New ways to use cerium may help shore up market demand for an abundant rare earth element and create more value from domestic rare-earth mining operations.
Advanced Manufacturing & Industrial Decarbonization
February 9, 2023The clean energy transition depends on critical materials like rare earth elements (REEs) that power wind turbine generators, electric vehicles and other clean energy technologies, materials, and processes. REEs are found together in mineral deposits, which are then separated from one another to use only the REEs needed for manufacturing. Rare earth elements are uniquely difficult, as some, such as cerium, are abundant in mineral deposits and not used widely. Others, like neodymium are widely used in clean energy technologies, but much less abundant. This challenge is often referred to as the rare earth balance problem. The U.S. Department of Energy’s (DOE) Advanced Materials and Manufacturing Technologies Office (AMMTO) and Critical Materials Institute (CMI), an Energy Innovation Hub, are working to address this problem by finding new ways to use cerium that will shore up market demand for an abundant REE and create more value from domestic rare-earth mining operations.
CMI paired cerium with aluminum to create Aluminum Cerium (Al-Ce) alloys with tailored-properties and unlocked an array of new applications for the REE. In 2020, recognizing the achievements of the alloy, the Aluminum Association awarded the official designation of this new class of Al-Ce alloys. This designation allows for the launch of global industrial applications and creates more opportunities for industry to produce the alloys using the designations and enabling CMI commercialization.
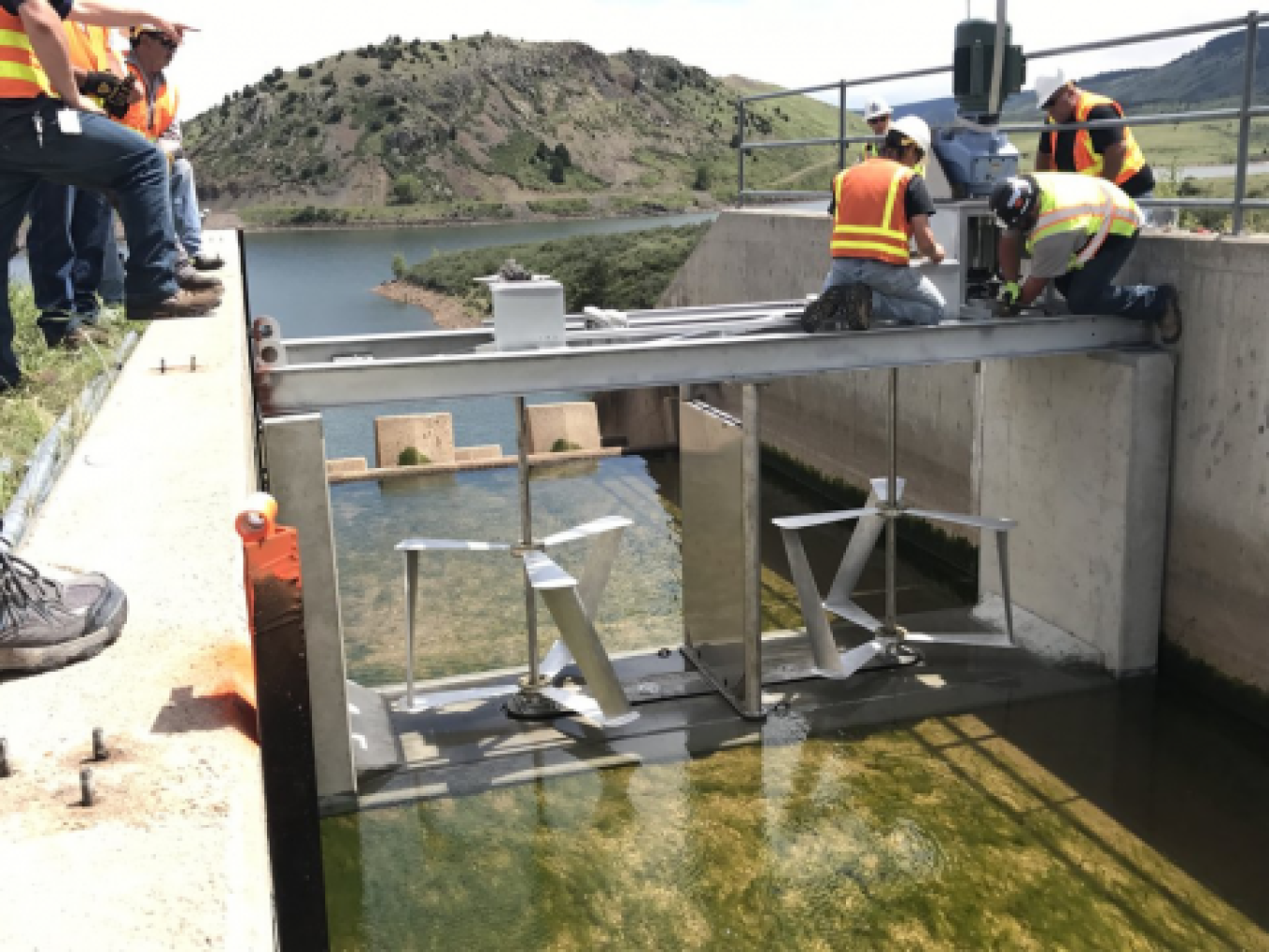
Over time, CMI has added several projects to its portfolio of Al-Ce alloys to boost scale-up, licensing, and commercialization efforts. These projects, supported by AMMTO, bring together the advanced expertise of researchers from CMI, DOE’s National Labs, and universities. The various development projects in CMI and scale-up of processing has received significant support from Eck Industries, an aluminum foundry in Wisconsin who signed an exclusive license with CMI to commercialize the Al-Ce alloys.
