Hubbell Lighting is a major manufacturer of LED and conventional luminaires and control solutions, and is one of the three largest lighting manufacturers based in the U.S.
April 19, 2017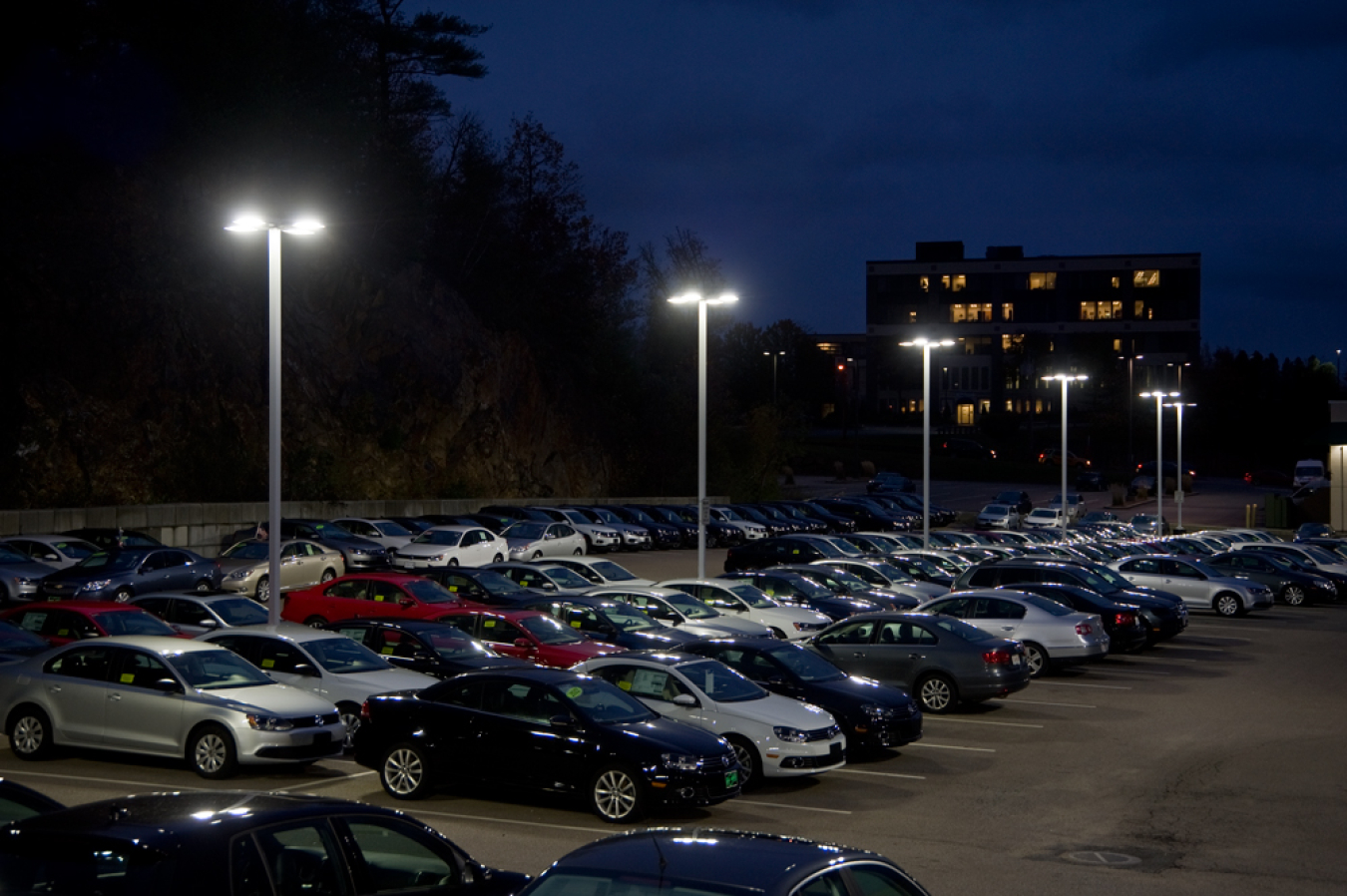
“Beacon Products Viper with Beaconnect” : The Viper is an area/roadway luminaire with Beaconnect wireless control system integrated into the fixture. It operates autonomously once programmed, has a real-time clock with battery backup for independent operation or functions as a mesh system when needed. Image courtesy of Hubbell Lighting.
Originally published via the Solid State Lighting weekly Postings.
