Small modular reactors are setting a new standard for safety in the nuclear industry.
September 2, 2020Absolutely nothing!
Small modular reactors, or SMRs, are setting a new standard for safety in the industry.
NuScale Power is moving through the U.S. Nuclear Regulatory Commission's (NRC) review process and is on pace to deliver America’s first SMR in 2029.
Its unique design allows the reactor to passively cool itself without any need for additional water, power or even operator action.
So why are these small advanced reactors so different?
In NuScale's case, it all comes down to simpler design choices, natural water flow and passive safety features.
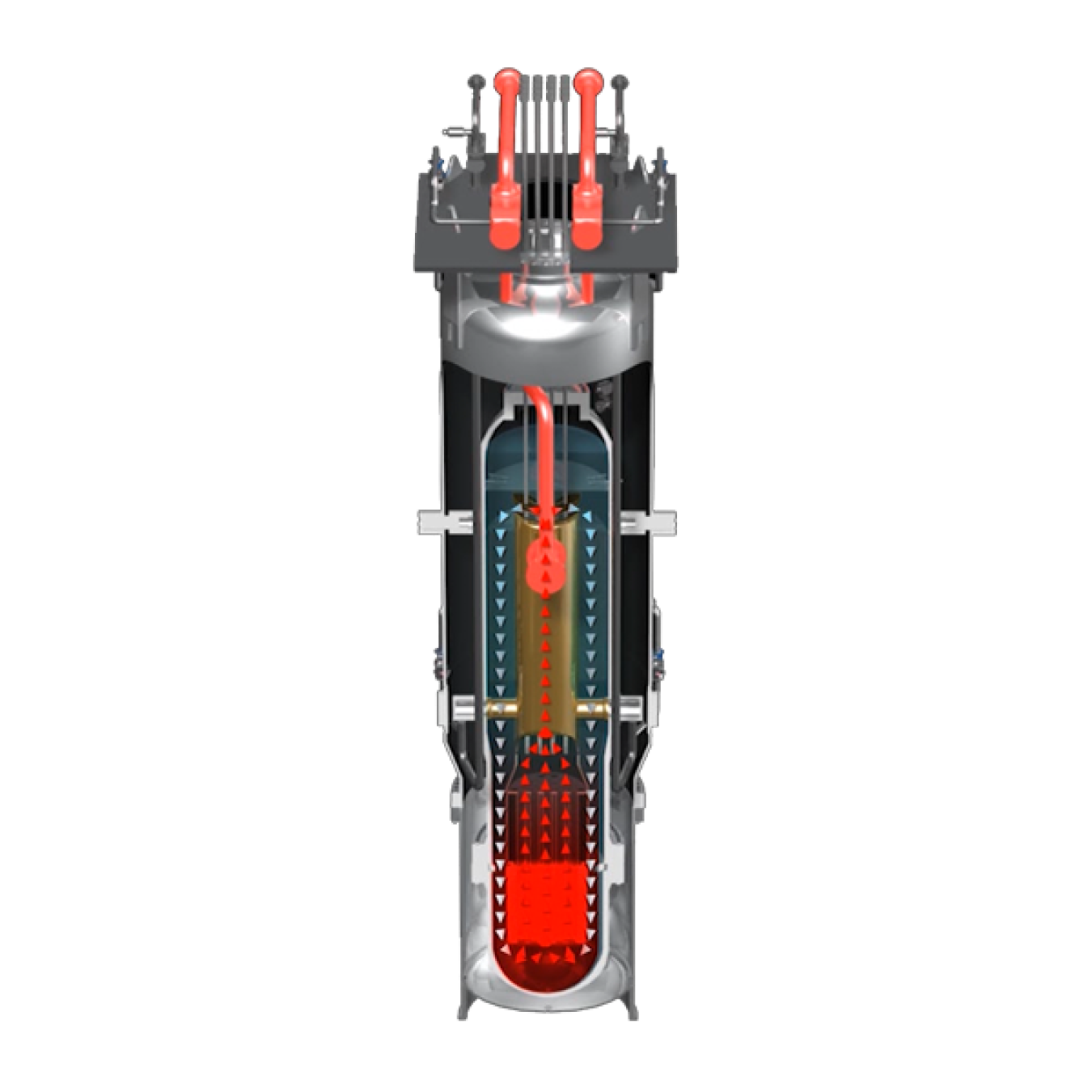
Enhanced Safety
NuScale’s design uses natural water circulation to passively cool its reactor.
