We interviewed LM Director Carmelo Melendez about the unprecedented response to the COVID-19 pandemic.
May 22, 2020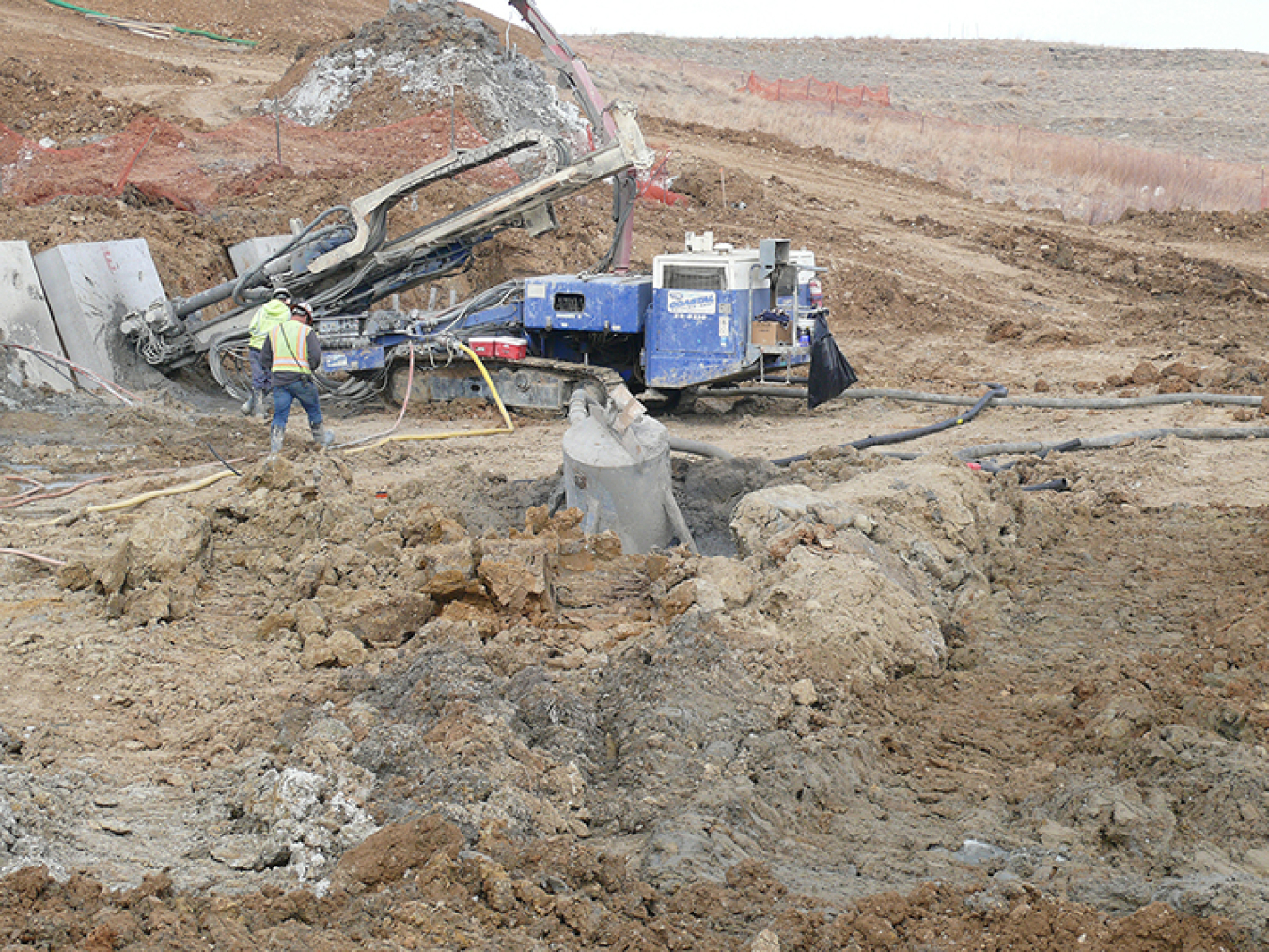
At the Original Landfill stabilization project at Rocky Flats Site, Colorado, subcontractors drill into bedrock through the center of a concrete block placed on the landfill’s west side, preparing to install a stabilization anchor.
