanes are made from petroleum, but in recent years foam makers have tried to incorporate renewable building blocks made from plants and algae. Until now, creating foams entirely from plants and algae was impractical, but researchers at Algenesis in La Jolla, California, are making exciting progress toward changing that!
Sunny San Diego and the Pursuit of 100% Renewable Foam
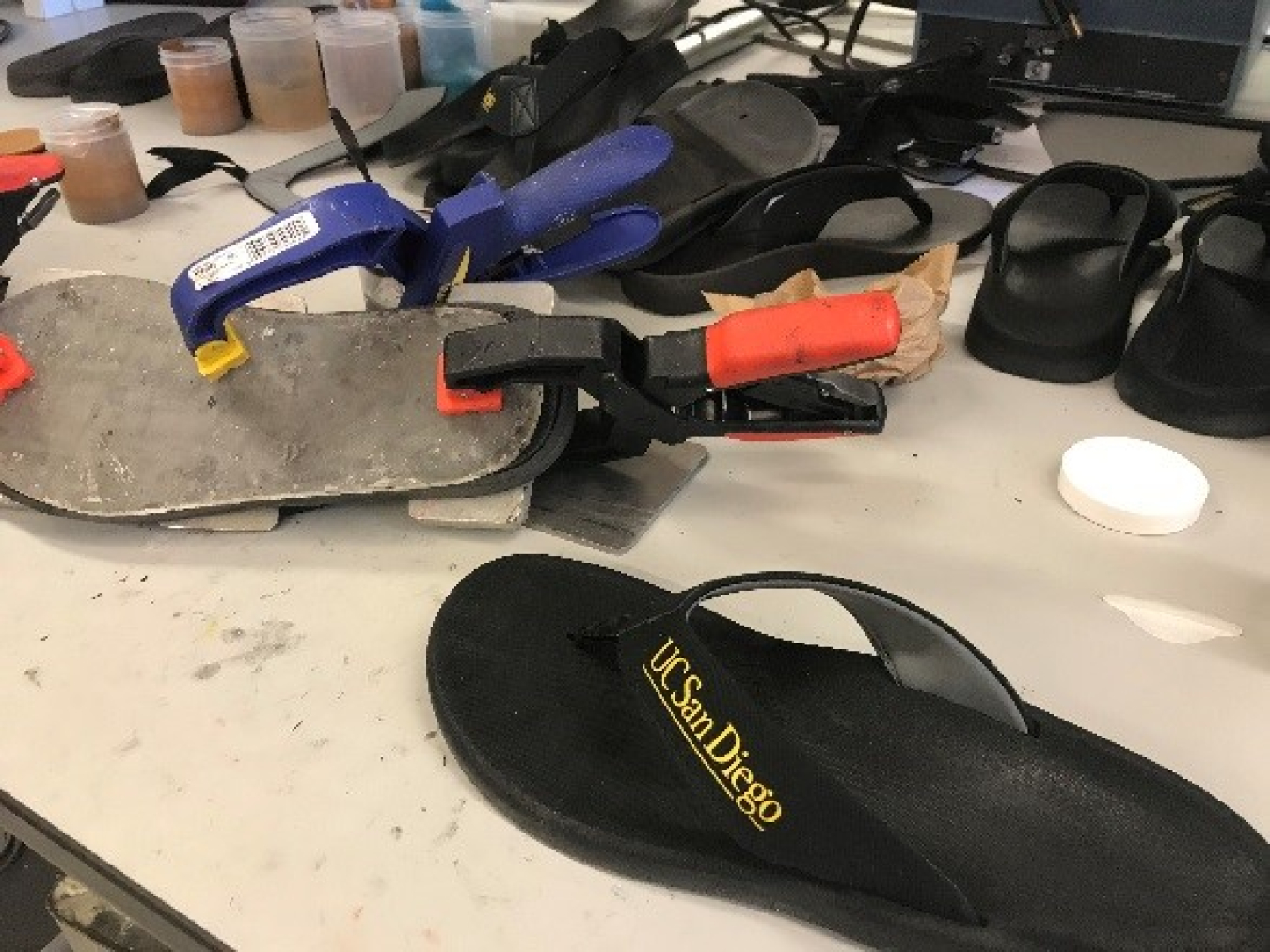
A flip-flop prototype made by Algenesis in their UCSD laboratory. Photo credit: Daniel Fishman
When the Advanced Algal Systems team at the Bioenergy Technologies Office (BETO), led by technical manager Daniel Fishman, last caught up with this group of researchers based at the University of California, San Diego (UCSD), including this blog’s co-author Professor Michael Burkart, they were making waves (literally!) with the world’s first algae-based surfboard. While that breakthrough generated interest globally, the BETO and UCSD project partners knew there was more work to be done, because the foam that went into the surfboard, and a range of other products like flip-flops, was only half algae. The other half of the foam recipe still called for a petroleum-based family of chemicals known as isocyanates.