The core is housed in a pressurized steel reactor vessel that is located within a steel containment vessel (kind of like a thermos bottle). Each module is submerged in water to help divert heat away from the reactor during off-normal conditions.
If emergency cooling is needed, specialized valves open automatically—allowing steam to discharge from the reactor vessel into the containment vessel. The steam then condenses and water flows back into the core through a second set of valves at the bottom of the reactor vessel. This helps cool the reactor down.
As the water boils, the steam that is created recirculates, setting up a passive safety cooling process that continues until the heat and pressure eventually stabilize.
Take a look:
Simple is Safe
NuScale’s specialized valves are part of an emergency core cooling (ECC) system that is fundamentally less complex than traditional reactor designs.
With fewer parts needed to accomplish the same safety function, the company’s simplified design allows the valves to open automatically without the need for additional pumps, power or operator action.
This leads to greater reliability of the safety system and lower capital costs when building the reactor.
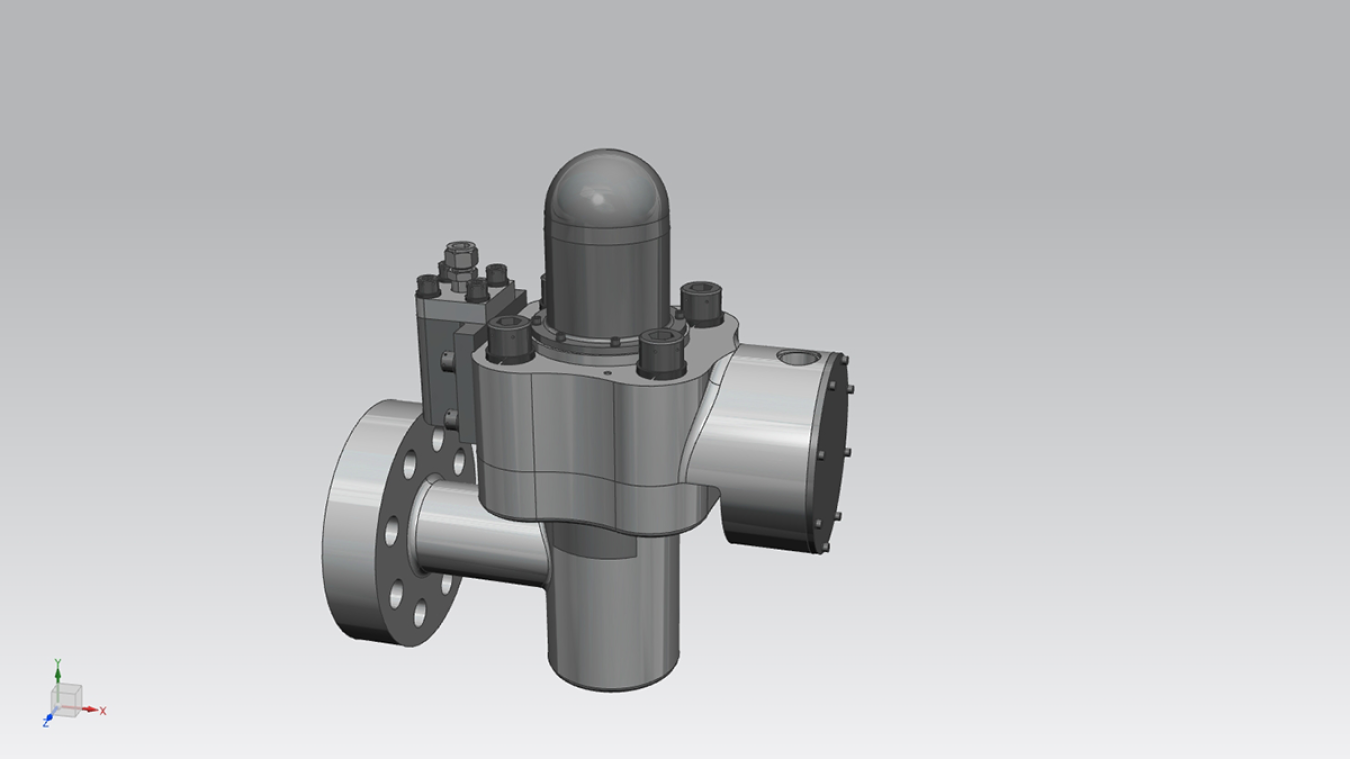
Built in the USA
NuScale selected an American supply chain to build a prototype of these valves for its ECC system.