We interviewed U.S. Department of Energy (DOE) Office of Legacy Management (LM) Director Carmelo Melendez about the unprecedented response to the COVID-19 pandemic. He explained how the organization transitioned from a field-centric organization, with sites and offices spread across the country, to one primarily defined by teleworking, all while ensuring that sites remain protective of people and the environment.
Q: Did you have any pandemic plans ready that could be used immediately when the COVID-19 pandemic started?
CM: No, we didn’t have any specific pandemic plans ready, but we had a Continuity of Operations plan, which we adapted as a guide on how to proceed. Our emergency operations plans had cursory information about pandemics and were a starting point in LM preparation. LM patterned most of our pandemic planning on the plan that DOE headquarters developed, which wasn’t completed until mid-to-late March. The plans had to be revised to meet the needs of our organization in the ever-changing situation. Ultimately, we adapted our overall emergency operations plan and were quickly able to move the entire organization into minimum-safe operations across the country.
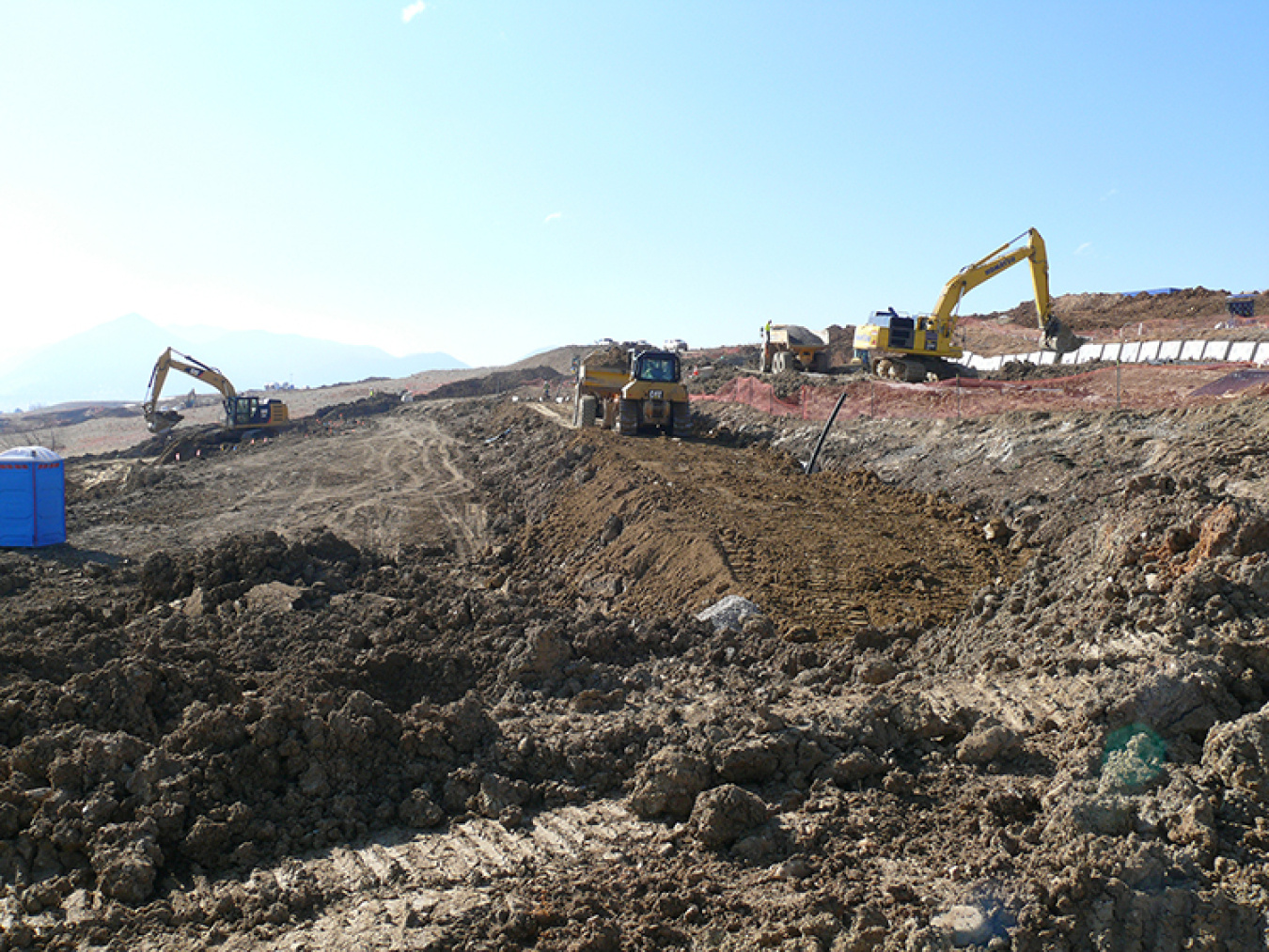
At the Original Landfill stabilization project at Rocky Flats Site, Colorado, equipment operators on the landfill’s east side place gravel in an interceptor ditch below anchor row three and place backfill soil over completed anchor row four.
