Hanford Waste Treatment and Immobilization Plant Analytical Laboratory team has completed a commissioning test of a high-efficiency particulate air filtration system that uses a new filter design that exceeds nuclear industry standards and requirements.
Office of Environmental Management
June 15, 2021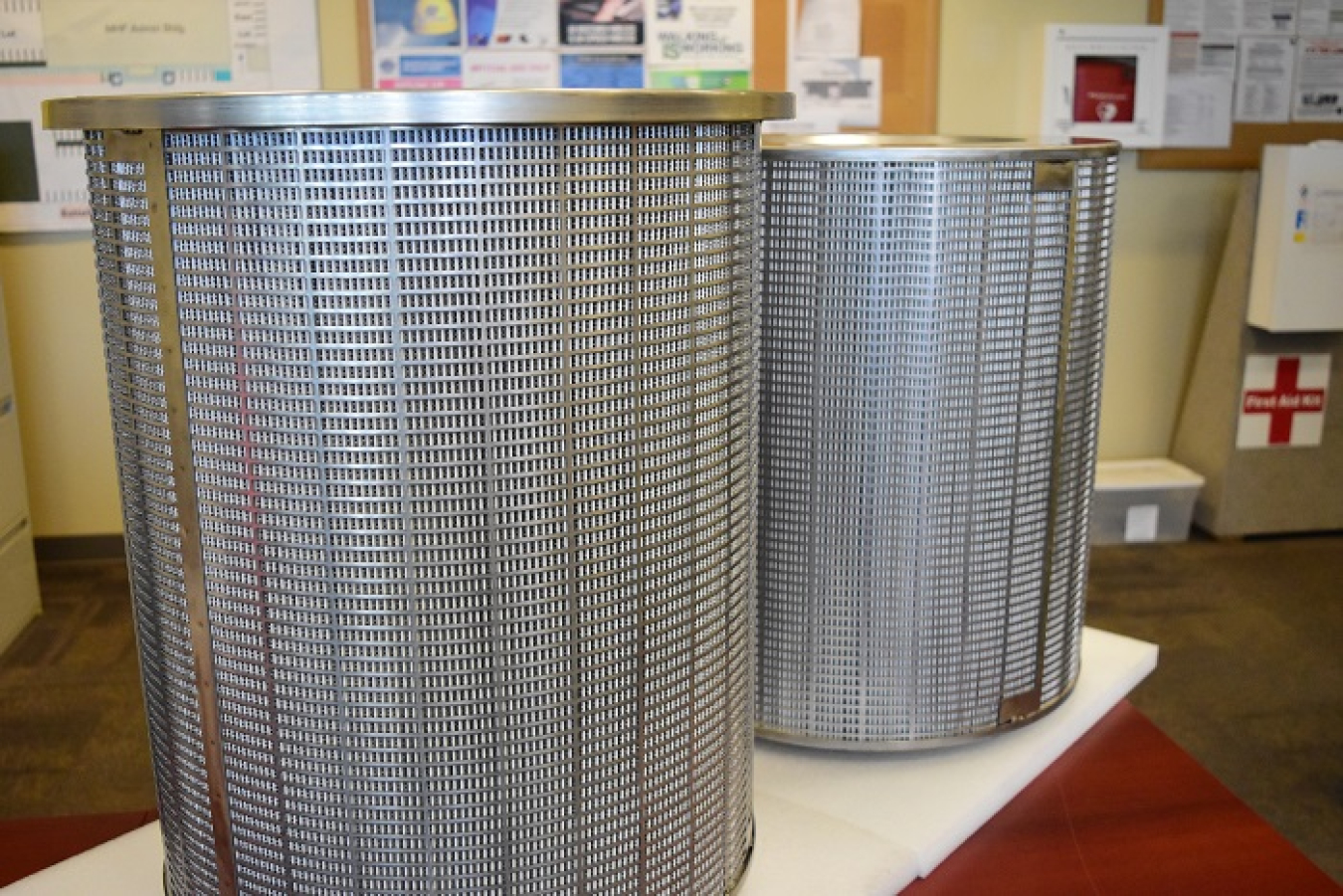
RICHLAND, Wash. – EM’s Hanford Waste Treatment and Immobilization Plant (WTP) Analytical Laboratory team has completed a commissioning test of a high-efficiency particulate air (HEPA) filtration system that uses a new filter design that exceeds nuclear industry standards and requirements.
Finishing the test was a prerequisite for the laboratory team to begin using scientific equipment with radioactive materials, which is required for operations.
“The plant team and Mississippi State University (MSU) have collaborated successfully throughout the design, installation, and multiple types of stringent tests of these special filters,” said Mat Irwin, Office of River Protection deputy assistant manager for the plant. “These filters have exceeded all standards required for HEPA filtration, and now we’re confident the overall system is ready for operations.”
HEPA filters are critical to the nuclear industry for their ability to filter airborne contaminants from ventilation and exhaust systems in accordance with state and federal requirements. The filters will also be used in the plant’s Low-Activity Waste (LAW) Facility, which is where large melters will immobilize Hanford tank waste in glass when operations begin.
“It was definitely a project-wide effort to safely carry out the tests,” said Jeffrey Peterson, a field test manager with Waste Treatment Completion Company, a subcontractor to WTP prime contractor Bechtel National, Inc. “The team included maintenance crews, commissioning technicians, on-site MSU experts, and test engineers making this important step toward melter heatup and ultimate operations possible.”
