At the Department of Energy’s (DOE) Critical Materials Institute (CMI), researchers from Oak Ridge National Laboratory (ORNL) and Idaho National Laboratory (INL) have been working together to develop new, cost-effective technologies for the...
Advanced Materials & Manufacturing Technologies Office
May 27, 2022At the Department of Energy’s (DOE) Critical Materials Institute (CMI), researchers from Oak Ridge National Laboratory (ORNL) and Idaho National Laboratory (INL) have been working together to develop new, cost-effective technologies for the separation of in-demand, rare-earth elements (REEs). The research, supported by DOE’s Advanced Manufacturing Office (AMO), recently moved closer to commercialization through a licensing agreement on the production of CMI’s REE extractants by Marshallton Research Lab, a manufacturer of organic chemicals, for use in a range of industrial applications.
REEs are a series of 17 metallic elements, several of which are critical to the development of high-performance magnets. REEs are naturally mineralized together and require chemical separation for technical application. REEs share similar physical and chemical properties, making them difficult to separate, and current separation techniques are costly and often handled by foreign entities. Global demand for REEs has increased steadily in recent years. However, the lack of domestic, midstream capabilities—the separation of the rare-earth oxides, and the processing of rare earth metals and alloys—is limiting domestic manufacturing growth. All of these factors have created an opportunity to develop cost-effective processes that can extract and separate REEs within the domestic supply chain.
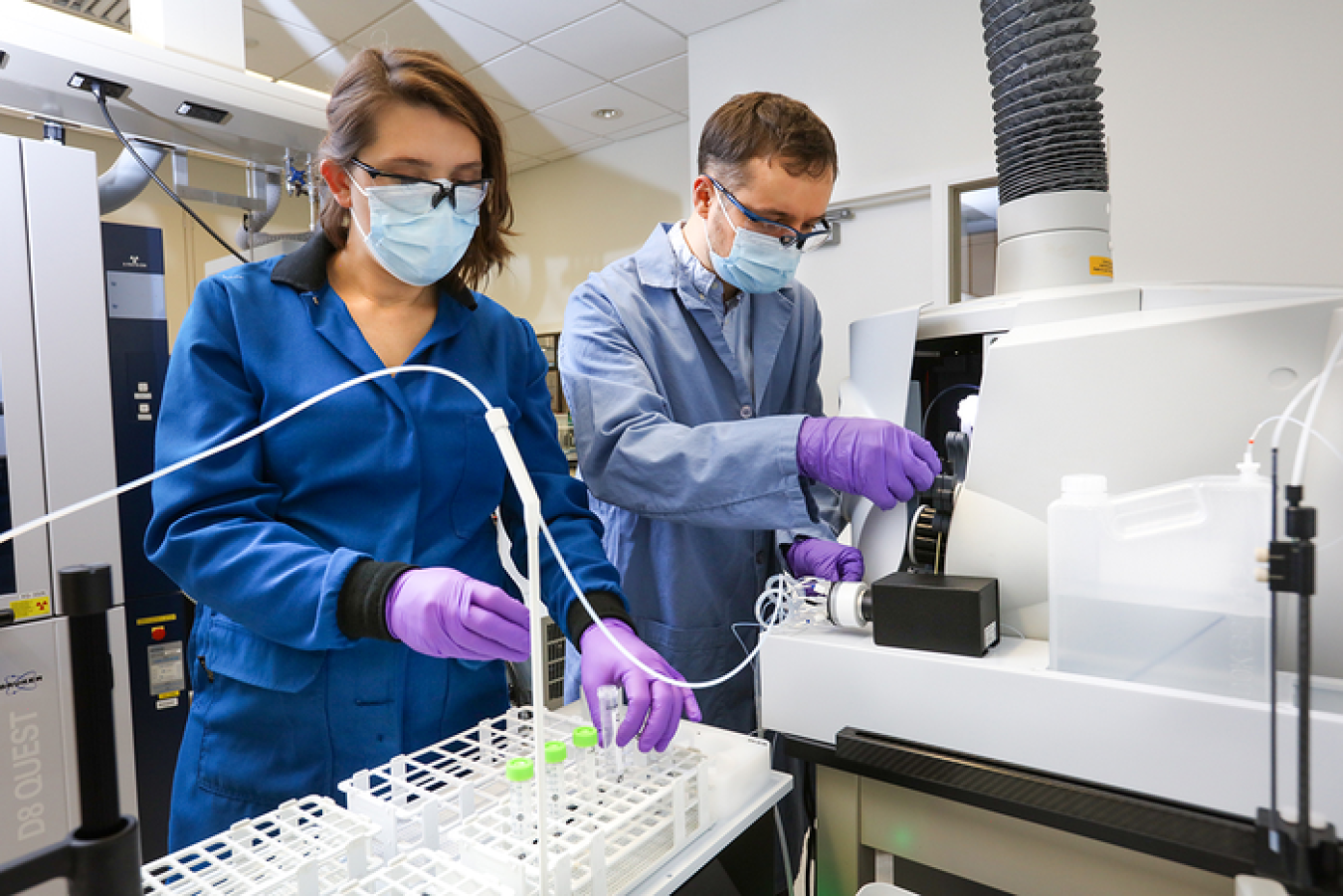
Santa Jansone-Popova, left, and Ilja Popovs quantify rare-earth element concentrations in liquid samples using a spectroscopy instrument. Credit: Genevieve Martin/ORNL, U.S. Dept. of Energy
At CMI, ORNL researchers developed a new extractant for REE separations by making structural changes to diglycolamide (DGA) ligands, organic molecules composed of carbon, hydrogen, oxygen, and nitrogen atoms, through the addition of substituents known as alkyls — fatty organic groups exclusively containing hydrogen and carbon atoms. Recognizing that chemically modifying the structure of DGAs in this manner could improve their properties and their efficiency in extracting REEs, ORNL and INL began testing using this extractant to separate REEs. Through testing, researchers explored ways to reduce complexity and waste, decrease costs, and simplify process sequences to limit the steps needed to achieve separation. ORNL greatly improved the ligands’ selectivity--the degree that a solvent prefers one metal over another: the new ligands had a selectivity of 2.5–3.1.
The process’ successful demonstration and cost-competitiveness relative to existing REE separation techniques attracted the attention of CMI partner Marshallton Research Laboratories, Inc. Marshallton provided feedback to the research team, helping them engineer the new extractant. This resulting REE separation process significantly outperformed current market equivalents. Marshallton became interested in producing the extractants and refined the process to further reduce costs, and they are working now to demonstrate and scale the process. Low-cost domestic separate REE separations would make the magnet supply chain that feeds domestic production of electric vehicle motors and wind turbines more secure and resilient.
CMI, an Energy Innovation Hub led by Ames Laboratory, is funded by DOE’s Advanced Manufacturing Office, and since its inception in 2013, CMI research has been awarded 26 U.S. patents, licensed 10 technologies, has received five Federal Laboratory Consortium awards and six R&D 100 Awards. Learn more about CMI here.