Q: How did you deal with physical rehabilitation work in the field? Did you stop work during the pandemic, or did you switch into minimal operation?
CM: We invoked Minimum Safety operations, or MINSAFE, as soon as the emergency started. We coordinated with regulators and stakeholders as things developed in the first few days. We continued fieldwork at the Rocky Flats, Colorado, and Weldon Spring, Missouri, sites, as well as in some selected activities. Our work did not stop; we were just very judicious and made risk-based decisions on what to stop and what to continue. We reviewed long-term surveillance and maintenance [LTS&M] activities and decisions were made on a case-by-case basis about which operations would stop. Our goal was to maintain good standing with all regulatory and compliance activities at our sites. This included continuing with projects that were critical to the safe, long-term management of our sites, particularly at our larger sites, where we have federal and contractor workers stationed.
LM is now responsible for 100 sites across the United States, from Alaska to Puerto Rico. We have delayed work at some sites requiring workers to travel overnight to reach a site. In addition, in areas where COVID-19 levels are higher, it is not safe to send workers to a site, or people from outside of an area are asked by local authorities not to come to the area.
However, for more remote sites, LM has maintained contact with regulators and local stakeholders. For example, on March 31, a 6.5-magnitude earthquake occurred in Idaho near the Lowman site, where LM conducts LTS&M on a small uranium mill tailings cell. Fortunately, a local fire chief who is a point of contact for LM in case of an emergency at that site was able to visit and report back to LM that there was no visible damage.
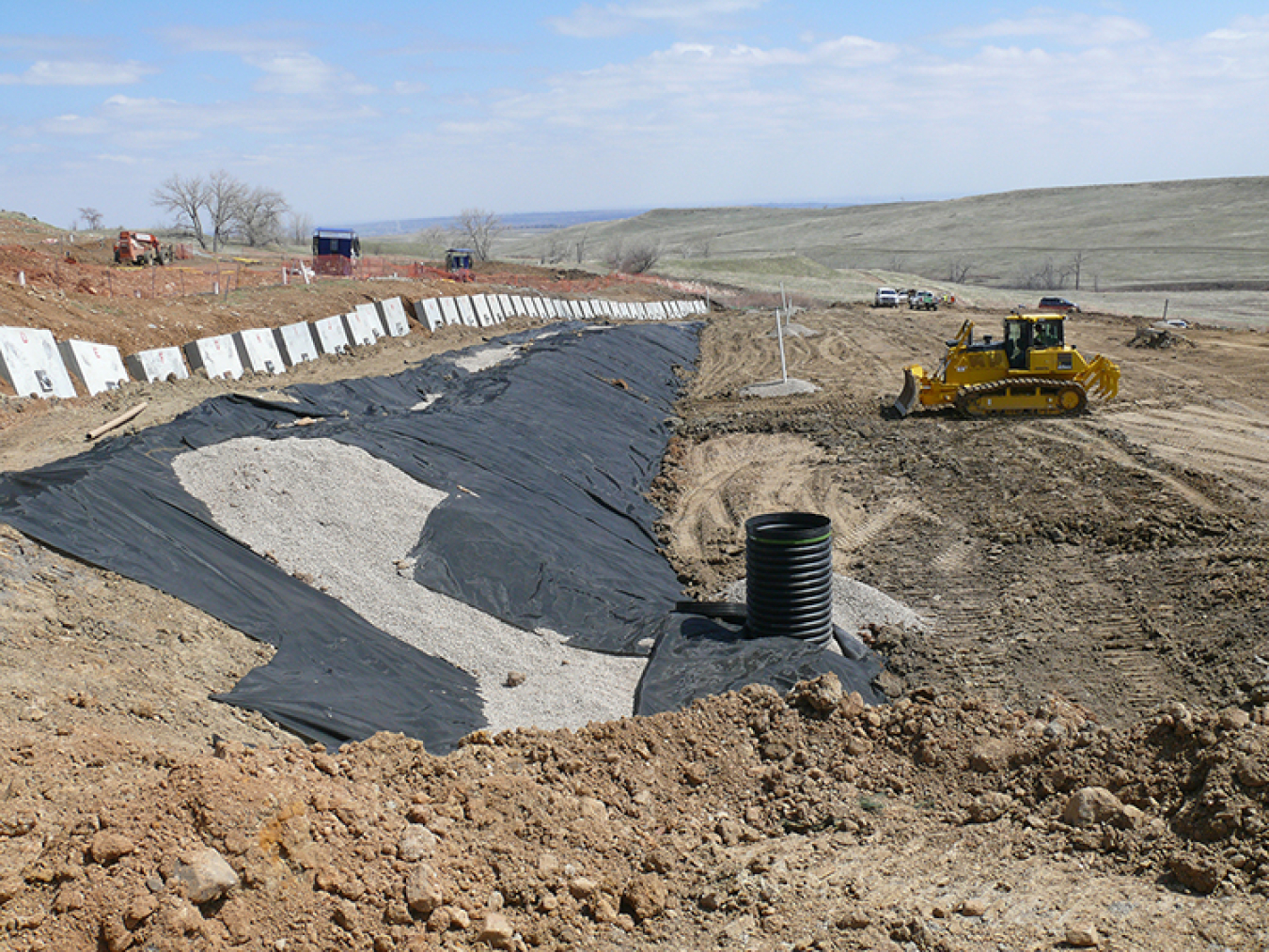
At the Original Landfill stabilization project at Rocky Flats Site, Colorado, an equipment operator grades soil on top of a drainage ditch below anchor row three on the landfill’s east side. A replacement stand pipe was installed to access seep 10.
Q: How did the pandemic affect LM’s overall work processes? Has telework been used, for example?
