Project Name: Integrated Thermal Energy Storage Heat Exchanger for Concentrating Solar Power Applications
Funding Opportunity: Generation 3 Concentrating Solar Power Systems
SETO Subprogram: Concentrating Solar Power
Location: Hampton, NH
SETO Award Amount: $1,178,556
Awardee Cost Share: $295,523
Principal Investigator: Jim Nash
This project team will develop a heat exchanger that uses a composite phase-changing material to store and release heat from a concentrating solar-thermal power (CSP) receiver to a supercritical carbon dioxide (sCO2) power-conversion cycle. The team will design a new heat exchanger and test the durability of its components by exposing them to high pressures and temperatures, helping to optimize the heat exchanger and create a scalable design for sCO2 CSP plants. This project, performing component-level research and development for a CSP system, is responsive to Topic 2b of the Generation 3 CSP funding program and could be integrated into Topic 1 system projects.
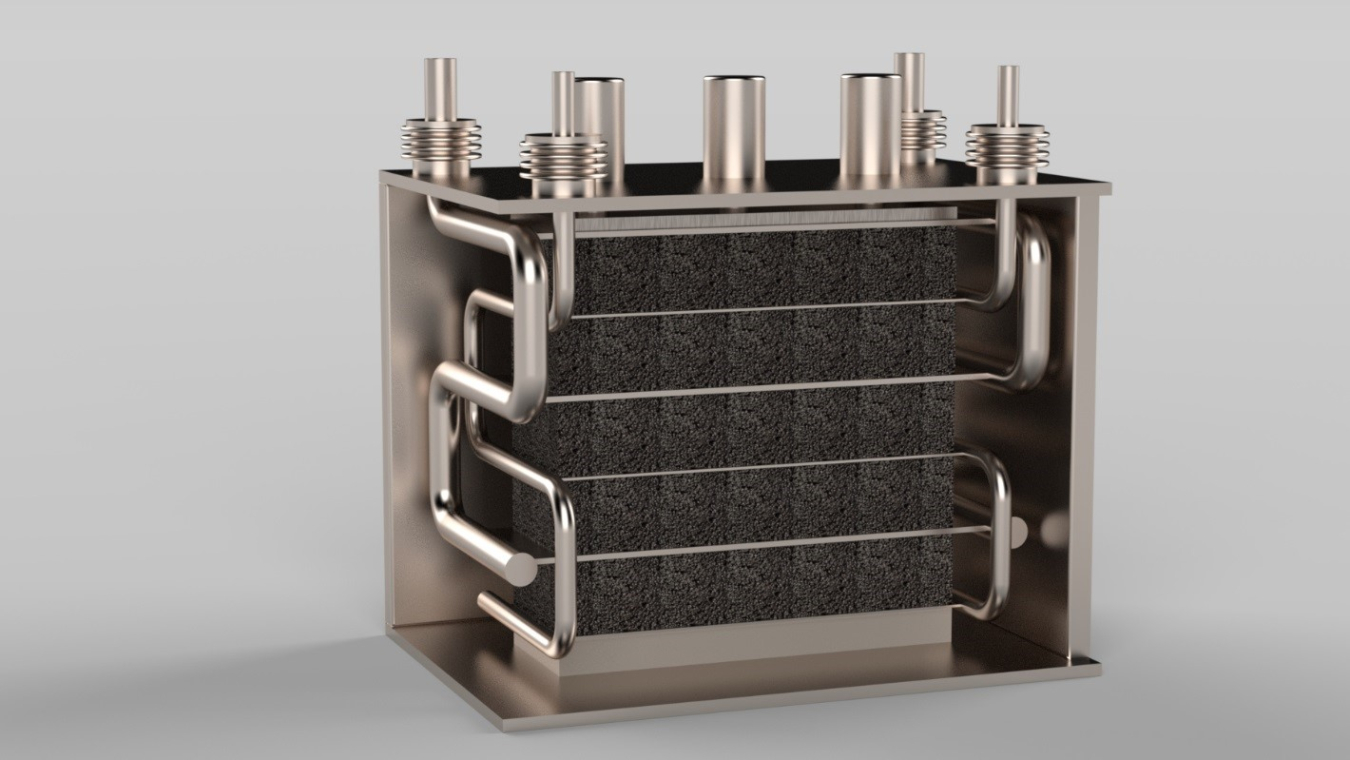
A rendering of Brayton Energy’s proposed thermal energy storage heat exchanger that uses a graphite foam and magnesium chloride phase-change composite material developed by Argonne National Laboratory. Image courtesy of Brayton Energy.
APPROACH
The team aims to develop a heat exchanger that transports a high-temperature, high-pressure fluid that can withstand more than 700° Celsius in a sCO2 CSP plant. The heat exchanger design is based on a composite phase-changing material—chloride salt encapsulated in graphite foam—that has both high-capacity latent heat storage and heat-transfer properties, which will minimize temperature drops during the heat transfer process. The team will test the heat exchanger by creating pressure at the point of contact between the metal and the salt composites, making sure the amount of heat transferred remains consistent. This will help to determine how much pressure is needed to optimize the movement of heat between the metal and the composite.
INNOVATIONS
Integrating heat exchangers with phase-change thermal energy storage systems while also achieving effective heat transfer is a challenge. This heat exchanger design will use materials that minimize temperature drops during the heat transfer process. The uniform heat transfer will maintain the performance of the heat exchanger, preventing damage from too much heat. The pressure testing will help optimize the heat exchanger’s performance by confirming the durability of its components, which will increase system efficiency.