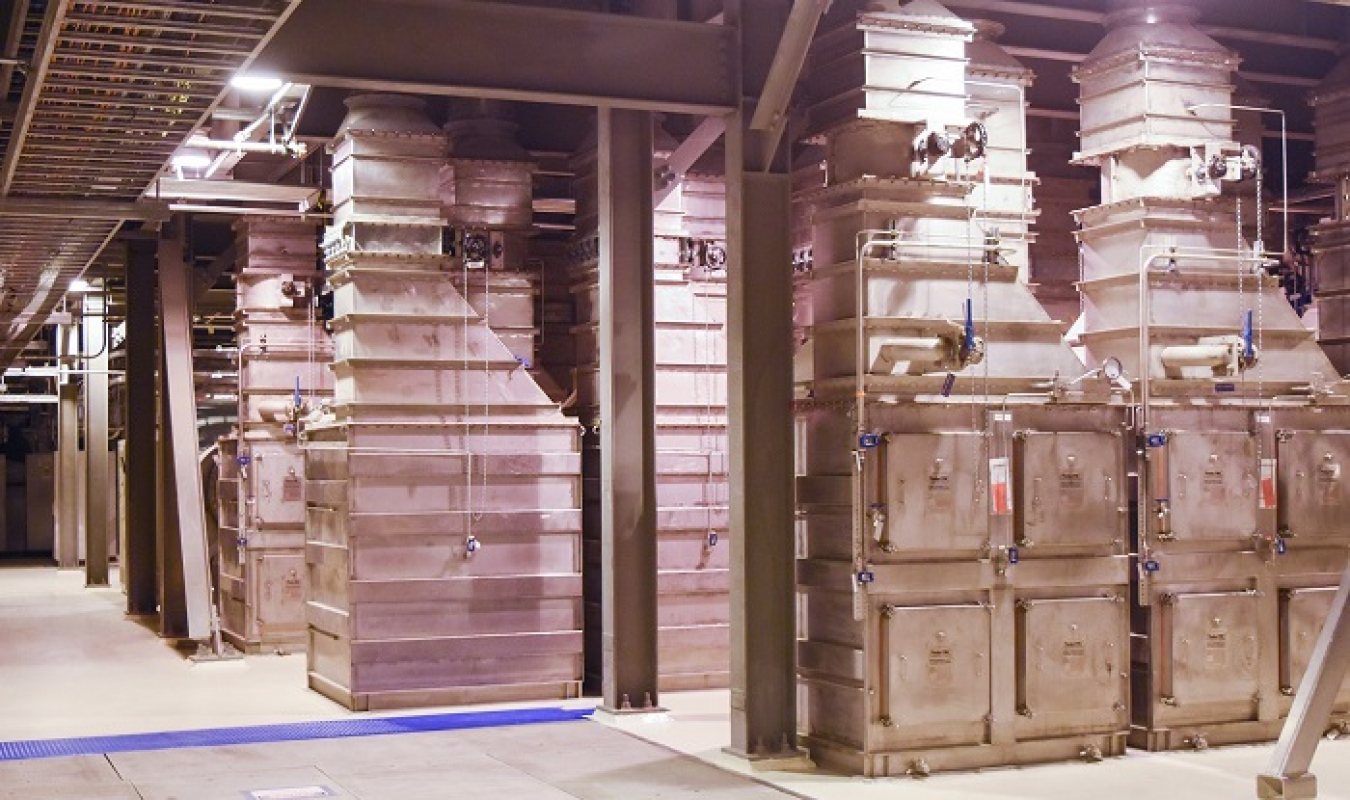
For testing, the team saturated each HEPA filter with an aerosol spray to simulate potential radioactive contamination, passed air through the filters, and collected and analyzed air samples on the other side to ensure the filters captured the simulant as designed. During future operations, air from the laboratory will flow through the HEPA filters before reaching the building’s environmental exhaust system, where it will then be sampled to ensure it meets Washington State Department of Health standards.
Each HEPA filter weighs more than 70 pounds and is used in multiple banks of four filters, called housings. In total, the laboratory commissioning team tested 128 filters to verify each one was installed correctly, sealed, functioned properly, and met operational air flow requirements. The filters are constructed of fragile fiberglass sheets resembling paper, which are pleated and installed in a filter pack, similar to a thick furnace filter.
The filters, designed by Bechtel and Porvair Filtration Group, are relatively new to the nuclear industry. Previous testing conducted at MSU demonstrated these filters are at least five times stronger than standard HEPA filters and exceed plant-specific standards and codes set by the American Society of Mechanical Engineers. Previous code compliance testing at MSU, Underwriters Laboratories, and the U.S. Army Edgewood Chemical Biological Center validated the filter performance.
Commissioning tests ensure utilities, equipment, and process systems are integrated and ready to support future plant operations. There are approximately 65 commissioning test packages, incorporating over 250 individual objectives, that span the plant’s LAW Facility, Analytical Laboratory, Effluent Management Facility, and Balance of Facilities.
The plant will vitrify, or immobilize in glass, tank waste as part of Hanford’s Direct-Feed Low-Activity Waste program. The program is a system of interdependent projects and infrastructure improvements, managed and highly integrated, that must operate together to vitrify the waste. During vitrification, the nuclear waste and glass-forming materials are mixed and heated up to 2,100 degrees Fahrenheit inside one of two large melters in the LAW Facility, then poured into stainless steel containers for safe storage.
Information on the commissioning process, including a loss-of-power test and melter heatup, is available on the Journey to Melter Heatup website.
The plant facilities can be viewed using the self-guided Hanford Virtual Tour.
To receive the latest news and updates about the Office of Environmental Management, submit your e-mail address.