CM: LM pivoted from an outside to an internal focus in response to the pandemic, to make sure the safety and health of our employees was our primary goal. Telework moved from voluntary to mandatory for most employees during MINSAFE. In fact, LM was uniquely ready for working remotely, because we are a regional organization maintaining sites across the country. We maintain excellent contact throughout the organization. Yet with COVID-19, we knew any activities that did not undermine our commitment to being protective of human health and the environment and that could be stopped in a controlled, safe way would have to be stopped during this pandemic and any work that could be completed remotely would continue. When the pandemic first started, we had to have everyone fully embrace using technology and make sure we had the resources available to help people work remotely in the most efficient way possible.
Ironically, just prior to shifting to almost complete telework, LM performed a drill in which everyone worked from home for a day. After the drill, help was provided to staff who had trouble logging in remotely. We quickly realized how valuable this exercise was after nearly everyone was working on LM’s computer network from home because of the pandemic.
At 16 sites, LM has solar-powered SOARS (System Operations and Analysis and Remote Sites) stations that transmit data using satellites. Among the types of data collected are pump control, flow rate, and in-line pressure for water treatment systems; meteorological data; and visual images from webcams. SOARS has allowed LM to operate some water treatment systems and monitor the condition of sites where we could not send staff during minimum-safe operations. However, the camera at the Bluewater mill tailings cells was not working prior to LM going into minimum-safe operations. The Bluewater site is in New Mexico, which has restricted workers from outside the state from traveling to the area to do work. While the SOARS stations have been valuable for some information during the pandemic, it is not ideal, because it is important to maintain the station with in-person staff.
