Underlying our aerospace, defense, and energy industries are manufacturing components that can resist extreme heat and pressure.
Advanced Materials & Manufacturing Technologies Office
October 13, 2022Underlying our aerospace, defense, and energy industries are manufacturing components that can resist extreme heat and pressure. These parts are often made out of a metal called Inconel 718-- a superbly strong, noncorrosive, temperature-tolerant, nickel-chromium alloy.
This metal is normally machined, peened, pulled, rolled, and welded to create the shape and microstructure needed to have the desired high-performance properties. The metal is typically used in parts for rocket motors, jet engines, pressure vessels, gas turbines, and the like. But working the metal is expensive. For parts with complex geometries and internal features, direct fabrication—producing a product in final form—would be the economic grail.
To achieve this, researchers have turned to additive manufacturing (AM), specifically laser powder-bed fusion (LPBF) technology, for "near-net-shape," close-to-final manufacturing of aerospace components. Since 3D objects are built layer by layer through AM, and different parts of the material have different cooling rates, a variety of cross-sections and microstructures are formed. The challenge is that the thermal conditions of LPBF results in microstructures and mechanical properties that fall short of what’s needed for the final product.
Post-processing heat treatments could help restore the desired properties, but designing the most effective treatment while maintaining the target microstructure requires computational muscle.
United Technologies Research Center (UTRC) working with Pratt & Whitney and UTC Aerospace Systems is developing a physics-based process model to predict microstructures for AM aerospace structural components made of nickel superalloys.
To tap the high-performance computers needed for modeling and simulation of 718 heat treatments, UTRC turned to the Advanced Materials & Manufacturing Technologies Office’s High Performance Computing for Manufacturing (HPC4Mfg) and the computational materials scientists at Oak Ridge National Laboratory (ORNL). HPC4Mfg connects industry partners with world-class supercomputing resources at DOE’s network of national labs.