A Simple Chemistry Tutorial on Polyurethanes
To understand what the researchers did next, we need a short primer on how polyurethanes are made.
Polyurethanes are prepared by reacting roughly equal amounts of one set of molecules known as polyols with another set of molecules known as diisocyanates. Combining these two chemical building blocks causes a reaction and builds a crosslinked molecular framework that we all recognize as the squishy foams incorporated into many common household products. Modifying the type of polyol or diisocyanate results in a range of physical properties, including:
- Rigid foams (insulation)
- Flexible foams (mattresses)
- Molded foam (car molding)
- Elastomers (skateboard wheels)
- Adhesives (construction glues)
- Coatings (paint)
The All Algae-Based Foam Breakthrough
Developing algae-based isocyanates needed for fully renewable foams would require a creative solution. The research team began by reviewing the existing process and found that today’s petroleum-based isocyanates are commercially produced by reacting organic amines with phosgene – a dangerous and expensive process only undertaken in a few locations globally.
By identifying the chemical composition of the algal material they had, the team realized that an existing process called the Curtius rearrangement, which can convert oils to acyl azides (AA) and then into diisocyanates, could offer a solution. Developed in 1885, the Curtius rearrangement was long known but has one major problem—the intermediate, azelaic diacylazide, is extremely explosive and could not be prepared safely in large quantities.