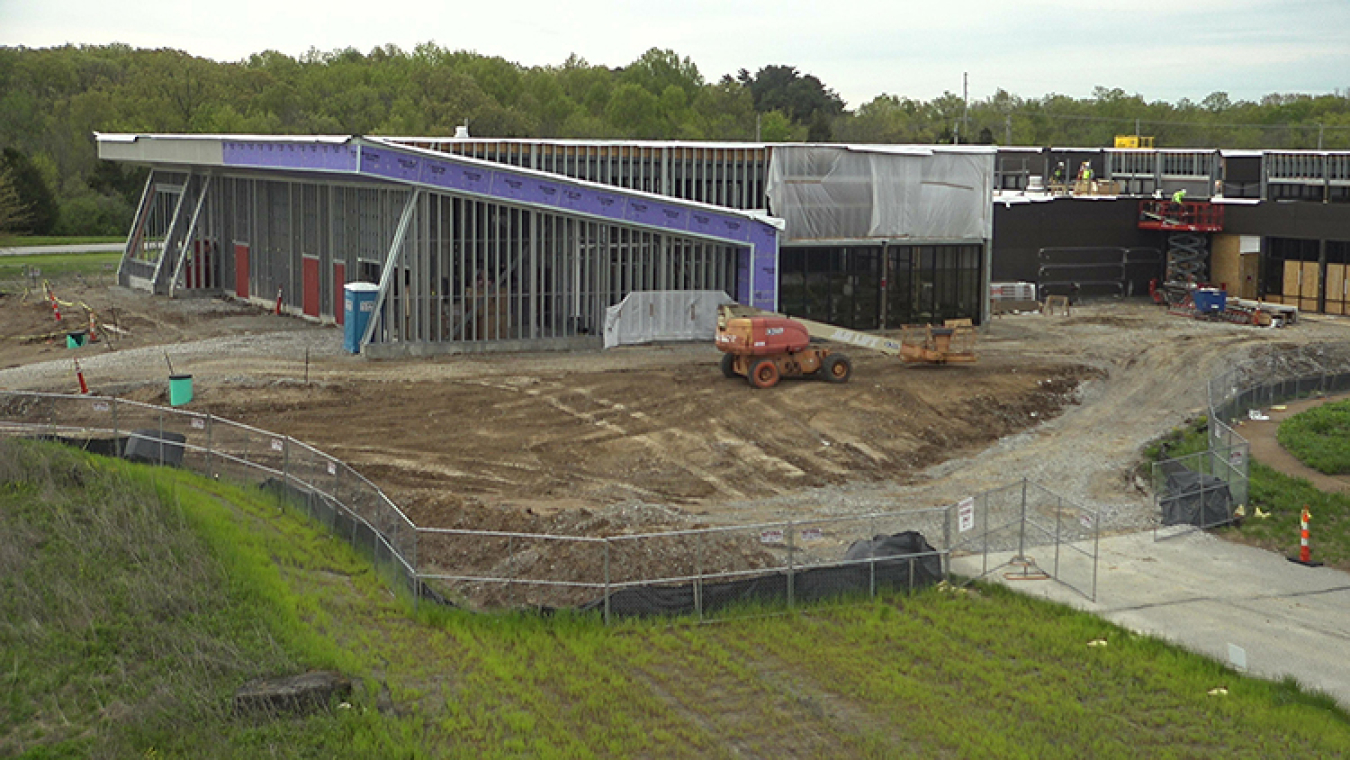
At the Weldon Spring Site in Missouri, U.S. Army Corps of Engineers contractors have completed exterior wall structures and began siding installation.
Q: How is occupational health and safety currently regulated under the new conditions?
CM: Because of the pandemic, we’ve had some reduction in requirements, such as keeping employees’ training current in certain areas like the hazardous waste 8-hour refresher and radiological control certifications. These are just two examples of activities where we were allowed to push the refresher training further than the normal year.
Something that has become normal is working from home. With the majority of our workforce teleworking, we needed to help all of our employees set up their home offices in the best manner possible to provide a comfortable place to work. We sent out an ergonomic workstation self-assessment checklist, along with the link to an ergonomics video to give some modification guidelines. We also have an ergonomist on staff to answer questions from employees.
For the few employees still working at job sites, social distancing protocols were instituted into the ongoing construction projects, along with increased use of personal protective equipment and procedures to achieve social distancing. We’ve included contractual modifications to LM’s support contractor and subcontractors. Access control points were enhanced with screening protocols for health status, recent exposure, and to assess employees’ readiness for work. Cleanings and disinfecting procedures were instituted for construction offices, equipment, and vehicles, and the number of persons in a vehicle and construction equipment were restricted. Additionally, if people had to travel to a job site, local hotel facilities were checked for COVID-19 response activities, such as restriction of social activities and distancing, enhanced cleaning, and reducing lodging to one person per room.
