The amount of salt mined so far in Panel 8 at EM’s Waste Isolation Pilot Plant is a lot, comparable in weight to more than 46,000 Ford F-150s, about 16,000 African bush elephants, nearly 510 Boeing 747s, and two Titanic's.
Office of Environmental Management
June 22, 2021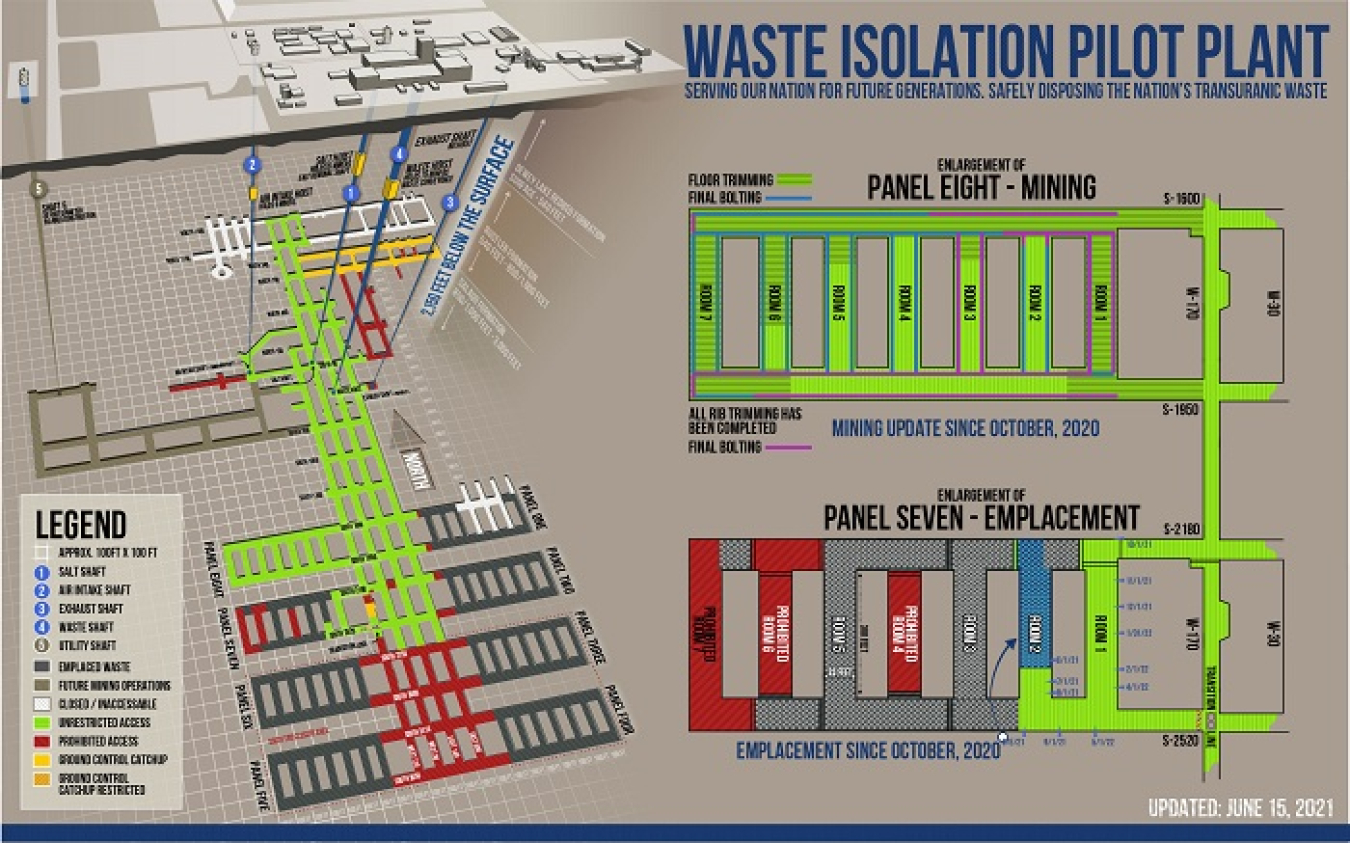
CARLSBAD, N.M. – By any measure, the amount of salt mined so far in Panel 8 at EM’s Waste Isolation Pilot Plant (WIPP) is a lot, comparable in weight to more than 46,000 Ford F-150s, about 16,000 African bush elephants, nearly 510 Boeing 747s, two Titanics, or enough to coat the rims of 3.6 million margarita glasses.
Creating a panel is a process honed by more than 30 years of experience in the underground. Miners working 2,150 feet underground extract salt to create space to emplace defense-related transuranic waste, using machines known as continuous miners to chew through and haul away 8 to 10 tons of rock per minute.