More Chemistry to Go with the Flow
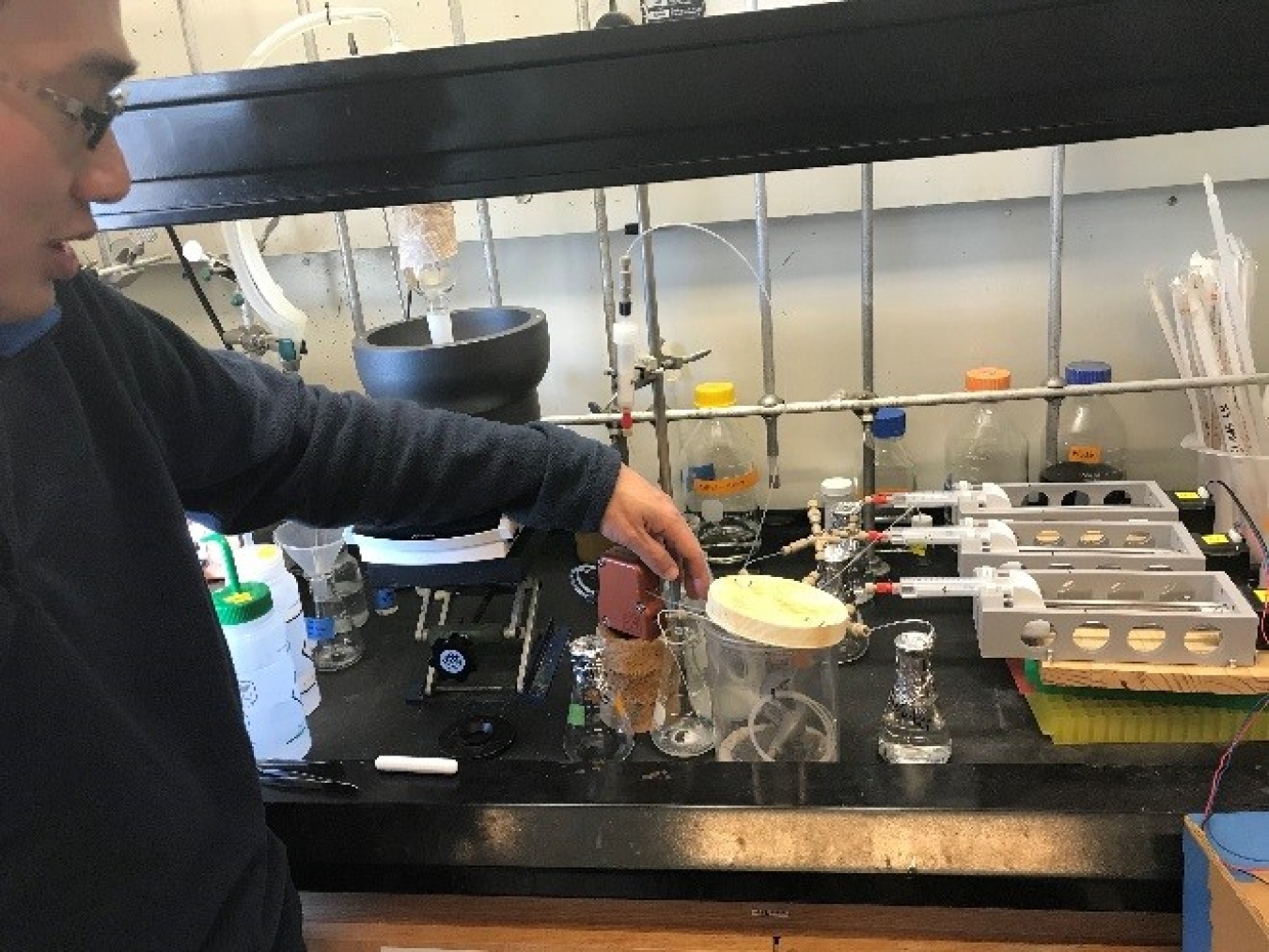
Researcher Dr. An Phung Hai shows off the 3D-printed flow reactor that makes previously dangerous chemistry for isocyanate production safe and accessible. Photo credit: Daniel Fishman
The inability to scale due to explosive intermediates was a no-go for the UCSD researchers, so they turned to flow chemistry. A rapidly growing area of academic and industrial research, flow chemistry uses pumps and tubing to carry out chemical reactions in a continuously flowing stream rather than in batch processes. This technology allows for the development of routes that may create dangerous intermediates, but the intermediates do not accumulate in significant quantities because they don’t need to be isolated. Instead, they immediately react in flow after they are formed and subsequently transform into a stable and safe end product.
In their flow chemistry set up, the UCSD team chemically converted AA into azelaic dihydrazide, a stable and easily purifiable precursor. It was then reacted in flow with nitrous acid to prepare azelaic diacylazide, which was immediately directed into a high-temperature flow reactor and converted into a stable and safe isocyanate.
The team first made a flow apparatus using 3D-printed parts to demonstrate proof of concept, then scaled up the process. Along the way, the team showed that the methodology can be used to prepare isocyanates from any organic acid derived from plants or algae.
