Bioprose Blog: Argonne National Laboratory researchers pioneer innovative approach to recover bioproducts.
July 25, 2019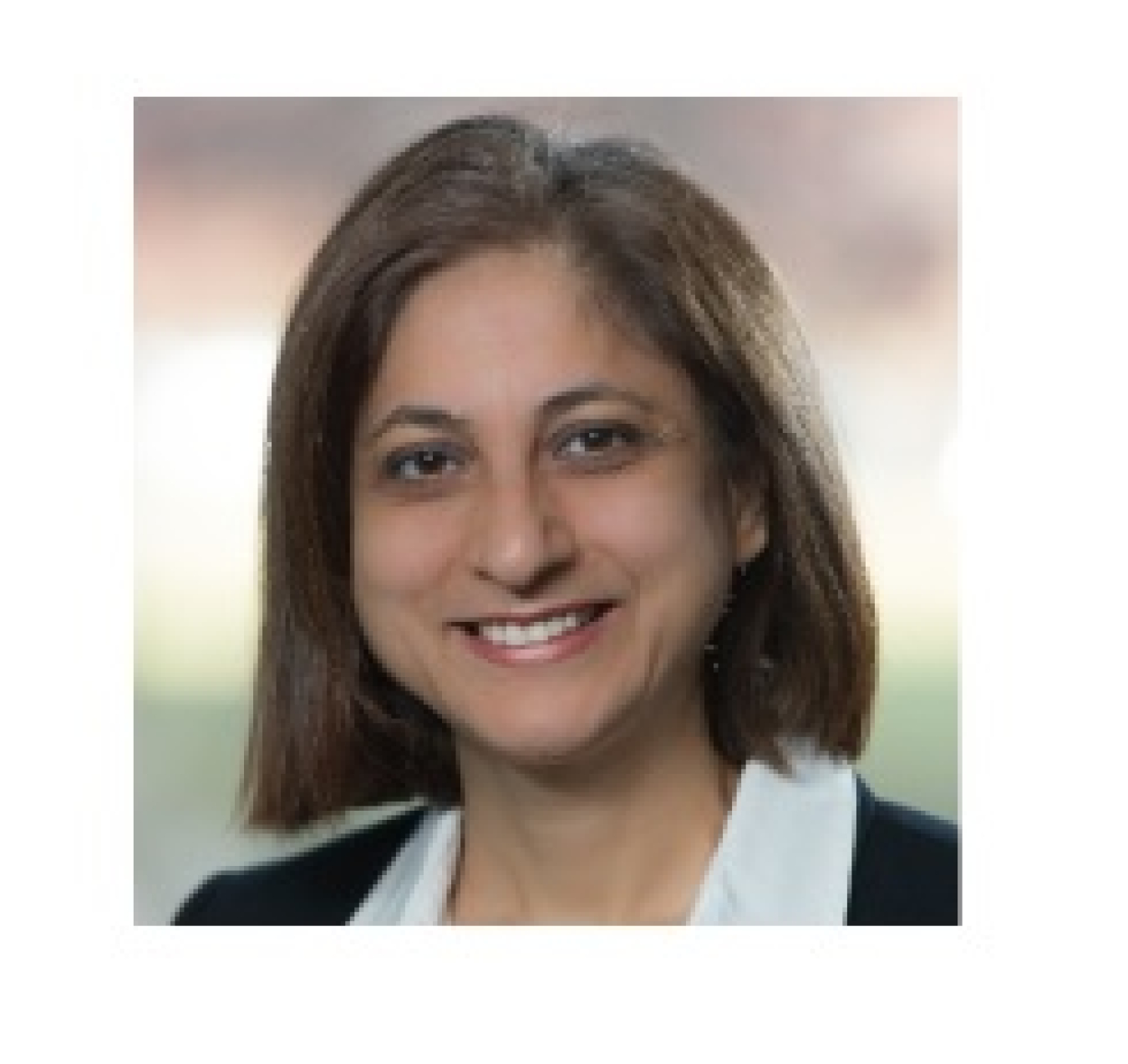
BIOPROSE BLOG
Through revolutionary scientific advances in the product manufacturing recovery process, manufacturers can now develop everyday materials and chemicals from renewable resources like plants, algae, and wastes.