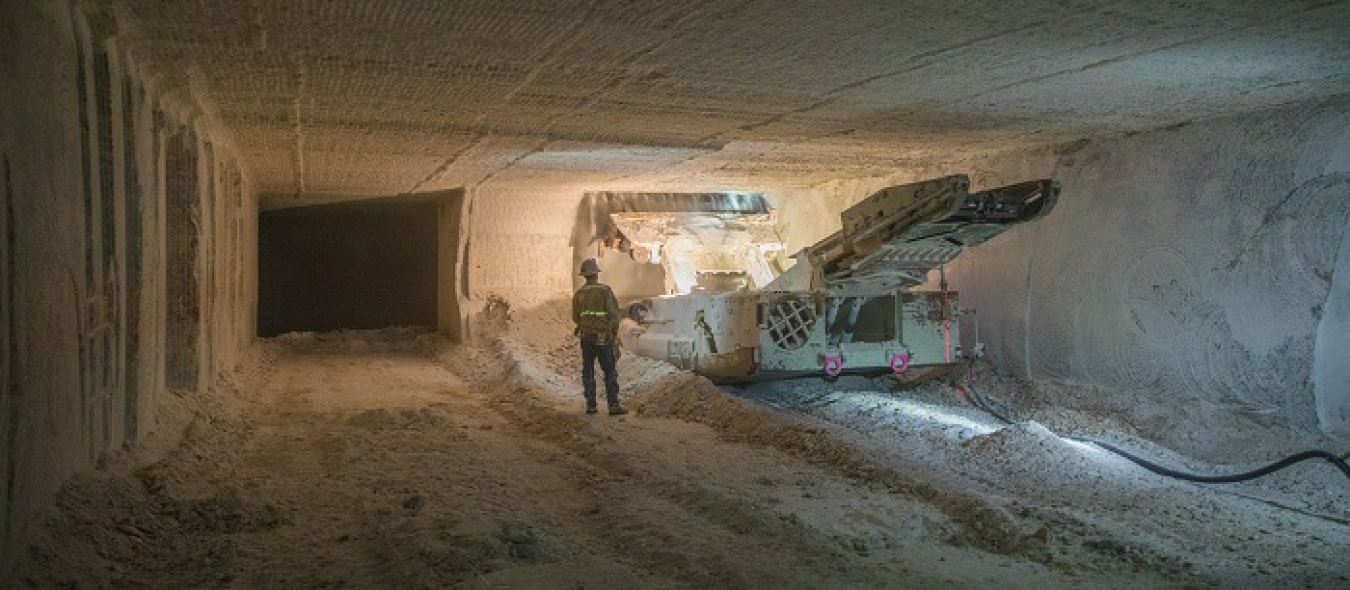
With WIPP’s Panel 8 scheduled for completion in a little over half a year, crews recently crossed the 100,000 tons mined threshold and as of mid-June are at 105,000 tons.
Lowering the floor is the final piece of mining in the panel, which consists of two drifts, or passageways, for air flow with seven rooms between them, making the layout look like a ladder. Each room is 33 feet wide, 16 feet high, and 300 feet long, equivalent to a football field from goal line to goal line.
“It may seem counterintuitive to dig down to get more height, but it’s the way we have traditionally created the panels,” WIPP mining manager David Sjomeling said.
WIPP practices “just in time” mining; Panel 8 will be ready about two months before Panel 7 is filled and sealed. It’s planned that way because salt “creeps,” or moves, 2 to 4 inches per year and begins to close the excavated space.
Panel 7 has 1.5 rooms remaining to be filled. Once Panel 7 is full, scheduled for around May 2022, bulkheads will seal the panel and waste emplacement will move to Panel 8.
Using laser devices for precise measurements, crews use a continuous miner machine to cut 8 to 10 tons of salt per minute, which is taken away by haul trucks to the salt hoist’s collector, known as a grizzly. From there, salt is carried to the surface to waiting 40-ton haul trucks that deposit the salt to the north of the site.
