Among Wisconsin’s economic sectors, the industrial sector represents the highest level of energy consumption. In 2007, this sector consumed approximately 623.5 trillion British thermal units (Btu). Wisconsin’s industrial sector includes energy-intensive industries, such as food processing, chemical manufacturing, plastics, and forest products. The Wisconsin Office of Energy Independence, along with its project partners, expanded the Wisconsin Save Energy Now (WisconSEN) Program that was established in October 2007 as part of a memorandum of understanding with the U.S. Department of Energy’s (DOE’s) Advanced Manufacturing Office (AMO; formerly the Industrial Technologies Program).
The program was funded as one of 23 state and 5 regional grants awarded by AMO in 2009. It informed industrial facilities about AMO’s Save Energy Now industrial energy efficiency resources and the goal of reducing industrial energy intensity in the state by 2.5% each year. To meet this objective, the project provided industrial companies with Energy Saving Assessments (ESA) and follow-up implementation assistance, as well as training, outreach and marketing services, and demonstrations of new and emerging technologies. In addition, a Superior Energy Performance (SEP) standard pilot program for plant certification was conducted. SEP is a national program designed to increase energy efficiency in the American manufacturing industry.
Through a partnership with local programs that provided project implementation support, participating customers completed energy-savings projects to reduce industrial energy intensity in Wisconsin. This project enhanced the state’s industrial energy efficiency programs and expanded the overall reach of these programs.
Purpose
The goal of WisconSEN was to build on efforts started in 2007 by Wisconsin Focus on Energy, which engaged the state’s industrial companies in an effort to overcome awareness, informational, time, technical, and financial risk barriers that prevent energy efficiency improvement. Wisconsin has previously been a leader in offering DOE trainings, and having done so, was well prepared to use the funding period to expand previous efforts. These efforts involved holding trainings on new technologies, common energy-saving measures, and certifying new DOE Qualified Specialists.
WisconSEN also recognized the crucial link between jobs and energy efficiency, and thus used the program as a chance to create and preserve energy jobs within the state that will last beyond the funding period.
Accomplishments
During the project period, Focus on Energy performed a total of 76 ESAs (27 in Phase I and 49 in Phase II). These facilities included paper and pulp mills, food processors, plastics manufacturers, metal casters, and other consumer goods manufacturers.
An example of these assessments included an audit of the supply, distribution, and demand of the compressed air systems in the assembly lines of a large food manufacturer in Wisconsin. This audit resulted in a retrofit recommendation that will reduce the plant’s electrical consumption by 28%. Once the retrofit is fully implemented, the savings will fund the project with a 7.6-month simple payback period and reduce the existing annual operating cost of the compressed air system by $53,412.
In addition, WPPI Energy power company conducted energy assessments for 43 (15 Phase I and 28 Phase II) small and medium industrial customers and 6 energy saving assessments (3 Phase I and 3 Phase II) for large industrial customers.
An example of these assessments included a refrigeration head pressure adjustment made at a food processing facility that resulted in $39,000 annual energy savings. Temperature setpoints or compressed air setpoints were often adjusted without documenting the savings achieved.
Based on the tracking of energy savings, more than 9.4 million kilowatt hours (kWh) have been saved from measures that were implemented. An additional 6.0 million kWh of savings are still being considered by assessment recipients.
In Phase I, six DOE Best Practice training events were completed, including an AIRMaster (Level III), Steam System Assessment, Process Heating Assessment, Motor System Management, Fan System Assessment, and Pump System Assessment. In Phase II, three Process Heating Assessment trainings were completed, with two focusing on heat treating. These events averaged 22 participants per training.