Novel Adsorbent Reduces Costs, Enhances Efficiency and Yield
Researchers led by Philip Laible at the U.S. Department of Energy’s (DOE’s) Argonne National Laboratory (ANL) have developed an innovative separation process based on high-surface area, flexible, and highly porous solids. ANL's unique materials approach incorporates an adsorbent directly into the fermentation process and could help bioproduct manufacturers overcome many of the challenges of separating the desired bioproducts, while lowering costs and increasing productivity and product quality.
Current bioproduct separation processes—including centrifugation, multi-step extractions, and distillation—are expensive and require large amounts of energy. In addition, particulates that are left over from renewable resources used as feedstocks can build up in the equipment, slowing down the separation process and decreasing the amount and purity of the bioproducts recovered.
In ANL’s novel approach, an adsorbent solid, known as a xerogel, is formed through polymerization of silicon-based materials around a nanostructured template and can separate and purify the bioproduct synthesized during the fermentation processes. ANL’s xerogel adsorbent:
- Improves the bioproduct yield as bioproduct concentrations never accumulate to appreciable levels
- Continuously removes the bioproduct, reducing the volume of bioreactor that is needed and allowing for the fermentation step to run continuously
- Recovers bioproduct in high purity
- Eliminates the need for additional raw materials (e.g., detergents, solvents, acids, bases) required for de-emulsification in traditional approaches.
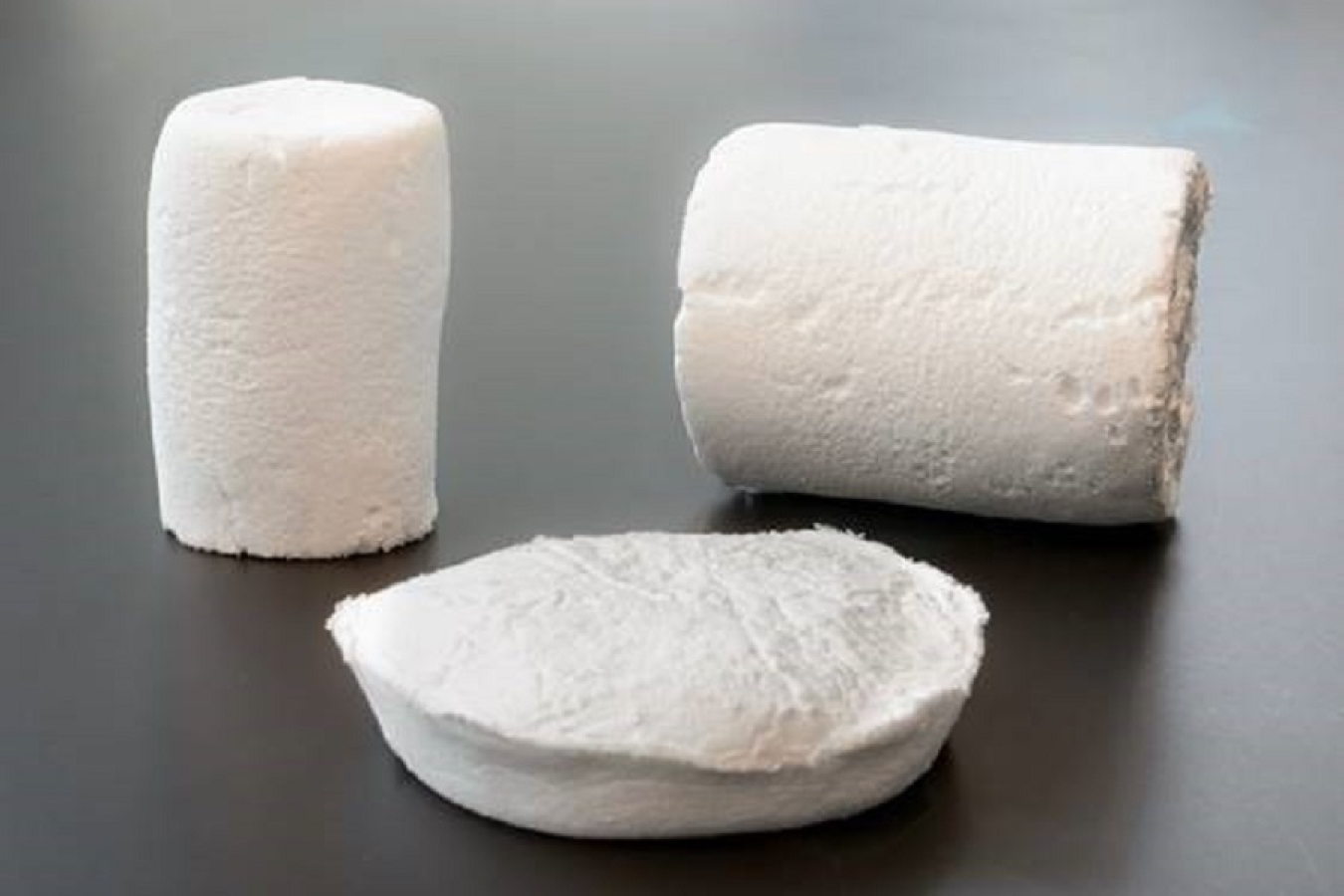