Sourcing the Algae Feedstock
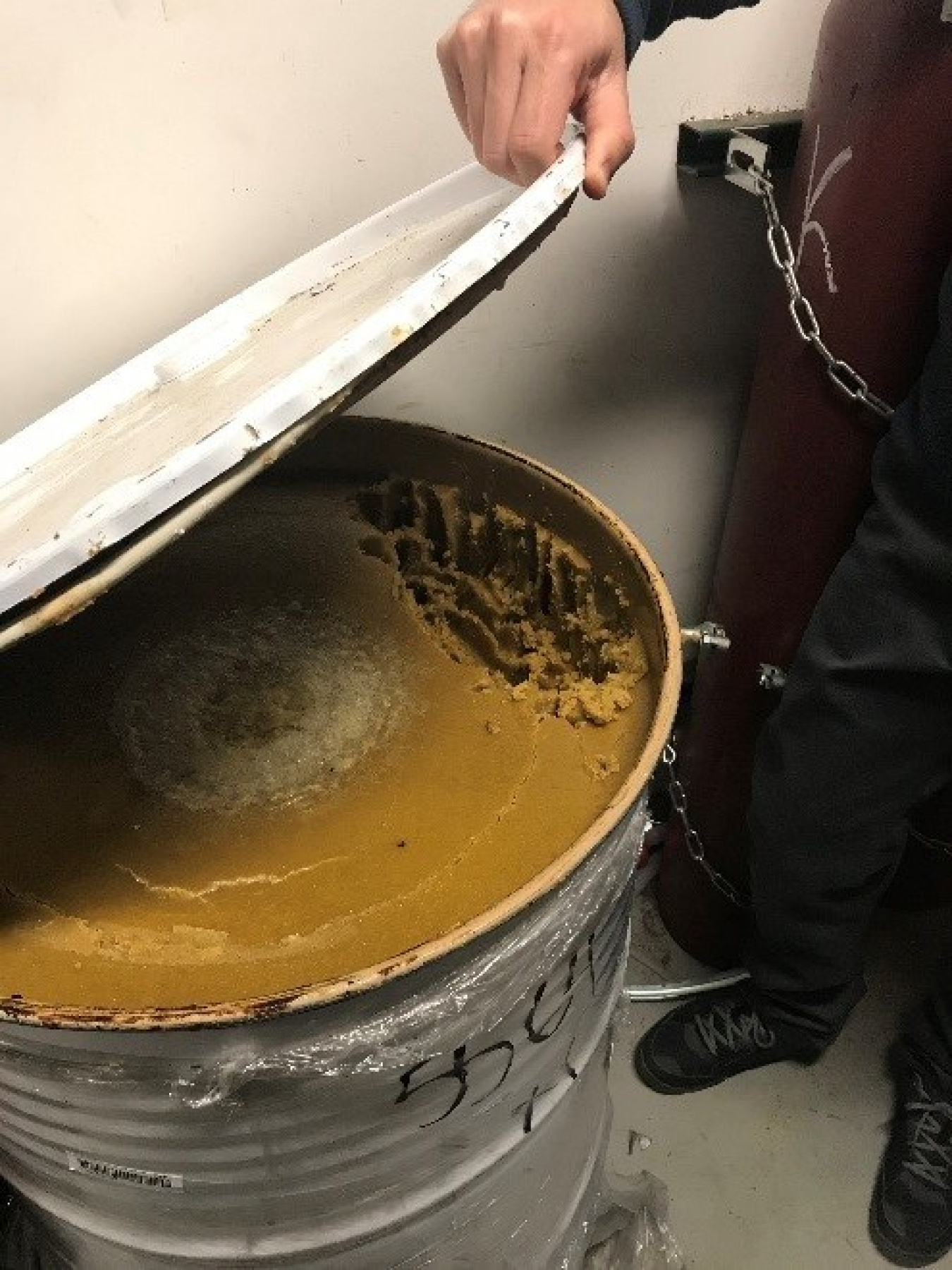
Algae oils left over after omega-3 extraction. The oils are purified and converted to renewable isocyanates via flow chemistry. Photo credit: Daniel Fishman
Now with a way to make both building blocks—the polyols and the isocyanates—from renewable sources, the team decided that rather than grow their own algae, they would use algae material they had readily on hand: a waste stream of algae oil that is a residual of commercial omega-3 oil production.
Among commercialized algae products, omega-3 fatty acids derived from algae are a valuable commodity in the animal feed and human nutraceutical sectors. Purification of omega-3s from algae oil generates a waste stream that contains mixtures of saturated and monounsaturated fatty acids, the perfect starting point for both the renewable isocyanate chemistry just developed, as well as the polyol chemistry previously described (Figure 1).
