EM’s Office of River Protection and its tank farms contractor are set to use virtual capabilities to inspect an upcoming project.
Office of Environmental Management
February 5, 2019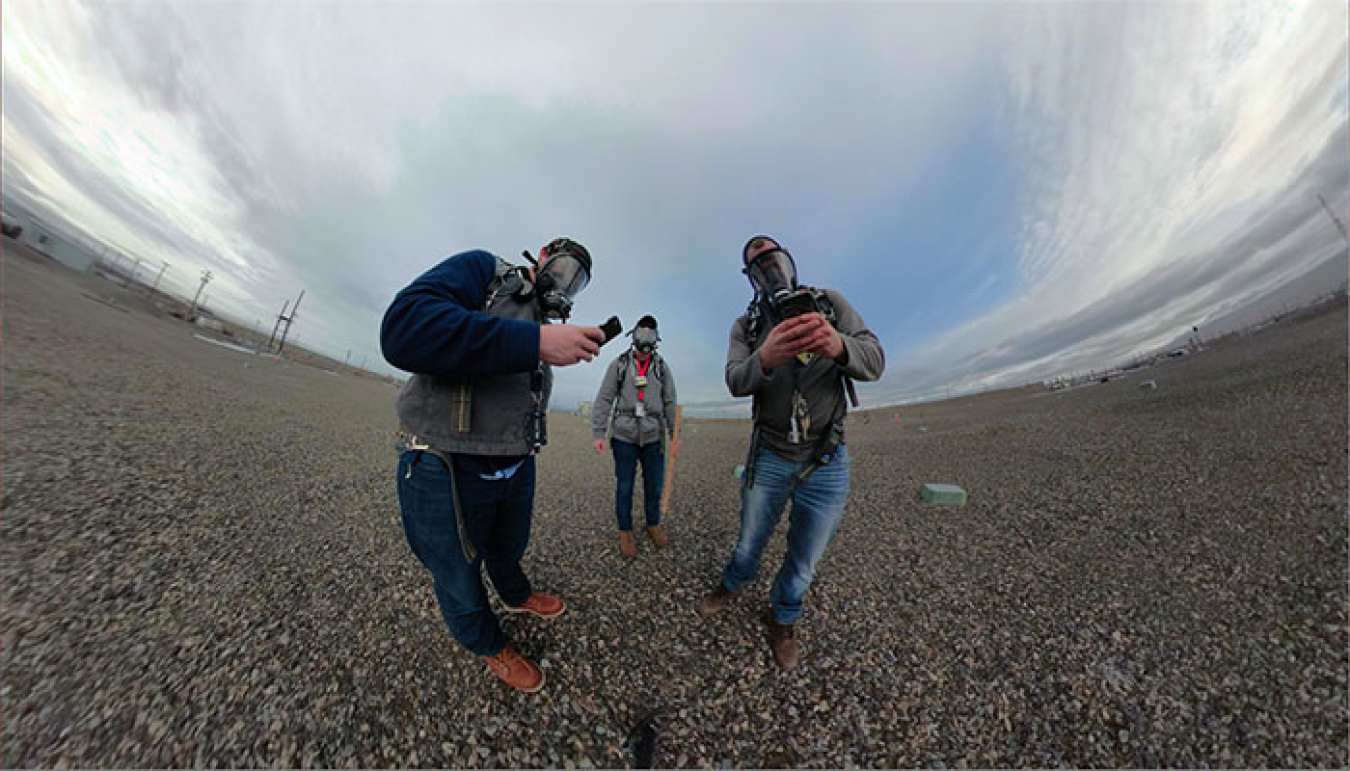
RICHLAND, Wash. – EM’s Office of River Protection and its tank farms contractor are set to use virtual capabilities to inspect an upcoming project, improving safety and efficiency.
Washington River Protection Solutions (WRPS) created 3-D scanning technology for engineers designing the interim surface barrier for the TX Farm, one of the Hanford Site’s largest with 18 single-shell tanks. Design work takes place this year, with construction scheduled to begin in 2020.
The technology allows the engineers to view every above-ground detail of the tank farm from their computers, zooming in and out of a 360-degree high-definition rendition of the area.
The barriers help prevent rain and snowmelt from intruding into the underground tanks or percolating into the soil and driving contaminants toward groundwater.
“On the last project of this type in SX Farm, our design team was unable to account for actual conditions on the surface that weren’t captured in the design drawings we were working from,” said Alex Pappas, WRPS closure and interim measures engineer. “Missing were the as-built details as they differed from the original design. The virtual walkdown technology gives us on-demand access to those items.”
This is the first use of the technology in WRPS field work. Pappas said its benefits are twofold.
“It’s cost effective, because it saves the cost of training engineers to go into the farms or hiring subcontractors,” he said. “More importantly, it minimizes risk by having fewer people in the tank farm and for shorter times. This was a huge win for us that will pay off as we move to the construction phase.”
Rather than enter the farm to collect the missing elements for TX Farm, which would have added cost, delayed work, and put workers at risk, the team collected all needed photos in an hour, stitched them together, and delivered them to the engineering team by week’s end.
Steve Eklund, WRPS human performance improvement facility visualization lead, said the virtual images of buildings or farms have many potential applications, including pre-job and post-job reviews, work planning, and employee training.
Last year, Eklund created a virtual inspection of the 242-A Evaporator. Viewers are taken through doors, up and down stairs, and can zoom in on equipment as needed, all remotely.
“That capability came in handy recently when an outside inspector who didn’t have the training or badging to enter the evaporator was able to get an up-close view of the equipment he needed to inspect without going inside,” Eklund said.