Finding uses for cerium supports domestic rare-earth mining operations and provides innovative materials to U.S. manufacturers. The Al-Ce alloys developed by CMI have proven to be adaptable, lightweight, resistant to corrosion, and stable in temperatures up to 500℃. Furthermore, there are reductions in energy and emissions associated with the production of the Al-Ce alloy, because it doesn’t require heat treatment, an energy-intensive process to soften metals and improve formability. So far, the alloy has been used across a diverse range of applications including cylinder heads, turbo chargers, and turbine blades for hydroelectric turbines, pistons, and rotors.
The impacts of the Al-Ce alloy are significant:
- A new market is created for cerium which addresses the rare earth balance problem where economic value is spread over a broader set of REEs beyond just the magnet REE. Increases in market demand then drives production of critical rare earth elements needed for magnets.
- Due to the alloys unique microstructure and resulting properties, Al-Ce alloy can be used to reduce energy use across multiple large-scale transportation applications.
Read more about the projects moving Al-Ce alloys closer to commercialization below:
1. Science-enabling Diverse Value Chain Product from Aluminum-Cerium Alloys
Led by Orlando Rios, University of Tennessee – Knoxville
This project explores the targeting of specific issues that would enable the deployment of a stronger Al-Ce alloy at high temperature, high ductility, and lower cost. The alloy is used in high-performance applications such as pistons, turbochargers, and cylinder heads.
The team used combinatorial sputtering, a process where large numbers of chemically distinct film samples can be made into a single deposition. This discovery allowed the team to create large libraries that expounded, clearly, on classes of alloys that either showed promising leads, or were dead ends. The team was particularly interested in materials with small coefficients of thermal expansion (CTE), as material changes react to temperature by either shrinking or expanding. Two key findings resulted from these efforts: the team found cerium to be an effective alternative to silicon in aluminum casting alloys across foundry manufacturing; and identified large classes of Al-Ce alloys with low CTEs at high operating temperatures. Both findings will help to diversify the REE supply chain and encourage industry adoption of REEs.
Upon successful development, this technology will improve economic competitiveness and provide domestic demand streams for aluminum alloys.
2. Accelerated Alloy Deployment and Rapid Assessment
Led by Ryan Ott, Ames National Laboratory
This project has bold goals: one is to enhance usage of elements that are overly produced, such as cerium, and decrease usage of critical elements, such as neodymium. Another is enabling technologies, such as additive manufacturing for critical materials, to allow the U.S. to be more competitive. The team is also working to accelerate the time frame that materials and technologies are developed, a necessary step to ensure we are able to adapt with ever-changing technologies.
This project works on developing and finding new pathways for materials and manufacturers. These efforts include the development of cost-effective high-performance magnets, and high-temperature Al alloys that use rare earth mining by-products. The team used a process that blended 3D printing, combi-arc melting, and thin film deposition to synthesize alloys over large
3. Al-REE Alloy Development for Advanced Manufacturing (AL-REE ADAM)
Led by Hunter Henderson, Lawrence Livermore National Laboratory (LLNL)
Working to correct the rare earth supply and demand imbalance, this project is looking to develop high volume and high value applications for overproduced cerium. The project features high value-added aluminum-cerium-based alloys, which would open the market to early adopters and diversify future cerium demand.
This project demonstrated metal 3D printing of aluminum rare-earth element (Al REE) alloy forms an internal degradation-resistant nanostructure. It also established the enhanced thermal performance of Al-REE alloys – proving eligibility for high-temperature applications previously unavailable to other Al alloys. This would greatly increase demand for the underutilized REE cerium.
The current alloy used in aerospace and defense components is Al Alloy 2618-T6. The team found the Al-Ce alloy outperformed that alloy, and at a high temperature. This is an exciting development that could garner industrial interest – increasing uses for cerium and diversifying REE supply chain efforts. The team will scale-up for demonstration and continue to improve performance at room temperature strength.
4. Cerium Gettering of Copper and Iron in Aluminum Alloy Recycling
Led by Ryan Ott, Ames National Laboratory
This project is exploring improvement of energy efficiency and economics of aluminum recycling through overly produced rare earth mining by-products, such as cerium. Research has demonstrated that the addition of small amounts of cerium to aluminum has increased alloy tolerances to impurities (copper and iron) and improved overall corrosion resistance. These additions also allow for lower quality aluminum to be used in the production of high-value alloys, reducing the need for both energy and cost intensive high-purity aluminum additions.
Research continues in opportunities that would compound cerium deterioration benefits with the focused addition of aluminum.
***
CMI, an Energy Innovation Hub led by Ames National Laboratory, is funded by DOE’s Advanced Materials and Manufacturing Technologies Office. Since its inception in 2013, CMI research has been awarded 30 U.S. patents, licensed 12 technologies, received five Federal Laboratory Consortium awards and seven R&D 100 Awards. Learn more about CMI.
The Advanced Materials and Manufacturing Technologies Office (AMMTO) supports the advancement of technologies to make the U.S. manufacturing sector more competitive and build a clean, decarbonized economy. AMMTO has three major program teams: next generation materials and processes, secure and sustainable materials, and energy technology manufacturing and workforce. These programs will meet our goals to manufacture clean energy technologies domestically, develop secure and sustainable supply chains, and support a skilled and inclusive manufacturing workforce. Read more about AMMTO..
For more information on rare earth elements, and the rare earth balance problem, view one of AMMTO's three deep-dive assessments which is focused on rare earth magnets. These deep-dive assessments aligned with DOEs roadmap release, “America’s Strategy to Secure the Supply Chain for a Robust Clean Energy Transition,” that outlined how the federal government plans to address the opportunities and challenges around the U.S. domestic supply chain.