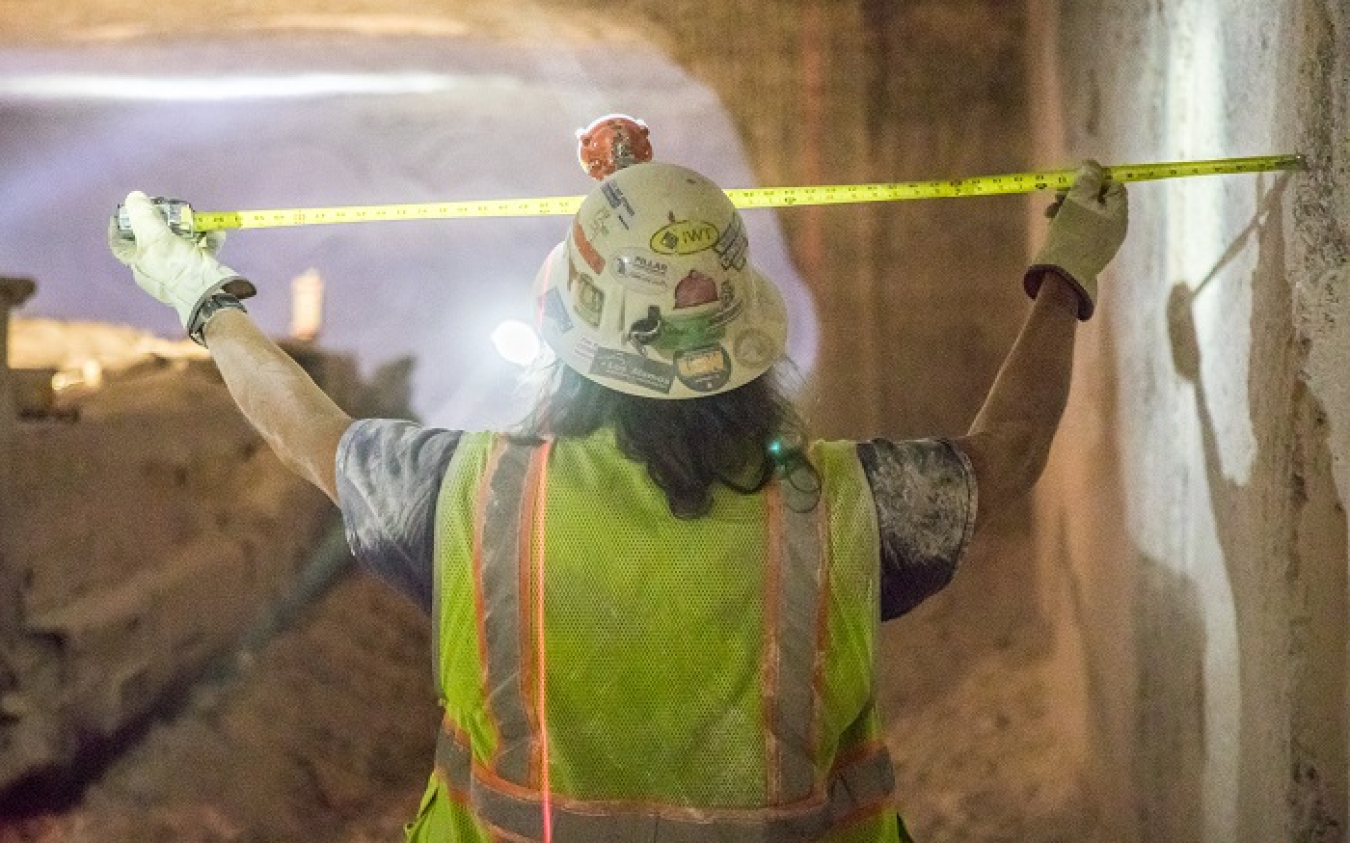
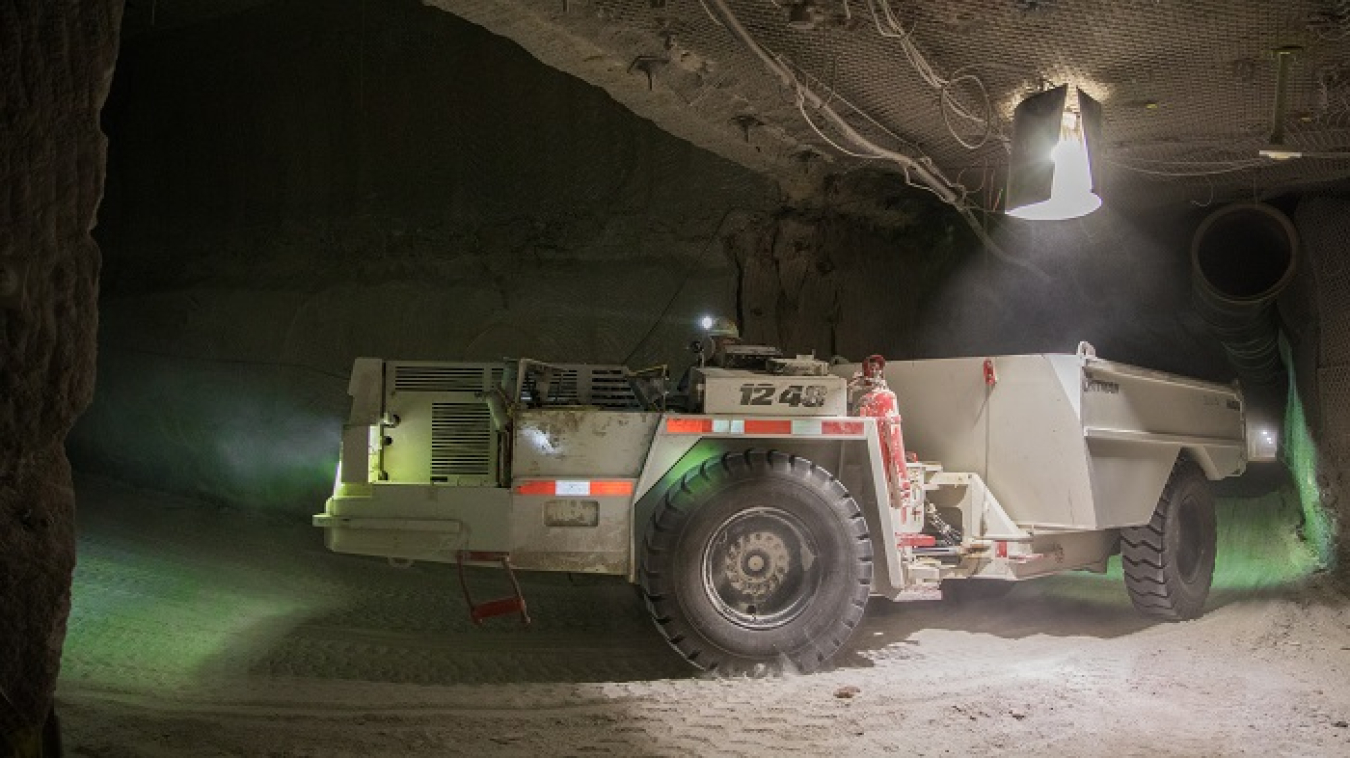
The “rough cut” that creates the panel’s outline is followed by the first round of bolting to stabilize salt movement, then the ribs, or walls, are cut to their final dimensions.
The rough cut’s first pass is limited to about 9 feet