Illinois-based Scot Forge Company will manufacture the forgings for many of the critical valve components. The forgings will then be machined, assembled, and tested in New York by Curtiss-Wright, Target Rock Division, the company which designed the valve for NuScale.
The theme here is American.
NuScale is looking domestically to identify U.S. suppliers to build its first SMR.
The Oregon-based company expects to have more than 90% of its supply chain made up of American materials and companies.
They recently brought BWX Technologies in Virginia on board to start the engineering work to manufacture the SMR. BWXT will also be responsible for integrating all of the different parts, including the ECC valves, into the manufacturing process.
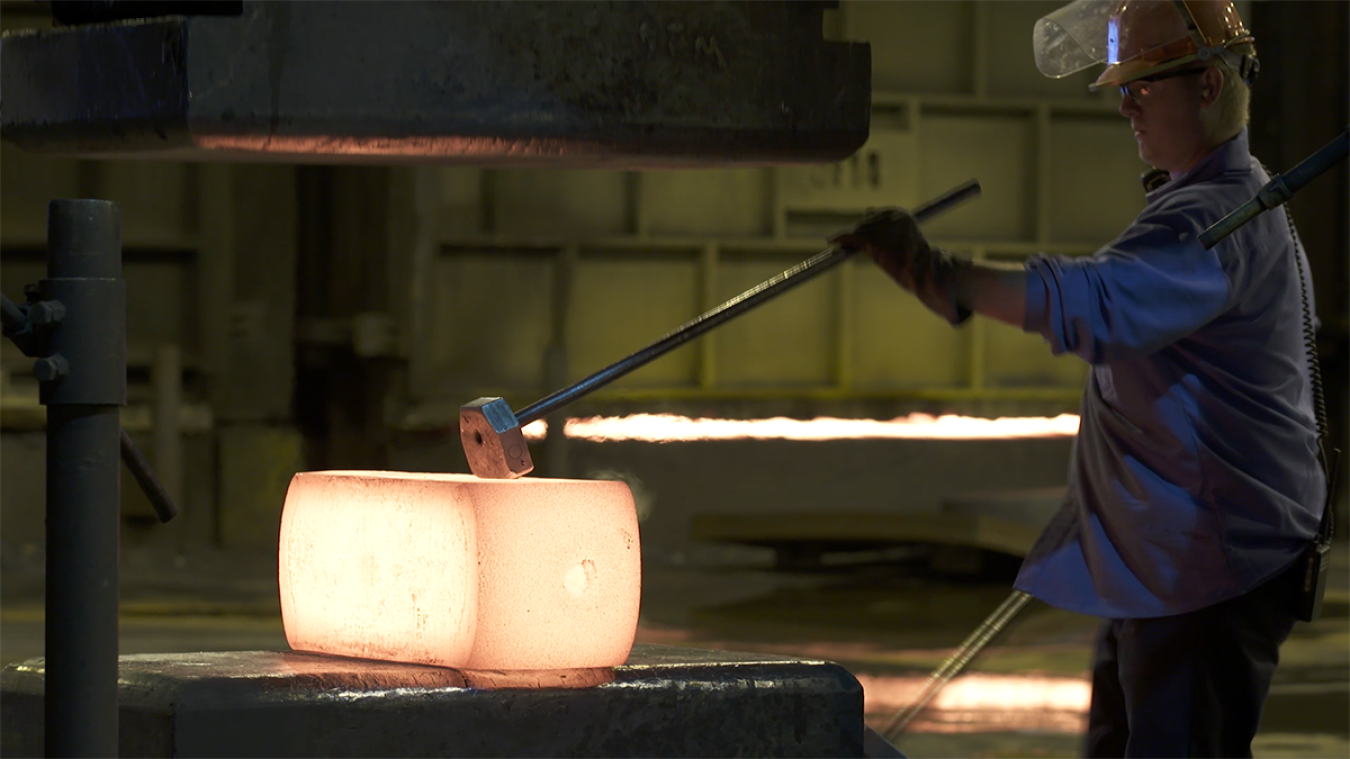
What’s Next?
The NRC recently issued its final safety evaluation report on NuScale's SMR design. The accomplishment is the first of its kind for a SMR and puts NuScale on track to receive a full design certification from the regulator by August 2021.
DOE has invested more than $400 million since 2014 to accelerate the development and deployment of SMRs.
Learn more about our work in this area.