Nanostructured adsorbents can be synthesized in a variety of formats to adapt to recovery processes that function under a variety of conditions and operate at a variety of scales. Photo: Phil Laible, ANL.
Xerogel and the Recovery Process
According to Dr. Laible, the xerogel looks and feels like a dense sponge. It can be folded and compressed but bounces back, retaining its shape and structure. Researchers can synthesize the xerogels using different mixtures of starting materials and tailor their properties to allow recovery of many types of desired bioproducts.
Dr. Laible’s team has demonstrated that, when specifically made to recover bioproducts, xerogel materials deliver excellent performance—adsorbing up to eight times their mass with nearly 100% selectivity, without negatively impacting the production process driven by engineered microorganisms in the bioreactor.
The resiliency of the xerogel adsorbent means the material can be reused for tens of cycles in bioreactors, significantly reducing bioproduct recovery costs. A simple mechanical compression of ANL’s adsorbents leads to the release of high-purity bioproducts and offers an alternative low-thermal-budget technology.
ANL’s work on xerogel began in fiscal year 2017 with funds from DOE’s Bioenergy Technology Office (BETO) and continues as part of the BETO Bioprocessing Separations Consortium (https://www.bioesep.org).
About BETO
DOE’s BETO supports early-stage research and development of energy efficiency and renewable production of biofuels, bioproducts, and biopower technologies that make energy more affordable and strengthen the reliability, resilience, and security of U.S. energy supply.
