The Office of Fossil Energy (FE) supports research and development of supercritical carbon dioxide (sCO2) power cycles that surpass the performance of advanced, ultra-supercritical steam. Developing highly efficient and lower-cost, indirectly heated sCO2 cycles will provide the technology base for more advanced, directly heated sCO2 cycles for clean fossil energy conversion. In addition, these direct-fired cycles can produce a high-purity stream of carbon dioxide for use/reuse or storage.
FE investments in this technology leverage the world-class capabilities of the DOE National Laboratories and those of private industry to accelerate the delivery of sCO2 power cycle benefits to U.S. industry and the nation.
Applications for Fossil Heat
FE and its individual programs are developing sCO2 cycle components. The objective is to design, build, and operate a 10 MWe pilot plant: the Supercritical Transformational Electric Power (STEP) test facility. This first-of-its-kind facility is being built by the Gas Technology Institute (GTI) in partnership with the Southwest Research Institute (SwRI) and General Electric (GE).
Indirect Fired: Heat from boilers can drive an sCO2 Brayton cycle to generate low-cost power.
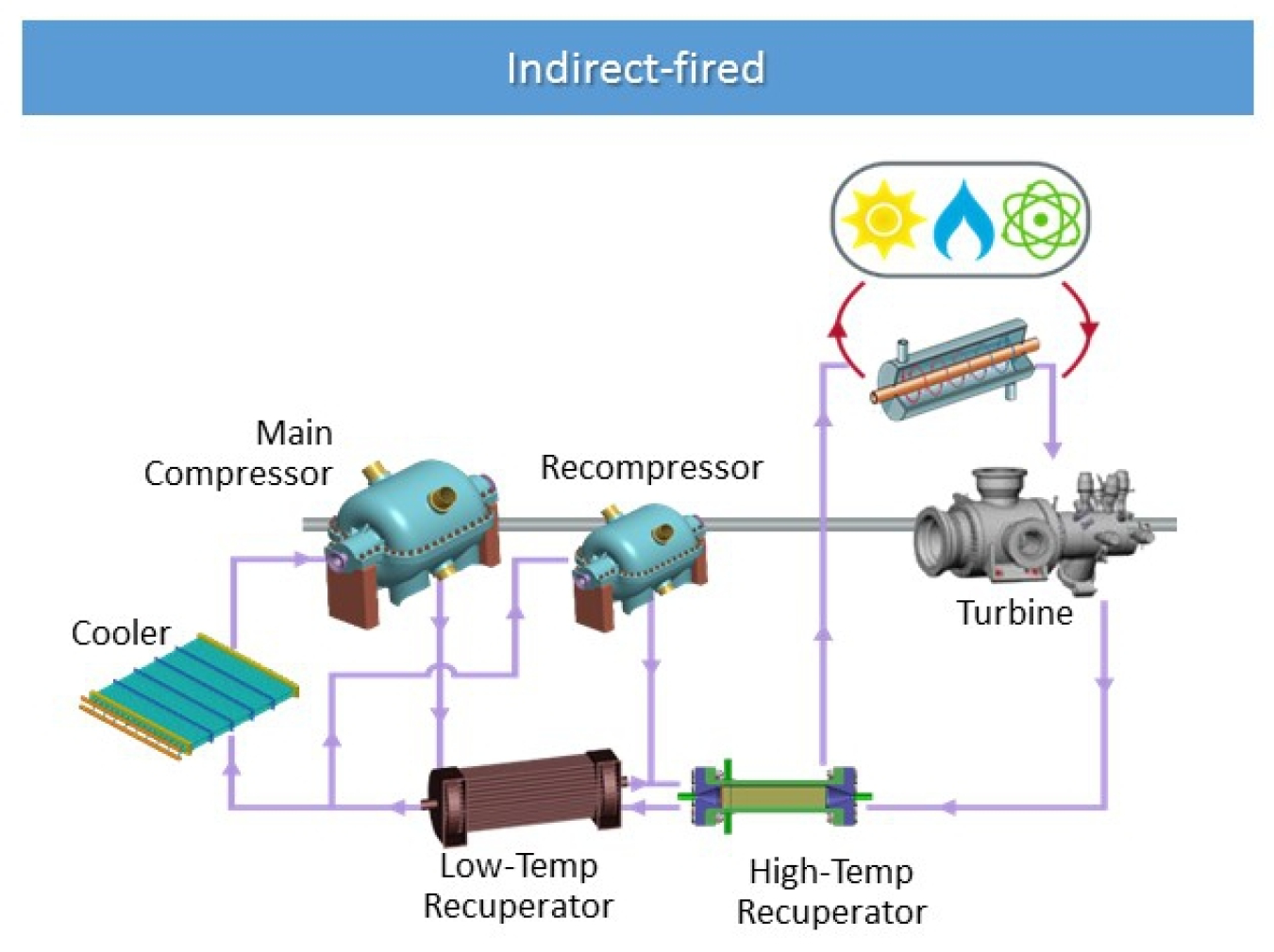
- Applicable to advanced combustion boilers
- >50 cycle efficiency (work out/heat in) possible
- High fluid density, low pressure ratio enable compact turbomachinery
- Ideally suited to constant temperature heat source
- Adaptable for dry cooling
Direct Fired: Directly fired SCO2 cycles combust fossil fuels with oxygen and the resulting steam/CO2 mixture is used to drive the turbine.