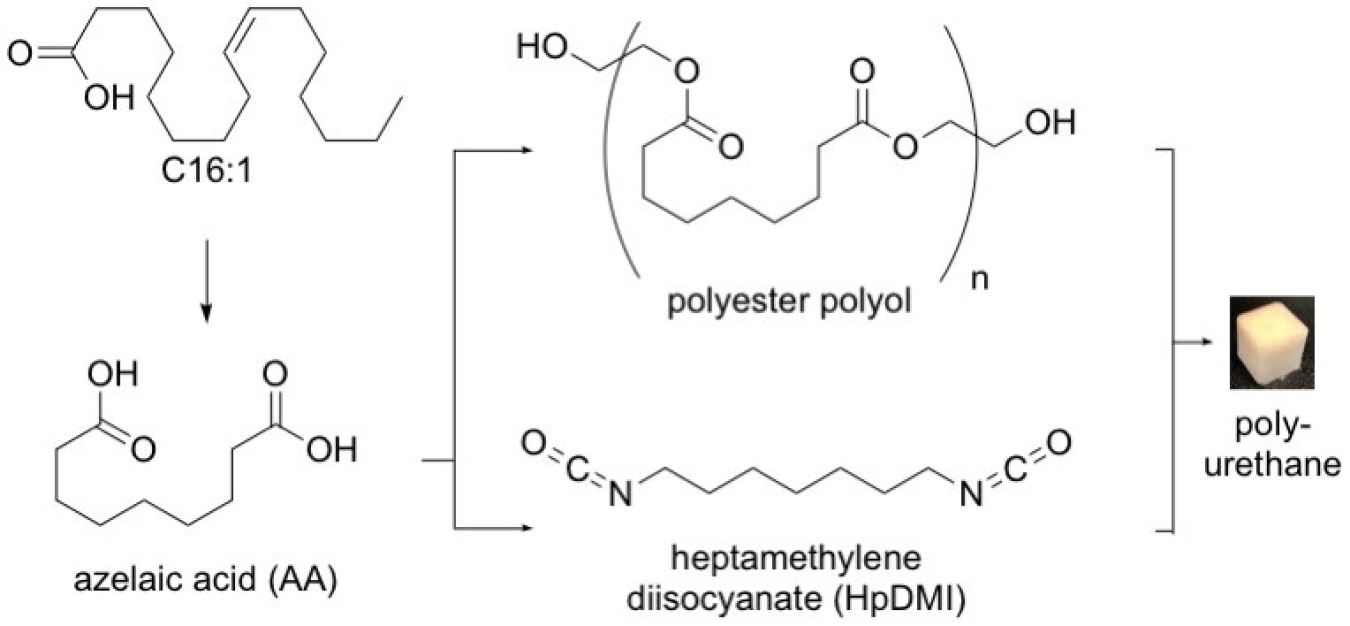
The chemical reaction to make polyurethanes from algae oil waste streams. Algae oils (specifically the molecule labeled C16:1) are converted into azelaic acid (AA), which can be then be converted into either polyols or diisocyanates. Credit: Dr. Burkart
Next Steps in the Pursuit of Commercial-Scale All-Renewable Foam
Moving forward, the UCSD team is scaling these flow chemistry processes and working to understand how to manipulate the material properties of the resulting foams to identify potential commercial opportunities. The waste algae oil from existing commercial applications, coupled with these new flow chemistry methods, could offer competitive, fully renewable solutions that are a worthy successor to the polyurethane foam products currently manufactured.
The complete process, funded by a U.S. Department of Energy grant, is described in detail in a manuscript entitled “Preparation of Mono- and Diisocyanates in Flow from Renewable Carboxylic Acids.”