by the reach of the miner’s rotating cutting head. The second finishing pass cuts from the floor, taking the floor-to-ceiling, or back, height from 9 to 16 feet.
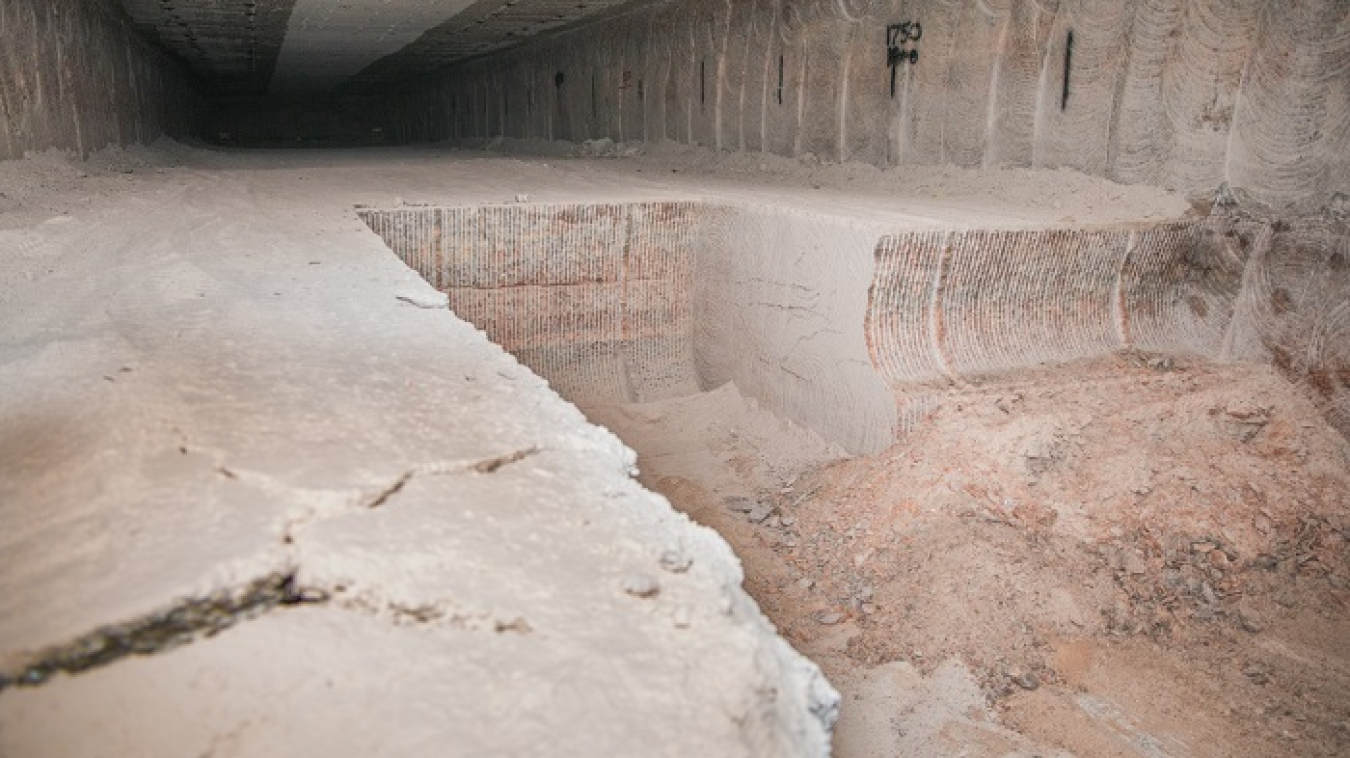
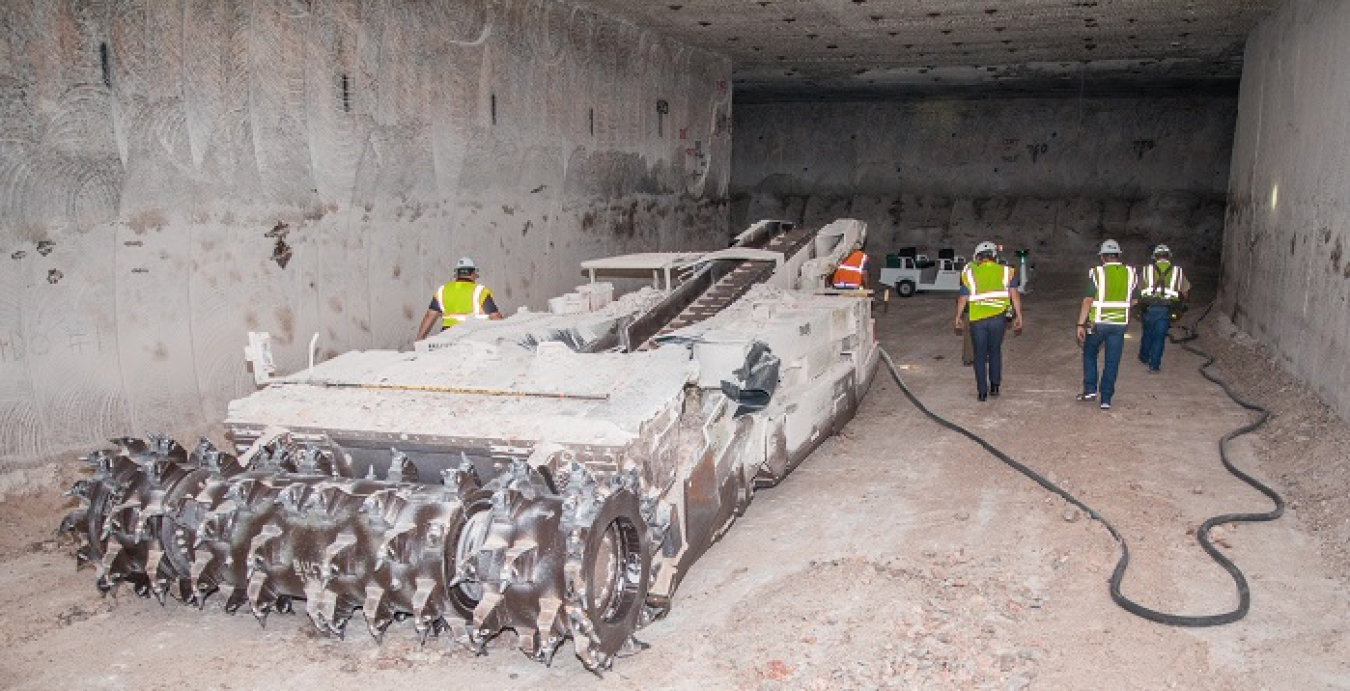
Floor mining is set to be finished in August. After that, the panel will be outfitted with power, lights, continuous air monitors, volatile organic compound monitors, mine phones, and bulkheads, which control airflow. That work is tentatively slated to be done by February.
To receive the latest news and updates about the Office of Environmental Management, submit your e-mail address.