Hanford Improves Safety Culture Following Recommendation
Office of Environmental Management
September 24, 2019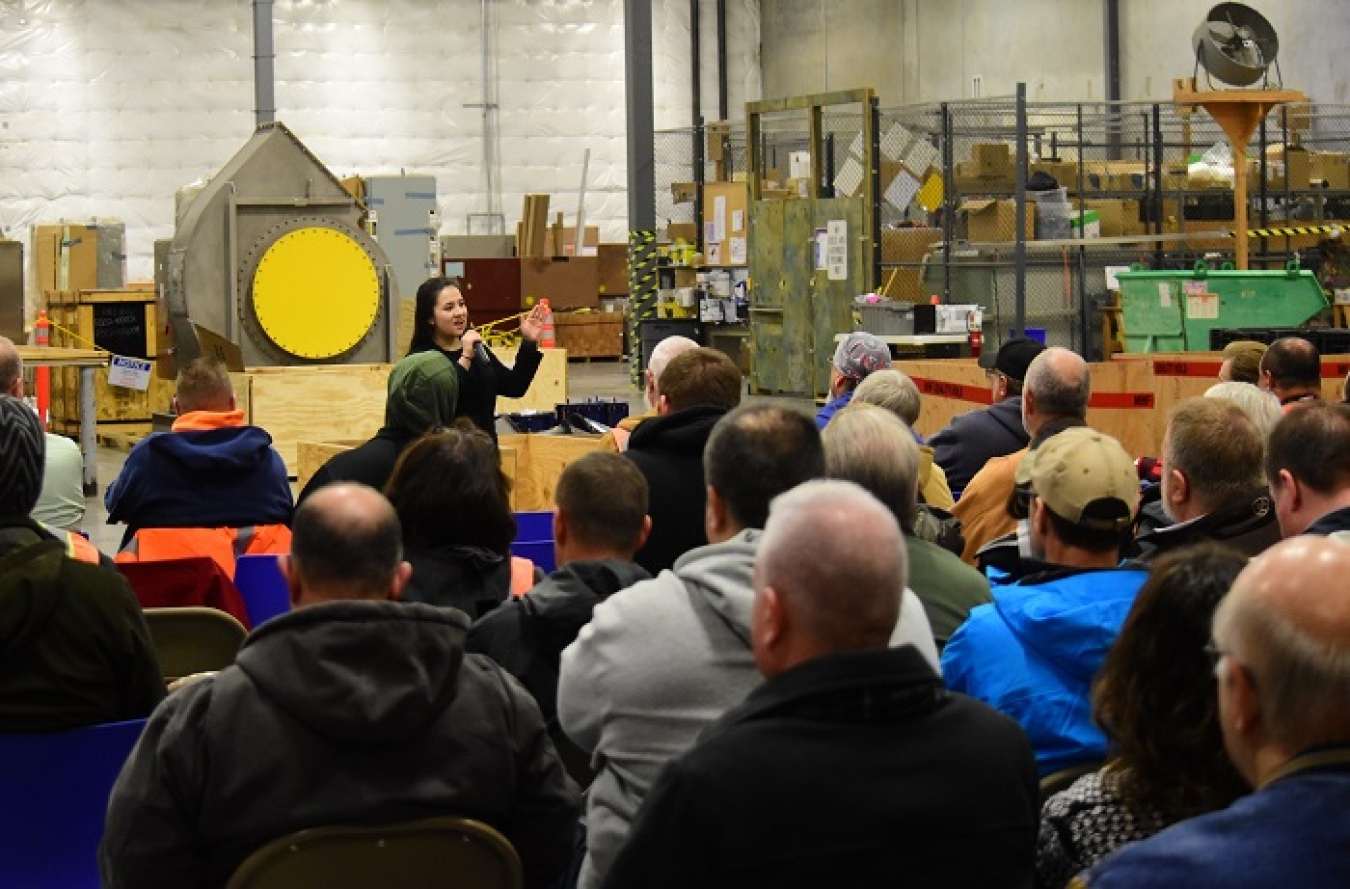
RICHLAND, Wash. – Meetings begin with a safety message, shifts begin with a safety briefing, and signs with safety reminders are located across the EM Hanford Site.
This has become the norm at the site over the last eight years, where EM’s Office of River Protection (ORP) has focused on improving its safety culture, especially at the Waste Treatment and Immobilization Plant (WTP).
Eight years ago, the Defense Nuclear Facilities Safety Board issued Recommendation 2011-1 indicating the WTP’s safety culture was flawed, and the board cited several observations indicating how it had become so. ORP immediately formulated a plan to improve.
Recently, the board chairman stated Recommendation 2011-1 would be closed. The board agreed ORP had “adequately addressed the underlying causes associated with the Board’s concerns.”
ORP Deputy Manager Ben Harp said the closure of Recommendation 2011-1 was a result of a lot of hard work by many employees and management to change the safety culture from 2011 to now.
“It took a lot of hard work to achieve the result that motivated the board to close Recommendation 2011-1,” Harp said.
The improvements went beyond messages, briefings, and signs.
To pinpoint the areas in most need of improvement, ORP reviewed past assessments. Some key focus areas were safety culture expectations and safety culture training. Industry best practices showed that establishing a diverse employee-driven group, a management-monitoring group, and a safety culture advisor would work best to improve the safety culture at WTP and the Hanford Site. ORP also created the Organizational and Safety Culture Improvement Council, Organizational Safety Culture Advisory Group, and a safety culture advisor position.
In addition, Hanford leadership saw the opportunity to bridge gaps between supervisors and staff. This included DOE training mandated by the Secretary of Energy for all DOE and DOE contractor senior leaders targeted at equipping senior leaders to lead a positive shift in the organization and culture by fostering a work environment that promotes trust, a questioning attitude, and receptiveness to raising issues.
Steps taken to improve the safety culture at the plant included improving management involvement, creating a consolidated area of information to set expectations, issuing surveys and self-assessments, increasing training, and clearly defining roles and responsibilities.
Over the last eight years, all employees have grown and an understanding of safety culture is now the expectation and not the exception. A working environment where employees feel their opinions are valued by leadership, especially when the exchange starts small, has spread throughout the workplace. Leadership willing to listen to opinions and open lines of communication with other industry leaders shows that positive change has occurred.