Daniel B. Fishman
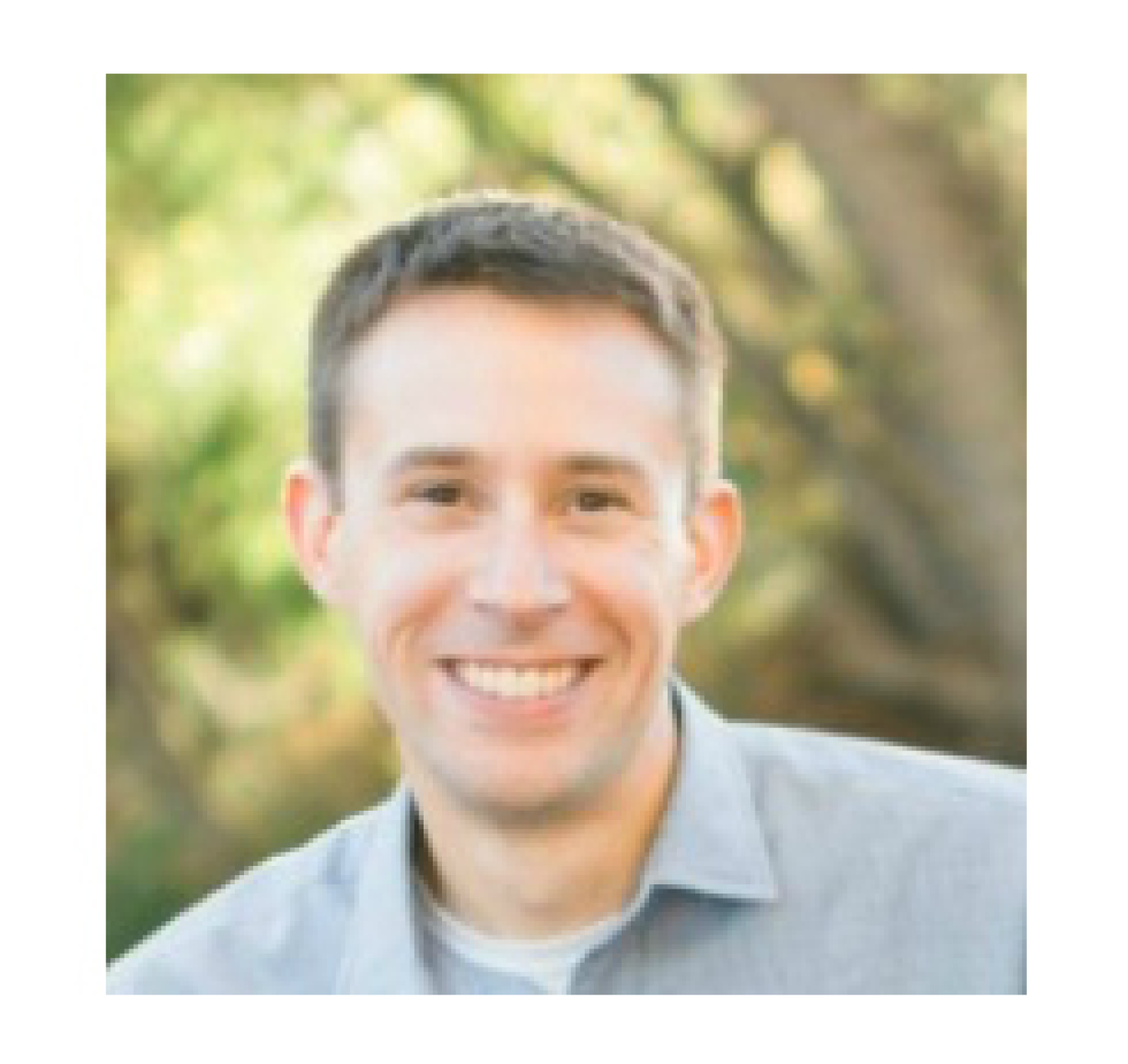
Daniel B. Fishman is a technology manager with the Bioenergy Technologies Office at the U.S. Department of Energy, where he helps manage the portfolio of applied research projects focused on developing algal biofuels. Daniel received his Master of Science in aquatic science from the University of Michigan’s School of Natural Resources and the Environment and has a background in aquatic ecology, dynamic ecosystem mathematical modeling, and harmful algal blooms. Daniel received a Bachelor of Science in environmental systems from Revelle College at the University of California, San Diego.
Meet our other bloggers ►
Return to Bioprose blog ►