As we return to limited operations, LM is embracing some guidelines from the Occupational Safety and Health Administration to bring people safely back into the workforce. Meanwhile, employees have to accept that the world has changed, and managment needs to prepare the workforce for how to safely return and social distance, as well as a myriad of other things that come with the controls necessary to reduce the risk of spreading the virus.
Q: What experiences do you take away from the pandemic for your future work?
CM: Semper Gumby! Always Flexible. 1. Have a good foundational Continuity of Operations plan. 2. Know what work activities must continue based on risk-based decisions with a safety consciousness. 3. Communicate internally and externally with employees and stakeholders.
For those involved in moving the organization to minimum-safe operations, it was too easy to assume that everyone in the organization understood what was going on. So, it’s important to communicate often and cover the same topics multiple times to reassure employees that we can and will get through this together and for employees to understand how work conditions and requirements will change, as LM begins resuming work at more sites. Also, we continue to maintain close coordination with regulatory agencies. This pandemic highlighted the need to be able to respond quickly to changing conditions, and LM was able to gain concurrence from our regulatory agencies in quick order, due to the close relationships maintained through our daily execution of LTS&M activities.
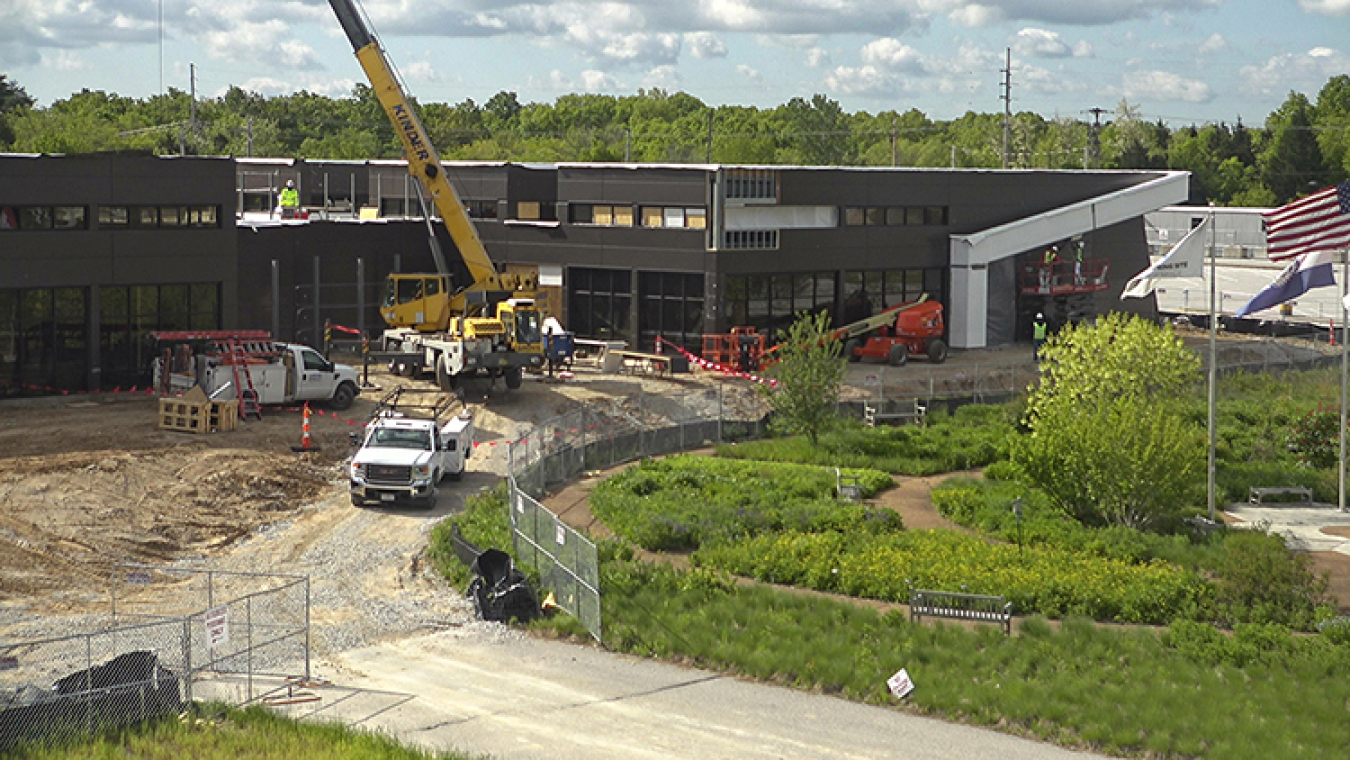
At the Weldon Spring Site in Missouri, U.S. Army Corps of Engineers contractors install exterior siding and glass on the southwest side of the building.