Although we don’t often hear about growth in U.S. manufacturing, the solid-state lighting industry has been steadily growing and establishing a manufacturing presence here at home, strengthening our country’s position as a leader in the technology. Solid-state lighting was not only born of U.S. ingenuity and R&D, but is also riding the crest of a worldwide trend toward greater energy efficiency. This presents a golden opportunity for U.S. companies to play an increased role in SSL manufacturing. From time to time, the Postings focus on SSL companies that manufacture here in the U.S. This is not intended to endorse or promote any of the companies, but rather to motivate and inspire other U.S. companies to follow suit. The philosophy and activities you’ll read about here are consistent with the recommendations set forth in the U.S. Department of Energy (DOE) white paper “Prospects for U.S.-Based Manufacturing in the SSL Industry.”
Hubbell Lighting and Control Solutions
Headquartered in Greenville, South Carolina, where more than 500 employees are based, Hubbell Lighting is a major manufacturer of LED and conventional luminaires and control solutions, and is one of the three largest lighting manufacturers based in the U.S. The company features a portfolio of brands that offer lighting and control solutions for virtually every application.
According to Director of Innovation and Technology Warren Weeks, Hubbell’s SSL revolution started in 2008. Prior to that, the company made virtually no LED lighting products, whereas today more than two-thirds of its commercial and industrial lighting is LED. Overall, about 55% of Hubbell’s products are LED, and the growth in LED products is expected to continue. Virtually all of Hubbell’s R&D efforts, Warren says, are focused on SSL, which the company considers to be the future of lighting.
With the introduction of LED lighting, Hubbell has evolved from an electrical lighting manufacturer to an electronics manufacturer. It now designs its own printed circuit boards, populates the printed circuit board assemblies, makes proprietary and interoperable controls technology, and writes its own firmware and software.
Founded in 1963, Hubbell Lighting has deep roots and historical expertise as an electrical manufacturer that used mechanical engineers to do most of its luminaire design. Warren notes that before SSL, lamps and ballasts were provided by a different set of manufacturers, so luminaire design and manufacturing mainly involved mechanical effort. Now, with the rapid adoption of solid-state lighting, Hubbell has transitioned to become an electronics manufacturer and features a workforce of skilled electronics engineers designing LED circuits, drivers, sensors, and controls systems in order to make the entire, integrated luminaire. The company has significantly changed its approach to the design of manufacturing, product testing, reliability testing, and quality systems, in response to SSL technology.
As might be expected, Hubbell has thousands of suppliers all over the world. Warren explains that the vast preponderance of its SSL luminaires and safety lighting – including the electrical circuits, LED boards, and optical solutions – are designed in the U.S. Electrical components are assembled in Hubbell-owned factories both here and abroad, depending on volume and complexity. Custom optics are designed and manufactured by key domestic suppliers, and SSL luminaires are manufactured and assembled in Hubbell facilities across the U.S., in locations that include Hudson, Wisconsin; Bristol, Pennsylvania; Christiansburg, Virginia; El Dorado, Arkansas; Elgin, Illinois; and Plympton, Massachusetts.
Warren says Hubbell is keeping a watchful eye on the cost-effective supply chain. With a healthy amount of domestic manufacturing (depending on product mix), the company’s overarching strategy is to be mindful of product complexity and mix without losing sight of what’s important to the customer. This is driven by the need to keep manufacturing nimble, so that Hubbell can react to customer demands quickly.
As the company has evolved in response to the transformative impact of SSL, the skill sets required of employees have evolved as well, and the recent shift has been dramatic. Besides the obvious transition to needing more electronics engineers, Hubbell now employs software engineers who design graphical user interfaces and apps for connected lighting systems. The engineers in the company’s factories need to understand such things as surface-mount-technology pick-and-place equipment, reflow ovens, coating systems, and inline electrical testing equipment.
As Warren notes, R&D is the foremost tool in Hubbell’s arsenal to prepare the company for changing markets, and its R&D labs in Greenville are the nerve center of this effort, which focuses on bringing new and better products to market quickly and efficiently to take advantage of new markets such as connected lighting, human-centric lighting, color-tunable products, and horticultural lighting. General lighting and safety lighting in commercial, industrial, indoor, outdoor, and residential markets remain a key focus.
As the lighting market shifts to SSL technology, Hubbell is one of many companies that are helping to reinforce U.S. manufacturing and R&D leadership This will not only help bring significant energy savings through more-efficient lighting products, but will benefit our economy by adding jobs at multiple levels of the supply chain.