For this project, industry partners first demonstrated a high-fidelity simulation tool that captured the evolution of as-built Inconel 718 microstructures. Simulations at ORNL used their phase-field code to ascertain how composition gradients, local composition, the strain field of preexisting dislocations, and heat-treatment temperatures affect the material’s microstructure. The modeling effort confirmed the value of using HPC and the phase-field simulation tool to design optimal post-process heat treatments that meet Inconel 718 target properties.
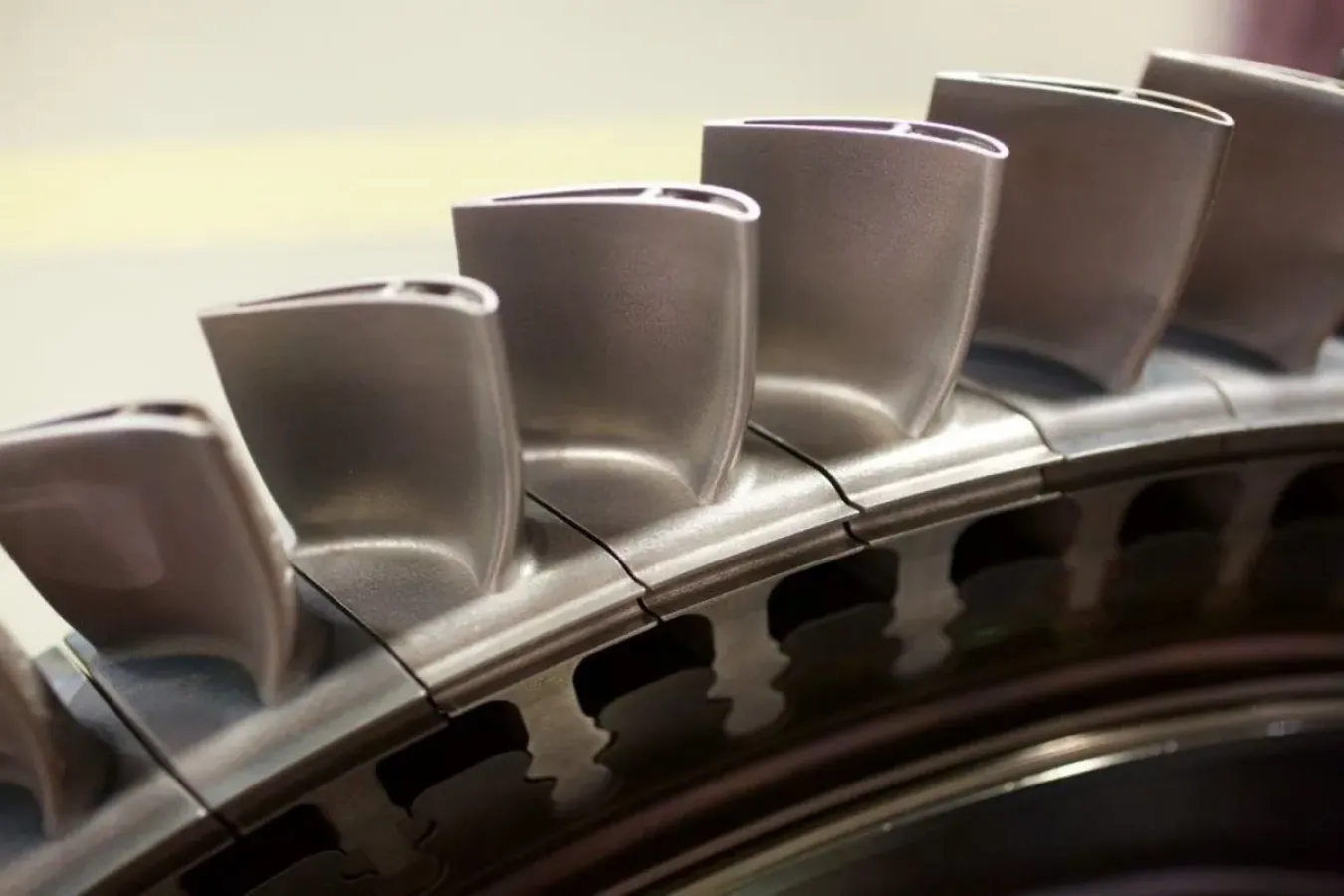
Above: A gas turbine manufactured using additive manufacturing technologies. Products with complex geometries are especially challenging for additive manufacturing methods; requiring cutting-edge computing power to simulate how the material responds to thermal treatments.
Researchers were able to eliminate the need for post-processing heat treatments, which spoil the fine microstructure produced during AM. Future modeling improvements will enable researchers to achieve optimal mechanical properties and discover whether optimized LFPB procedures can avoid negative microstructural characteristics which degrade the performance of the material.
The processing and post-processing innovations guided by HPC-based predictive modeling can be used by manufacturers of critical AM products. By cutting development time and experimental cost, reducing energy consumption for both AM and heat treatments, and minimizing failed parts and optimization iterations, AM manufacturers can anticipate 30–40% savings in energy costs, besides conservation of time and materials—a sizable benefit to the national economy and the bottom line.
This makes additive manufacturing a much more viable manufacturing technique for high performance materials. By manufacturing components at or near the shape at which you need them to be, rather than beginning with a metal and working it into the desired shape, manufacturers can save time, energy, material, and costs throughout the manufacturing process.
***
The Advanced Materials and Manufacturing Technologies Office (AMMTO) supports the advancement of technologies to make the U.S. manufacturing sector more competitive and build a strong, cost-effective energy sector. AMMTO has three major program teams: next generation materials and processes, secure material supply chains, and energy technology manufacturing and workforce. These programs will accelerate the manufacturing of renewable energy technologies domestically, development of secure supply chains, and the fostering of a skilled and inclusive manufacturing workforce.
Read more about AMMTO here.