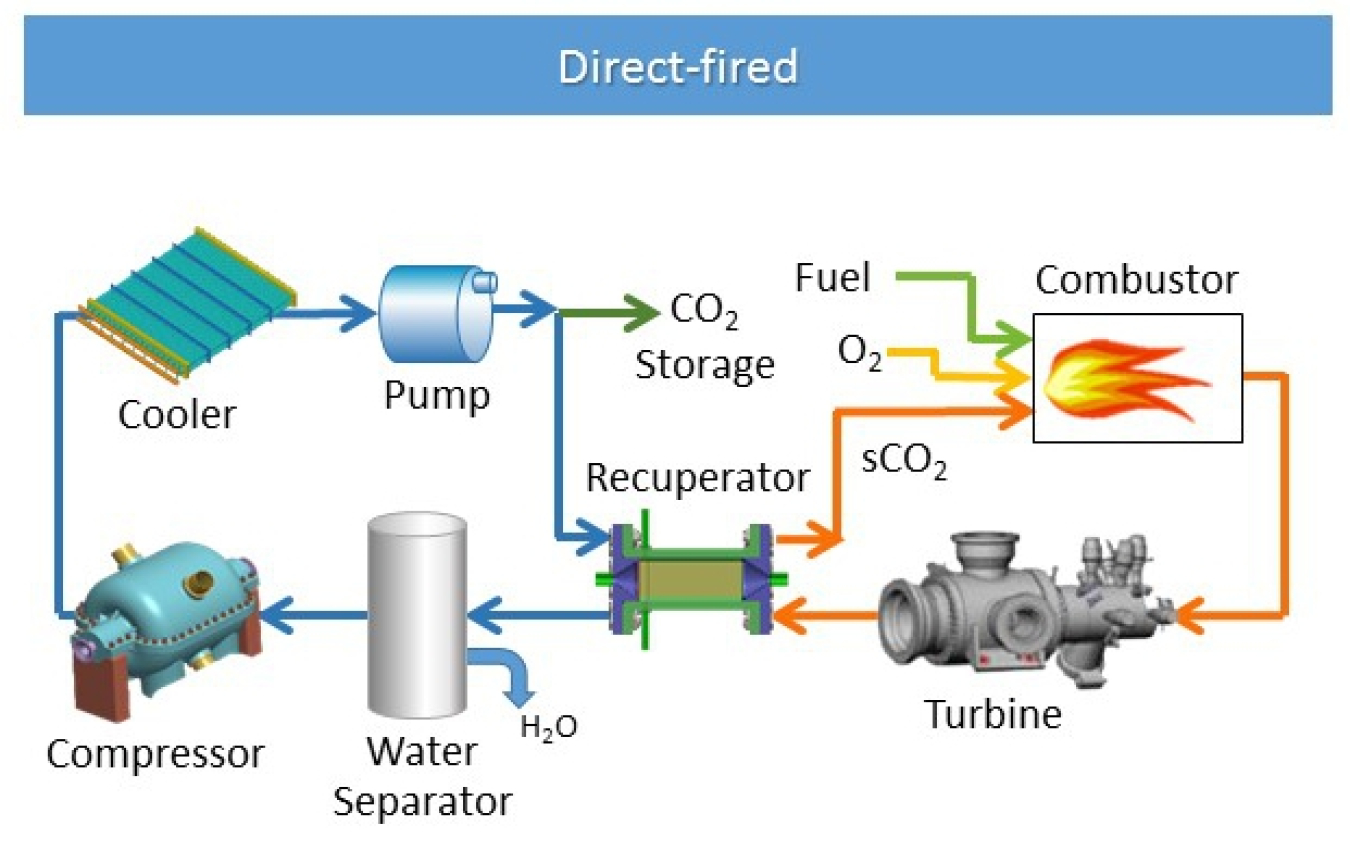
Direct-fired fossil based application cycle
- Application to coal gasification or natural gas
- Fuel flexible: coal syngas and natural gas
- 95% CO2 capture at storage pressure
- Net water producer, if dry-cooled
Benefits
- Intelligent thermodynamics for optimal efficiency.
- Significantly reduced fuel usage.
- Capability for greatly reduced water usage.
- Greatly expanded range of scalability.
- Compact systems that reduce costs and footprint.
- Lower electricity cost for U.S. industries.
Research Priorities
- Demonstrate the operation and performance of a commercial-scale plant.
- Better understand erosion and corrosion mechanisms.
- Develop compatible seals and bearings.
- Develop cost-effective and efficient heat exchangers.
Near-Term Goals
- Develop operational procedures for parallel compression near the CO2 critical point.
- Develop system operational procedures for optimal performance under various conditions.
- Collaborate with industry to develop seals and bearings.
- Collaborate with industry on heat exchanger designs to optimize performance and reduce cost.
- Develop the economic models for these systems.