Both capital projects at EM’s WIPP are making remarkable progress due to a determined, creative workforce that is overcoming the challenges of the multimillion-dollar work so the facility can operate safely and compliantly for decades to come.
Office of Environmental Management
December 13, 2022
CARLSBAD, N.M. – One is very visible, and one you can’t really see. But both capital projects at EM’s Waste Isolation Pilot Plant (WIPP) are making remarkable progress due to a determined, creative workforce that is overcoming the challenges of the multimillion-dollar work so the facility can operate safely and compliantly for decades to come.
“WIPP’s utility shaft and the Safety Significant Confinement Ventilation System (SSCVS) are making very good progress and are overcoming supply chain issues with creative workarounds,” said Steve Smith, capital and infrastructure projects manager with WIPP management and operations contractor Nuclear Waste Partnership (NWP).
The shaft will be an air intake for the massive SSCVS being constructed. It is WIPP’s fifth shaft — there are also salt, waste, air intake and exhaust shafts — and upon completion, the utility shaft will be the site’s largest at 26 feet in finished diameter.
The utility shaft will provide air into the mine, including mining on new panels to the west of the WIPP facility. The SSCVS will increase airflow in the underground from 170,000 to 540,000 cubic feet per minute, providing enough airflow to simultaneously mine, emplace waste and bolt. Bolting controls the movement of salt rock — known as salt creep — in the WIPP underground.
Since the post-COVID recommencement of excavating at the utility shaft in June, crews have worked around the clock to reach 720 feet — en route to the final shaft depth of 2,275 feet. The shaft is lined with concrete to 712 feet.
Debris is blasted one-half layer at a time; as of Nov. 30, 134 blasts have loosened enough rock for 2,285 buckets of muck to be removed to the surface. Muck is currently being hauled east across the WIPP access road to a salt pile north of the site. The New Mexico Environment Department recently approved the use of a new salt pile on the west side of the road.
On order are two air intake fans — which will generate 520,000 cubic feet per minute of airflow, forcing air down the shaft and into the WIPP underground — along with battery packs for a hybrid bolter and a continuous mining machine.
“The utility shaft is tracking to the schedule, progressing through some of the most difficult geology now and still maintaining the overall project schedule,” Smith said. “Though you can’t see it, as it is all subsurface, excellent progress is being made.”
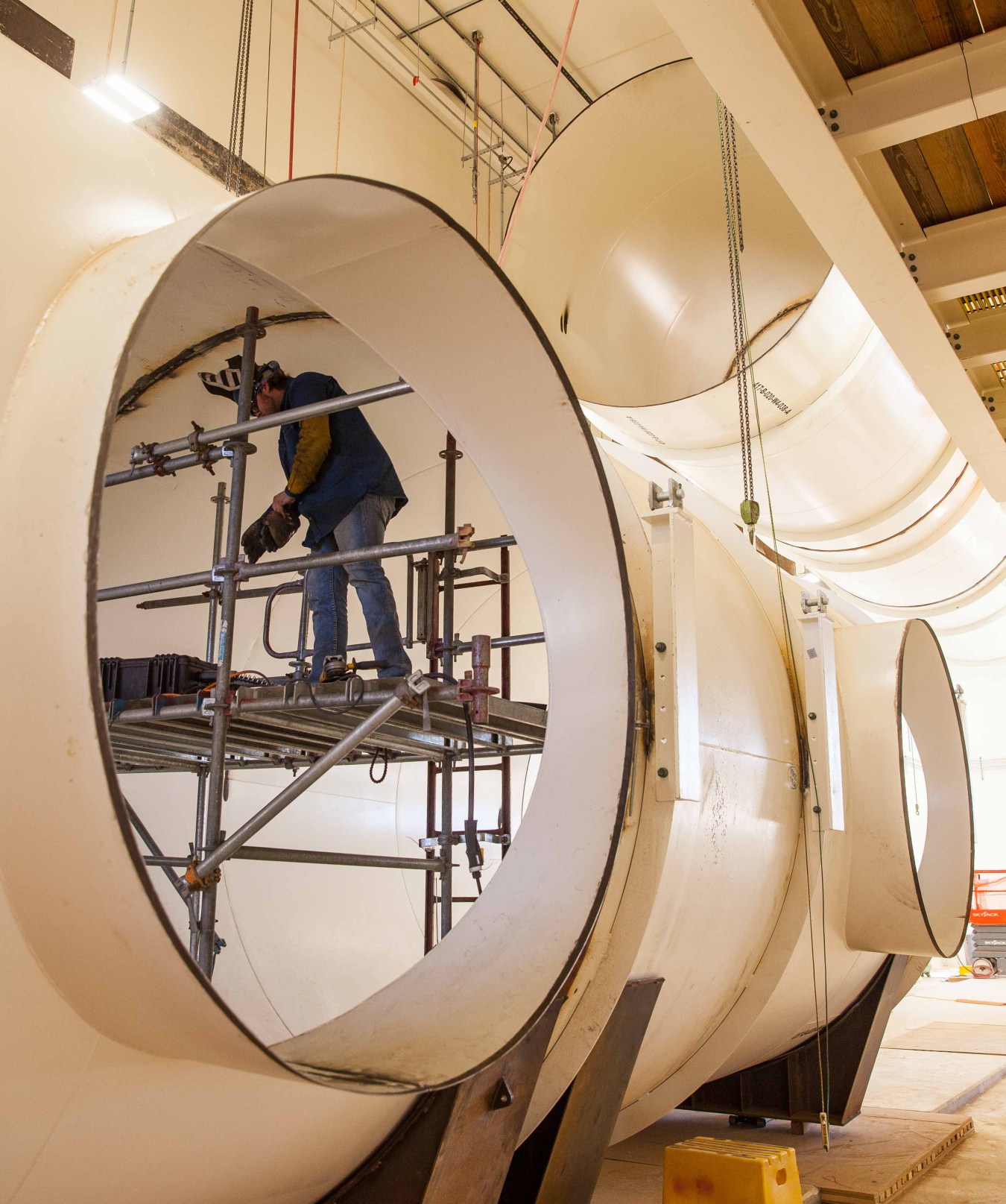
As part of the Safety Significant Confinement Ventilation System, this Salt Reduction Building (SRB) ductwork will connect to fans that will move air from the underground to the New Filter Building after removing salt. The ductwork is now connected to the ceiling of the SRB.
More visible is construction on the SSCVS, which consists of two buildings, the Salt Reduction Building (SRB) and the New Filter Building (NFB).
The SRB will use demisters and other equipment to drop salt from the underground airflow as it reaches the surface.
Fans will then move the air to the NFB, where 1,000-horsepower fans, already onsite, will pull the air through 22 high-efficiency particulate air (HEPA) filter banks before exhausting the air through a 125-foot stack. The switchable filter banks mean work in the WIPP underground will not have to slow during filter changes.
At the NFB, workers have finished installing columns and roof beams, and most wall panels. At the SRB, crews completed the HVAC ducting; main airflow ductwork; and a weather-tight, multi-layer, multi-material roof.
“Anyone can look at the SSCVS project and see the structures are erected and the majority of the Salt Reduction Building equipment is installed,” Smith said.
To receive the latest news and updates about the Office of Environmental Management, submit your e-mail address.