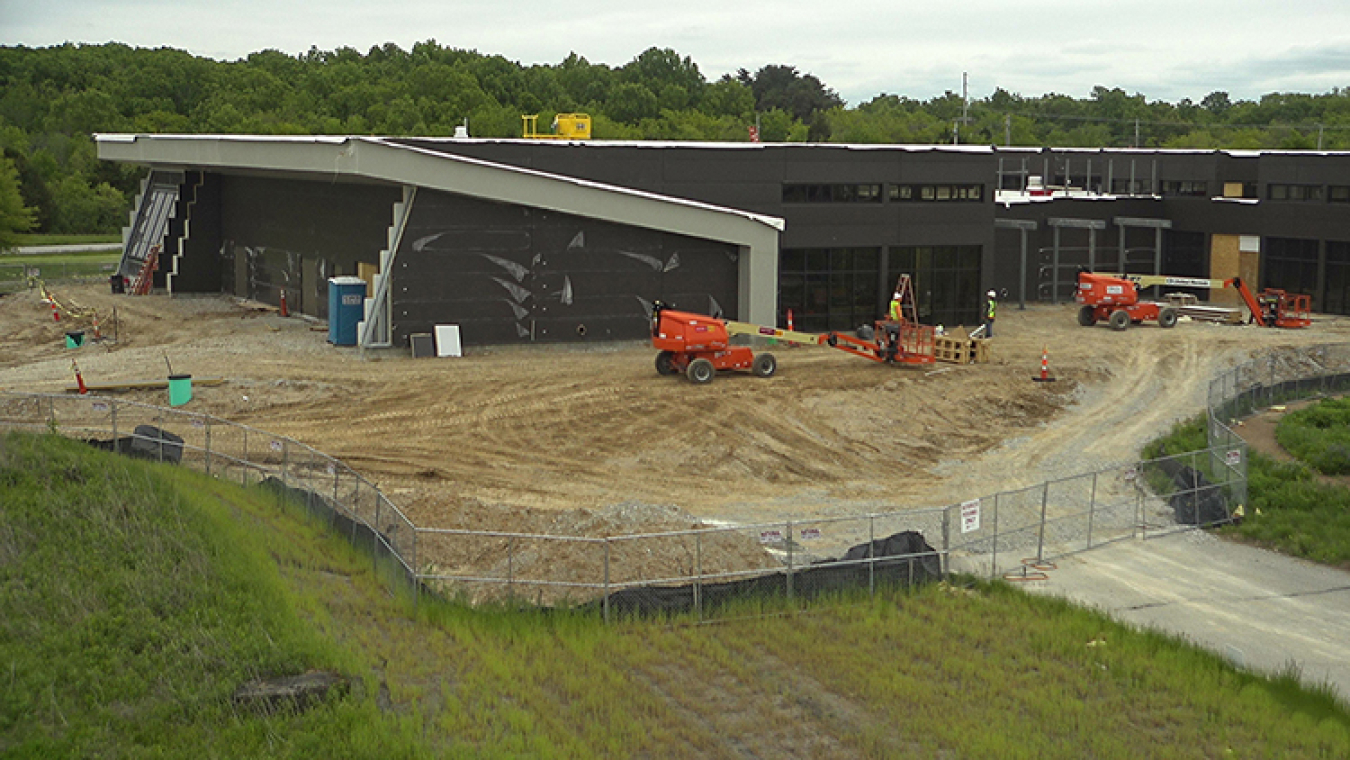
At the Weldon Spring Site in Missouri, U.S. Army Corps of Engineers contractors install exterior siding and glass on the northwest side of the building.