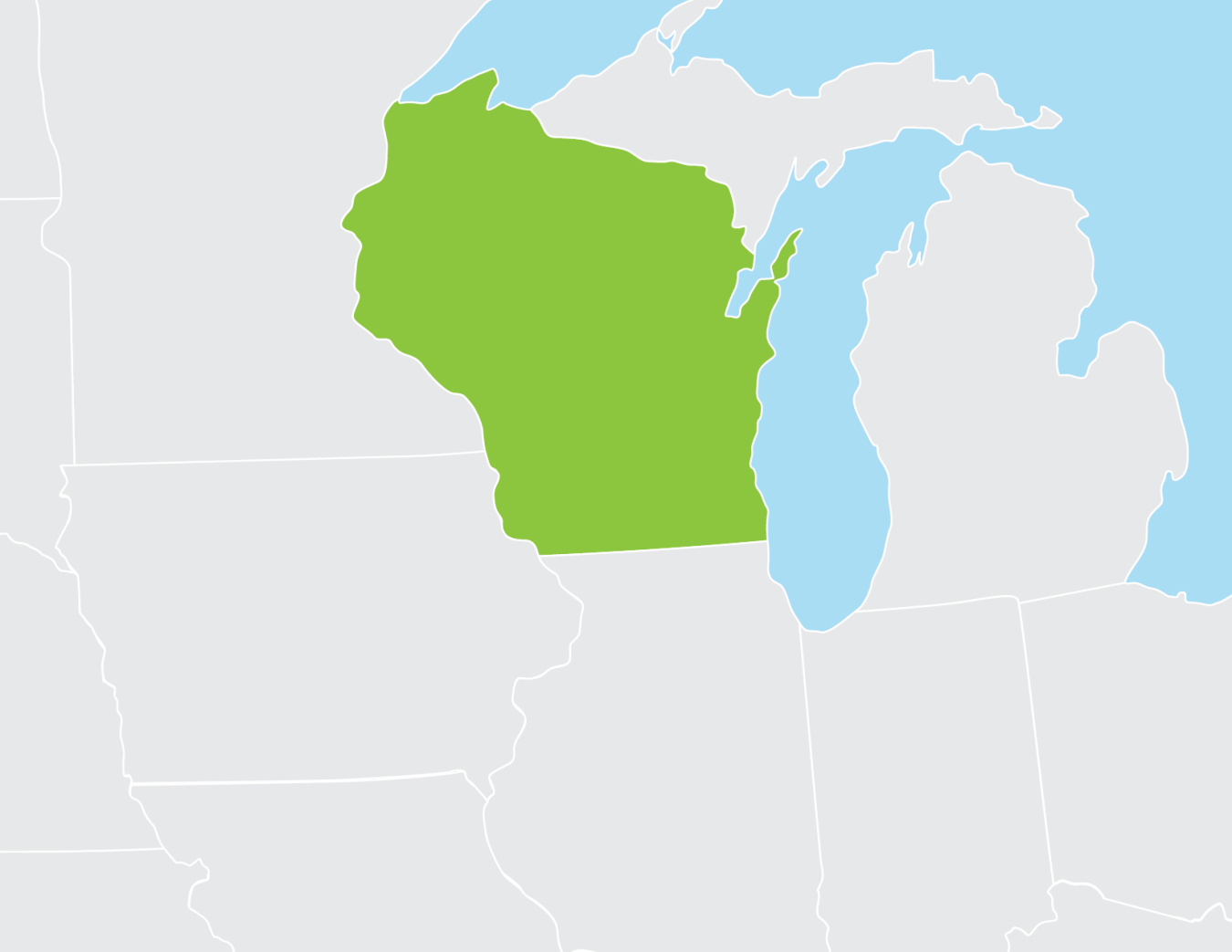
The Wisconsin Save Energy Now Program is focused on reducing industrial energy intensity in the state by performing assessments, holding trainings, and piloting ISO 50001 locally.
PROJECT MISSION
To continue to inform industrial facilities about AMO’s industrial energy efficiency resources and the goal of reducing industrial energy intensity in the state by 2.5% each year.
PROJECT FUNDING
- Funding source: American Recovery and Reinvestment Act (ARRA) U.S. Department of Energy, Advanced Manufacturing Office
- Amount: $348,662 $545,000
- Project period: 9/30/2009 to 6/30/2011 5/1/2011 to 12/31/2013
PROJECT BENEFITS
- Projected savings of 16 trillion Btu annually over the three-year project period, totaling up to 48 trillion Btu.
- Increased technical and financial energy efficiency assistance available to Wisconsin’s 12,000 industrial companies.
- Increased energy efficiency educational opportunities through training sessions and outreach services.
PRIMARY INVESTIGATORS
Wisconsin State Energy Office, Madison, Wisconsin
PROJECT AWARD PARTNERS
- Focus on Energy, Madison, Wisconsin
- Science Applications International Corporation, Oak Ridge, Tennessee
- Wisconsin Industrial Energy Group, Madison, Wisconsin
- WPPI Energy, Sun Prairie, Wisconsin
CONTACTS
Megan Levy
Wisconsin State Energy Office
201 W. Washington Ave.
Madison, WI 53703
Phone: 608-266-5054
Email: megan.levy@wisconsin.gov
Jamey Evans
U.S. Department of Energy
Advanced Manufacturing Office
Phone: 720-356-1536
Email: jamey.evans@go.doe.gov
Sandy Glatt
U.S. Department of Energy
Advanced Manufacturing Office
Phone: 720-356-1544
Email: sandy.glatt@go.doe.gov
Last Updated: January 2015
Three companies initially expressed an interest in becoming ISO 50001 certified; therefore, the project partners provided support and coaching to these companies within this process. Ultimately, the mentoring and training was completed for two of the companies.
Program Highlights
Program Activity | Number Completed |
---|---|
Energy Savings Assessments | 125 |
Trainings | 6 |
ISO 50001 Pilot | 2 |
Technology Demonstrations | 3 |