Dr. Meltem Urgun-Demirtas
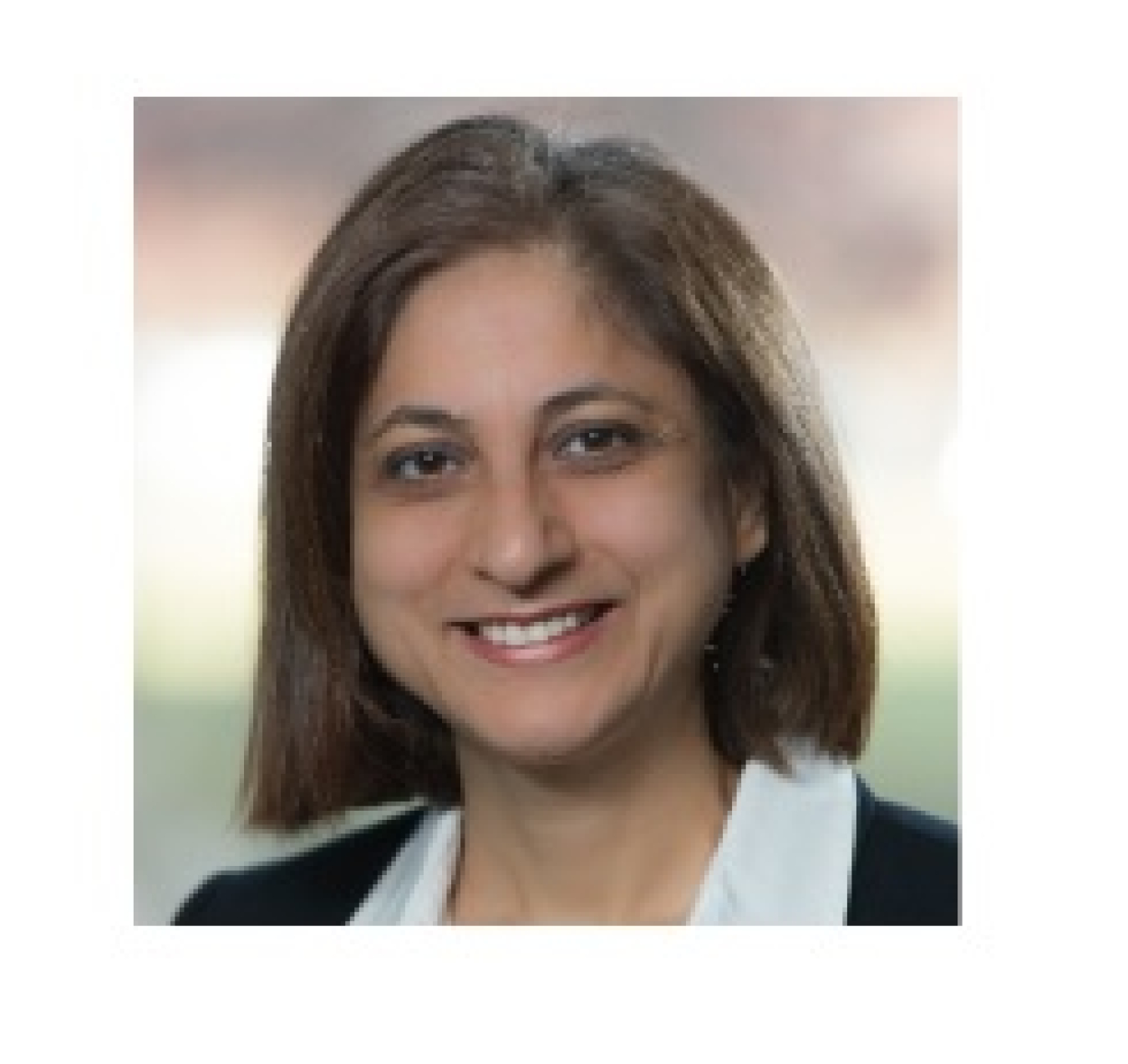
Meltem Urgun-Demirtas is a group leader of process development research in Argonne National Laboratory’s Energy Systems division, where she brings over 15 years of diverse experience in waste and water treatment, biofuels production, and materials synthesis for energy and environmental applications. She has extensive experience in design and operation of chemical and bioprocesses from bench to field scale, techno-economic assessment, modeling and optimization of processes. She is a fellow of the Northwestern University—Argonne Institute of Science and Engineering. Dr. Urgun-Demirtas has published over 30 journal papers and 50 conference papers and holds four patents/patent applications. Prior to working at Argonne, she was a research engineer at BP North America. She received a Bachelor of Science in chemical engineering and a Ph.D. in environmental engineering.
Meet our other bloggers ►
Return to Bioprose blog ►